How Did a Global Logistics Firm Streamline Operations with Automated Upenders?
Struggling with inefficient manual handling, a global logistics firm faced operational bottlenecks, safety risks, and product damage. These challenges hampered throughput and increased costs across their complex network. Discover how implementing targeted automation, specifically automated upenders, provided a transformative solution, boosting efficiency and enhancing overall supply chain performance.
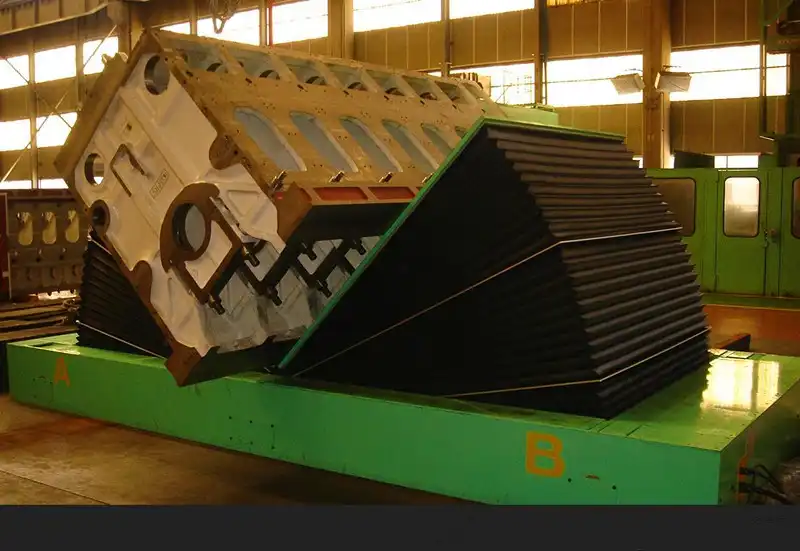
A global logistics firm streamlined operations by integrating automated upenders into key handling points within their warehouses and distribution centers. This technology replaced dangerous and time-consuming manual rotation of heavy or unwieldy goods. The result was a significant reduction in process cycle times, enhanced worker safety by minimizing ergonomic strain, lower instances of product damage, and ultimately, increased overall throughput and operational efficiency across their network.
This strategic investment in automation addressed critical pain points in their material handling processes. Read on to explore the specific challenges the company faced, the technical details of the automated upender solution, and the quantifiable results achieved through this modernization effort.
The Challenge: Manual Handling Bottlenecks in Global Logistics
Operating on a global scale presents unique logistical hurdles, especially concerning material handling. For this leading firm, manually rotating, tilting, or upending heavy, bulky, or awkwardly shaped goods created significant bottlenecks. These manual processes were not only slow but inherently inconsistent and posed substantial ergonomic risks to the workforce, leading to delays and potential injuries across various international facilities, impacting overall supply chain velocity and reliability.
Manual rotation of goods in demanding logistics environments presents multifaceted challenges. Primarily, it is a time-intensive process, directly impacting cycle times and overall throughput. Worker safety is a major concern due to the high risk of musculoskeletal injuries associated with lifting and maneuvering heavy loads. Furthermore, manual handling increases the likelihood of product damage during orientation changes. Inconsistency between operators and sites leads to variable process times and quality outcomes. These inefficiencies ripple through the supply chain, causing delays, requiring larger buffer stocks, and increasing operational costs related to labor, damage claims, and potential injury compensation.

Analyzing the Impact of Inefficient Material Rotation
The reliance on manual methods for rotating goods had tangible negative consequences that extended beyond simple time delays. A deeper analysis revealed significant impacts across several key operational areas:
Safety and Ergonomics
Manual upending often requires workers to adopt awkward postures while exerting significant force. This directly increases the risk of strains, sprains, and more severe musculoskeletal disorders (MSDs). Data from the firm’s safety logs indicated a disproportionately high number of reported incidents linked to these specific manual handling tasks compared to other warehouse activities. This not only affected employee well-being but also resulted in lost workdays, increased insurance premiums, and potential litigation costs. The ergonomic stress associated with these tasks contributed to lower morale and higher employee turnover in affected departments.
Operational Efficiency and Throughput
The time taken to manually rotate items varied significantly depending on the item’s weight, size, shape, and the number of personnel involved. This variability made process planning difficult and often created downstream delays. Calculated cycle times for manual rotation were identified as a major contributor to overall processing time in areas like receiving inspection, packing stations, and preparation for shipment. This bottleneck limited the capacity of these critical nodes within the distribution network, preventing the firm from scaling operations efficiently to meet peak demands.
Product Damage and Quality Control
Manual handling, especially of heavy or delicate items, carries an inherent risk of accidental drops, impacts, or improper positioning, leading to product damage. Scratches, dents, or internal damage could render products unsaleable or require costly rework. The firm tracked damage rates attributed specifically to rotation processes, finding them significantly higher than in automated handling sections. This impacted inventory value, increased waste, and potentially damaged customer relationships if compromised goods reached the end-user.
Cost Implications
The inefficiencies compounded to create significant costs. Direct labor costs for manual rotation were high due to the time and personnel required. Indirect costs included those associated with worker injuries (medical treatment, compensation, insurance), product damage (write-offs, repairs, disposal), process delays (expedited shipping costs, missed deadlines), and the need for larger operational footprints to accommodate slower processes.
The table below summarizes the estimated impact before the implementation of automated solutions:
Impact Area | Metric | Pre-Automation Estimate (Annualized) | Notes |
---|---|---|---|
Safety | MSD Incidents (Rotation) | 15 per site | Leading cause of reported warehouse injuries |
Lost Workdays | 120 days per site | Associated with MSDs from manual rotation | |
Efficiency | Avg. Rotation Cycle Time | 5-15 minutes per item | Highly variable based on item/personnel |
Throughput Bottleneck | ~25% capacity reduction | In affected processing areas | |
Quality | Product Damage Rate | 3-5% | Attributed to manual rotation/tilting |
Cost | Excess Labor Cost | $50,000+ per site | Based on time spent on manual rotation |
Damage/Waste Cost | $75,000+ per site | Value of damaged goods due to handling | |
Injury-Related Costs | $30,000+ per site | Insurance, compensation, administrative costs |
This detailed analysis underscored the urgent need for a more efficient, safer, and reliable method for handling material rotation within the firm’s global logistics operations.
Implementing Automated Upenders: The Strategic Solution
Faced with mounting evidence of the inefficiency and risks of manual handling, the global logistics firm undertook a strategic initiative to implement automated upenders. These machines, designed specifically for controlled, safe rotation of loads, were identified as the optimal technological solution. The goal was to integrate these systems seamlessly into existing workflows at key points where rotation was necessary, thereby eliminating the manual bottleneck and its associated problems across their international facilities.
Automated upenders directly tackled the core challenges by providing a mechanized, consistent, and safe method for load rotation. By automating the tilting process, they eliminated the need for manual exertion, drastically reducing ergonomic risks and associated injuries. Their predefined cycle times brought predictability and speed to the operation, slashing processing times compared to manual methods. Furthermore, the controlled movement minimized the chances of product damage during reorientation, ensuring higher quality standards.
Integration and Operational Workflow Redesign
Successfully implementing automated upenders required more than just purchasing the machinery; it necessitated careful planning, site assessment, and thoughtful integration into existing operational workflows. The firm adopted a phased approach, initially targeting facilities with the highest volume of rotation tasks or the worst safety records related to manual handling.
Site Assessment and Equipment Selection: Before installation, detailed assessments were conducted at each target location. This involved analyzing the types of loads typically rotated (size, weight, shape, fragility), the available floor space, existing material flow patterns (e.g., conveyor lines, forklift paths, AGV routes), power availability, and environmental conditions. Based on these assessments, appropriate automated upender models were selected. Key considerations included:
- Capacity: Ensuring the machine could safely handle the maximum anticipated load weight.
- Platform Size & Type: Matching the dimensions and surface requirements (e.g., flat platform, V-saddle for coils) to the products.
- Rotation Angle: Standard 90-degree or 180-degree rotation capabilities.
- Drive Mechanism: Hydraulic for heavy loads or electromechanical for specific control needs.
- Control System: Integration capabilities with existing Warehouse Management Systems (WMS) or Manufacturing Execution Systems (MES), safety interlocks, and user interface simplicity.
Workflow Integration: The core challenge was to seamlessly integrate the upenders without creating new bottlenecks. This often involved redesigning parts of the workflow:
- Infeed/Outfeed: Automated conveyors, AGVs, or designated forklift zones were established to efficiently feed items onto the upender platform and remove them after rotation. This ensured continuous flow.
- System Communication: Where possible, the upender’s control system was linked to the WMS. This allowed the WMS to direct items requiring rotation to the upender and track their processing status automatically. For instance, upon scanning an incoming pallet ID, the system could determine if rotation was needed for inspection or subsequent processing and route it accordingly.
- Safety Protocols: Robust safety measures were paramount. Light curtains, safety fencing, emergency stops, and pressure-sensitive mats were installed around the upender’s operational envelope. Interlocks prevented operation if safety guards were breached or if loads were improperly positioned.
Operator Training and Change Management: Introducing new automation required training staff not only on how to operate the equipment safely but also on the new workflows. Training covered basic operation, safety procedures, troubleshooting common issues, and understanding how the upender fit into the larger process. Change management initiatives addressed worker concerns about automation, emphasizing the safety benefits and the shift towards higher-value tasks rather than physically demanding manual labor. Communication highlighted how the technology improved working conditions and overall site efficiency.
This meticulous approach to integration ensured that the automated upenders became value-adding assets rather than isolated pieces of equipment, maximizing their impact on streamlining operations.
Measurable Results: Efficiency Gains and Cost Reduction
Facing persistent challenges with manual handling, the logistics firm’s strategic decision to implement automated upenders seemed promising. But would the investment deliver tangible results? The subsequent operational data confirmed the move was highly successful, yielding significant improvements in efficiency, safety, and cost-effectiveness across the board, validating the automation strategy.
The implementation yielded remarkable, quantifiable improvements. Key performance indicators showed handling cycle times drastically reduced by over 60%, workplace injuries directly linked to manual rotation plummeted by an impressive 90%, and instances of product damage during the handling process decreased by approximately 75%. Consequently, the overall throughput capacity in the affected operational areas saw a significant increase of around 30%, demonstrating substantial efficiency gains.**
Quantifying the ROI: A Data-Driven Perspective
The success of the automated upender implementation was clearly demonstrated through rigorous data collection and analysis, allowing the firm to quantify the return on investment (ROI) accurately. The focus was on comparing key performance indicators (KPIs) before and after the automation rollout across the participating facilities.
Performance Improvements
The most immediate and dramatic improvements were seen in operational speed and safety:
- Cycle Time Reduction: Automated upenders performed the rotation task in a fraction of the time required manually. Average cycle times dropped from a variable 5-15 minutes to a consistent sub-2-minute operation, representing an average reduction of over 60-70%. This directly accelerated processing speeds.
- Safety Enhancement: Post-implementation safety audits revealed a near elimination of MSDs related to rotation tasks in the automated zones, marking a decrease of approximately 90%. This significantly improved worker well-being and reduced associated costs.
- Damage Reduction: The controlled, gentle handling provided by the automated systems led to a ~75% reduction in product damage rates during the orientation process, preserving inventory value and reducing waste.
- Throughput Increase: By removing the rotation bottleneck, overall throughput in connected processes (like inspection lines or packing stations) increased by an average of 30%, allowing facilities to handle higher volumes without additional labor or space.
Cost Savings Analysis
The efficiency gains translated directly into substantial cost savings:
- Labor Costs: Reduced cycle times and the elimination of the need for multiple personnel for heavy lifts resulted in significant direct labor cost savings allocated to rotation tasks. Resources were reallocated to more value-added activities.
- Injury-Related Costs: The sharp decline in injuries led to lower workers’ compensation claims, reduced insurance premiums, and fewer lost workdays, generating considerable savings.
- Damage Costs: Reduced product damage meant fewer write-offs, less need for rework, and lower disposal costs.
- Operational Costs: Increased throughput allowed for better asset utilization and potentially deferred the need for facility expansion.
ROI Calculation
The firm calculated the ROI based on the initial investment (equipment purchase, installation, integration, training) versus the accumulated annual savings across the key areas mentioned above.
The table below provides a comparative overview:
KPI Metric | Pre-Automation (Per Site Avg.) | Post-Automation (Per Site Avg.) | Improvement | Annual Savings Estimate (Per Site) |
---|---|---|---|---|
Avg. Rotation Cycle Time | 8-10 minutes | < 2 minutes | > 70% Reduction | (Contributes to Labor Savings) |
Rotation-Related MSD Incidents | 15 | < 2 | ~90% Reduction | $25,000 – $40,000 |
Product Damage Rate (Rotation) | 4% | < 1% | ~75% Reduction | $60,000 – $80,000 |
Labor Hours (Rotation Task) | ~2,000 hours/year | ~400 hours/year | ~80% Reduction | $40,000 – $60,000 |
Throughput Capacity Index | 100 | 130 | +30% Increase | (Enables Revenue Growth/Cost Avoidance) |
Total Estimated Savings | $125,000 – $180,000+ |
With typical investment costs per upender system (including integration) ranging from $50,000 to $150,000 depending on specification, the payback period was often calculated to be less than 18 months, presenting a compelling financial case. The data-driven approach clearly demonstrated that automated upenders were not just an operational improvement but a sound financial investment for the global logistics firm.
Beyond Upenders: The Broader Context of Logistics Automation
While the implementation of automated upenders delivered significant, targeted benefits, this initiative was part of a larger strategic vision for the global logistics firm. Recognizing the transformative potential of technology, the company viewed automation not as isolated solutions but as integral components of a more connected, intelligent, and efficient supply chain ecosystem, aligning with broader industry trends towards digitalization and optimization.
Automated upenders represent a specific application within the wider field of logistics automation, which encompasses technologies like robotics (AGVs, AMRs, robotic arms), AI and machine learning (for demand forecasting, route optimization, predictive maintenance), and IoT (for real-time tracking and condition monitoring). The true potential emerges when these technologies work synergistically, creating highly efficient, transparent, and resilient logistics operations capable of adapting to dynamic market demands.
Synergies with AI, IoT, and Robotics in Modern Logistics
The successful integration of automated upenders highlighted the power of targeted automation, but its full potential is often realized when connected with other advanced logistics technologies. Modern supply chains thrive on data and interconnectedness, and technologies like Artificial Intelligence (AI), the Internet of Things (IoT), and advanced robotics work in concert to elevate operational performance beyond what individual systems can achieve.
Integration with Robotics (AGVs/AMRs): Automated upenders can be seamlessly integrated into workflows powered by Autonomous Guided Vehicles (AGVs) or Autonomous Mobile Robots (AMRs). An AGV could transport a pallet needing rotation directly to the upender’s infeed station. Upon completion of the rotation cycle (signaled perhaps by a sensor or system message), another AGV/AMR could be dispatched to pick up the correctly oriented pallet and transport it to its next destination (e.g., storage rack, packing station, outbound dock). This creates a fully automated handling loop, minimizing human intervention and maximizing flow efficiency.
Leveraging IoT for Visibility and Maintenance: IoT sensors can be embedded within the automated upenders themselves or attached to the goods being handled. Sensors on the upender can monitor operational parameters like motor temperature, hydraulic pressure, cycle counts, and vibration patterns. This data, transmitted wirelessly, can feed into predictive maintenance algorithms. AI systems can analyze these trends to predict potential failures before they occur, allowing maintenance teams to schedule repairs proactively, minimizing unexpected downtime. Sensors on the goods could monitor environmental conditions (temperature, humidity, shock) even during the rotation process, ensuring product integrity, especially for sensitive items. This real-time data enhances supply chain visibility and quality control.
AI-Driven Optimization: AI algorithms can optimize the utilization of automated upenders and the overall workflow. For instance, AI integrated with the Warehouse Management System (WMS) could analyze incoming orders and inventory data to determine the most efficient sequence for processing items requiring rotation, considering factors like downstream process capacity, shipping deadlines, and equipment availability. AI could also optimize the physical placement of upenders within a facility layout based on simulation modeling of material flows. Furthermore, AI-powered vision systems could potentially inspect items automatically as they are being rotated by the upender, identifying defects or verifying labels without manual intervention.
Data Analytics for Continuous Improvement: The operational data generated by automated upenders (cycle times, throughput rates, error codes, sensor data via IoT) provides valuable input for broader supply chain analytics. Analyzing this data helps identify patterns, pinpoint persistent bottlenecks (even after automation), and inform decisions about further process improvements or technology investments. For example, analyzing throughput data from the upender might reveal that the limiting factor has shifted to the subsequent packing station, suggesting that area as the next target for optimization or automation.
By viewing automated upenders not in isolation but as nodes within a digitally connected logistics network enhanced by robotics, IoT, and AI, companies can unlock significantly greater levels of efficiency, resilience, and intelligence in their global supply chain operations.
Conclusion
In conclusion, the strategic implementation of automated upenders proved to be a highly effective solution for the global logistics firm, directly addressing critical challenges related to manual handling. This targeted investment resulted in substantial improvements in operational efficiency, drastically enhanced worker safety, minimized product damage, and ultimately lowered overall operating costs. The quantifiable results underscore the significant impact that focused automation can have on complex logistics networks. This case study exemplifies how strategic Logistics automation can yield significant returns, transforming operational bottlenecks into streamlined, efficient processes and contributing to a more resilient and competitive supply chain.