Aligning Mold Flipper Capabilities with Business Objectives
Effectively integrating mold flipper capabilities with overarching business objectives is paramount for manufacturers seeking a competitive edge. This alignment ensures that investments in mold handling technology translate directly into measurable improvements in efficiency, safety, and profitability, driving sustainable growth and operational excellence in today’s dynamic market.
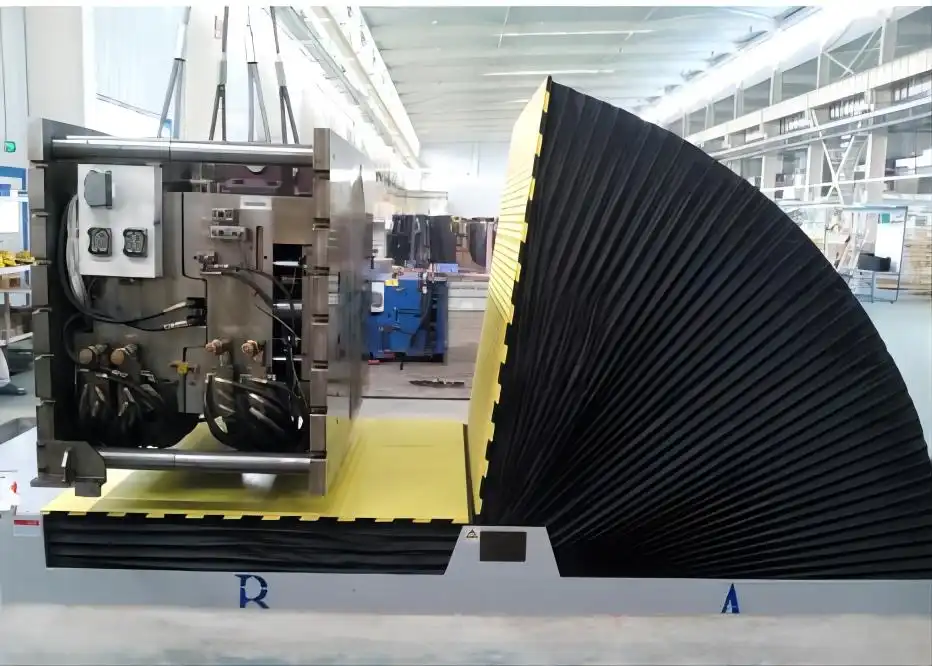
To align mold flipper capabilities with business objectives, companies must first clearly define their strategic goals—be it cost reduction, enhanced safety, or increased production throughput. Then, evaluate how specific mold flipper features, such as automation level, load capacity, and cycle time, directly contribute to achieving these targets. This strategic procurement ensures technology serves broader business ambitions, maximizing ROI and operational impact.
The journey from recognizing an operational need for a mold flipper to realizing its full strategic potential involves more than just a purchase; it requires a thoughtful integration into the company’s core objectives. By understanding the nuances of this alignment, businesses can transform a seemingly simple piece of equipment into a powerful catalyst for growth and efficiency. Let’s delve into how this critical connection can be forged and optimized.
Understanding the Strategic Value of Mold Flippers
The strategic value of mold flippers extends far beyond mere operational convenience. In a competitive manufacturing landscape, these machines are pivotal in enhancing efficiency, ensuring worker safety, and reducing costly downtime. Their adoption is a strategic move towards leaner, more agile, and ultimately more profitable production processes.
The strategic value of mold flippers lies in their ability to directly address core business imperatives such as operational efficiency, cost reduction, and workplace safety. By automating and streamlining the mold handling process, these machines reduce labor-intensive tasks, minimize the risk of injuries and mold damage, and significantly cut down on changeover times. This leads to increased production uptime, better resource utilization, and a stronger bottom line. Recent industry analyses show companies investing in advanced mold flipping technology can achieve productivity improvements of up to 30%. Furthermore, the integration of smart features like IoT connectivity enhances data-driven decision-making, allowing for predictive maintenance and optimized performance, thereby future-proofing manufacturing operations and contributing to long-term strategic goals like sustainability and market leadership. This makes mold flippers a key enabler for businesses aiming for operational excellence and sustainable growth.
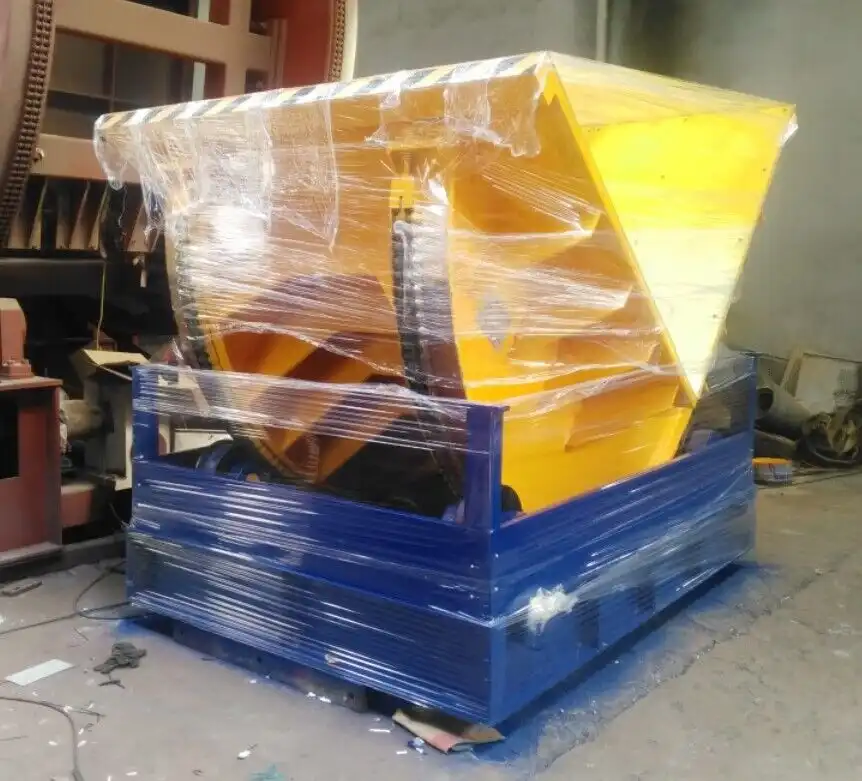
Decoding the Demand: Why Mold Flippers are a Strategic Imperative
The decision to invest in mold flippers isn’t made in a vacuum; it’s driven by compelling market forces and internal business needs. Understanding these demand drivers is crucial for appreciating the strategic imperative behind acquiring such equipment.
Key Demand Drivers Influencing Purchasing Decisions:
-
Technological Advancements: The evolution of mold flippers is a significant driver. Modern machines incorporate automation, smart sensors, and IoT connectivity, leading to enhanced operational efficiency, reduced cycle times, and improved product quality. Data from industry analyses highlight that companies adopting these technologies can see productivity improvements of up to 30%. This technological leap encourages businesses to upgrade, viewing it as a strategic investment rather than a mere replacement. For instance, smart mold flippers can provide real-time data on performance, enabling predictive maintenance and minimizing unexpected downtimes, directly contributing to the business objective of maximizing uptime.
-
Material Innovations: The materials used in mold production (e.g., lightweight composites) influence the design and efficiency requirements of mold flippers. Lighter yet durable materials reduce energy consumption during operation and lower long-term maintenance costs. This trend towards advanced materials necessitates mold flippers capable of handling these new molds effectively and safely, aligning with business goals of cost reduction and sustainability.
-
Increasing Automation: The broader manufacturing trend towards automation to improve throughput and manage labor costs directly impacts the demand for automated mold flippers. These systems minimize human intervention, reducing risks associated with manual handling and ensuring precision and safety compliance. Approximately 57% of manufacturers expect to integrate more automation tech within five years, underscoring the strategic shift towards such solutions for improved profit margins.
-
Labor Cost Considerations: Evaluating labor expenses against the investment in advanced machinery is a critical factor. Automated mold flippers can undertake tasks traditionally performed by human workers, potentially yielding long-term savings. Industries facing skill shortages or high labor costs are particularly motivated. Reports indicate an average reduction of 20% in direct labor costs after implementing automated mold handling solutions.
-
Growing Awareness of Sustainability: Sustainability initiatives are increasingly influencing purchasing decisions. Companies seek equipment that minimizes waste and reduces carbon footprints. Energy-efficient mold flippers appeal to businesses adhering to eco-friendly standards, contributing to lower operational costs through energy savings and aligning with corporate social responsibility objectives.
The interplay of these drivers demonstrates that investing in a mold flipper is not just an operational upgrade but a strategic decision to enhance overall business performance.
Strategic Impact Comparison: Manual vs. Mold Flipper
To illustrate the strategic value, consider the impact on key business metrics:
Feature/Metric | Manual Mold Handling | Automated Mold Flipper Handling | Strategic Implication for Business Objectives |
---|---|---|---|
Changeover Time | High (e.g., 2-4 hours) | Low (e.g., 0.5-1 hour) | Increased production uptime, faster response to market demand (Agility objective) |
Labor Requirement | Multiple operators, high physical strain | Minimal operator involvement, reduced physical strain | Lower labor costs, improved worker morale and retention (Cost Reduction & HR objectives) |
Safety Risk | High risk of injuries, mold damage | Significantly reduced risk of injuries and mold damage | Lower workers’ compensation costs, reduced insurance premiums, fewer production stoppages (Safety & Risk Mgt obj.) |
Mold Lifespan | Potentially reduced due to handling stress/accidents | Extended due to controlled, gentle handling | Lower mold replacement/repair costs, better ROI on mold investments (Asset Management & Cost Reduction obj.) |
Process Consistency | Variable, operator-dependent | Highly consistent and repeatable | Improved product quality, reduced scrap rates (Quality & Efficiency objectives) |
Data Collection | Manual, often inaccurate | Automated (with smart flippers), real-time data available | Enables predictive maintenance, process optimization, better decision-making (Operational Excellence objective) |
The table clearly shows that adopting mold flippers aligns directly with core business objectives related to efficiency, cost, safety, quality, and agility. This strategic alignment justifies the investment beyond simple operational improvement, positioning it as a contributor to overall business success and competitiveness. As market growth projections indicate rising investment driven by technological integration, businesses that strategically leverage mold flipper capabilities will be better positioned for future challenges and opportunities.
Key Mold Flipper Capabilities to Align with Business Goals
Identifying the right mold flipper capabilities is crucial for ensuring they directly support and enhance your specific business objectives. It’s not a one-size-fits-all scenario; the optimal features will vary depending on whether your primary goals are speed, safety, precision, cost savings, or sustainability.
Key mold flipper capabilities to align with business goals include automation levels (from semi-automatic to fully integrated robotic systems), load capacity and size versatility, rotation speed and precision, safety features (e.g., interlocks, sensors, light curtains), and data connectivity for smart factory integration. These directly impact efficiency, safety, and cost-effectiveness, supporting objectives like increased throughput, reduced labor costs, and enhanced workplace safety.
Matching Features to Strategic Imperatives
The technical specifications of a mold flipper are not just features; they are enablers of strategic outcomes. Aligning these capabilities with your business goals ensures that the technology delivers tangible value.
-
Automation and Smart Technology:
- Capability: Fully automated cycles, robotic integration, PLC controls, IoT connectivity, sensor-based monitoring.
- Business Objectives Alignment:
- Increased Throughput & Efficiency: Automated sequences reduce cycle times significantly compared to manual or semi-automatic methods. This directly supports goals of higher production output and faster order fulfillment. Data indicates up to 30% productivity improvements.
- Reduced Labor Costs: Minimizes the need for manual intervention, freeing up skilled labor for other value-added tasks and reducing direct labor costs by an average of 20%.
- Enhanced Product Quality & Consistency: Programmed movements ensure repeatable precision, reducing the risk of mold misalignment or damage that can affect part quality.
- Predictive Maintenance: IoT sensors can monitor equipment health, predict failures, and schedule maintenance proactively, minimizing unplanned downtime. This aligns with objectives for maximizing operational availability.
-
Load Capacity, Size Versatility, and Rotation Angle:
- Capability: Wide range of weight capacities (from a few tons to over 50 tons), ability to handle various mold dimensions, 90-degree, 180-degree, or even 360-degree rotation.
- Business Objectives Alignment:
- Operational Flexibility: The ability to handle a diverse range of mold sizes and weights means the flipper can support varied production lines or future changes in mold design, aligning with goals of agility and future-proofing investments.
- Optimized Space Utilization: Efficiently designed flippers can help optimize floor space in the tool room or near presses.
- Specific Process Needs: Precise rotation angles are critical for certain maintenance, cleaning, or mold assembly tasks. Ensuring the flipper meets these specific angles supports process optimization goals.
-
Safety Systems and Ergonomics:
- Capability: Safety interlocks, emergency stops, light curtains, physical guarding, audible/visual alarms, ergonomic controls for any operator interaction.
- Business Objectives Alignment:
- Enhanced Workplace Safety: Directly supports the primary business objective of creating a safe working environment, reducing lost-time incidents, and lowering workers’ compensation costs. Compliance with OSHA and regional safety standards is also met.
- Improved Employee Morale & Retention: A safer, less physically demanding environment can boost morale and make it easier to retain skilled workers.
- Reduced Risk of Mold Damage: Controlled movements and safety systems also protect the expensive molds themselves from accidental damage during handling.
-
Material Compatibility and Durability:
- Capability: Robust construction, surfaces that won’t damage molds (e.g., polyurethane-coated platforms), resistance to harsh toolroom environments.
- Business Objectives Alignment:
- Asset Protection (Molds): Gentle handling preserves the lifespan and integrity of valuable molds, aligning with objectives for cost control and maximizing asset ROI.
- Equipment Longevity (Flipper): Durable construction ensures the mold flipper itself has a long operational life with minimal maintenance, supporting long-term cost-effectiveness.
- Sustainability: Compatibility with newer, lightweight mold materials (like composites) supports broader sustainability goals by enabling their use, which can lower energy consumption.
-
Energy Efficiency and Sustainability Features:
- Capability: Energy-efficient motors, optimized hydraulic/electric systems, use of recyclable or sustainable materials in the flipper’s construction.
- Business Objectives Alignment:
- Reduced Operational Costs: Lower energy consumption directly translates to savings on utility bills.
- Corporate Social Responsibility (CSR) & Sustainability Goals: Demonstrates a commitment to environmental stewardship, which is increasingly important for brand image and regulatory compliance. Growing awareness of sustainability influences purchasing choices, and eco-friendly equipment appeals to businesses adhering to these standards.
By carefully evaluating these capabilities against the backdrop of specific business objectives—be it improving safety metrics by X%, reducing changeover times by Y minutes, or cutting operational costs by Z%—companies can select or specify a mold flipper that is not just a tool, but a strategic asset. This targeted approach ensures that the investment contributes directly to achieving desired business outcomes and provides a clear justification for the expenditure.
Measuring the Impact: KPIs for Mold Flipper Alignment
To truly understand if your mold flipper capabilities are aligned with business objectives, you need to measure their impact. Key Performance Indicators (KPIs) provide tangible evidence of success or areas needing improvement, transforming anecdotal observations into actionable data for financial and operational decision-making.
Businesses can measure the impact of aligning mold flipper capabilities with objectives by tracking KPIs such as Return on Investment (ROI), Payback Period, Overall Equipment Effectiveness (OEE) improvement for associated machinery, reduction in mold changeover times, decrease in workplace incident rates related to mold handling, and savings from reduced mold damage. These metrics provide quantifiable evidence of the alignment’s success.
Translating Alignment into Measurable Outcomes
Effective alignment isn’t just a concept; it’s a result that can be quantified. By establishing relevant KPIs before, during, and after the implementation of a mold flipper, businesses can demonstrate the value delivered.
Key Performance Indicators (KPIs) for Mold Flipper Integration:
-
Financial KPIs:
- Return on Investment (ROI):
- Definition: Measures the profitability of the investment relative to its cost.
ROI = (Net Profit / Cost of Investment) x 100
. - Alignment Insight: A strong positive ROI indicates that the financial benefits (cost savings, increased revenue from uptime) outweigh the initial and ongoing costs of the mold flipper, directly supporting profitability objectives.
- Definition: Measures the profitability of the investment relative to its cost.
- Payback Period:
- Definition: The time it takes for the initial investment to be recouped through accumulated savings or profits.
Payback Period = Initial Investment / Annual Cash Inflow
. - Alignment Insight: A shorter payback period signifies a quicker return and lower risk, aligning with financial prudence and capital efficiency goals.
- Definition: The time it takes for the initial investment to be recouped through accumulated savings or profits.
- Cost Savings (Labor, Maintenance, Damage):
- Definition: Direct reduction in operational expenses. Quantify savings from reduced manual labor hours for mold flipping, lower mold repair/replacement costs due to gentle handling, and decreased maintenance on production machinery due to faster, smoother changeovers.
- Alignment Insight: Directly contributes to the business objective of cost reduction and improved profit margins.
- Return on Investment (ROI):
-
Operational Efficiency KPIs:
- Mold Changeover Time Reduction:
- Definition: The average time taken to switch molds. Measure before and after mold flipper implementation.
- Alignment Insight: Significant reductions directly impact production flexibility and machine uptime, supporting objectives for increased throughput and responsiveness.
- Overall Equipment Effectiveness (OEE) of Production Machinery:
- Definition: For machines serviced by the mold flipper (e.g., injection molding machines), OEE (
Availability x Performance x Quality
) improvements can be an indicator. Reduced changeover time (Availability) and potentially fewer defects from damaged molds (Quality) contribute. - Alignment Insight: Higher OEE means better utilization of capital-intensive production assets, aligning with efficiency and productivity goals.
- Definition: For machines serviced by the mold flipper (e.g., injection molding machines), OEE (
- Cycle Time Improvement (Overall Production):
- Definition: While the flipper itself has a cycle time, its impact on the overall production cycle for parts requiring frequent mold changes.
- Alignment Insight: Supports objectives for faster delivery and increased output.
- Mold Changeover Time Reduction:
-
Safety & Compliance KPIs:
- Reduction in Injury Rates:
- Definition: Number of mold-handling related injuries (e.g., TRIR – Total Recordable Incident Rate) before and after.
- Alignment Insight: Directly measures the success of safety-focused business objectives, leading to lower insurance costs and improved employee well-being.
- Near-Miss Reporting Related to Mold Handling:
- Definition: Tracking near-miss incidents can indicate improving safety culture and effectiveness of new equipment.
- Alignment Insight: Proactive measure showing risk reduction, even if actual injuries were already low.
- Compliance with Safety Regulations (e.g., OSHA):
- Definition: Number of non-compliance issues or citations related to manual mold handling.
- Alignment Insight: Ensures adherence to legal and ethical standards, avoiding fines and reputational damage.
- Reduction in Injury Rates:
Structuring KPI Tracking for Mold Flipper Alignment:
KPI Category | Specific KPI | Measurement Method | Baseline (Pre-Flipper) | Target (Post-Flipper) | Frequency | Business Objective Supported |
---|---|---|---|---|---|---|
Financial | Labor Cost Savings (Mold Handling) | (Hours saved/flip) x (Flips/month) x (Avg. Labor Rate) | $X / month | $X – Y / month | Monthly | Cost Reduction, Profitability |
Mold Damage Costs | Cost of repairs/replacements due to handling incidents | $A / year | < 0.25A / year | Annually | Asset Protection, Cost Reduction | |
Operational | Avg. Mold Changeover Time | Time study for N changeovers | Z minutes | < 0.5Z minutes | Weekly | Increased Uptime, Production Efficiency, Agility |
Production Machine Uptime | (Total Available Time – Downtime) / Total Available Time | P% | > P + Q% | Daily | Throughput, Asset Utilization | |
Safety | Mold Handling Injury Rate | Number of incidents / Total work hours x Constant | R | < 0.1R | Quarterly | Workplace Safety, Employee Well-being, Cost Reduction (Ins.) |
Adherence to Safety Protocols | Audit scores for mold handling procedures | S% | >95% | Monthly | Regulatory Compliance, Risk Mitigation |
By systematically tracking these KPIs, businesses can move beyond assumptions and gain a clear, data-driven understanding of how well their mold flipper investment is aligned with, and contributing to, their broader business objectives. This not only justifies the initial expenditure but also provides insights for continuous improvement and optimization of mold handling processes. This data-driven approach is crucial for demonstrating value to stakeholders and ensuring that technological investments yield the desired strategic outcomes.
Overcoming Challenges in Aligning Mold Flippers with Business Strategy
Integrating mold flippers effectively with broader business strategy isn’t always seamless. Companies often face hurdles ranging from initial investment costs to operational integration and ensuring the technology delivers on its promised benefits. Recognizing and proactively addressing these challenges is key to successful alignment.
Common challenges in aligning mold flippers with business strategy include high initial capital investment, navigating complex regulatory compliance for safety and environment, overcoming resistance to change from an established workforce, and ensuring the chosen technology truly matches long-term operational needs. Solutions involve thorough ROI analysis to justify costs, phased implementation, comprehensive training programs to build operator skill and acceptance, and selecting versatile, future-proof equipment adaptable to evolving business demands and technological advancements.**
A primary challenge is the high initial capital investment. Mold flipping technology, especially advanced automated systems, can represent a significant upfront cost. Finance departments may scrutinize such expenditures, requiring robust justification. To overcome this, businesses must develop a comprehensive business case focusing on long-term ROI, including savings from reduced labor, increased uptime, lower injury-related costs (medical, compensation, insurance), and minimized mold damage. Quantifying these benefits clearly demonstrates that the investment is not merely an expense but a strategic move towards greater efficiency and profitability. For example, data showing an average reduction of 20% in direct labor costs and productivity improvements up to 30% can be compelling.
Regulatory compliance is another hurdle. Mold flippers must adhere to stringent safety standards (e.g., OSHA in the U.S., CE marking in Europe) and potentially environmental regulations. Navigating this landscape can be complex and time-consuming. The solution lies in partnering with reputable suppliers who guarantee compliance and provide necessary documentation. Investing in equipment with built-in safety features like interlocks, light curtains, and emergency stops, and conducting thorough risk assessments pre-installation, are crucial. For instance, European Union’s REACH regulation regarding chemical substances might indirectly influence material choices for molds and flipper components, pushing businesses toward cleaner technologies.
Technological expertise and workforce adaptation present further challenges. Operating and maintaining advanced mold flippers requires skilled personnel. There might be resistance to change from employees accustomed to traditional methods, or a skills gap. Comprehensive training programs are essential, not just on operation but also on the benefits of the new technology. Emphasizing how the flipper improves safety and reduces physical strain can help gain buy-in. Partnering with vendors for ongoing technical support and training can also bridge the expertise gap. Highlighting that 57% of manufacturers plan to integrate more automation can show this is an industry-wide shift.
Integration with existing systems and processes can be complex. A new mold flipper needs to fit physically within the plant layout and integrate smoothly with existing workflows, potentially involving other automated systems or MES (Manufacturing Execution Systems). Careful planning, including site surveys, process mapping, and consultation with equipment suppliers and system integrators, is vital. A phased implementation approach might be less disruptive than a full-scale immediate change.
Finally, supply chain dynamics for raw materials used in both molds and potentially the flippers themselves can affect long-term operational costs and availability. Fluctuations in steel or component prices can impact maintenance and replacement parts. While less direct to the flipper’s alignment, ensuring the flipper supports efficient handling of molds made from diverse or newly adopted materials (driven by material innovation or supply chain shifts) helps maintain strategic alignment with cost and material sourcing objectives. Diversifying suppliers for critical components or adopting flippers designed for longevity and with readily available spare parts can mitigate these risks.
By proactively identifying these potential challenges and strategizing solutions, businesses can ensure a smoother integration of mold flipper technology, thereby maximizing its contribution to achieving overarching business objectives and securing a strong return on investment.
Conclusion
Aligning mold flipper capabilities with business objectives is not merely a technical consideration but a strategic imperative for modern manufacturing. It involves a holistic approach, from understanding core demand drivers and selecting appropriate technological features to meticulously measuring impact through relevant KPIs and proactively addressing implementation challenges. When businesses successfully forge this alignment, mold flipper technology transcends its role as mere equipment, becoming a catalyst for enhanced safety, improved operational efficiency, significant cost savings, and ultimately, a stronger competitive position in the market. This strategic integration ensures that investments translate into tangible, sustainable value, driving the business towards its overarching goals.