Optimizing Your Operations: Cold/Hot Rolled Coil Automatic Packing Line Specifications
This technical specification from the FHOPE team details the capabilities and requirements of an automatic packing line designed for various metal coils, including:
- Cold Rolled Coils: Accommodates various dimensions and specifications typical of cold-rolled steel.
- Hot Rolled Coils: Suitable for the unique characteristics of hot-rolled steel coils.
- Galvanized Coils: Designed to handle galvanized products requiring specific corrosion protection during packaging.
- Coated Coils: Compatible with painted or surface-treated coils demanding careful handling.
- Stainless Steel Coils: Capable of processing various grades and sizes of stainless steel.
Please note that adjustments can be configured based on specific operational needs and equipment variations.

I. Core Components of the Automatic Coil Packing Line
- 1. Main Wrapping Unit (1 set)
The heart of the steel coil packaging system, this orbital wrapper executes the primary packaging functions. It manages shuttle movement through the coil eye, applies packing material with controlled tension, and features automatic material feeding and cutting. The unit ensures precise positioning relative to the coil's outer diameter, making it ideal for efficiently and reliably packaging large master coils.
- 2. Coil Transport Trolleys (2 sets)
These specialized trolleys facilitate the efficient movement and handling of steel coils throughout the packaging process. Two trolleys enable a continuous workflow, transporting coils to and from the main wrapping unit, minimizing handling time and supporting potential 360-degree coil rotation requirements.
- 3. Equipment Operation Station (HMI Control) (1 set)
This station incorporates a Human-Machine Interface (HMI) for intuitive control and comprehensive monitoring of the entire packing line. The touchscreen interface allows operators to manage settings, adjust parameters, and monitor key performance indicators (speed, throughput, error alerts) in real-time, facilitating informed decisions and optimizing performance. Its user-friendly design streamlines operator training and enhances overall productivity.
- 4. Electrical Control Cabinet (with Air Conditioning Room) (1 set)
Housing essential electrical components like the PLC, inverters, and drives, this cabinet ensures reliable system operation. Built to industrial standards (IP55 rated), it provides protection against environmental factors and overheating (via integrated air conditioning), ensuring component longevity and system safety through organized electrical management.
- 5. Hydraulic System (1 set)
This system supplies the necessary hydraulic power for critical machine functions, such as orbital locking and precise positioning adjustments. It ensures smooth, controlled, and safe movements. The system includes a pump, filter, and hydraulic oil (4 liters), delivering the required force for efficient operation.
- 6. Spare Parts Kit (1 Year Supply) (1 set)
A comprehensive set of recommended spare parts sufficient for one year of typical operation is included. This proactive measure ensures that routine maintenance and unexpected repairs can be performed swiftly, minimizing operational downtime and maintaining consistent production flow. Having critical parts readily available enhances the line's overall reliability and efficiency.
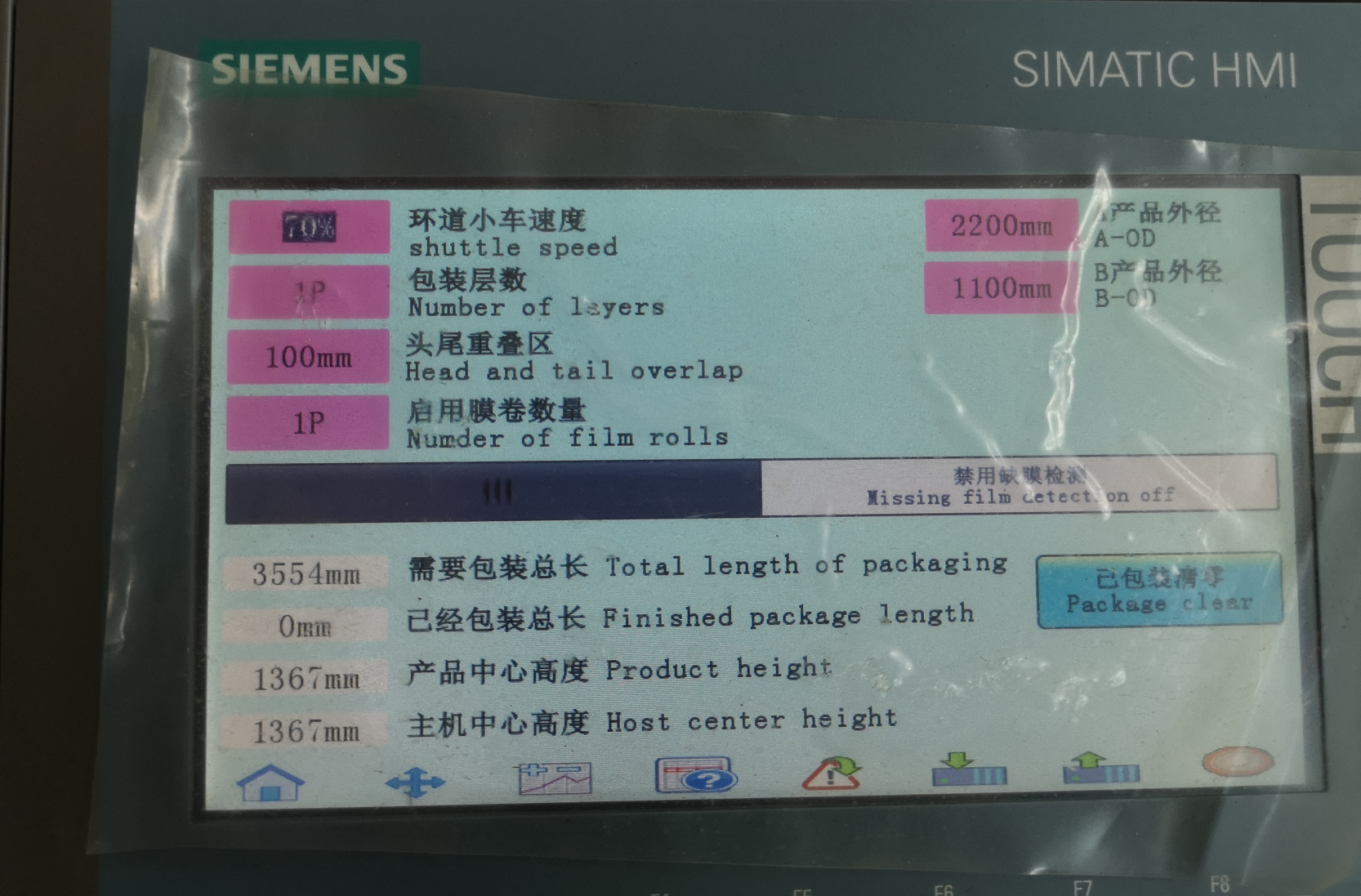
II. Key Functions and Capabilities of the FHOPE Automatic Packaging Line
Functional Highlights:
- 1. Automatic Centering and Wrapping
This feature ensures precision and operational ease. The system automatically centers the coil, initiates film loading, manages film breaking, and adjusts the wrapping height based on the coil's outer diameter for a tailored fit. It incorporates inner diameter verification and height adjustment capabilities, alongside precise tension control, guaranteeing optimal and secure wrapping for effective coil protection.
- 2. Integrated Safety Systems
Operator and equipment safety is paramount. The line includes robust safety features such as a physical safety fence (1800mm height), emergency stop switches, interlock systems, and light beam sensors. These components work together to create a secure operating environment, adhering to CE safety standards and allowing for immediate shutdown if necessary.
- 3. Packaging Throughput
Designed for efficiency, the line offers a packaging capacity of 10 coils per hour or more (subject to conditions outlined in section 6-5). This throughput capability ensures production demands are met consistently, optimizing resource utilization and contributing to overall operational efficiency.
- 4. Efficient Coil Handling with Dual Trolleys
The use of two packaging trolleys enables continuous operation. While one trolley is engaged in the wrapping cycle, the other can handle coil loading or unloading. This parallel processing maximizes efficiency, increases throughput, and significantly enhances productivity by minimizing idle time.
- 5. Dual Material Capability
The system supports the simultaneous application of two different types of packaging materials (e.g., stretch film and bubble film). This flexibility allows for tailored protection strategies based on the specific requirements of the coil product, ensuring optimal preservation during transport and storage.
- 6. Adjustable Overlap Control
The overlap rate of the packaging material is adjustable, typically within a range of 20-50% or more. This allows operators to customize the film application density, enhancing the protective barrier against environmental factors like moisture, dust, and physical impacts, ensuring package integrity.
- 7. Dual Control Options (HMI & Buttons)
The operation station features both an HMI touchscreen and a physical button control panel. This dual-interface design enhances usability, offering operators the choice between intuitive graphical control and quick, tactile button access for different operational scenarios.
- 8. Independent Operation Modes
The HMI and button controls can operate independently, providing maximum flexibility. Operators can utilize automated sequences via the HMI for routine tasks or switch to manual button control for specific adjustments or procedures, ensuring adaptability to various operational needs.

III. Coil Specification Requirements for Packaging
- 1. Coil Inner Diameter (ID)
Range: 500 mm - 850 mm
This range ensures compatibility with the packaging line's main wrapping unit and handling equipment, facilitating smooth passage through the coil eye during wrapping.
- 2. Coil Outer Diameter (OD)
Range: 800 mm - 1250 mm
Defining the maximum and minimum outer dimensions is crucial for ensuring the coil fits within the machine's processing envelope and allows for correct positioning and wrapping adjustments.
- 3. Coil Width
Maximum: 2000 mm (with capability for narrower coils, e.g., 600 mm)
The system is designed primarily for coils up to 2000 mm wide, accommodating standard industry sizes, while retaining flexibility for processing smaller width coils as needed.
- 4. Coil Weight
Maximum: Below 5 metric tons (5000 kg)
This weight limitation ensures the structural integrity and safe operation of the handling trolleys and wrapping machinery, aligning with equipment load capacities.
IV. Additional Technical and Service Requirements
- 1. Packaging Materials for Testing
Requirement: Sufficient packaging material (e.g., stretch film, bubble wrap) must be provided by the client for testing purposes throughout the commissioning phase until final equipment acceptance.
Rationale: Ensures the system can be thoroughly tested and validated using the actual materials intended for production before official handover.
- 2. Packaging Material Specifications
Reference: Detailed specifications for compatible packaging materials are provided in the accompanying attachment.
Importance: Adhering to these specifications (e.g., material type, thickness, roll dimensions) ensures optimal performance, avoids equipment jams, and guarantees the desired level of product protection.
- 3. Project Support Services
Scope: Service includes on-site installation supervision, full equipment commissioning by qualified technicians, and comprehensive operator training.
Benefit: Provides end-to-end support for a smooth transition from delivery to full operational capability, ensuring staff are proficient in safe and efficient equipment use.
- 4. PLC Program Access
Requirement: Full source code for the Programmable Logic Controller (PLC) program must be provided.
Value: Enables client-side technicians or approved third parties to understand the control logic for advanced troubleshooting, future modifications, or integration with other plant systems.
- 5. Documentation Requirements
Deliverables: Operation Manual, Spare Parts List, and Electrical/Circuit Diagrams.
Format: Must be provided in both physical hardcopy and digital PDF formats.
Purpose: Ensures essential documentation is readily accessible for operators and maintenance personnel, facilitating effective operation, training, and prompt repairs.
- 6. Labeling Language
Requirement: All labels on the operation station and electrical cabinets must be provided in English, Chinese, and Vietnamese.
Benefit: Enhances usability and safety for a multilingual workforce, ensuring clear understanding of controls, warnings, and component identification.
- 7. Power Supply Specifications
Standard: AC 380V, 50Hz, 3-phase power.
Note: Confirms the required electrical input for the equipment, ensuring compatibility with the site's power infrastructure for safe and correct operation.
- 8. Indicator Light Color Codes
Standard:
- Red: Equipment in Operation / Running
- Green: Equipment Stopped / Ready
- Yellow: Abnormal Condition / Fault / Warning
Purpose: Provides immediate, clear visual status updates to operators, enhancing situational awareness and safety around the machinery.
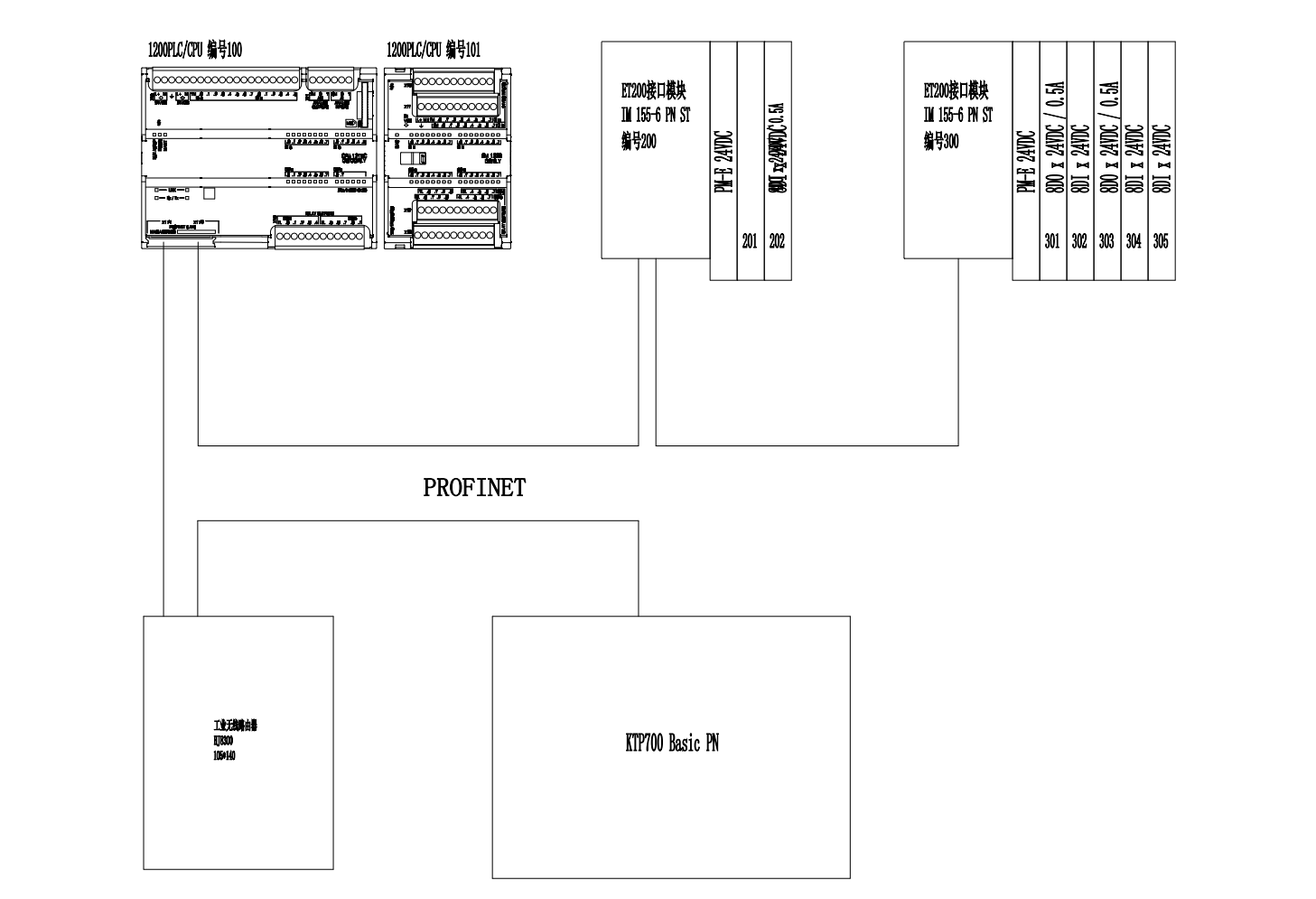
V. Documentation Standards: Operation Manual
1. Provision of Documentation
Comprehensive documentation, including the Operation Manual, Spare Parts List, and Circuit Diagrams, must be supplied in both physical hardcopy and universally accessible PDF format. This dual format ensures convenience for all users – hard copies for quick on-site reference during operation or maintenance, and digital PDFs for easy storage, sharing, and remote access. This documentation is vital for effective operator training, routine maintenance scheduling, and efficient troubleshooting.
2. Acceptance Criteria
Failure to provide the complete set of documentation (Operation Manual, Spare Parts List, Circuit Diagrams) in both specified formats (hardcopy and PDF) constitutes grounds for rejection of the equipment delivery. This strict requirement underscores the critical importance of documentation for safe, efficient, and sustainable operation. Lack of proper documentation can impede training, complicate maintenance, increase downtime, and potentially compromise safety.
3. Rationale
Complete and accessible documentation is fundamental to enabling users to operate, maintain, and troubleshoot the coil packing line effectively and safely throughout its lifecycle. It empowers maintenance teams with the necessary information (part numbers, wiring schematics) and provides operators with clear instructions and safety protocols. Shipments lacking this essential package may be deemed incomplete and unacceptable, potentially leading to operational delays and associated costs.