Optimizing Coil Handling: A Fabricator's Guide to Automatic Packing and Tapping Systems
Handling large, heavy coils of metal efficiently and safely is a critical aspect of modern metal fabrication and processing operations. Manual methods for packing and securing these coils can be time-consuming, labor-intensive, and pose potential safety risks. Automatic coil packing and tapping machines offer a robust solution, streamlining the end-of-line process, improving package quality, and enhancing overall productivity.
This guide explores the functions, benefits, and key considerations when implementing automated systems for coil packing (wrapping) and tapping.
Video demonstrating an automatic coil packing and tapping sequence.
The Challenge of Manual Coil Handling
Traditionally, securing coils for shipment or storage involves manual labor for wrapping protective materials and applying tape or strapping. This approach presents several challenges:
- Inconsistency: Manual wrapping can lead to variations in tension and coverage, potentially compromising protection.
- Speed Limitations: Manual processes are inherently slower, creating bottlenecks in high-volume production environments.
- Labor Costs: Significant manpower may be required, increasing operational expenses.
- Safety Concerns: Handling heavy coils and packaging materials manually increases the risk of worker injury.
Automated systems directly address these issues, offering a more controlled, efficient, and safer alternative.

Core Functionality: Automatic Coil Packing (Wrapping)
The primary function of an automatic coil packing machine, often referred to as a coil stretch wrapper, is to apply protective layers around the circumference and through the eye of the coil.
- Process: The machine typically rotates the coil or the wrapping mechanism around the coil, applying materials like stretch film, VCI (Volatile Corrosion Inhibitor) film, paper, or other protective layers.
- Benefits: This provides a tight, secure wrap that protects the coil from moisture, dust, scratches, and corrosion during handling, storage, and transportation. The automation ensures consistent tension and overlap for optimal protection.
Core Functionality: Automatic Coil Tapping
Once the coil is wrapped, the tapping machine secures the ends of the wrapping material or applies specific securing tapes.
- Process: An automatic tapping head precisely applies adhesive tape, such as BOPP (Biaxially Oriented Polypropylene) tape, to designated points on the wrapped coil. This often involves automatic positioning systems to ensure accuracy.
- Benefits: Tapping prevents the wrap from unraveling and can also be used to secure labels or documentation. Automating this step eliminates another manual touchpoint and ensures consistent tape application.
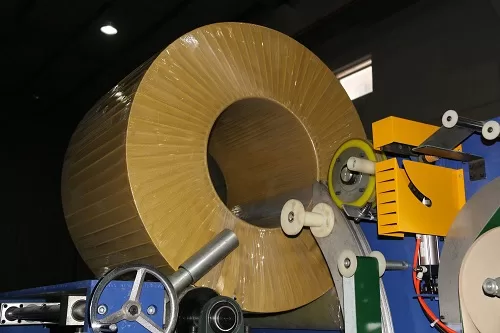
Key Technologies Driving Automation
Modern automatic coil packing and tapping systems rely on several core technologies to deliver performance and reliability:
- Programmable Logic Controllers (PLC): The "brain" of the system, controlling the sequence of operations, motor speeds, and positioning based on pre-programmed parameters.
- Human-Machine Interface (HMI): Touchscreen panels that allow operators to monitor the process, select recipes for different coil sizes, adjust settings, and troubleshoot issues.
- Servo Motors & Drives: Provide precise control over the speed and position of rotating elements (like the coil support or wrapping arm) and linear actuators (like the tapping head).
- Sensors: Detect coil presence, dimensions, and position, ensuring accurate wrapping and tapping cycles.
- Mechanical Guides & Positioning Systems: Ensure the coil is correctly centered and supported during the automated process.
Selecting the Right Automated System: Key Considerations
Choosing the appropriate automatic coil packing and tapping equipment requires careful evaluation. Here are critical factors to consider to Automate Coil Packing effectively:
1. Performance: Speed and Accuracy
- Throughput Needs: Evaluate the required cycles per hour based on your production output.
- Positioning Precision: Ensure the machine can accurately handle your range of coil diameters, widths, and weights for consistent wrapping and tapping. Look for systems with robust servo motor control and reliable sensor technology.
2. Reliability: Durability and Uptime
- Construction Quality: Assess the build quality, materials used (e.g., heavy-duty steel frame), and the reputation of component suppliers.
- Maintenance Requirements: Understand the recommended preventative maintenance schedule and the ease of accessing service points. Well-built machines minimize downtime.
3. Operational Simplicity: Ease of Use
- Intuitive Interface (HMI): A clear and user-friendly HMI reduces training time and minimizes operator errors.
- Changeover Time: If handling various coil sizes, evaluate how quickly and easily the machine can be adjusted.
4. Integration and Footprint
- System Compatibility: Consider how the machine will integrate with existing upstream (e.g., slitting lines, recoilers) and downstream (e.g., conveyors, palletizers) equipment. Compatibility with plant-level control systems (MES/ERP) might be necessary.
- Space Requirements: Ensure the machine's footprint fits within your available floor space, including allowances for safe operation and material staging.
5. Safety Features
- Guarding and Interlocks: Verify the presence of adequate physical guarding, safety interlocks on access doors, emergency stops, and potentially light curtains or safety scanners.
6. Customization and Flexibility
- Coil Specifications: Confirm the machine can handle your specific range of inner/outer diameters, widths, and maximum weights.
- Wrapping Materials: Ensure compatibility with the types of stretch film, VCI, or paper you intend to use.
Optimizing Workflow for Maximum Productivity
Simply installing automated equipment isn't enough; integrating it effectively into your workflow is crucial.
- Layout Planning: Position the system strategically to ensure smooth material flow from production to the packing station and onwards to storage or shipping. Allow adequate space for coil infeed and outfeed.
- Upstream/Downstream Synchronization: Ensure preceding and subsequent processes can keep pace with the automated packing system to avoid bottlenecks.
- Operator Training: Properly train personnel on machine operation, safety procedures, basic troubleshooting, and routine maintenance checks.
steel packing machine3 Tangible Benefits of Automation
Implementing automatic coil packing and tapping systems delivers significant advantages:
- Increased Throughput: Consistent, automated cycles significantly outperform manual methods, boosting overall output.
- Improved Package Quality: Uniform wrapping tension and precise tapping ensure better coil protection and a professional appearance.
- Reduced Labor Costs: Automating repetitive tasks frees up personnel for higher-value activities.
- Enhanced Worker Safety: Eliminates manual handling risks associated with heavy coils and repetitive motions.
- Minimized Material Waste: Controlled application of wrapping film and tape reduces overuse.
- Greater Consistency: Every coil is packed to the same standard, improving reliability and customer satisfaction.
By carefully selecting the right equipment and optimizing the surrounding workflow, manufacturers can leverage automatic coil packing and tapping machines to achieve substantial improvements in efficiency, quality, safety, and overall operational performance.