How Can Mold Upenders Help Reduce Workplace Injuries in a Factory?
Struggling with workplace injuries linked to manual mold handling? The physical strain of lifting, rotating, and positioning heavy molds often leads to costly musculoskeletal disorders (MSDs) and lost productivity. Ignoring these ergonomic hazards puts your workforce at risk and impacts your bottom line. Mold upenders offer a vital solution.
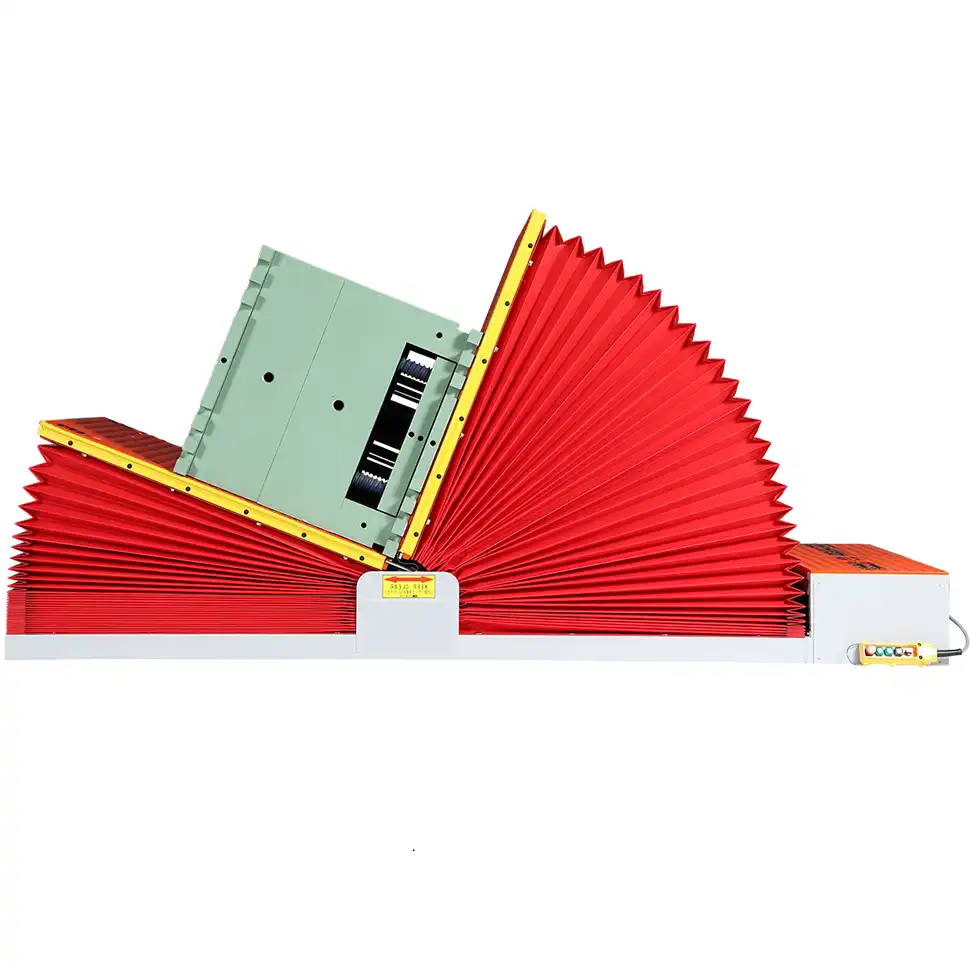
Mold upenders significantly reduce workplace injuries by automating the hazardous task of manually rotating or tilting heavy molds. They eliminate strenuous lifting, awkward postures, and forceful exertion, which are primary causes of musculoskeletal disorders (MSDs). By providing controlled, stable movement, these machines minimize risks like strains, sprains, and crushing injuries, thereby enhancing overall factory safety protocols and promoting ergonomic solutions for demanding industrial tasks.
Implementing engineered solutions like mold upenders is a critical step towards creating a safer, more efficient manufacturing environment. Let’s delve deeper into how these machines specifically target ergonomic risks and contribute to a healthier workforce.
Understanding the Ergonomic Risks in Mold Handling
Handling large, heavy molds is an inherent part of many manufacturing processes, particularly in foundries, injection molding, and die-casting operations. However, the manual manipulation of these objects presents significant ergonomic risks, frequently leading to debilitating workplace injuries and impacting operational efficiency. Understanding these specific hazards is the first step towards effective injury prevention.
Ergonomic risks in manual mold handling primarily involve high force exertions, awkward postures, and repetitive motions. Workers often strain muscles lifting excessive weight, twist their bodies unnaturally to maneuver molds, or reach excessively. Repetitive handling cycles exacerbate fatigue and wear on joints and soft tissues. Contact stress from sharp edges or leaning against equipment, combined with potential vibration exposure if tools are used nearby, further elevates the risk of developing serious musculoskeletal disorders (MSDs) like back pain, tendinitis, and carpal tunnel syndrome, directly contravening robust factory safety protocols.
The High Cost of Musculoskeletal Disorders (MSDs)
Musculoskeletal disorders are not minor inconveniences; they represent a substantial burden on both employees and employers. According to OSHA and the Bureau of Labor Statistics, MSDs are among the most frequently reported causes of lost or restricted work time. Industries like manufacturing and foundries, where manual material handling is common, often see higher rates of these injuries.
The primary ergonomic risk factors identified by OSHA include:
- Exerting Excessive Force: Manually lifting, pushing, pulling, or carrying heavy molds demands significant physical effort, straining muscles and the spine.
- Awkward Postures: Bending, twisting, reaching overhead, kneeling, or squatting while handling molds places unnatural stress on joints and ligaments. Maintaining static postures for long periods also contributes to fatigue and discomfort.
- Repetitive Motions: Performing the same or similar movements frequently, such as repeatedly flipping or positioning molds, can lead to cumulative trauma disorders.
- Contact Stress: Pressure from sharp edges of molds or equipment digging into the body can impede circulation and damage nerves.
- Vibration: While less direct in mold handling itself, associated tasks might involve vibrating tools, adding to the overall physical load.
The consequences of these risks manifest as MSDs, including lower back pain, shoulder injuries, carpal tunnel syndrome, tendinitis, and herniated discs. These injuries often develop gradually, starting as discomfort and progressing to severe pain and functional limitation if the hazardous exposures continue.
The costs associated with MSDs are multi-faceted:
- Direct Costs: Workers’ compensation payments, medical expenses, and rehabilitation costs.
- Indirect Costs: Lost productivity due to employee absence or restricted duty, costs of training replacement workers, decreased morale, potential impact on product quality, and administrative time spent managing claims. Indirect costs can often be several times higher than direct costs.
Implementing ergonomic solutions like mold upenders directly targets these risk factors by replacing manual force with mechanical power and ensuring controlled, stable movement, thereby reducing the likelihood and severity of MSDs.
Risk Factor Comparison | Manual Mold Handling | Handling with Mold Upender |
---|---|---|
Force Exertion | High (Lifting, Pushing, Pulling) | Very Low (Operating controls) |
Awkward Postures | High (Bending, Twisting, Reaching) | Minimal (Standing/Operating) |
Repetition Strain | High (If frequent handling) | Low (Machine performs repetitive rotation) |
Risk of Sudden Movement | Moderate to High (Loss of grip, slip) | Very Low (Controlled mechanical movement) |
Potential Injury Types | Back Strains, Sprains, Herniated Discs, Shoulder Injuries | Minimal; potential pinch points if unguarded |
Associated Costs (Est.) | High (Workers’ Comp, Lost Time, Quality) | Low (Initial Investment + Maintenance) |
Investing in ergonomic equipment is not merely an expense; it’s a strategic investment in workforce health, safety, and overall operational efficiency, crucial for long-term risk reduction.
Mold Upenders as a Primary Ergonomic Solution
Given the significant ergonomic hazards associated with manual mold handling, implementing engineering controls is the most effective strategy for injury prevention. Mold upenders, also known as mold flippers or tilters, stand out as a primary ergonomic solution specifically designed to address the high-risk tasks of rotating and positioning heavy, bulky molds safely and efficiently.
Mold upenders act as a crucial ergonomic intervention by automating the dangerous process of rotating heavy molds. They eliminate the need for manual lifting, pushing, and pulling, significantly reducing forceful exertions and awkward postures like bending and twisting. By providing a stable, powered platform for controlled 90-degree or 180-degree rotation, these machines prevent sudden load shifts and minimize the risk of strains, sprains, and crushing injuries, offering effective injury prevention.
Key Features and Mechanisms Benefiting Safety
Mold upenders achieve significant safety improvements through their specific design features and operational mechanisms. Understanding how these components work highlights their ergonomic benefits:
-
Powered Rotation/Tilting: The core function of a mold upender is its ability to rotate or tilt heavy loads, typically 90 or 180 degrees, using hydraulic or electromechanical power. This completely eliminates the need for workers to manually exert high forces to flip or turn molds, which is a major source of back and shoulder injuries. The machine bears the load and performs the strenuous movement.
-
Stable Load Platform: Molds are securely placed onto a robust platform or table surface. During the rotation cycle, the mold remains contained and supported, preventing it from slipping, tipping, or falling, which could cause crushing injuries or damage to the mold itself. This stability contrasts sharply with the instability inherent in manual methods or using inadequate equipment like cranes with slings.
-
Controlled Movement: The rotation process is smooth and controlled, typically managed via pendant or console controls. This predictability eliminates the sudden jerks or unexpected load shifts that can occur during manual handling or with less precise lifting equipment, further reducing the risk of strains and sprains. Speed control options allow the cycle to be adjusted for different load types.
-
Reduced Handling: By integrating the upender into the workflow (e.g., receiving a mold from a transport cart, rotating it, and positioning it for the next process step or maintenance), the number of times the mold needs to be manually handled or repositioned using other potentially hazardous methods (like cranes) is minimized. Fewer handling steps mean fewer opportunities for injury.
-
Ergonomic Working Height: Many mold upenders can be designed or integrated with lift tables to present the mold at an optimal working height after rotation. This reduces the need for workers to bend, stoop, or reach excessively while performing maintenance, cleaning, or inspection tasks on the mold, addressing awkward posture risks.
-
Capacity and Customization: Mold upenders are available in various load capacities and platform sizes to safely handle different mold weights and dimensions. Custom features, such as conveyor integration, specific platform surfaces, or specialized clamping, can further enhance safety and efficiency for particular applications.
By incorporating these features, mold upenders directly mitigate the primary ergonomic risk factors—force, posture, and repetition—associated with manual mold manipulation, making them an essential component of modern factory safety protocols aimed at risk reduction.
Integrating Mold Upenders into Factory Safety Protocols
Experiencing frequent injuries or near-misses during mold handling? Simply purchasing a mold upender isn’t a complete solution. Without proper integration into your workflow and safety protocols, even advanced equipment can be misused, failing to deliver the expected safety benefits and potentially introducing new hazards. Effective implementation is key.
Integrating mold upenders involves incorporating their use into standard operating procedures (SOPs), conducting thorough risk assessments for the modified workflow, and providing comprehensive operator training. This ensures the equipment is used correctly and safely, maximizing its ergonomic benefits. Effective factory safety protocols require documenting procedures, defining responsibilities, and ensuring regular maintenance checks are performed on the upender.
Implementation Steps and Training Requirements
Successfully integrating a mold upender requires a systematic approach, moving beyond simple installation to ensure it becomes a seamless and safe part of the production or maintenance process. This involves careful planning, clear procedures, and robust training.
1. Risk Assessment and Needs Analysis:
Before purchasing, conduct a thorough risk assessment of the existing mold handling process to identify specific hazards and quantify risks. Determine the size, weight, frequency, and rotation requirements for the molds being handled. This analysis informs the selection of the appropriate mold upender model (capacity, size, power type – hydraulic/electric) and identifies necessary safety features (guarding, interlocks, emergency stops).
2. Workflow Integration Planning:
Determine precisely where the upender will fit into the material flow. Consider how molds will arrive at the upender (e.g., forklift, crane, AGV, conveyor) and how they will depart after rotation. Ensure adequate floor space, clear access routes, and proper foundations. The goal is to minimize manual handling steps before and after the upender cycle. Consider integration with adjacent equipment if possible (e.g., automated loading/unloading).
3. Installation and Commissioning:
Ensure the upender is installed according to manufacturer specifications and relevant safety standards. This includes proper anchoring, electrical connections, hydraulic system checks (if applicable), and functional testing of all controls and safety devices (e.g., E-stops, limit switches, guarding interlocks). Commissioning should verify the machine operates smoothly and safely throughout its full range of motion.
4. Developing Standard Operating Procedures (SOPs):
Create clear, step-by-step SOPs for operating the mold upender. These should cover:
- Pre-operational checks (visual inspection, control checks).
- Proper loading and positioning of the mold.
- Operating the rotation cycle safely.
- Unloading procedures.
- Emergency stop procedures.
- Lockout/Tagout (LOTO) procedures for maintenance.
These SOPs should be readily accessible to operators.
5. Comprehensive Training:
Training is critical for safe operation and is mandated by OSHA principles. Training should cover:
- Operator Training: Understanding the machine’s controls, capabilities, limitations, SOPs, specific hazards (pinch points, crush zones), emergency procedures, and basic troubleshooting. Hands-on practice under supervision is essential.
- Maintenance Training: Understanding LOTO procedures, preventative maintenance schedules, lubrication requirements, hydraulic/electrical system basics, and troubleshooting specific machine faults.
- Awareness Training: For workers in the vicinity, understanding the machine’s operation, designated safe zones, and potential hazards.
6. Regular Maintenance and Inspection:
Establish a preventative maintenance schedule based on manufacturer recommendations and usage frequency. Regular inspections should check for wear, damage, leaks, proper functioning of safety devices, and control responsiveness. Keep detailed maintenance logs.
Integration Phase | Key Activities | Responsibility | Outcome |
---|---|---|---|
Planning & Selection | Risk Assessment, Define Specs, Select Model, Plan Workflow Integration | Engineering, Safety, Production | Appropriate Machine Chosen, Layout Defined |
Installation & Setup | Physical Installation, Utility Connections, Commissioning, Safety Checks | Maintenance, Installers | Machine Operational and Verified Safe |
Procedures & Training | Develop SOPs & LOTO, Conduct Operator/Maintenance/Awareness Training | Safety, Production, Maintenance | Competent Operators, Safe Work Practices |
Ongoing Operation | Adherence to SOPs, Regular PM & Inspections, Refresher Training as Needed | Operators, Maintenance, Safety | Sustained Safe Operation, Injury Prevention |
Following these steps ensures the mold upender effectively enhances safety and becomes a valuable asset rather than just another piece of equipment. This structured approach aligns with best practices for implementing engineering controls and strengthening overall factory safety protocols.
Quantifying the Impact: ROI and Safety Metrics
Investing in capital equipment like a mold upender requires justification beyond just safety improvement; demonstrating a tangible return on investment (ROI) is often crucial. Fortunately, the benefits of reducing ergonomic risks through mold upenders translate directly into measurable financial and operational gains, reinforcing their value proposition.
Quantifying the impact involves tracking key safety metrics before and after implementation, such as reductions in MSD incidence rates, lost workdays, and workers’ compensation costs related to mold handling. Calculating ROI considers these direct cost savings alongside potential productivity gains (faster cycle times, reduced downtime) compared to the initial investment and ongoing maintenance costs, showcasing the financial benefits of improved factory safety protocols.
Evaluating the effectiveness of a mold upender involves looking at several key areas:
-
Reduction in Injury Rates: This is the primary safety metric. Track the number and severity of MSDs (specifically back strains, shoulder injuries, etc.) related to mold handling tasks before and after the upender installation. Utilize OSHA 300 logs and internal incident reports. A significant decrease demonstrates the direct impact on worker safety.
-
Lower Workers’ Compensation Costs: Fewer injuries lead directly to reduced workers’ compensation insurance premiums and claim payouts. Calculate the cost savings from avoided claims, including medical expenses and indemnity payments. This often forms the largest component of the tangible ROI.
-
Decreased Lost Workdays: MSDs frequently result in employees needing time off work or being placed on restricted duty. Track the reduction in lost workdays and restricted duty days associated with mold handling tasks. This translates to improved labor availability and reduced costs associated with absenteeism and temporary replacements.
-
Increased Productivity and Efficiency: While safety is paramount, mold upenders often improve operational efficiency. Automating the rotation process can be significantly faster than manual methods or using cumbersome overhead cranes. Measure cycle times for mold rotation before and after. Reduced downtime for injury recovery also contributes to overall productivity gains.
-
Improved Employee Morale: While harder to quantify directly, reducing physically demanding and hazardous tasks can significantly boost employee morale and job satisfaction. This can indirectly lead to lower turnover rates and improved engagement. Surveys or feedback sessions can provide qualitative data.
-
Enhanced Compliance: Properly implemented mold upenders help ensure compliance with OSHA’s General Duty Clause (Section 5(a)(1)), which requires employers to provide a workplace free from recognized hazards likely to cause death or serious physical harm, including ergonomic hazards.
Calculating ROI involves summing the quantifiable cost savings (reduced workers’ comp, fewer lost days, productivity gains) over a specific period (e.g., 1-3 years) and comparing this to the total cost of the mold upender (purchase price, installation, training, maintenance). Often, the payback period for such ergonomic investments is surprisingly short, especially when considering the high costs associated with even a single serious MSD claim.
Conclusion
In conclusion, mold upenders are far more than just material handling devices; they are essential engineering controls for mitigating significant ergonomic risks in manufacturing environments. By automating the strenuous and hazardous task of rotating heavy molds, they directly address key causes of costly musculoskeletal disorders, such as excessive force and awkward postures. Implementing these machines, supported by robust training and integration into factory safety protocols, leads to measurable improvements in worker safety, reduced injury-related costs, and often, enhanced productivity. Prioritizing Safety improvement through ergonomic solutions like mold upenders is a strategic investment in a healthier, safer, and more efficient workforce.