Eco-Friendly Packaging: How Automated Systems Reduce Resource Waste in Steel Coil Packaging
In today's rapidly evolving industrial landscape, sustainability is a critical priority, particularly for resource-intensive sectors like the steel industry. Effectively packaging steel coils presents significant challenges regarding resource waste and environmental impact. Traditional, manual packaging methods often result in excess material use, inconsistent application, and higher energy consumption, contributing to increased costs and a larger ecological footprint.
Fortunately, advancements in technology offer a powerful solution: automated steel coil packaging systems. These systems not only streamline operations and enhance efficiency but also drastically reduce material and energy waste. This article explores how implementing automated systems contributes to more eco-friendly packaging practices in the steel industry, delivering substantial environmental and economic benefits.
1. The Environmental Footprint of Traditional Steel Coil Packaging
Traditional methods for packaging steel coils often fall short in terms of efficiency and sustainability. Manual packaging processes typically involve:
- Inconsistent Wrapping: Manual application of stretch film or paper often leads to uneven layers and excessive material usage to ensure perceived protection.
- Material Overuse: Strapping might be applied with inconsistent tension, leading workers to use more straps than structurally necessary.
- Energy Waste: Older machinery and prolonged manual handling can consume significant amounts of energy.
- Higher Risk of Damage: Inconsistent packaging quality increases the risk of coils being damaged during handling and transit, leading to waste of the product itself.
These inefficiencies collectively contribute to a substantial environmental impact, generating unnecessary material waste and consuming excess energy. Furthermore, companies relying on outdated methods face increasing pressure from regulations and market expectations to adopt more sustainable operations. Automation provides a clear pathway to address these challenges.

2. Precision Material Application: How Automated Systems Cut Waste
A primary advantage of automated systems in promoting eco-friendly packaging is their ability to minimize packaging material consumption through precision. Key features include:
- Optimized Material Dispensing: Automated wrapping machines (e.g., orbital stretch wrappers) use sensors and programmable logic controllers (PLCs) to measure coil dimensions and apply the precise amount of film or paper required for secure protection, significantly reducing overuse common in manual wrapping.
- Consistent Film Stretching: Advanced wrappers pre-stretch film to its optimal yield point, ensuring maximum coverage and load stability with minimum material. This can reduce film consumption by 50% or more compared to manual methods.
- Accurate Strapping: Automated strapping machines apply straps with consistent, pre-set tension, ensuring coil security without unnecessary extra straps. They precisely cut strap lengths, minimizing scrap.
By eliminating the guesswork and variability inherent in manual processes, automation ensures optimal material usage for every coil, leading to substantial reductions in plastic waste, paper consumption, and strapping material scrap.
3. Enhancing Energy Efficiency in Packaging Operations
Automated steel coil packaging systems are engineered for greater energy efficiency compared to manual methods and older equipment:
- Optimized Machine Cycles: Automation ensures machines run only when needed, utilizing efficient start/stop sequences and minimizing idle time energy consumption.
- Energy-Saving Components: Modern systems often incorporate variable frequency drives (VFDs) and servo motors, which adjust energy consumption based on the load requirements, unlike older motors that run at full power constantly.
- Integrated Operations: Combining multiple packaging steps (e.g., conveying, wrapping, strapping, labeling) into a single automated line reduces overall energy demand compared to operating separate, less efficient machines.
- Power-Saving Modes: Many automated machines feature low-power standby modes during periods of inactivity, further conserving energy.
These design considerations significantly lower the energy consumed per packaged coil, reducing operational costs and the facility's carbon footprint.
4. Consistency and Accuracy: Eliminating Rework and Waste
Manual packaging quality can vary significantly between operators and shifts, leading to inconsistencies that compromise protection and often result in material overuse as a precaution. Automated systems provide unwavering consistency:
- Uniform Application: Every coil receives the same high-quality packaging according to pre-defined specifications, regardless of operator skill or fatigue.
- Reduced Errors: Automation minimizes human error, drastically reducing the likelihood of improperly packaged coils that require rework (unwrapping and re-packaging), which consumes additional materials, time, and energy.
- Improved Load Integrity: Consistent wrapping and strapping enhance the stability and protection of the coil, reducing the risk of damage during handling and transit.
This high level of accuracy and repeatability ensures that resources are used effectively the first time, directly contributing to waste reduction and operational efficiency.
5. Optimizing Packaging for Reduced Transportation Emissions
The benefits of automation extend to logistics and transportation sustainability. Optimized packaging achieved through automation can lead to:
- Compact Packaging: Precise wrapping and strapping create tighter, more uniform packages that eliminate unnecessary bulk often associated with over-packaged manual methods.
- Improved Space Utilization: More compact coils allow for denser loading of trucks, railcars, or shipping containers, maximizing the payload per shipment.
- Fewer Shipments: Transporting more coils per vehicle reduces the total number of trips required to move the same volume of product.
- Lower Fuel Consumption: Reduced transportation frequency directly translates to lower fuel consumption and associated greenhouse gas emissions (Source: EPA SmartWay Program).
By enhancing load density and reducing transport needs, automated packaging contributes to a more sustainable supply chain.
6. Automated Palletizing: Reducing End-of-Line Packaging Waste
The palletizing process, where finished coils are prepared for shipment on pallets, is another area where automation drives sustainability:
- Efficient Stacking Patterns: Automated palletizing systems utilize robotics and intelligent software to arrange coils on pallets in optimized patterns, maximizing stability and space efficiency.
- Reduced Secondary Packaging: Stable, well-arranged loads often require less secondary packaging material (like excessive shrink wrap or corner boards) to secure them for transit.
- Integration with Wrapping/Strapping: Automated palletizers can seamlessly integrate with upstream wrapping and strapping systems, ensuring the entire end-of-line process is optimized for minimal material use.
- Compatibility with Reusable Pallets: These systems can easily handle various pallet types, facilitating the use of reusable or recyclable pallets , further reducing wood or plastic waste.
Automating palletizing minimizes material consumption and enhances load security, contributing significantly to overall resource waste reduction.
7. Leveraging Smart Technology for Continuous Improvement
Modern automated packaging systems increasingly incorporate smart technology and Industrial Internet of Things (IIoT) capabilities:
- Real-Time Monitoring: Sensors integrated into the machinery track key parameters like material consumption (film length, strap count), energy usage, and cycle times.
- Data Analytics: Collected data can be analyzed to identify trends, pinpoint inefficiencies, and measure performance against sustainability targets.
- Predictive Maintenance: Monitoring machine health helps predict potential failures, allowing for proactive maintenance that prevents unexpected downtime and associated waste (e.g., damaged product during a breakdown).
- Automated Adjustments: Advanced systems can automatically adjust settings (e.g., film tension, wrap counts) based on real-time feedback, ensuring optimal performance and minimal waste without constant operator intervention.
This data-driven approach enables continuous improvement, helping companies refine their packaging processes to further reduce waste and enhance sustainability efforts.
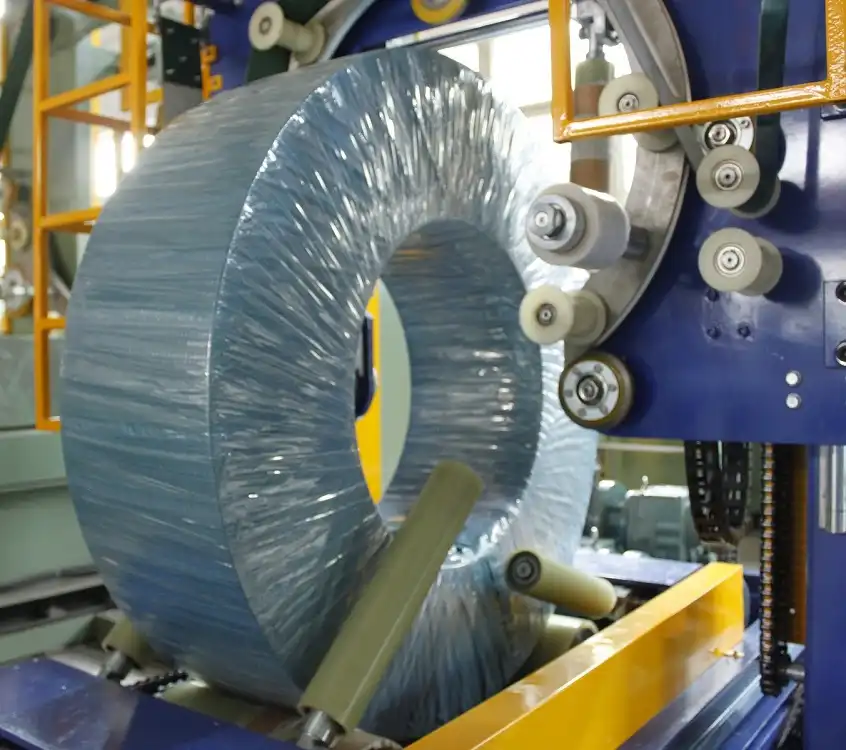
8. Lowering Operational Costs Through Efficient Automation
Beyond the clear environmental benefits, automated packaging systems deliver significant economic advantages by reducing operational costs:
- Reduced Labor Costs: Automation minimizes the need for manual labor in repetitive tasks like wrapping, strapping, and palletizing, allowing personnel to be reassigned to higher-value roles.
- Lower Material Expenses: Precise material application directly translates to lower spending on consumables like stretch film, paper, and strapping.
- Decreased Energy Bills: Energy-efficient designs lead to reduced electricity consumption and lower utility costs.
- Reduced Damage and Returns: Consistent, high-quality packaging minimizes product damage during transit, reducing the costs associated with returns, replacements, and scrap.
These combined savings enhance profitability, making the investment in automation economically sound alongside its sustainability benefits.
9. Facilitating the Use of Sustainable Packaging Materials
Automation is compatible with, and often enhances the effectiveness of, sustainable packaging materials:
- Thinner Gauge Films: High-performance automated stretch wrappers can effectively apply thinner gauge films that reduce plastic usage while maintaining load containment, something difficult to achieve manually.
- Recycled Content Materials: Automated systems can handle films and straps made with recycled content, supporting circular economy initiatives.
- Biodegradable & Compostable Options: As biodegradable or compostable films become viable for industrial use, automated systems offer the precise control needed for their effective application.
- Paper-Based Solutions: Automated systems can efficiently apply protective paper wraps (like VCI paper for corrosion inhibition) as an alternative to plastic films where appropriate.
- PET Strapping: Automated strappers easily handle PET (Polyethylene Terephthalate) strapping, a recyclable alternative to steel straps (Learn about PET Strapping properties).
By enabling the effective use of these materials, automation further enhances the eco-friendly credentials of steel coil packaging.
10. Ensuring Compliance with Environmental Regulations
Governments and industry bodies worldwide are implementing stricter regulations regarding waste management, recycling, and carbon emissions. Automated systems help steel producers meet these requirements:
- Quantifiable Reductions: The data generated by automated systems (see section 7) provides clear metrics on material and energy savings, facilitating compliance reporting.
- Reduced Waste Generation: Lower material consumption directly reduces the amount of waste generated, helping meet landfill diversion or recycling targets.
- Lower Carbon Footprint: Reduced energy consumption and optimized transportation contribute to a lower overall carbon footprint, aligning with climate goals and potential carbon pricing schemes.
- Demonstrable Commitment: Implementing advanced automation showcases a company's proactive commitment to environmental stewardship, enhancing its reputation with regulators, customers, and investors.
Investing in automation is a strategic move to ensure ongoing compliance and mitigate risks associated with environmental regulations.
11. Reducing Waste Across the Entire Supply Chain
The positive impacts of automated packaging systems ripple throughout the supply chain:
- Improved Product Protection: Securely packaged coils are less susceptible to damage during handling, storage, and transit, minimizing waste not just of packaging materials but of the valuable steel product itself.
- Enhanced Handling Efficiency: Uniformly packaged coils are easier and safer to handle with forklifts, cranes, and automated storage/retrieval systems (AS/RS), reducing handling errors and potential damage.
- Streamlined Receiving: Customers receive consistently packaged, damage-free coils, simplifying their receiving and unpacking processes and reducing their own waste generation.
By ensuring package integrity and optimizing logistics, automation contributes to waste reduction at multiple points from the mill to the end-user.
12. Achieving Long-Term Sustainability Through Automation Investment
Investing in automated steel coil packaging is not just about immediate gains; it's a strategic commitment to long-term sustainability:
- Durability and Scalability: Industrial automation is built for longevity and can often be scaled or upgraded to meet future production needs, providing a lasting solution.
- Continuous Improvement: The technology facilitates ongoing optimization, allowing companies to continually refine processes and further reduce their environmental impact over time.
- Enhanced Brand Reputation: Demonstrating a commitment to sustainability through tangible investments like automation appeals to environmentally conscious customers, investors, and talent.
- Future-Proofing Operations: As sustainability requirements inevitably become more stringent, automated systems provide the foundation for meeting future challenges.
Automation represents a durable investment that yields continuous environmental and economic benefits, positioning companies for sustained success.
13. Case Study: Quantifiable Impact of Automated Steel Coil Packaging
Consider a mid-sized steel service center that transitioned from manual packaging to a fully automated coil packaging line integrating conveying, wrapping, through-eye strapping, and labeling.
Results after one year:
- Material Reduction:
- Stretch film consumption decreased by 30% due to optimized pre-stretch and application control.
- Strapping material usage dropped by 15% through consistent tensioning and elimination of redundant straps.
- Energy Savings: Measured energy consumption per coil packaged decreased by 20%.
- Operational Efficiency: Packaging throughput increased by 50%, reducing bottlenecks and labor requirements per coil.
- Damage Reduction: Reports of coil damage during transit decreased by over 60%, significantly reducing replacement costs and material waste.
- Transportation: Improved package density allowed for an average 10% increase in coils per truckload, lowering transport emissions and costs.
This real-world example underscores the substantial, measurable benefits automation delivers in reducing waste, lowering costs, and improving overall sustainability.
Conclusion: Embracing Automation for a Greener Steel Industry
As the global focus on sustainable practices intensifies, the steel industry has a significant opportunity to reduce its environmental footprint through optimized packaging. Automated packaging systems offer a proven, effective solution to minimize resource waste, decrease energy consumption, enhance packaging consistency, and improve transportation efficiency.
By leveraging precision engineering, energy-efficient designs, smart technology, and compatibility with sustainable materials, automation transforms steel coil packaging from a potential source of waste into a streamlined, eco-conscious operation. Companies that invest in automation not only contribute positively to environmental goals but also gain a competitive edge through cost savings, improved operational efficiency, and enhanced brand reputation. Adopting these technologies is crucial for achieving long-term sustainability and operational excellence in the modern steel industry.