Mastering Large Load Packaging: An In-Depth Look at Horizontal Orbital Stretch Wrappers
Wrapping large, long, or irregularly shaped products presents unique challenges in industrial packaging. Standard pallet wrappers are often unsuitable for items like lumber, pipes, extrusions, assembled furniture, or large rolls of textiles. This is where the horizontal orbital stretch wrapper provides an effective and efficient solution.
Unlike conventional turntable or rotary arm wrappers that rotate the load itself, a horizontal orbital stretch wrapper keeps the product stationary (often moving linearly on a conveyor) while a ring carrying the stretch film roll rotates around the item. This orbital motion allows for complete encapsulation of long or bulky products with stretch film, providing stability, protection, and unitization.
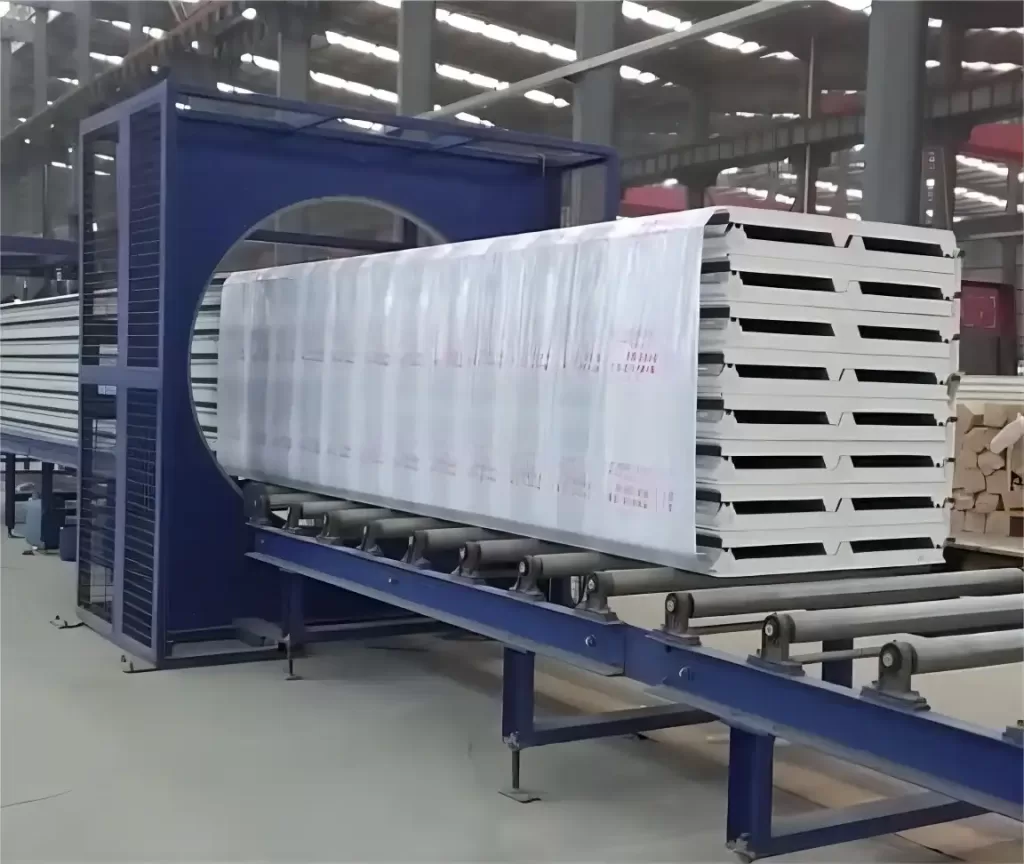
How Horizontal Orbital Stretch Wrappers Work
The typical operational sequence involves:
- Infeed: The product is fed into the wrapping zone, usually via powered conveyors.
- Wrapping Cycle: As the product moves through the machine's ring opening, the rotating ring dispenses stretch film, applying it around the circumference of the load. The film is typically pre-stretched for better material efficiency and load containment.
- Film Management: The machine automatically clamps, cuts, and seals the film at the beginning and end of the cycle.
- Outfeed: The fully wrapped product exits the machine, ready for storage or transport.
Advanced systems offer programmable wrap patterns, adjustable film tension, and variable rotation speeds to accommodate different product types and protection requirements.
Key Technical Specifications and Considerations
While specifications vary greatly depending on the specific model and manufacturer, typical parameters illustrate the capabilities of these machines:
Note: Specific parameters can vary significantly between models and manufacturers. The specifications listed below are illustrative examples.
Type: Horizontal Orbital Stretch Wrapper
Package Size Compatibility: Designed for large/long items. Handles varying dimensions, e.g., Length up to 6000mm; Width up to 1200mm; Height up to 1200mm. Ensure the machine's ring diameter accommodates your largest product cross-section.
Wrapping Material: Typically Linear Low-Density Polyethylene (LLDPE) stretch film. Compatibility with specific film gauges and pre-stretch levels is important. [External Link Placeholder: Authoritative Source on Stretch Film Properties]
Maximum Film Roll Diameter: Determines how long the machine can run unattended, e.g., 500mm.
Film Roll Width: Common widths range up to 750mm, influencing coverage per rotation.
Rotation Speed: Adjustable, often up to 15 RPM or higher, impacting throughput.
Power Requirements: Varies based on machine size and features; often 380V, 50Hz, three-phase in industrial settings.
Machine Dimensions (Approximate): Footprint varies considerably, e.g., Length: 4000mm; Width: 2500mm; Height: 2200mm.
Machine Weight (Approximate): Can be substantial, e.g., 1500kg (highly variable).
Control System: Typically PLC (Programmable Logic Controller) controlled with an HMI (Human-Machine Interface), often a touchscreen, for setting parameters and diagnostics.
Safety Features: Essential systems include guard enclosures around the rotating ring, safety interlocks on access doors, clearly marked emergency stop buttons, and light curtains. [External Link Placeholder: Link to relevant safety standards, e.g., PMMI B155.1]
Potential Throughput: Production rates can range up to 50 packages per hour or more, heavily dependent on product length, required wrap pattern, and conveyor speed.
Warranty: Standard manufacturer warranties are typically provided (e.g., 1-2 years).
horizontal orbital stretch wrapper with timber feeder and strapping machine Core Benefits of Using Horizontal Orbital Wrappers
Employing this technology offers several advantages:
- Load Stability: Securely bundles long or awkward items, preventing shifting during handling and transit.
- Enhanced Protection: Provides full coverage, shielding products from dust, moisture, dirt, and minor abrasions. Opaque film options can also offer UV protection or conceal contents.
- Increased Efficiency: Automates a previously manual or difficult wrapping process, increasing throughput and reducing labor costs.
- Versatility: Handles a wide range of product shapes and sizes that cannot be processed on traditional wrapping equipment.
Common Industry Applications
Horizontal orbital stretch wrappers are invaluable in various sectors:
Building Supplies and Construction
Securely bundles and protects long items like timber, lumber packs, PVC pipes, metal extrusions, and conduit. Wrapping ensures bundles remain intact and protected from weather exposure during transport and yard storage.
Furniture Manufacturing
Provides protective packaging for large, assembled pieces such as sofas, cabinets, tables, and mattresses. The wrap conforms to irregular shapes, preventing scratches, scuffs, and dust accumulation during shipping and warehousing.
Textiles and Rolled Goods
Effectively wraps large rolls of fabric, carpets, nonwovens, or artificial turf. This maintains cleanliness, prevents telescoping of rolls, and protects materials from environmental factors, preserving quality.
Other Industries
Used for packaging doors, windows, metal sheeting, automotive parts, and other large or elongated products requiring secure unitization and protection.
Considerations When Selecting a System
Choosing the right horizontal orbital wrapper involves evaluating:
- Load Dimensions & Weight: Ensure the machine's ring diameter and conveyor capacity match your product range.
- Speed Requirements: Match the machine's throughput capabilities to your production line's output.
- Automation Level: Determine the need for fully automatic operation, including integration with existing conveyor systems.
- Film Specifications: Consider required film type, thickness (gauge), and pre-stretch capabilities.
Maintenance and Safe Operation
Like all industrial machinery, regular maintenance according to the manufacturer's guidelines is crucial for reliable performance and longevity. Adherence to safety protocols, including proper operator training, use of safety guards, and awareness of emergency stop procedures, is paramount to prevent accidents.
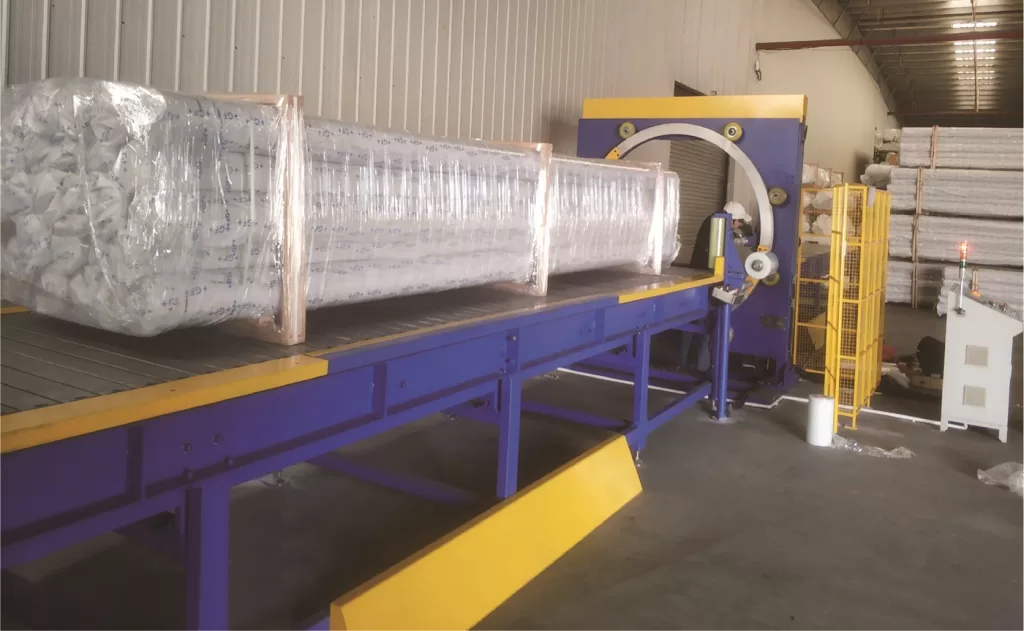
Conclusion
Horizontal orbital stretch wrappers offer a specialized and highly effective solution for packaging large, long, and challenging loads. By securely wrapping products that are difficult or impossible to handle on conventional equipment, these machines enhance product protection, improve load stability, increase operational efficiency, and provide versatility across numerous industries. Understanding their operation, capabilities, and benefits is key for manufacturers and distributors dealing with oversized goods.