What Safeguards Can Be Put in Place to Prevent an Individual from Coil Packing Machine Fail
Are you tired of downtime caused by coil packing machine failures? Do you worry about the safety of your personnel operating heavy machinery? Imagine a seamless, efficient coil packing process, free from unexpected breakdowns and, more importantly, safe for every operator. The secret? Robust safeguards. Let’s explore how implementing the right protective measures can revolutionize your coil packing operations, ensuring both productivity and peace of mind.
Implementing comprehensive safeguards is crucial to prevent coil packing machine failures and ensure operator safety. These measures range from physical barriers like fixed guards and interlocked systems to advanced safety devices such as light curtains and two-hand controls. Regular maintenance, thorough risk assessments, and comprehensive training programs are equally vital in creating a safe and efficient coil packing environment.
Ensuring the smooth operation and longevity of your coil packing machine isn’t just about preventing costly repairs; it’s fundamentally about protecting the individuals who work with and around this powerful equipment. Dive in as we unpack the essential safeguards that can make coil packing operations safer and more reliable.
Fixed Guards: The First Line of Defense in Coil Packing Safety
Are you overlooking the simplest, yet most effective, safety measure for your coil packing line? Many facilities rely on complex systems, but often, the most robust solution is also the most straightforward. Fixed guards, offering a permanent physical barrier, are your frontline defense against coil packing machine hazards. Let’s examine how these steadfast protectors can significantly enhance safety and minimize the risk of machine failure.
Fixed guards are permanent barriers designed to prevent access to hazardous areas of a coil packing machine. Constructed from robust materials like sheet metal or wire mesh, they enclose dangerous moving parts such as rollers, belts, and gears, eliminating direct contact and significantly reducing the risk of accidents. Their simplicity and durability make them a cornerstone of effective safeguarding, requiring minimal maintenance while providing maximum protection for operators and minimizing potential machine damage from accidental interference.
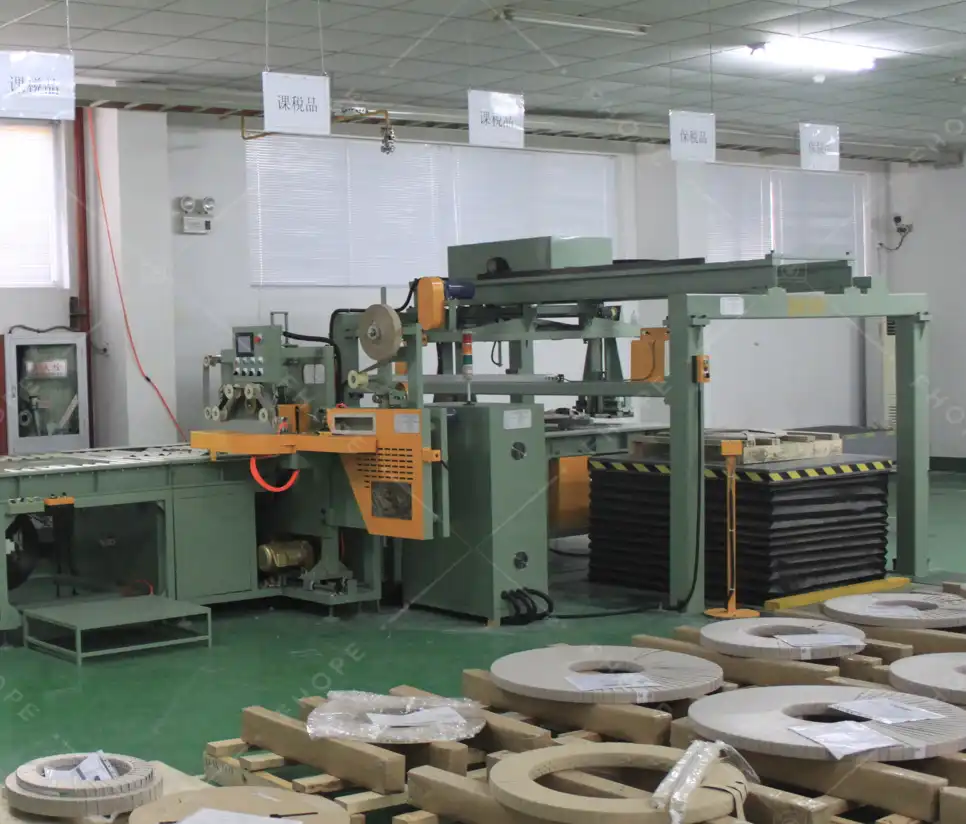
Dive Deeper into Fixed Guard Strategies for Coil Packing Lines
Fixed guards are not merely metal sheets bolted onto machinery; they are strategically designed components integral to a comprehensive safety system. To truly appreciate their effectiveness, let’s dissect their application in coil packing and consider the nuances of implementation.
Understanding Fixed Guard Applications in Coil Packing
The beauty of fixed guards lies in their versatility. In coil packing, they can be deployed across numerous critical points:
- Enclosing Drive Mechanisms: Belts, chains, gears, and motors powering the conveyor systems and wrapping mechanisms are prime candidates for fixed guards. These areas, constantly in motion, pose significant entanglement and crush hazards.
- Point of Operation Isolation: While "point of operation" is less defined in automated packing compared to machining, areas where coils are manipulated, wrapped, or secured can be considered operational zones requiring fixed barriers to prevent accidental entry during cycles.
- Perimeter Guarding for Automated Zones: In fully automated coil packing lines, entire sections might be enclosed by fixed guards, creating safe zones and restricting access to robotic arms and automated handling equipment.
Advantages and Limitations of Fixed Guards: A Detailed Look
To make informed decisions about safeguard implementation, it’s essential to weigh the pros and cons. Fixed guards, while generally preferred, have specific contexts where they excel and areas where alternative solutions might be more appropriate.
Feature | Advantages | Limitations |
---|---|---|
Protection Level | Maximum. Provides a robust physical barrier against hazards. | Can sometimes obstruct visibility of the machine operation, requiring transparent materials in sections. |
Maintenance | Minimal. Durable construction requires very little upkeep. | Machine adjustments or repairs often necessitate guard removal, requiring lockout/tagout procedures. |
Cost | Generally cost-effective due to simple design and minimal moving parts. | May require custom fabrication for complex machine geometries. |
Application | Ideal for permanently hazardous areas, power transmission, and perimeter safety. | Can be less flexible for operations requiring frequent access or adjustments. |
Complexity | Simple to design and install. | Can sometimes complicate routine maintenance tasks if not thoughtfully designed with access points. |
Best Practices for Implementing Fixed Guards
Effective fixed guard implementation goes beyond simply attaching barriers. Consider these best practices:
- Robust Construction: Use materials appropriate for the industrial environment – heavy gauge sheet metal, sturdy wire mesh, and secure fasteners.
- Interference-Free Design: Ensure guards do not interfere with normal machine operation, material flow, or routine adjustments outside of hazardous zones.
- Visibility Considerations: Where visibility is critical, incorporate transparent panels of polycarbonate or safety glass into the guard design.
- Maintenance Access Points: Design guards with access panels secured with tool-requiring fasteners for lubrication, inspection, and minor adjustments within the guarded area, minimizing full guard removal.
- Compliance and Standards: Adhere to relevant safety standards (OSHA, ANSI, ISO) regarding guard construction, opening sizes, and mounting requirements.
By meticulously planning and implementing fixed guards, you create a fundamentally safer coil packing environment, reducing risks and setting the stage for more advanced safeguards to further enhance operator protection.
Interlocked Guards: Smart Safety for Coil Packing Efficiency
Imagine a safeguard that not only physically protects your coil packing operators but also intelligently responds to their actions, halting dangerous processes the moment a hazard is detected. Interlocked guards bring this intelligent safety to life, adding a layer of dynamic protection that fixed guards alone cannot provide. Let’s explore how these "smart" guards elevate safety protocols in modern coil packing facilities.
Interlocked guards are designed to automatically shut down the coil packing machine’s power when the guard is opened or removed, preventing operation while a hazardous area is accessible. This system, utilizing electrical, mechanical, or pneumatic interlocks, ensures that moving parts are completely stopped before an operator can reach into a danger zone. Interlocked guards offer a superior level of safety by actively controlling machine operation based on guard status, allowing for safe access during maintenance and jam clearing while preventing accidental restarts.
Delving into Interlocked Guard Technology and Application
Interlocked guards are more than just barriers; they are integrated safety systems. To fully grasp their value, we need to examine the technology behind them and how they are strategically applied within coil packing lines.
The Mechanics of Interlocked Guard Systems
At their core, interlocked guards function through a simple yet crucial principle: interruption of the power supply upon guard breach. This is achieved through various interlocking mechanisms:
- Electrical Interlocks: These are the most common, using safety switches wired into the machine’s control circuit. Opening the guard breaks the circuit, immediately stopping the machine. Safety relays or safety PLCs are often used to ensure high reliability and fault tolerance.
- Mechanical Interlocks: Employ physical linkages that disengage clutches or brakes when the guard is opened. These are often found in older machinery but can be less reliable than electrical systems in modern, high-speed lines.
- Pneumatic/Hydraulic Interlocks: Utilize valves that dump pressure in pneumatic or hydraulic systems when the guard is breached, causing an immediate stop. These are suitable for machines primarily powered by fluid systems.
Strategic Placement of Interlocked Guards in Coil Packing
Interlocked guards are particularly valuable in coil packing areas requiring occasional operator access for tasks like:
- Jam Clearing: Coil lines, especially slitting and cut-to-length operations, can experience jams. Interlocked guards on access points allow operators to safely intervene without full power isolation procedures for minor clears.
- Maintenance Zones: Areas requiring frequent but non-routine maintenance, such as wrapping heads or strapping units, benefit from interlocked access points, streamlining servicing while maintaining a high safety level during operation.
- Inspection Stations: If manual quality checks are integrated into the line, interlocked guards at inspection points allow for safe access for brief periods without halting the entire process.
Advantages and Considerations of Interlocked Guards
While offering enhanced safety and operational flexibility, interlocked guards also present certain considerations for implementation:
Feature | Advantages | Limitations |
---|---|---|
Safety Level | High. Actively prevents machine operation when guards are not properly in place. | Requires careful adjustment and regular maintenance to ensure interlock reliability. |
Accessibility | Allows safe access for authorized personnel for specific tasks without full system shutdown. | Can be bypassed or defeated if not properly designed and implemented with tamper-resistant switches and controls. |
Efficiency | Minimizes downtime compared to full lockout/tagout for minor interventions. | May slow down certain operations if frequent guard opening/closing is required. |
Cost | Moderate to high, depending on the complexity of the interlock system and integration with existing controls. | Requires skilled personnel for installation, maintenance, and troubleshooting of electrical/mechanical systems. |
Complexity | More complex than fixed guards, requiring electrical/mechanical integration and robust safety control circuitry. | Potential for nuisance stops if interlocks are overly sensitive or not properly adjusted to environmental factors like vibration. |
Ensuring Interlocked Guard Effectiveness
To maximize the benefits of interlocked guards, adhere to these key principles:
- Robust Interlock Mechanisms: Use safety-rated interlock switches and components certified to relevant standards (e.g., EN ISO 14119).
- Fail-Safe Design: Ensure the interlock system is designed to fail to a safe state – i.e., machine stops upon any component failure within the safety circuit.
- Tamper Resistance: Use tamper-resistant switches and mounting methods to prevent unauthorized bypassing or defeat of the interlock system.
- Regular Inspection and Testing: Implement a rigorous schedule for inspecting and functionally testing interlock systems to verify proper operation and identify any potential faults.
- Training and Procedures: Train all operators, maintenance personnel, and authorized users on the correct operation, limitations, and importance of interlocked guards, as well as procedures for jam clearing and maintenance within interlocked zones.
Interlocked guards represent a significant step up in coil packing safety, blending robust physical protection with intelligent control systems. When properly implemented and maintained, they create a safer and more efficient operational environment.
Adjustable and Self-Adjusting Guards: Flexible Safeguards for Dynamic Coil Handling
In the diverse world of coil packing, not all coils are created equal. Varying sizes, shapes, and processing needs demand flexible safeguarding solutions that adapt to the dynamic nature of operations. Adjustable and self-adjusting guards rise to this challenge, offering protection that conforms to the changing parameters of coil handling. Let’s examine how these adaptable safeguards enhance safety without compromising operational versatility.
Adjustable guards allow manual repositioning to accommodate different coil sizes or operational needs, providing a barrier that can be tailored to specific production runs. Self-adjusting guards, even more dynamically, automatically adapt their opening based on the size of the coil entering the hazardous area, offering continuous optimal protection without manual intervention. Both types provide enhanced flexibility in safeguarding, crucial for coil packing lines handling diverse product ranges, ensuring consistent safety across varying operational parameters.
Exploring Adaptable Guarding for Versatile Coil Packing
Adjustable and self-adjusting guards address a critical need in coil packing – the ability to safeguard operations without sacrificing the flexibility required to handle a wide range of coil specifications.
Adjustable Guards: Manually Tailored Protection
Adjustable guards offer a balance between fixed protection and operational adaptability. Key features include:
- Manual Repositioning: Operators can adjust the guard’s position, height, or opening size using hand knobs, levers, or simple tools.
- Versatility for Batch Production: Ideal for lines handling batches of coils with similar dimensions, where guards can be adjusted at setup and remain fixed for the production run.
- Examples in Coil Packing: Adjustable barrier guards around wrapping stations or strapping units can be modified to suit different coil diameters or widths. Adjustable shields on conveyor sections can accommodate varying coil heights.
Self-Adjusting Guards: Dynamic, Automated Safety
Self-adjusting guards take flexibility to the next level, offering automated adaptation:
- Stock-Responsive Movement: Guards automatically move based on the coil’s size and position, opening only as much as necessary for material passage and immediately returning to the protective position.
- Continuous Optimal Guarding: Provides the smallest possible opening at all times, maximizing safety without operator intervention during production.
- Examples in Coil Packing: Self-adjusting guards are well-suited for in-feed points to wrapping machines or strapping heads, where coils of varying sizes are continuously processed. They can also be used on conveyor sections where coil dimensions might fluctuate.
Advantages and Practicalities of Flexible Guards
Choosing between adjustable and self-adjusting guards depends on the specific operational context and level of automation desired:
Feature | Adjustable Guards | Self-Adjusting Guards |
---|---|---|
Flexibility | Good. Manually adaptable to different coil sizes and operations. | Excellent. Automatically adapts to varying coil sizes in real-time. |
Response Time | Manual adjustment required between batches or size changes. | Dynamic and immediate, adjusting with each coil. |
Operator Involvement | Requires operator setup and adjustment; potential for inconsistent adjustments. | Minimizes operator intervention, ensuring consistent safeguarding regardless of operator variability. |
Safety Consistency | Dependent on correct manual adjustment; potential for human error in setup. | High. Provides consistently optimal protection as guard adapts automatically. |
Cost | Lower to moderate, depending on complexity of adjustment mechanisms. | Moderate to higher, due to more complex mechanical design and potentially sensors or actuators for automated movement. |
Maintenance | Moderate. Requires periodic checks of adjustment mechanisms. | Moderate to high. May require more frequent maintenance due to moving parts and potential for sensor calibration. |
Optimizing Flexible Guard Implementation
To effectively utilize adjustable and self-adjusting guards:
- Match Guard Type to Operational Needs: Choose adjustable guards for batch production with infrequent size changes; opt for self-adjusting guards for continuous lines with variable coil dimensions.
- Robust Adjustment Mechanisms: Ensure adjustable guards have sturdy, easily manipulated, and lockable adjustment mechanisms to prevent drift or unauthorized alteration.
- Reliable Self-Adjustment: For self-adjusting guards, select robust mechanisms (mechanical linkages, pneumatic cylinders, etc.) and reliable sensors that can withstand the industrial environment and ensure consistent, accurate response.
- Clear Adjustment Indicators: For adjustable guards, provide clear scales or indicators to guide operators in making correct adjustments for different coil sizes, reducing guesswork and errors.
- Regular Checks and Maintenance: Implement schedules for inspecting and maintaining both adjustable and self-adjusting guards, ensuring mechanisms are free of debris, move smoothly, and are correctly calibrated.
Adjustable and self-adjusting guards provide essential flexibility in coil packing safety, enabling facilities to handle diverse product lines without compromising operator protection. By carefully selecting and implementing these adaptable safeguards, you can achieve both safety and operational efficiency.
Advanced Safety Devices: Elevating Coil Packing Protection Beyond Physical Barriers
While physical guards form the foundation of coil packing safety, advanced safety devices offer a sophisticated layer of protection, going beyond simple barriers to actively sense and respond to potential hazards. These technologies, ranging from light curtains to safety scanners, create dynamic safety zones and enable more nuanced safeguarding strategies. Let’s explore how these cutting-edge devices revolutionize safety protocols in modern coil packing environments.
Advanced safety devices in coil packing extend protection beyond physical barriers by using electro-sensitive technologies to detect operator presence near hazardous areas. Light curtains create invisible safety planes, immediately stopping machine motion when breached. Safety laser scanners establish customizable safety zones, slowing or stopping machinery based on proximity. Two-hand controls require operators to use both hands to initiate machine cycles, ensuring hands are safely away from danger zones. These devices, integrated with sophisticated safety controllers, provide a dynamic and responsive safety system, enhancing both operator protection and production efficiency by allowing for more flexible and ergonomic workflows compared to traditional guards alone.
Unpacking Advanced Safety Technologies in Coil Packing
Advanced safety devices represent a paradigm shift in machine safeguarding, moving from passive barriers to active, intelligent protection. Let’s dissect some key technologies and their application in coil packing.
Electro-Sensitive Protective Equipment (ESPE): Light Curtains and Safety Scanners
ESPE, encompassing light curtains and safety laser scanners, are at the forefront of advanced safeguarding:
- Light Curtains: These create a vertical or horizontal "curtain" of light beams. If any beam is broken by an operator’s hand, arm, or body, the safety controller immediately signals the machine to stop. Light curtains are ideal for guarding access points to hazardous zones like wrapping heads, strapping units, or conveyor transfer points.
- Safety Laser Scanners: Emit pulsed laser beams to create customizable 2D safety zones. These zones can be configured for warning and danger levels, slowing down or stopping the machine based on operator proximity. Safety scanners are particularly useful for area guarding around robotic cells or within larger automated sections of a coil packing line, offering flexible protection zones that adapt to different operational modes.
Two-Hand Controls: Ensuring Intentional and Safe Operation
Two-hand controls are a classic yet still vital safety device, especially in semi-automated coil packing tasks:
- Concurrent Operation Requirement: These systems require the operator to press and hold two spatially separated buttons or controls simultaneously to initiate a machine cycle. This ensures that both hands are intentionally engaged and safely positioned away from the point of operation during startup.
- Application in Coil Packing: Two-hand controls are suitable for manually initiated steps in coil packing processes, such as activating clamps, presses, or certain wrapping functions, where operator hand placement near the action point could be hazardous if controls were single-hand operated.
Advantages of Advanced Safety Devices in Coil Packing
Integrating advanced safety devices offers numerous benefits:
- Enhanced Ergonomics: Compared to bulky physical guards, ESPE and two-hand controls can allow for more open and ergonomic workspaces, improving operator comfort and efficiency.
- Increased Flexibility: ESPE, particularly safety scanners, enable flexible safety zones that can be reconfigured for different production needs or machine layouts, adapting to evolving operational requirements.
- Improved Visibility: Light curtains and laser scanners do not obstruct the view of the machine operation, facilitating monitoring and troubleshooting.
- Faster Intervention: ESPE can trigger machine stops faster than some mechanical guards or traditional safety circuits, minimizing potential injury in dynamic situations.
- Integration with Automation: Advanced safety devices are readily integrated with modern automated coil packing lines, complementing robotic systems and sophisticated control architectures.
Considerations for Advanced Safety Device Implementation
Successful implementation requires careful planning and expertise:
- Risk Assessment is Paramount: Proper selection and placement of advanced safety devices must be based on a thorough risk assessment to identify specific hazards, required safety levels, and appropriate device types.
- Safety Controller Integration: Advanced safety devices require integration with safety-rated controllers (safety PLCs or safety relays) to ensure proper functioning of the entire safety system and achieve desired safety levels (Performance Level or Safety Integrity Level).
- Proper Installation and Commissioning: Correct installation, alignment, and commissioning by trained personnel are crucial for device effectiveness and reliability.
- Regular Verification and Validation: Periodic testing and validation of advanced safety devices and their integration with the machine control system are mandatory to maintain safety integrity over time.
- Operator Training is Essential: Operators must be thoroughly trained on the function, limitations, and proper interaction with advanced safety devices. They need to understand how the devices protect them and what behaviors are required to maintain a safe working environment.
Advanced safety devices are not a replacement for fundamental safeguarding principles like risk assessment and layered protection. Rather, they represent a powerful enhancement, enabling coil packing facilities to achieve higher levels of safety, flexibility, and operational efficiency in increasingly automated environments.
Conclusion
In the demanding environment of coil packing, where heavy materials and powerful machinery are the norm, safety guard implementation is not merely a compliance exercise—it’s a fundamental operational imperative. By strategically layering fixed, interlocked, adjustable, and self-adjusting guards with advanced safety devices like light curtains and two-hand controls, facilities can create a robust safety ecosystem. This multi-faceted approach, coupled with rigorous risk assessment, consistent maintenance, and comprehensive operator training, ensures a coil packing process that is not only efficient and productive but, above all, safe for every individual involved. Embracing these safeguards is an investment in your workforce, your equipment, and the long-term success of your coil packing operations. Learn more about coil packing line solutions that prioritize safety and efficiency.