Ensuring steel coils are packed securely and arrive in perfect condition requires stringent quality control. From the initial stages of material selection to the final dispatch, numerous measures are implemented to minimize damage and uphold product integrity during steel coil packing.
Quality control measures in steel coil packing encompass visual inspections for defects, dimensional checks against specifications, weight verification, and rigorous testing of packaging materials. These procedures guarantee that each coil is properly secured, protected from environmental factors, and meets defined quality benchmarks before leaving the factory.
Steel coil packing is not merely about wrapping steel; it’s a detailed process requiring meticulous attention to detail. Let’s explore the essential quality control measures that underpin effective steel coil packing.
Key Stages of Quality Control in Steel Coil Packing
Quality control in steel coil packing is a multi-stage process, starting well before the actual packing begins. It involves careful checks at each step to prevent potential issues and ensure the final packed coil is of the highest standard.
Effective quality control during steel coil packing starts with material inspection, extends through the wrapping and securing processes, and culminates in a final inspection before dispatch. Key stages include verifying packaging material strength, checking wrapping tension, and confirming secure fastening to prevent transit damage. This holistic approach minimizes defects and ensures customer satisfaction.
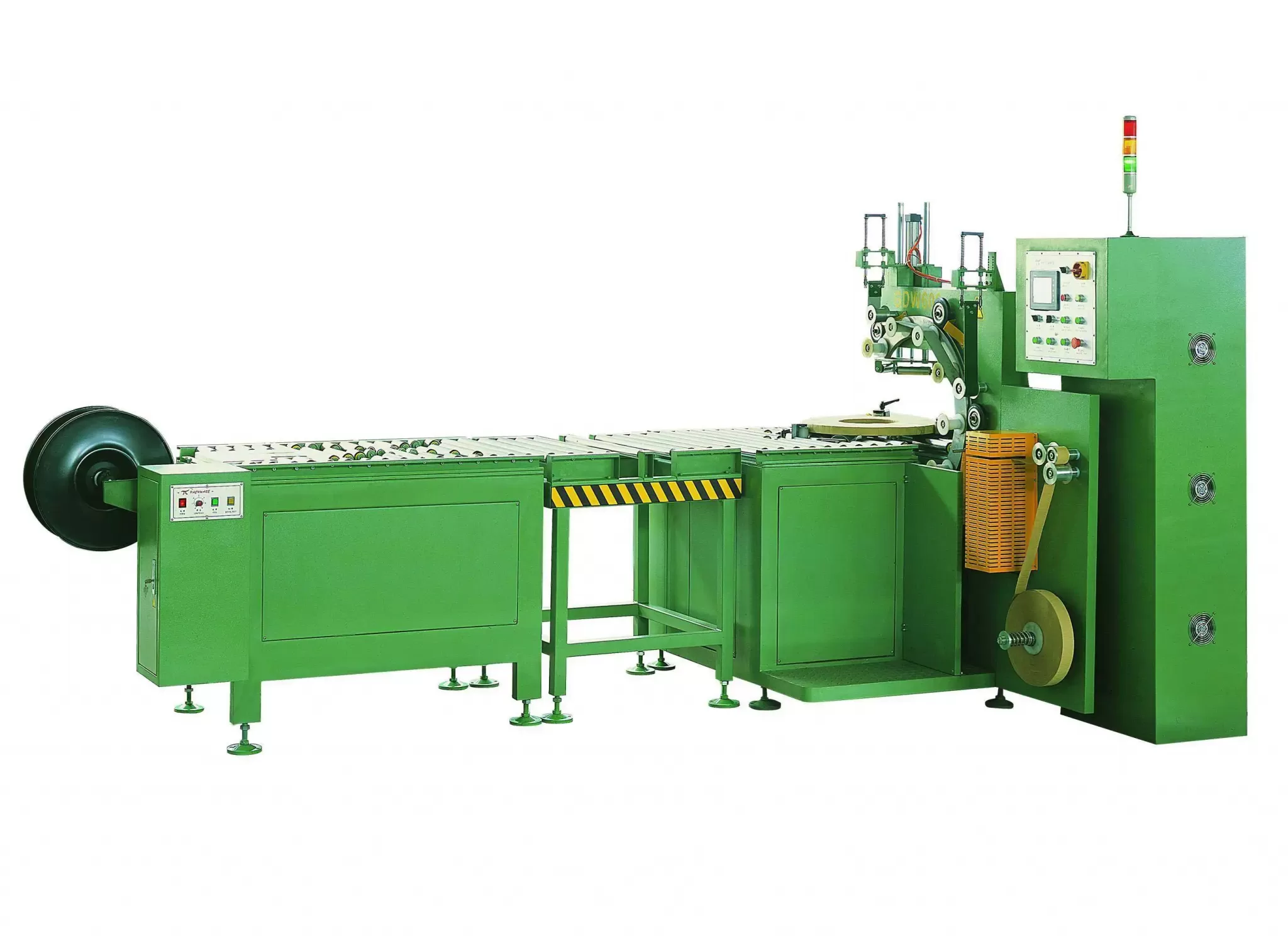
To truly understand the breadth of quality control, we need to break down each stage. How do these measures work in practice, and what are the critical checkpoints? Let’s delve deeper into the specific measures applied during steel coil packing and examine their individual contributions to overall quality.
Deep Dive into Material Inspection and Preparation
The foundation of quality packing lies in the quality of materials used. Inspecting these materials rigorously before they are used is paramount. This initial check prevents substandard materials from entering the packing process, which could compromise the protection of the steel coils.
Pre-packing material inspection is crucial. This involves verifying the tensile strength of wrapping films, the robustness of wooden pallets or skids, and the integrity of banding straps. Defects at this stage can lead to packaging failure, rendering subsequent efforts ineffective. Ensuring high-quality input materials is the first line of defense in quality control.
Material Type | Inspection Criteria | Testing Method | Acceptable Range | Rejection Criteria |
---|---|---|---|---|
Wrapping Film (PE/PP) | Tensile Strength, Tear Resistance, Thickness, Width | Tensile Test Machine, Micrometer | Tensile Strength: ≥ 20 MPa, Thickness: ±5% of spec | Tensile Strength < 20 MPa, Thickness deviation > 5% |
Steel Banding Straps | Tensile Strength, Width, Thickness, Corrosion Resistance | Tensile Test Machine, Caliper, Salt Spray Test | Tensile Strength: ≥ 500 MPa, Corrosion: > 72 hrs | Tensile Strength < 500 MPa, Corrosion < 72 hrs |
Wooden Pallets/Skids | Wood Type, Moisture Content, Load Bearing Capacity | Visual Inspection, Moisture Meter, Load Test | Moisture Content: ≤ 15%, Load Capacity: ≥ 2 Tons | Moisture Content > 15%, Load Capacity < 2 Tons |
Edge Protectors (Cardboard/Plastic) | Compression Strength, Thickness, Dimension Accuracy | Compression Test Machine, Caliper | Compression Strength: ≥ 3 MPa, Dimension: ±2mm | Compression Strength < 3 MPa, Dimension deviation > 2mm |
This table illustrates the detailed approach to material inspection. Each material component is subjected to specific tests and must meet predefined criteria. For instance, wrapping film needs to have a minimum tensile strength to withstand the stresses during wrapping and transit. Similarly, wooden pallets must have a low moisture content to prevent fungal growth and sufficient load-bearing capacity to support the weight of the steel coils. Edge protectors are tested for compression strength to ensure they can effectively cushion coil edges. By rigorously inspecting each component, potential weaknesses in the packaging are identified and eliminated before they can cause issues in the later stages. This proactive material quality control significantly contributes to reducing defects and ensuring the overall reliability of the steel coil packing process.
Implementing Robust Quality control During Wrapping
The wrapping stage is where the protective layers are applied to the steel coil. Effective quality control here is vital to ensure that these layers are applied correctly and provide the necessary protection against physical damage and environmental exposure.
During wrapping, quality control focuses on maintaining correct tension, overlap, and layer count. Automated systems monitor film tension and adjust wrapping parameters in real-time, ensuring consistent and secure wrapping across the entire coil surface. Visual checks confirm proper overlap and absence of film tears or punctures. This meticulous wrapping process is crucial for preventing moisture ingress and physical damage.
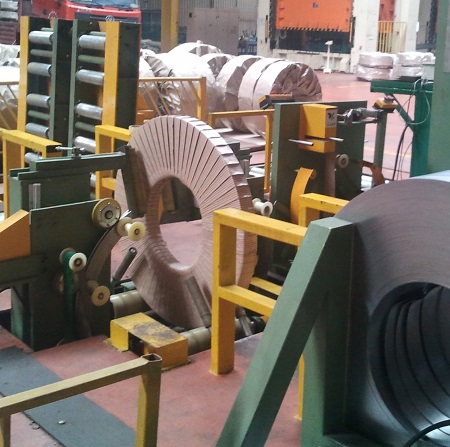
Let’s delve into the technical aspects of ensuring quality during wrapping. What specific techniques and technologies are employed to maintain consistency and detect deviations?
Advanced Techniques for Wrapping Quality Assurance
Modern steel coil packing utilizes advanced technologies to enhance the precision and reliability of the wrapping process. These technologies allow for real-time monitoring and adjustments, minimizing human error and ensuring consistent quality across large production volumes.
Automated wrapping systems with in-line sensors are now standard. These systems use sensors to measure wrapping tension, overlap percentage, and layer thickness in real-time. Deviations from pre-set parameters trigger automatic adjustments to maintain optimal wrapping quality. Some advanced systems also incorporate vision systems to detect wrapping defects like tears or incorrect overlaps immediately. These technologies represent a significant leap in ensuring consistent wrapping quality.
Here’s a look at some key technologies used and their benefits:
- Tension Control Systems: These systems use feedback loops to maintain constant film tension throughout the wrapping cycle. Benefits include preventing film breakage due to over-tension and loose wrapping due to under-tension, ensuring uniform tightness and coil stability.
- Overlap Monitoring: Sensors measure the overlap percentage of each film layer, ensuring adequate coverage and sealing. This prevents gaps that could expose the steel coil to moisture or contaminants.
- Layer Counting Mechanisms: Automated counters accurately apply the specified number of wrapping layers, guaranteeing sufficient protection based on coil size and transport conditions.
- Vision Inspection Systems: Cameras and image processing software analyze the wrapped coil surface, identifying defects such as film tears, wrinkles, or misalignments immediately after wrapping. This allows for immediate corrective action.
- Data Logging and Reporting: Sophisticated systems log wrapping parameters for each coil, providing a detailed quality record. This data is invaluable for process optimization and traceability in case of any post-packing issues.
By integrating these advanced techniques, steel coil packing operations can achieve a level of quality and consistency that was previously unattainable. These technologies not only reduce defects but also enhance efficiency and minimize material waste, contributing to a more sustainable and cost-effective packing process.
Securing and Fastening: Ensuring Stability for Transit
After wrapping, securing the coil to a pallet or skid and applying banding are critical steps to ensure stability during handling and transit. Poor fastening can lead to coil shifting, damage to the wrapping, and even coil unravelling, resulting in significant product damage.
Quality control in securing and fastening involves verifying the correct placement of edge protectors, applying adequate banding tension, and ensuring proper skid attachment. Banding tension meters are used to confirm straps are tightened to the specified level, and visual checks ensure correct edge protector positioning and skid integrity. These measures are vital for preventing movement and damage during transportation.

Let’s examine the specific procedures and tools used to ensure coils are securely fastened for their journey. What are the key considerations for banding and skid attachment?
Banding and Skid Attachment Best Practices
Effective banding and skid attachment are essential for the safe transit of steel coils. These processes must be carefully controlled to ensure that the coils remain stable and protected throughout the supply chain.
Banding best practices include using banding of appropriate tensile strength and width for the coil weight and size, applying the correct number of bands in optimal positions, and ensuring consistent tension across all bands. Skid attachment involves selecting skids of sufficient load-bearing capacity, securely fastening the coil to the skid using bolts or additional banding, and verifying skid stability before moving the packed coil. Adhering to these best practices minimizes transit damage and ensures coils arrive safely.
Here’s a breakdown of critical aspects:
- Banding Material Selection: Choosing the right type of banding (steel, polyester, polypropylene) based on coil weight, size, and anticipated transit stresses. Steel banding is typically preferred for heavier coils due to its superior strength.
- Banding Tension Control: Using calibrated tensioning tools to apply consistent and correct tension. Under-tensioned bands can loosen during transit, while over-tensioned bands can damage coil edges or wrapping. Tension meters should be used regularly to verify tool accuracy.
- Banding Pattern and Number: Applying bands in a pattern that maximizes coil stability, typically including circumferential and radial bands. The number of bands should be determined by coil weight and dimensions, with heavier coils requiring more bands.
- Edge Protector Placement: Precisely positioning edge protectors under banding to prevent banding from cutting into coil edges or damaging the wrapping film. Edge protectors should be of sufficient size and compression strength to distribute banding pressure effectively.
- Skid and Pallet Selection: Choosing skids or pallets rated for the weight and dimensions of the steel coil. Pallets should be inspected for damage before use, and wood should be treated to prevent pests and moisture absorption.
- Skid Attachment Methods: Securing coils to skids using bolts, screws, or additional banding. Bolting provides a more robust attachment for heavier coils. For banding attachment, ensure bands are routed through skid supports for maximum stability.
- Stability Testing: Conducting stability tests, such as tilt tests or vibration tests, on packed coils to simulate transit conditions and identify potential weaknesses in fastening.
By meticulously following these best practices, manufacturers can significantly reduce the risk of damage during transit. Proper banding and skid attachment are not just about securing the coil; they are about ensuring product integrity and customer satisfaction upon delivery.
Final Inspection and Defect Reduction Strategies
The final stage of quality control is a comprehensive inspection of the packed steel coil before it leaves the facility. This final check acts as a last line of defense, catching any defects that may have slipped through earlier stages and ensuring only high-quality packed coils are shipped.
Final inspection includes a visual check for any external damage to wrapping or banding, verification of correct labeling and documentation, and a final weight and dimension confirmation. Any non-conformances are documented, and corrective actions are implemented, which may include re-wrapping or re-banding the coil. Data from final inspections is used to identify recurring issues and drive process improvements. This stage is crucial for continuous defect reduction.
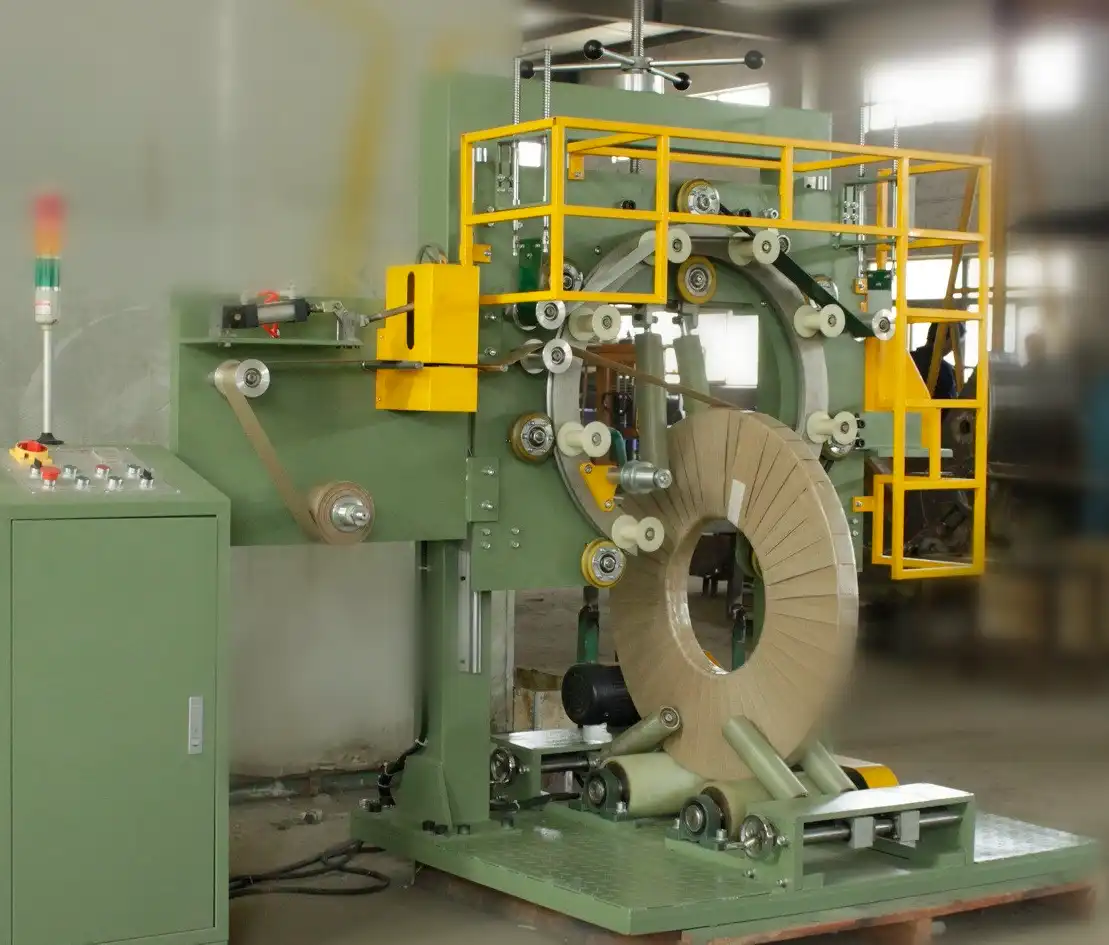
How can final inspection data be effectively used not just to catch defects but also to prevent them in the future? Let’s explore strategies for leveraging inspection data for continuous improvement and defect reduction.
Data-Driven Defect Reduction and Continuous Improvement
Final inspection data is a goldmine of information for continuous improvement. By systematically collecting, analyzing, and acting upon this data, manufacturers can identify root causes of defects, implement preventive measures, and continuously enhance their steel coil packing processes.
Implementing a robust data collection system during final inspection is key. This includes recording defect types, frequencies, locations on the coil, and potential root causes. Analyzing this data using statistical process control (SPC) techniques can reveal trends and patterns. Corrective and preventive actions (CAPA) should be implemented based on data analysis, and the effectiveness of these actions should be monitored through ongoing data collection. This data-driven approach ensures a cycle of continuous improvement.
Strategies for defect reduction using final inspection data:
- Defect Pareto Analysis: Identify the most frequent types of defects observed during final inspection. Focus improvement efforts on addressing these "vital few" defects that contribute to the majority of quality issues.
- Root Cause Analysis (RCA): For each significant defect type, conduct a thorough RCA to determine the underlying causes. Tools like 5 Whys or Fishbone diagrams can be used to systematically investigate and identify root causes, which may range from material quality issues to operator errors or machine malfunctions.
- Corrective Action Implementation: Develop and implement specific corrective actions to address identified root causes. These actions might involve process changes, equipment adjustments, operator training, or supplier quality improvements.
- Preventive Action Planning: Beyond addressing existing defects, use data to proactively identify potential failure modes and implement preventive actions to avoid future occurrences. This could include enhancing material specifications, improving machine maintenance schedules, or refining operator training programs.
- SPC Charting and Monitoring: Use control charts to track key quality metrics (e.g., defect rates, wrapping tension variability) over time. SPC helps to monitor process stability, detect process drifts, and evaluate the effectiveness of implemented improvements.
- Feedback Loops and Process Adjustments: Establish feedback loops to communicate final inspection findings back to upstream processes (e.g., wrapping, banding, material selection). This allows for timely adjustments and prevents defects from recurring in subsequent production runs.
- Regular Data Review and Management Review: Conduct regular reviews of final inspection data and CAPA effectiveness. Management reviews should assess overall quality performance, identify areas for further improvement, and allocate resources for ongoing quality enhancement initiatives.
By embracing a data-driven approach to defect reduction, steel coil packing operations can move beyond reactive defect correction to proactive quality management. This leads to higher product quality, reduced waste, improved efficiency, and ultimately, greater customer satisfaction and business success.
Conclusion
Quality control in steel coil packing is a multifaceted endeavor, requiring attention to detail at every stage. From meticulous material inspection to precise wrapping and secure fastening, each measure plays a crucial role in ensuring the integrity of the packed coil. By implementing robust quality control procedures and leveraging data for continuous improvement, manufacturers can significantly reduce defects, enhance product protection, and maintain customer trust. Continuous vigilance and a commitment to quality are the cornerstones of successful steel coil packing operations.