What Makes the Aluminum Profile High-Speed Wrapping Machine a Game Changer in Packaging?
In my work at FHOPEPACK, I often see how the packaging industry grows steadily. The Aluminum Profile High-Speed Wrapping Machine stands out among other packaging innovations. It is truly remarkable.
Many people ask why it matters. This machine increases efficiency and consistency for those who work with aluminum profiles. It offers speed, precision, and protection. It uses an advanced wrapping method that tightens and guards products. It significantly lowers labor costs. It reduces waste. It raises packaging standards across industries.
I want to share my findings on this machine. I will look at how it works. I will also highlight its benefits. Then I will explain how to choose the right model.
How Does the High-Speed Wrapping Machine Work for Aluminum Profiles?
I have seen many packaging machines in my time. This high-speed unit stands out. It handles aluminum profiles with a special method. Its flow is surprisingly straightforward. It saves time.
The machine uses rollers or conveyors to move profiles into position. Sensors check complete alignment before wrapping begins. Then the machine applies stretch film around the profiles. It secures each layer. The process is quick and neat. The tension adjusts automatically. This keeps the profiles safe from damage or shifting.
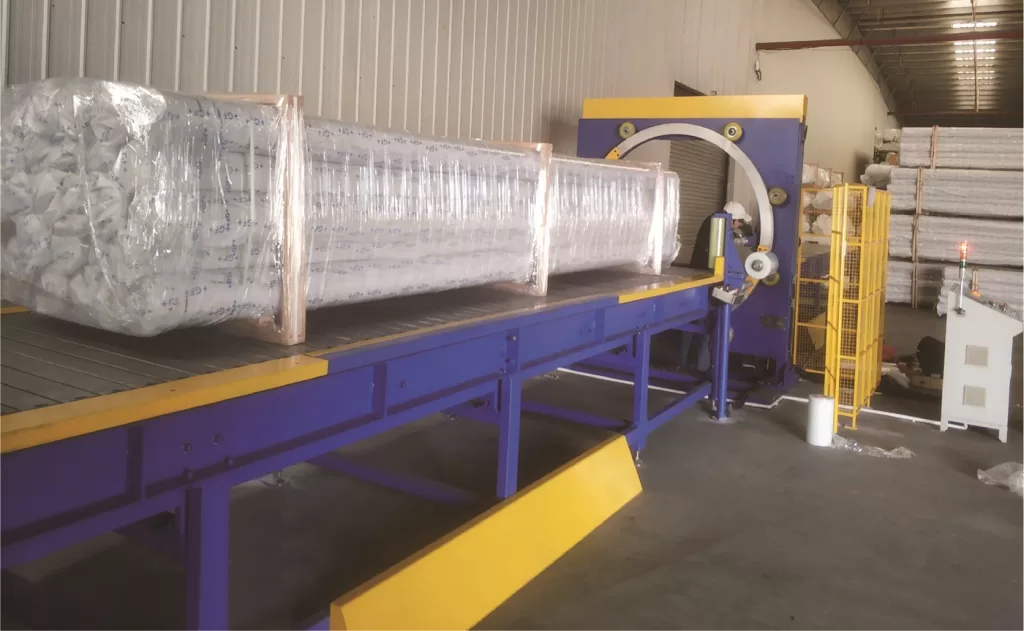
Examining Each Step in Detail
From my perspective at FHOPEPACK, I see that each stage of this high-speed wrapping process is vital. First, I load the aluminum profiles onto a dedicated feeding station. This station aligns the profiles so they stay straight. The system checks for length and shape. Then the profiles move forward. I watch how the rollers guide them toward the wrapping area. I find that the controlled motion lowers the chance of collision.
Next, the wrapping stage grips the stretch film. The film spool unwinds at a regulated pace. That keeps tension consistent. I have noticed that even slight shifts in tension can affect the final wrap. The machine's sensors continually monitor the process. They adjust the film feed to keep uniform coverage. This helps prevent gaps or folds in the wrapping material.
After the profiles pass through the main wrapping area, a finishing mechanism seals the edges. This ensures a neat and secure package. The system then cuts the film at the end of each cycle. This precise approach saves material. It also makes the packing visually neat. I have spoken with operators who like this system because it is user-friendly. They say it does not require advanced training. It also reduces manual errors.
Below is a simple table that shows the main steps involved:
Step | Action | Benefit |
---|---|---|
Feeding | Profiles loaded and aligned | Reduced collision and misplacement |
Wrapping | Film applied under controlled tension | Uniform protection and consistent wrap |
Sealing | Edges secured and excess film trimmed | Clean appearance and safer handling |
Each phase has its own importance. I learned that smooth transitions between steps save time. They also increase throughput. That is how I see the entire process come together to provide a high level of protection for aluminum profiles.
What Are the Benefits of Using an Automated Packing System?
I learned a lot about automated systems during my time at FHOPEPACK. They offer special advantages. They take repetitive tasks off our hands. They help businesses achieve better packaging results.
An automated packing system standardizes operations. It avoids human error. It lowers much labor needs. It boosts throughput. It also improves quality. The system coordinates film tension. It adjusts wrapping speed. It keeps products intact. It saves film. It reduces breakage. It cuts down rework. It makes overall packing smoother.
Understanding the Core Advantages
During my career at FHOPEPACK, I have seen the shift from manual packing to automated solutions. I want to talk about some advantages that stand out. First, I notice that automated systems decrease the margin of error by using sensors. These sensors check product dimensions and orientation. This is a big improvement over manual methods. Sometimes, I would see mistakes or oversights when people rushed during busy production periods. But automated machines keep a steady pace. They stay focused on every detail.
Another key advantage is time savings. The system completes tasks quickly. It also does them consistently. This is especially important when dealing with high-volume orders. I recall one time I had to pack large batches of aluminum profiles by hand. It was tiring. The automated approach changed the entire workflow. It also lowered worker fatigue and stress.
Then there is cost effectiveness. While the initial investment in an automated system can be higher, it often pays for itself through lower labor costs and less material waste. Maintenance can be planned. That minimizes downtime. Also, the system can integrate with other equipment. That allows for a smooth production chain. This synergy improves the entire packaging process.
The table below summarizes some of these benefits:
Benefit | Description | Impact on Business |
---|---|---|
Reduced Errors | Sensors and precise control lower mistakes | Fewer rejects and rework |
Faster Throughput | Automated cycles run at consistent high speeds | More orders fulfilled quickly |
Cost Savings | Less wasted material and optimized labor usage | Better returns on investment |
When I look at these features, I see how automation can transform a factory floor. It frees up skilled labor for more intricate tasks. It also ensures consistent product quality. That creates a better reputation for a business. So I believe the benefits are substantial.
How to Choose the Right Wrapping Machine for Your Aluminum Profile Packaging Needs?
I remember my first time selecting machinery at FHOPEPACK. I had many choices. I had to think about speed, budget, and product requirements. This decision process was quite very intense.
Choosing a wrapping machine involves checking production rate, material usage, machine footprint, and customization. It is also important to review software integration. Some machines let you track data in real time. Others allow quick film changeovers. You should weigh your budget and consider future expansion. That helps maximize your investment.
Key Factors for Making the Right Decision
From my background at FHOPEPACK, I have learned that certain factors stand out when you pick a wrapping machine for aluminum profiles. First, you should look at your production scale. If you handle high volumes, you need a machine that can keep up with demand. Otherwise, you might spend too much time waiting on slow wraps. Also, consider the range of profile sizes you handle. A flexible machine can adapt to different widths and lengths. That helps you avoid investing in multiple machines.
Second, think about how much automation you need. Some businesses want a fully automated line that includes feeding, wrapping, and unloading. Others prefer a semi-automated solution. They might have workers place items on conveyors or remove them at the end. I have seen both approaches work well. It depends on your workforce and your budget.
Third, maintenance and support are crucial. A machine that is easy to maintain reduces downtime. Check for spare parts availability and service response times. I recall a situation where a small part failed. Production halted for days because we could not get that part quickly. Good suppliers offer strong after-sales support. They also provide training for operators.
Here is a table that outlines some major considerations:
Consideration | Description | Reason to Evaluate |
---|---|---|
Production Volume | Expected number of profiles to wrap daily | Ensures capacity and meets demand |
Profile Variations | Different shapes and sizes | Maintains versatility and reduces cost |
Automation Level | Full or partial automation | Balances budget and labor availability |
Maintenance Needs | Ease of service and spare parts availability | Minimizes downtime and lost output |
If you think about these factors, you can narrow your choices. That saves time and money. You will also see better performance in the long run. I have found that a well-chosen machine pays dividends by delivering consistent results. That is why careful planning is essential.
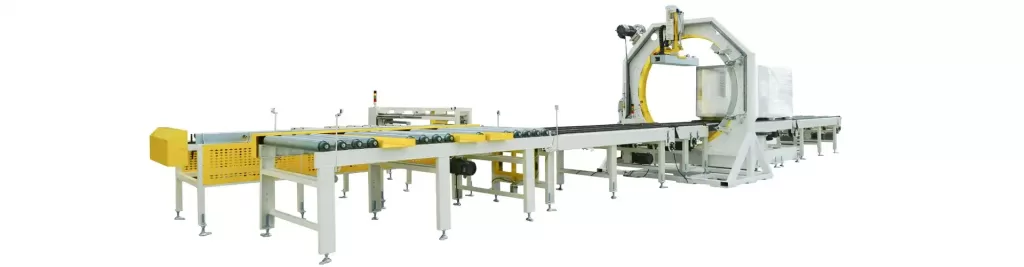
Conclusion
I appreciate the role advanced packaging machines play in our industry. I see them transforming how we handle aluminum profiles. By choosing the right high-speed wrapping machine, we raise efficiency, reduce errors, and improve outcomes. That aligns with FHOPEPACK’s mission to share knowledge and encourage better manufacturing practices. I trust this guide helps others.