Design of the Hydraulic System Structure for a Fully Hydraulic Truck Bogie Upender
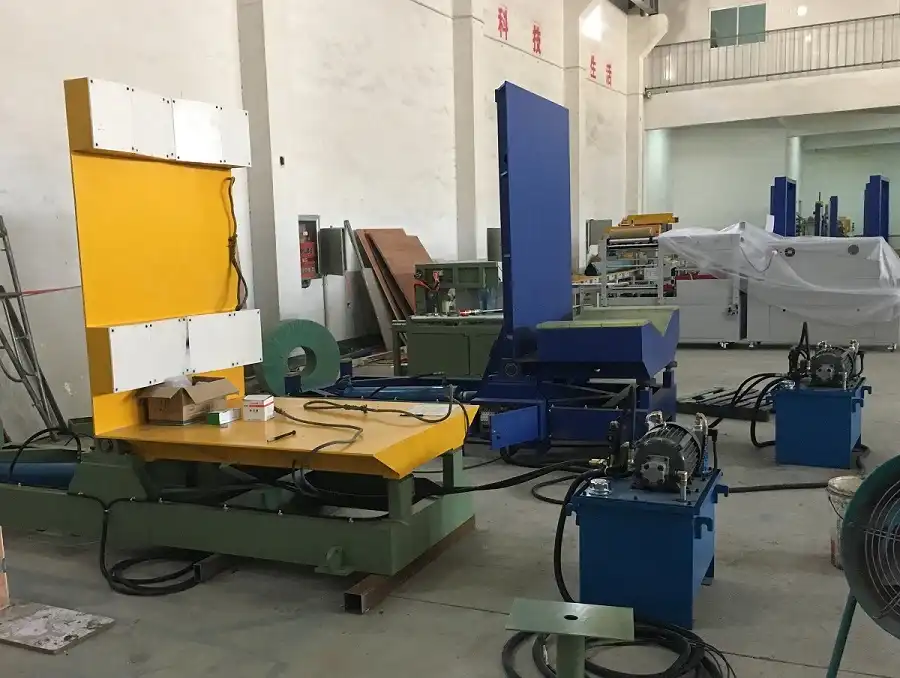
1. Introduction: The Crucial Role of Hydraulics in Truck Bogie Upenders
The design and optimization of the hydraulic system structure within a fully hydraulic truck bogie upender are paramount to its functionality, safety, and efficiency. A truck bogie upender is specialized industrial equipment designed to lift, rotate, and reposition heavy truck or railway bogies (wheelsets with frames) for assembly, maintenance, or inspection. Given the immense weight and awkward geometry of bogies, the hydraulic system provides the necessary force and precise control for these demanding operations.
Recent advancements in hydraulic technology have led to significant improvements over traditional models, enhancing the system's reliability and broadening its applicability. These optimizations not only improve current industrial processes but also pave the way for future innovations in heavy machinery hydraulics.
The mechanical industry remains a cornerstone of economic strength and technological progress. As global competition intensifies, refining core equipment like bogie upenders is critical. Manufacturers must meet stringent performance standards demanded by large-scale production and maintenance facilities, making sophisticated hydraulic system design an urgent priority.
Modern hydraulics integrates seamlessly with microelectronics, computer controls, and sensor technology, creating comprehensive automation systems. Today's hydraulic systems excel in:
- High-Pressure & High-Power Performance: Delivering substantial force reliably.
- Speed & Precision: Enabling rapid yet controlled movements.
- Durability & Longevity: Ensuring long operational life under heavy loads.
- Compactness: Offering high power density in relatively small footprints.
Key technological advancements influencing hydraulic design include proportional and servo control, digital monitoring, computer-aided design (CAD), computer-aided testing (CAT), mechatronics integration, and a strong focus on energy efficiency and contamination control.
2. Understanding the Demands: Handling Truck Bogies
Designing an effective hydraulic system for a bogie upender requires addressing specific challenges:
- Heavy Loads: Truck bogies can weigh several tons, demanding robust lifting and rotating mechanisms.
- Complex Geometry: Bogies have irregular shapes and centers of gravity, requiring stable and controlled rotation to prevent damage or instability.
- Precision Requirements: Accurate positioning is often needed for maintenance or assembly tasks.
- Safety Criticality: Uncontrolled movement could lead to severe accidents or equipment damage.
The hydraulic system must be engineered to meet these demands reliably and consistently.
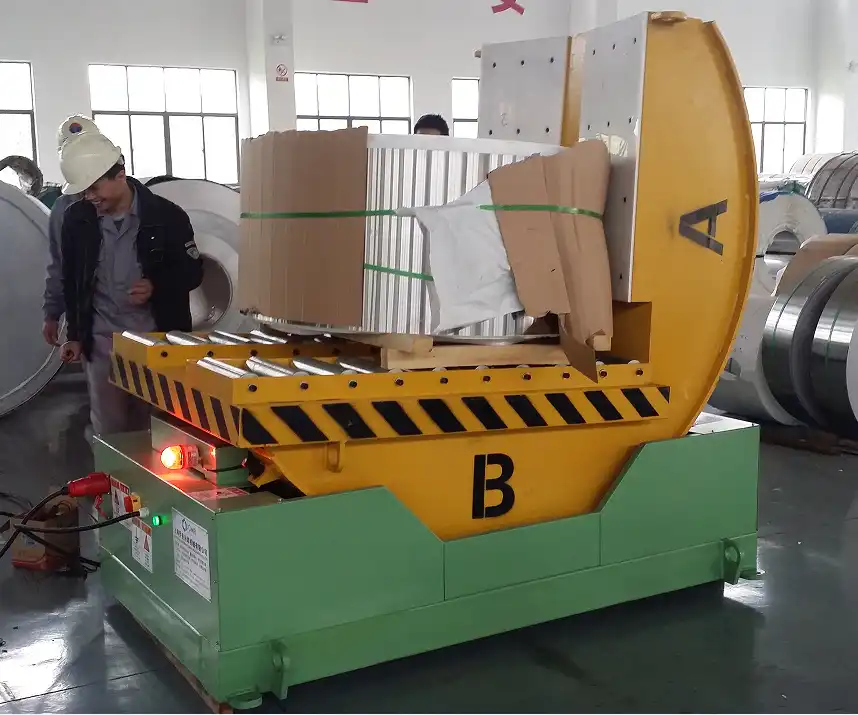
3. Key Components and Design Enhancements of the Hydraulic System
The hydraulic system of a modern truck bogie upender is a sophisticated assembly designed for optimal performance. Key design considerations and enhancements include:
3.1. High-Capacity Hydraulic Drive System
This is the heart of the upender, providing the power for lifting and rotation.
- Components: Typically includes high-pressure hydraulic pumps (e.g., variable displacement piston pumps for efficiency), hydraulic motors or cylinders for actuation, and associated control valves.
- Optimization: Designed to deliver consistent torque and smooth acceleration/deceleration, even under maximum load. Variable displacement pumps adjust flow based on demand, saving energy during idle periods or lighter operations.
3.2. Precision Control: Proportional and Servo Valves
Achieving smooth, accurate movement requires advanced control elements.
- Proportional Control: Allows for variable adjustment of speed and force, giving operators fine control over the rotation and tilting process. This prevents jerky movements that could destabilize the load.
- Servo Control: Offers higher accuracy and faster response times, enabling precise positioning and dynamic adjustments to compensate for shifting loads or complex maneuvers. Essential for applications requiring exact orientation.
3.3. Integrated Digital Control and Monitoring
Modern systems leverage digital technology for enhanced operation and maintenance.
- Real-Time Monitoring: Sensors track critical parameters like pressure, temperature, fluid level, and filter condition. This data is displayed to the operator and logged for analysis.
- Automated Adjustments: Control systems (often PLC-based) can automatically adjust parameters to maintain optimal performance and prevent damage (e.g., reducing speed if overheating is detected).
- Diagnostics: Facilitates easier troubleshooting by providing detailed system status and error codes, reducing downtime.
3.4. Robust Filtration and Sealing
Maintaining hydraulic fluid cleanliness and system integrity is vital for longevity.
- Advanced Filtration: Multi-stage filtration systems (e.g., suction strainers, pressure filters, return line filters) remove contaminants that can damage sensitive components like pumps and servo valves.
- High-Quality Seals: Advanced seal materials and designs prevent internal and external leakage, ensuring consistent pressure, reducing fluid consumption, and preventing environmental contamination.
3.5. Safety Mechanisms and Interlocks
Safety is paramount when handling heavy loads.
- Overload Protection: Pressure relief valves prevent the system from exceeding maximum safe operating pressures.
- Load-Holding Valves: Counterbalance valves or pilot-operated check valves prevent the load from drifting down or rotating unexpectedly if hydraulic pressure is lost.
- Emergency Stops: Easily accessible E-stop buttons immediately halt all hydraulic functions.
- Interlocks: May prevent operation unless safety gates are closed or the bogie is correctly positioned.
- Mechanical Locking: Some designs incorporate mechanical locks to secure the load in a specific position for extended periods or maintenance.
3.6. Modular and Compact Architecture
Flexibility and ease of maintenance are key design goals.
- Modular Design: Components are often grouped into modules (e.g., power unit, valve block), simplifying assembly, maintenance, and potential upgrades.
- Compact Footprint: Efficient layout minimizes the space required for the hydraulic system, important in often-crowded industrial environments.
3.7. Energy-Efficient Design Considerations
Reducing operational costs and environmental impact is increasingly important.
- Efficient Components: Use of variable speed drives for pumps, energy-efficient motors, and correctly sized components minimizes energy consumption.
- Load Sensing Systems: Pumps only generate the required pressure and flow needed for the current operation, reducing wasted energy.
- Fluid Management: Systems designed to minimize fluid degradation and leakage contribute to sustainability.
4. Importance of Advanced Hydraulic Technology in Heavy Industrial Applications
The widespread use of hydraulic technology in demanding industrial sectors highlights its indispensable role. For equipment like truck bogie upenders, hydraulics offers unparalleled advantages:
- High Power Density: Delivers significant force and torque from relatively compact components.
- Smooth & Precise Control: Enables fine adjustments in speed and position, crucial for handling heavy, sensitive loads.
- Robustness & Reliability: Hydraulic components are generally durable and capable of withstanding harsh industrial environments and heavy loads.
- Flexibility: Adaptable to various control strategies, from simple manual operation to sophisticated automated sequences.
The continuous integration of electronics and digital controls further enhances hydraulic system capabilities, leading to smarter, safer, and more efficient heavy machinery. Developments in CAD and simulation tools allow engineers to optimize designs for performance and reliability before physical prototyping. As industries move towards greater automation and sustainability, intelligent and efficient hydraulic systems will remain critical enablers.
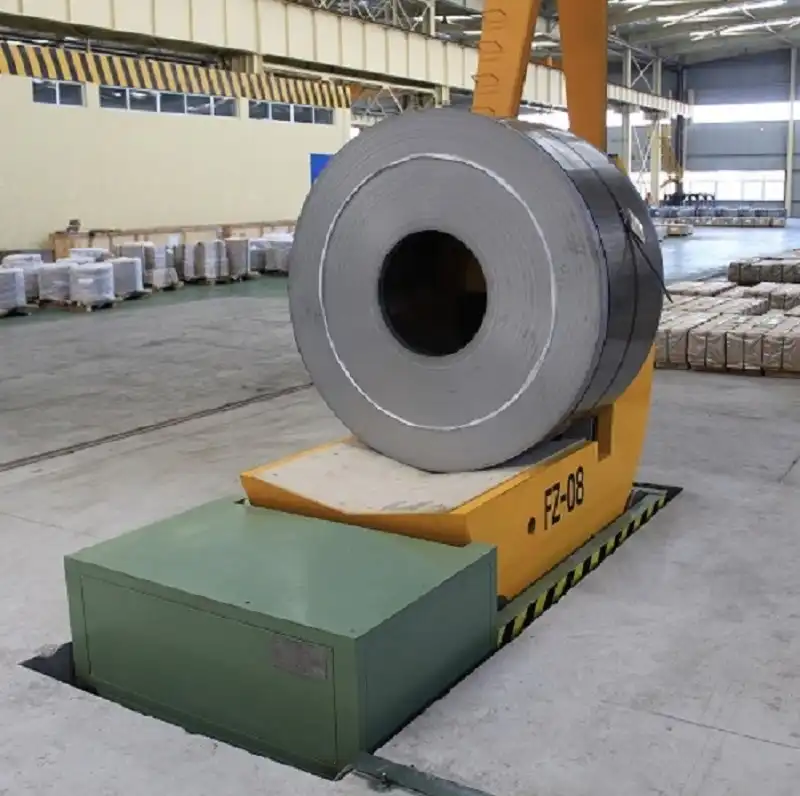
5. Conclusion: Optimizing Bogie Handling through Hydraulic System Design
The design of the hydraulic system structure for a fully hydraulic truck bogie upender is a critical factor in achieving safe, efficient, and precise operation. By incorporating optimized drive systems, advanced proportional and servo controls, digital monitoring, robust safety features, and energy-efficient components, modern upenders meet the rigorous demands of handling heavy truck bogies.
These advancements demonstrate the power and versatility of modern hydraulic technology in challenging industrial applications. As technology evolves, hydraulic systems will continue to be refined, offering even greater integration, intelligence, and efficiency, supporting the ongoing advancement of manufacturing, maintenance, and logistics operations worldwide.

Get Your Best Solution !