
1. High-Efficiency Rope Wire Coil Wrapping Machine: A Guide for Cable and Wire Manufacturers
In the competitive landscape of industrial manufacturing, maximizing efficiency and ensuring precision are non-negotiable. For cable and wire manufacturers, the packaging of rope wire coils represents a critical operational step influencing both productivity and final product integrity. The advent of the high-efficiency rope wire coil wrapping machine marks a significant advancement, offering automated solutions that enhance operations. This guide explores this innovative technology and its transformative impact on industrial cable and wire packaging processes.
2. Understanding the Importance of Effective Coil Wrapping
Before examining the machinery, it's essential to grasp why effective coil wrapping is vital in the cable and wire sector. Rope wire coils serve diverse applications, including construction, maritime operations, industrial equipment, and telecommunications. Proper packaging ensures these coils are:
- Protected from environmental elements like moisture, dust, and corrosion.
- Securely wrapped to prevent unwinding during handling, transport, and storage.
- Maintained in their intended shape and structural integrity.
- Easily identifiable and manageable for downstream processes and end-users.
Inadequate or inconsistent wrapping can lead to product damage, material waste, operational delays, and ultimately, diminished customer satisfaction. High-efficiency wrapping machines provide a reliable solution to mitigate these risks.
3. The Evolution of Coil Wrapping Technology
The path to modern automated wrapping systems reflects continuous industrial innovation:
- Manual Wrapping: Highly labor-intensive, prone to inconsistency, and slow.
- Semi-Automatic Machines: Introduced better consistency but still required considerable operator involvement.
- Automatic Single-Axis Machines: Increased throughput but offered limited wrapping pattern flexibility.
- Multi-Axis Automatic Machines: Provided enhanced adaptability and precision for comprehensive wrapping coverage.
- Smart, Connected Wrapping Systems: Represent the current state-of-the-art, incorporating data analytics, IoT connectivity, and integration with broader manufacturing systems (Industry 4.0).
This progression highlights the industry's drive towards greater automation, efficiency, reliability, and quality in coil packaging.
4. Key Features of Modern High-Efficiency Rope Wire Coil Wrapping Machines
Contemporary high-efficiency wrapping machines integrate numerous advanced features that distinguish them from older technologies. Understanding these capabilities is key to selecting the right equipment:
4.1. Multi-Axis Wrapping Capability
Unlike simpler machines, advanced systems operate along multiple axes, enabling:
- Complete Coverage: Ensures the wrapping material covers the entire coil surface, including inner and outer diameters and faces.
- Sophisticated Wrapping Patterns: Allows for customized patterns that provide targeted protection and stability.
- Adaptability: Easily adjusts to various coil dimensions (diameter, height, weight) and shapes.
This capability guarantees thorough protection and secure packaging regardless of the coil's specifications.
4.2. Automated Loading, Unloading, and Handling Systems
Efficiency gains begin with automated material handling. Leading machines often feature:
- Robotic Integration: Arms or grippers for precise coil loading onto the wrapping station and unloading afterwards.
- Conveyor Integration: Seamless movement of coils into and out of the wrapping zone, often connecting directly to upstream and downstream processes.
- Automatic Adjustment: Sensors detect coil dimensions and automatically select the appropriate wrapping program or parameters.
These features significantly increase throughput, reduce manual labor requirements, enhance operator safety by minimizing heavy lifting, and decrease the risk of handling errors.
4.3. Precision Tension Control
Applying the correct wrapping material tension is critical—too loose, and the coil isn't secure; too tight, and the product can be damaged. Look for systems with:
- Dynamic Tension Adjustment: Automatically modifies tension based on the coil section being wrapped (e.g., tighter on the outer layers, gentler near the core).
- Programmable Tension Settings: Allows for different tension profiles based on product type and material characteristics.
- Real-Time Monitoring: Sensors provide feedback to ensure consistent tension application throughout the cycle.
Optimal tension control secures the coil effectively while preserving the integrity of the underlying wire or cable.
4.4. Versatile Wrapping Material Compatibility
Different applications demand different protective materials. High-efficiency machines are designed for flexibility:
- Broad Material Range: Compatible with various wrapping materials like stretch film (LLDPE), VCI (Vapor Corrosion Inhibitor) film, woven fabric, crepe paper, or HDPE.
- Quick Material Changeover: Systems designed for efficient switching between material types or roll sizes.
- Optimized Dispensing: Mechanisms adjust to handle the specific properties of different materials effectively.
This versatility allows manufacturers to select the ideal wrapping solution for each product without requiring dedicated machines for each material type.
4.5. Integrated Quality Control and Data Systems
Maintaining packaging quality and process traceability is crucial. Advanced machines often incorporate:
- Vision Systems: Cameras for inspecting wrap quality, detecting defects, or verifying label placement.
- Integrated Labeling/Marking: Automatic application of labels, barcodes, or direct marking on the wrap for identification and tracking.
- Weight Verification: Checkweighing systems to confirm proper material usage or product weight.
- Data Logging: Recording key process parameters (tension, material usage, cycle time) for each coil.
These features support quality assurance programs, facilitate regulatory compliance, and provide valuable data for process analysis.
4.6. User-Friendly HMI and Controls
Ease of operation is essential for maximizing uptime and minimizing errors. Modern machines typically include:
- Touchscreen Interfaces (HMI): Intuitive graphical displays for machine setup, operation, and diagnostics.
- Recipe Management: Storage of pre-programmed wrapping parameters for different coil types, enabling quick changeovers.
- Multi-Language Support: Accommodates diverse workforces.
- Remote Access/Monitoring: Allows for off-site diagnostics and performance tracking.
User-friendly controls reduce operator training time and empower staff to manage the machine effectively.
4.7. Data Collection and Connectivity (Industry 4.0 Ready)
Integration into the broader manufacturing ecosystem is increasingly important. High-efficiency machines offer:
- Real-Time Performance Monitoring: Dashboard displays of key performance indicators (KPIs) like OEE (Overall Equipment Effectiveness).
- Production Reporting: Automatic generation of logs detailing throughput, material consumption, and downtime.
- MES/ERP Integration: Connectivity protocols (like OPC-UA) to exchange data with Manufacturing Execution Systems or Enterprise Resource Planning software.
Leveraging this data enables manufacturers to optimize wrapping processes, schedule maintenance proactively, and make informed decisions to improve overall plant efficiency.
5. Benefits of Investing in High-Efficiency Rope Wire Coil Wrapping Technology
Adopting automated, high-efficiency wrapping solutions delivers significant operational advantages:
5.1. Dramatic Increase in Productivity and Throughput
Automated systems operate significantly faster than manual or semi-automatic methods. Depending on the machine configuration and coil size, throughput can reach 30-60+ coils per hour, drastically increasing packaging capacity and reducing bottlenecks.
5.2. Substantial Reduction in Labor Costs
Automation minimizes the need for manual labor in the wrapping process. A single automated machine can often perform the work of multiple operators, freeing up personnel for higher-value tasks and reducing direct labor expenses.
5.3. Enhanced Product Protection and Packaging Quality
Machine-controlled wrapping ensures consistency and precision unmatched by manual methods:
- Uniform Application: Consistent tension and overlap provide reliable protection.
- Reduced Damage: Minimizes the risk of coil damage during handling, shipping, and storage.
- Improved Aesthetics: Professional, consistent packaging enhances brand perception.
Better protection leads to fewer product returns, reduced scrap, and increased customer satisfaction.
5.4. Improved Workplace Safety
Automating the handling and wrapping of heavy, potentially cumbersome wire coils significantly reduces ergonomic risks and manual handling injuries. This leads to:
- Fewer lost-time incidents.
- Reduced worker fatigue.
- Lower potential for workers' compensation claims.
Creating a safer work environment is a crucial benefit of automation.
5.5. Material Optimization and Waste Reduction
High-efficiency machines are engineered for optimal material usage:
- Precise Control: Apply only the necessary amount of wrapping material.
- Reduced Waste: Minimizes film breaks, inconsistent wraps, and excess material usage compared to manual methods.
- Cost Savings: Lower consumption of stretch film, paper, or other materials directly impacts operating costs.
- Sustainability: Contributes to environmental goals by reducing packaging waste.
5.6. Flexibility to Handle Diverse Product Ranges
Modern wrapping machines offer significant adaptability:
- Wide Range Capability: Can often handle coils of varying diameters, heights, and weights within a single machine.
- Multiple Materials: Easily switch between different wrapping materials based on product requirements.
- Quick Changeovers: Recipe management allows rapid adjustments for different product lines.
This flexibility ensures the investment remains valuable even as production needs evolve.
5.7. Data-Driven Process Improvement and Traceability
The data generated by smart wrapping systems enables continuous improvement:
- Identify Inefficiencies: Pinpoint bottlenecks or areas for optimization in the packaging process.
- Optimize Settings: Fine-tune machine parameters for specific products to maximize quality and efficiency.
- Track Performance: Monitor OEE and other KPIs to measure progress and justify the investment.
- Enhance Traceability: Log wrapping parameters for each coil, supporting quality control and troubleshooting efforts.
6. Factors to Consider When Selecting a Rope Wire Coil Wrapping Machine
Choosing the right machine requires careful evaluation of your specific needs and operational context:
6.1. Production Volume and Speed Requirements
Analyze current output and project future growth. Select a machine with sufficient capacity (coils per hour) to meet peak demand, considering loading/unloading cycle times as part of the overall throughput calculation.
6.2. Coil Specifications
Document the full range of coils to be wrapped:
- Minimum and maximum diameter.
- Minimum and maximum height/width.
- Minimum and maximum weight.
- Material type (wire, cable, hose, etc.) and any specific handling sensitivities.
Ensure the machine's specifications comfortably accommodate your entire product range.
6.3. Wrapping Material Requirements
Identify the types of wrapping materials you currently use or plan to use (e.g., stretch film gauge and width, paper type, VCI requirements). Verify the machine's compatibility and ease of changeover between material types.
6.4. Facility Layout and Space Constraints
Measure the available floor space, considering not just the machine footprint but also necessary clearances for operation, maintenance access, coil staging (infeed/outfeed), and material storage.
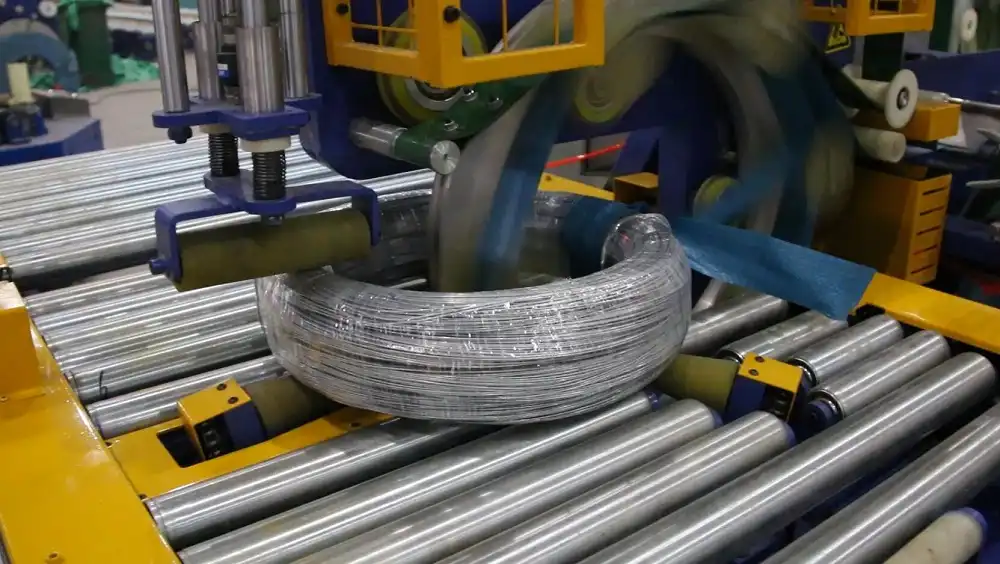
6.5. Integration with Existing Production Lines
Evaluate how the wrapping machine will interface with upstream (e.g., coiling/spooling lines) and downstream (e.g., palletizing, warehousing) systems. Consider conveyor heights, communication protocols, and overall workflow compatibility.
6.6. Manufacturer Reputation, Service, and Support
Research potential suppliers. Consider:
- Their experience in the cable and wire industry.
- Customer references and case studies.
- Availability of local technical support, spare parts, and service technicians.
- Warranty terms and post-installation support programs. Reliable support is critical for minimizing downtime.
6.7. Total Cost of Ownership (TCO)
Look beyond the initial purchase price. Factor in:
- Installation and commissioning costs.
- Energy consumption.
- Consumable costs (wrapping materials).
- Maintenance requirements (preventive maintenance schedule, spare parts cost).
- Operator training costs.
- Expected machine lifespan and potential upgrade paths. Calculate the projected Return on Investment (ROI) based on labor savings, material savings, productivity gains, and quality improvements.
6.8. Ease of Use and Training Requirements
Assess the machine's control system (HMI) intuitiveness. Consider the level of training required for operators and maintenance staff. User-friendly machines lead to faster adoption and fewer errors.
7. Implementing Your New Wrapping Machine: Best Practices
Successful implementation is key to realizing the full benefits of your investment:
7.1. Thorough Site Preparation
Ensure the installation area is ready before the machine arrives:
- Confirm adequate and properly located utilities (electrical power, compressed air).
- Verify floor loading capacity and levelness.
- Plan clear access routes for machine delivery and installation.
- Prepare foundations or mounting points as required.
7.2. Comprehensive Staff Training
Invest time in training personnel:
- Utilize manufacturer-provided training for operators on machine setup, operation, recipe management, and basic troubleshooting.
- Ensure maintenance staff receive detailed training on mechanical and electrical systems, preventive maintenance procedures, and diagnostics.
- Develop clear Standard Operating Procedures (SOPs) for consistent operation.
7.3. Pilot Testing and Process Optimization
Before full production integration, conduct thorough testing:
- Run trials with representative samples of all coil types.
- Fine-tune wrapping recipes (tension, overlap, number of wraps) to achieve optimal package quality and material usage for each product.
- Validate integration with upstream/downstream equipment.
- Collect baseline performance data.
This phase helps identify and resolve any unforeseen issues and ensures the machine meets your specific requirements.
7.4. Establish a Robust Preventive Maintenance Plan
Proactive maintenance is crucial for longevity and reliability:
- Follow the manufacturer's recommended maintenance schedule diligently.
- Keep essential spare parts in stock to minimize downtime during repairs.
- Train maintenance staff on routine checks and lubrication.
- Maintain a log of all maintenance activities.
steel wire packing machine with paper2 8. Future Trends in Rope Wire Coil Wrapping Technology
The technology continues to evolve. Keep an eye on these emerging trends:
8.1. Artificial Intelligence (AI) and Machine Learning (ML)
Future systems may leverage AI/ML for:
- Self-Optimization: Automatically adjusting wrapping parameters based on real-time sensor feedback for optimal performance.
- Predictive Maintenance: Analyzing machine data to anticipate potential failures before they occur.
- Adaptive Control: Modifying operations dynamically based on upstream/downstream conditions.
8.2. Enhanced Sustainability Features
Growing environmental focus drives innovation in:
- Material Reduction: Advanced algorithms and tension control to use even less wrapping material effectively.
- Eco-Friendly Materials: Increased compatibility with biodegradable, recycled-content, or thinner-gauge films and papers.
- Energy Efficiency: Motors, drives, and operating modes designed to minimize power consumption.
8.3. Augmented Reality (AR) for Operations and Maintenance
AR technology could offer:
- Guided Procedures: Overlaying digital instructions onto the physical machine for complex tasks like maintenance or changeovers.
- Remote Assistance: Enabling experts to guide on-site technicians remotely.
- Enhanced Training: Providing immersive, interactive learning experiences.
8.4. Increased Modularity and Customization
Expect greater flexibility in machine design:
- Modular Components: Allowing easier upgrades or modifications as needs change.
- Broader Application Range: Machines capable of handling an even wider variety of coil sizes, shapes, and weights.
- Robotic Integration: Tighter and more seamless integration with robotic handling systems. For more information on industry automation trends, consult resources like the Association for Advancing Automation (A3).
Considering these trends can help inform purchasing decisions for long-term value.
9. Case Studies: Realizing Value with Advanced Coil Wrapping
Examining real-world examples illustrates the impact of this technology:
9.1. Company A: Boosting Productivity in Electrical Wire Manufacturing
A mid-sized electrical wire producer implemented a modern multi-axis automatic coil wrapper. Key results included:
- 50% increase in packaging throughput compared to their previous semi-automatic system.
- 30% reduction in stretch film consumption due to optimized tension control and wrapping patterns.
- Reassignment of two full-time operators previously dedicated to manual wrapping tasks.
- Achieved a full Return on Investment (ROI) within 14 months.
The manufacturer cited the consistent wrap quality and reliability as major factors in improving customer satisfaction.
9.2. Company B: Enhancing Safety and Quality in Industrial Cable Production
A large manufacturer of heavy industrial cables upgraded to a fully automated wrapping line with integrated safety features and data connectivity. Notable benefits were:
- 70% decrease in reported manual handling incidents related to coil packaging.
- Significant improvement in package integrity during cross-country shipping, reducing damage claims.
- Utilization of real-time production data to optimize line balancing, contributing to a 15-20% increase in overall line efficiency.
- Enhanced traceability for quality assurance purposes.
This company emphasized the safety improvements and the value of actionable data provided by the system. You can often find video demonstrations of such systems in action:
10. Conclusion: Embracing Efficiency in Rope Wire Coil Wrapping
Investing in a high-efficiency rope wire coil wrapping machine represents a strategic move towards operational excellence for cable and wire manufacturers. It's an investment in enhanced productivity, superior product protection, improved workplace safety, reduced operating costs, and future readiness.
As outlined, modern automated wrapping systems offer a multitude of features and benefits that directly address the challenges of industrial packaging. The key to success lies in carefully evaluating your specific requirements, selecting the appropriate technology, and implementing it effectively within your production environment. Consider exploring related resources on packaging line optimization for further insights.
By adopting advanced coil wrapping technology, manufacturers can achieve a significant competitive advantage. Taking the time to research options, consult with suppliers, and plan for integration will position your company to reap the rewards of efficiency, quality, and reliability in your coil packaging operations for years to come.