What Does a Textile Company’s Mold Upender Automation Upgrade Look Like?
Struggling with slow, hazardous manual handling of heavy molds or machine components in your textile facility? These traditional methods often lead to production bottlenecks, safety risks, and potential damage to valuable equipment. Embracing automation offers a path to enhanced efficiency, improved safety, and greater operational control.
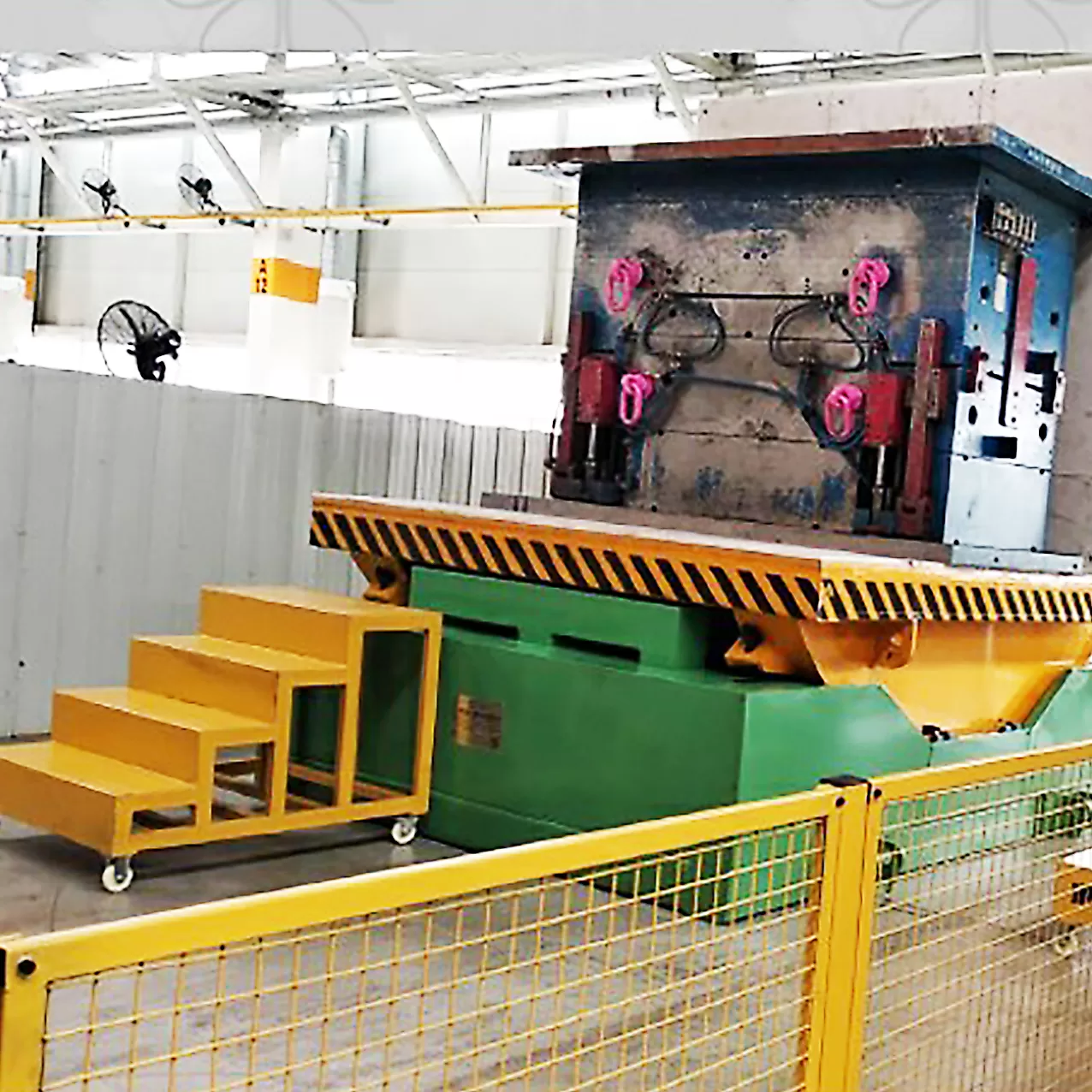
A textile company’s mold upender automation upgrade typically involves replacing manual or semi-automated tilting and rotating processes with specialized automated equipment. This machinery is designed for the safe, efficient, and precise manipulation (tilting, inverting, rotating) of heavy molds, dies, rollers, or large components used in textile manufacturing or maintenance. Integration with existing production lines and control systems is key for seamless operation and data capture.
This transition signifies a move towards smarter, safer, and more productive manufacturing environments. Delving deeper reveals the specific drivers compelling textile companies to invest in this technology, the typical stages of implementation, the core technologies involved, and the measurable benefits that justify the upgrade. Understanding this process illuminates how targeted automation can solve critical operational challenges within the demanding textile sector.
Why Automate Mold Handling in Textiles?
In the competitive textile industry, efficiency and safety are paramount. Traditional methods of handling heavy molds, large dye vats, or sizeable machine components often involve manual labor or basic lifting aids, creating significant bottlenecks, posing safety hazards to workers, and risking damage to expensive equipment. Automation emerges as a powerful solution to these persistent challenges, driving operational excellence.
Automating mold handling in textiles addresses critical pain points by significantly enhancing worker safety through the elimination of strenuous manual lifting and manipulation of heavy loads. It boosts operational efficiency by drastically reducing the time required for mold changes, maintenance access, or component rotation, leading to increased machine uptime. Furthermore, automation ensures precise and controlled movement, minimizing the risk of damage to delicate or expensive molds and machinery components, thereby reducing repair costs and extending equipment life. It also optimizes labor allocation and integrates seamlessly into smart factory ecosystems for better process control and data visibility.
Overcoming Traditional Limitations
The shift towards automated mold upenders is driven by the need to overcome the inherent drawbacks of manual or semi-automated methods. These limitations directly impact safety, productivity, and profitability.
Safety Concerns with Manual Handling
Manual handling of heavy or awkwardly shaped molds and components is a major source of workplace injuries in manufacturing environments. Strains, sprains, crush injuries, and falls are common risks associated with lifting, pushing, pulling, and rotating these items. Automated mold upenders remove the operator from direct physical contact during the manipulation process, drastically reducing the potential for such incidents and improving overall workplace safety compliance. This aligns with the broader industry trend, similar to how automation in weaving or cutting reduced repetitive strain injuries.
Efficiency Bottlenecks in Maintenance & Changeovers
Machine maintenance and product line changeovers often require molds or large components to be repositioned or inverted. Manual methods are inherently slow, requiring significant manpower and careful coordination. This downtime directly impacts production schedules and overall equipment effectiveness (OEE). Automated upenders perform these tasks significantly faster, often reducing handling times from hours to minutes, thereby minimizing non-productive periods and maximizing throughput. The efficiency gains mirror those seen in broader textile automation, where tasks completing in minutes once took hours.
Risk of Damage to Expensive Molds/Components
Textile machinery components, molds for specific processes (like non-woven fabric formation or specialized finishing), and large printing rollers can be extremely expensive and sensitive to damage. Accidental drops, impacts during manual handling, or improper positioning can lead to costly repairs or replacements, alongside extended production halts. Automated mold upenders provide smooth, controlled, and precise movement, ensuring components are handled securely and positioned accurately, safeguarding these critical assets.
Feature | Manual/Semi-Auto Handling | Automated Mold Upender | Impact in Textiles |
---|---|---|---|
Safety | High risk of injury | Minimal operator physical interaction | Reduced Lost Time Incidents (LTIs), Safer workplace |
Time/Operation | Hours (Variable) | Minutes (Consistent) | Increased machine uptime, Faster changeovers/PM |
Damage Risk | Moderate to High | Very Low | Lower repair/replacement costs, Extended asset life |
Labor Required | 2+ Operators | 1 Operator (Monitoring) | Reduced labor costs, Reallocation of workforce |
Precision | Low | High (Controlled movement & positioning) | Consistent quality, Fewer setup errors |
Process Control | Limited | Integrated with PLC/SCADA | Data logging, Remote monitoring, Process integration |
By addressing these core limitations, the automation of mold handling becomes a strategic investment, contributing directly to a safer, more efficient, and cost-effective textile manufacturing operation.
The Process: Transitioning to Automated Mold Upenders
Implementing an automated mold upender system is more than just purchasing a piece of equipment; it’s a strategic project requiring careful planning, integration, and change management. Successfully transitioning from manual or outdated methods to a fully automated solution involves several distinct phases, ensuring the technology meets specific operational needs and delivers the expected return on investment within the textile facility.
The transition process typically begins with a thorough assessment of current handling procedures, safety records, and efficiency metrics to identify specific needs and justify the investment. This is followed by selecting the appropriate automated mold upender solution based on load capacity, rotation requirements, space constraints, and control features. Subsequent stages involve detailed integration planning, physical installation and commissioning, and crucial operator training alongside updated safety protocols.
Key Stages of Implementation
A structured approach ensures a smooth and effective upgrade:
-
Needs Analysis and Feasibility Study: This initial phase involves quantifying the problems with the current system. Data is collected on handling times, safety incidents related to mold handling, equipment damage frequency and cost, labor requirements, and downtime associated with changeovers or maintenance requiring mold manipulation. This data builds the business case, defining the required capabilities (load capacity, size handling, rotation angle, speed) and calculating the potential ROI. Input from operators, maintenance staff, and safety officers is crucial.
-
Vendor Selection and Solution Specification: Based on the needs analysis, potential vendors are identified and evaluated. Detailed specifications are developed for the automated mold upender, covering aspects like:
- Maximum load weight and dimensions.
- Required rotation angle (e.g., 90°, 180°).
- Platform size and surface type (e.g., anti-slip, V-block for rollers).
- Drive mechanism (hydraulic or electro-mechanical).
- Control system requirements (e.g., PLC brand, HMI features, remote control).
- Safety features (interlocks, light curtains, E-stops, load sensors).
- Integration capabilities (e.g., communication protocols like Profinet, Ethernet/IP).
- Footprint and utility requirements (power, hydraulics).
-
Integration Planning: This critical stage focuses on how the new equipment will fit into the existing workflow and infrastructure.
- Physical Integration: Determining the optimal location, foundation requirements, necessary modifications to the surrounding area, and integration with material flow systems (e.g., overhead cranes, AGVs, conveyors).
- Control System Integration: Planning how the upender’s controls will interface with existing machine controls, Manufacturing Execution Systems (MES), or SCADA systems. This includes signal exchange for operational sequencing, status monitoring, and safety interlocking.
-
Installation and Commissioning: The selected vendor installs the equipment according to the plan. Commissioning involves rigorous testing to ensure the upender operates correctly, meets all specified performance criteria (speed, accuracy, load handling), and that all safety systems are fully functional and validated (e.g., Factory Acceptance Test – FAT, Site Acceptance Test – SAT).
-
Operator and Maintenance Training: Comprehensive training is provided to operators on the safe and efficient use of the new equipment, including control panel operation, loading/unloading procedures, and emergency protocols. Maintenance personnel receive training on preventative maintenance schedules, troubleshooting, and repair procedures.
-
Go-Live and Performance Monitoring: The automated system is put into regular operation. Performance is closely monitored against the initial KPIs (cycle time, safety incidents, uptime) established during the needs analysis phase to verify the achieved benefits and identify any areas for further optimization. Continuous improvement practices are applied based on operational feedback and data.
This methodical approach, mirroring successful automation projects across industries like the textile examples provided (e.g., ModernTex’s transition), ensures the mold upender automation upgrade delivers tangible results and integrates effectively into the manufacturing ecosystem.
Technologies Enabling the Upgrade
Manual mold handling methods, often relying on brute force or basic mechanical aids, are inefficient and inherently risky. The transition to automated mold upenders leverages a suite of modern engineering technologies designed for reliability, precision, and safety. Understanding these core components reveals how automation transforms this critical process.
The key technologies enabling a mold upender automation upgrade include robust mechanical structures engineered to handle specific load capacities and sizes, coupled with powerful and precise drive systems (typically electro-hydraulic or electro-mechanical). Sophisticated control systems, often utilizing Programmable Logic Controllers (PLCs) and Human-Machine Interfaces (HMIs), manage operation sequences, while integrated sensors and safety mechanisms ensure accurate positioning and protect personnel and equipment.
Core Components of Automated Mold Upenders
The effectiveness and safety of automated mold upenders rely on the integration of several key technological elements:
Drive Systems (Hydraulic vs. Electric)
The power source for tilting or rotating the load is critical.
- Hydraulic Systems: Often preferred for very heavy loads due to their high power density and relatively lower initial cost for high force applications. They provide smooth motion but require hydraulic power units, associated piping, and pose potential leak risks. Regular maintenance of seals and fluid is necessary.
- Electro-mechanical Systems: Utilize electric motors, gearboxes, and often screw mechanisms or chain drives. They offer precise control, cleaner operation (no hydraulic fluid), lower energy consumption during idle periods, and easier integration with sophisticated electronic controls. While potentially having a higher initial cost for very high loads, they often require less maintenance than hydraulic systems. The choice depends on load, duty cycle, required precision, and environmental considerations.
Control Systems (PLCs, HMIs)
These form the "brain" of the automated upender.
- Programmable Logic Controllers (PLCs): Industrial computers that manage the sequence of operations, interpret sensor inputs, control motor/valve actuation, and enforce safety logic. They provide reliability, flexibility for programming different operational modes, and connectivity options.
- Human-Machine Interfaces (HMIs): Typically touchscreen panels that allow operators to initiate cycles, select modes, monitor system status, view diagnostics, and acknowledge alarms. Modern HMIs offer intuitive graphical interfaces for ease of use. Remote pendants or wireless controls might also be used for operator convenience and safety during loading/unloading.
Safety Features (Interlocks, Sensors, E-stops)
Safety is paramount in automated heavy handling.
- Safety Interlocks: Prevent operation under unsafe conditions (e.g., access gates must be closed, load must be properly secured).
- Presence Sensing Devices: Light curtains or area scanners detect personnel intrusion into the operating zone, triggering a safe stop.
- Load Sensors/Limit Switches: Confirm the load is correctly positioned and within capacity limits before and during operation. Positional sensors ensure accurate stopping at desired angles.
- Emergency Stops (E-stops): Prominently located buttons that immediately halt all motion in an emergency.
- Mechanical Locks/Fail-Safes: Prevent unintended movement in case of power loss or component failure, especially in hydraulic systems (e.g., pilot-operated check valves).
Technology Feature | Description | Benefit in Textile Mold Handling |
---|---|---|
Heavy-Duty Structure | Engineered steel frame/platform designed for specific weight & dimensions | Reliable handling of large textile molds, rollers, or machine parts |
Precision Drive System | Controlled hydraulic cylinders or electric motor/gearbox/screw drive | Smooth, repeatable tilting/rotation, prevents jarring/damage |
PLC Control | Manages operational logic, sequences, and safety interlocks | Automated cycles, consistent performance, integration capability |
HMI Interface | Touchscreen/buttons for operator input, status monitoring, diagnostics | User-friendly operation, clear system feedback, easier troubleshooting |
Position Sensors | Limit switches, encoders, proximity sensors track platform angle/position | Accurate stopping at desired angles (e.g., 90°, 180°), process precision |
Safety Interlocks | Switches on gates, guards, load clamps ensuring safe conditions | Prevents operation if hazards exist, enhances personnel safety |
Presence Sensing | Light curtains, laser scanners detecting intrusion | Stops machine if personnel enter hazardous zone during operation |
Connectivity Options | Ethernet/IP, Profinet, Modbus TCP for communication with other systems | Integration into MES/SCADA, remote monitoring, Industry 4.0 readiness |
The synergy of these technologies transforms mold handling from a manual, high-risk task into a controlled, efficient, and safe automated process, contributing significantly to the overall modernization of textile manufacturing facilities.
Measuring Success: KPIs and Real-World Impact
Implementing an automated mold upender system is a significant investment for any textile company. Therefore, measuring its success and quantifying the return on investment (ROI) is crucial. This involves tracking specific Key Performance Indicators (KPIs) that reflect improvements in efficiency, safety, cost reduction, and overall operational performance compared to the previous manual or semi-automated methods.
The success of a mold upender automation upgrade is primarily measured through tangible improvements in KPIs such as a significant reduction in the cycle time required for mold handling during changeovers or maintenance (boosting productivity), a measurable decrease in safety incidents related to manual handling (improving workplace safety), lower costs associated with mold or component damage, increased Overall Equipment Effectiveness (OEE) due to reduced downtime, and optimized labor utilization.
Quantifiable Benefits and ROI
Tracking specific metrics provides clear evidence of the upgrade’s impact:
-
Cycle Time Reduction: One of the most direct benefits is the speed increase. Measure the time taken to complete a standard mold upending operation (e.g., tilting a dye vat for cleaning, rotating a printing roller for maintenance) before and after automation. A reduction from, say, 60 minutes with manual rigging to 10 minutes with the automated upender directly translates to less downtime. This mirrors the broader benefits seen in textile automation where production times were slashed significantly, as highlighted in the ModernTex case study.
-
Safety Improvement: Track the number of safety incidents (near misses, first aid cases, Lost Time Incidents – LTIs) related to mold/heavy component handling. A reduction, ideally to zero, demonstrates a clear improvement in workplace safety and can lead to lower insurance premiums and associated costs. This is often a primary driver for automation in physically demanding tasks.
-
Reduced Damage Costs: Monitor the frequency and cost of repairs or replacements for molds, rollers, or machine components damaged during handling. Automation provides controlled, precise movement, drastically minimizing impacts and drops. Quantifying the reduction in these costs contributes directly to the ROI calculation.
-
Increased Overall Equipment Effectiveness (OEE): OEE is a composite metric calculated as Availability x Performance x Quality. By reducing changeover and maintenance downtime (improving Availability) and potentially enabling faster machine cycles or setups (improving Performance), the automated upender contributes to a higher OEE for the associated production machinery.
-
Labor Optimization: While automation might reduce the number of operators directly involved in the handling task (e.g., from 2-3 manual handlers to 1 monitor), it allows for reallocation of that labor to higher-value tasks like quality control, machine operation, or preventative maintenance. Calculate the cost savings or the value generated by reallocated labor.
-
Improved Ergonomics and Morale: While harder to quantify directly in monetary terms, reducing physically strenuous tasks improves worker ergonomics and can boost morale by demonstrating investment in better working conditions. This can indirectly impact productivity and employee retention.
By consistently tracking these KPIs, textile companies can validate the effectiveness of their mold upender automation upgrade, demonstrate tangible ROI to stakeholders, and reinforce the value of adopting smart manufacturing technologies for enhanced competitiveness and operational resilience. The data gathered also informs future automation decisions within the facility.
Conclusion
In conclusion, upgrading to automated mold upenders represents a significant step forward for textile companies seeking enhanced operational efficiency, improved worker safety, and better protection of valuable assets. The transition involves replacing labor-intensive and risk-prone manual methods with precisely controlled, automated systems. This shift addresses key challenges like production bottlenecks during changeovers, the high risk of injuries associated with heavy lifting, and the potential for costly damage to molds and machinery. As demonstrated through the analysis of process stages, enabling technologies, and measurable KPIs, this targeted automation delivers substantial benefits. This Automation case study approach to improving a specific handling task reflects the wider industry trend towards smarter, safer, and more competitive manufacturing practices within the textile sector.