What Are the Challenges of Implementing Steel Wire Drawing Machines in Small-Scale Industries?
Implementing steel wire drawing machines presents unique hurdles for small-scale industries. These range from financial constraints and space limitations to skill gaps and material sourcing issues. Overcoming these challenges is crucial for competing effectively.
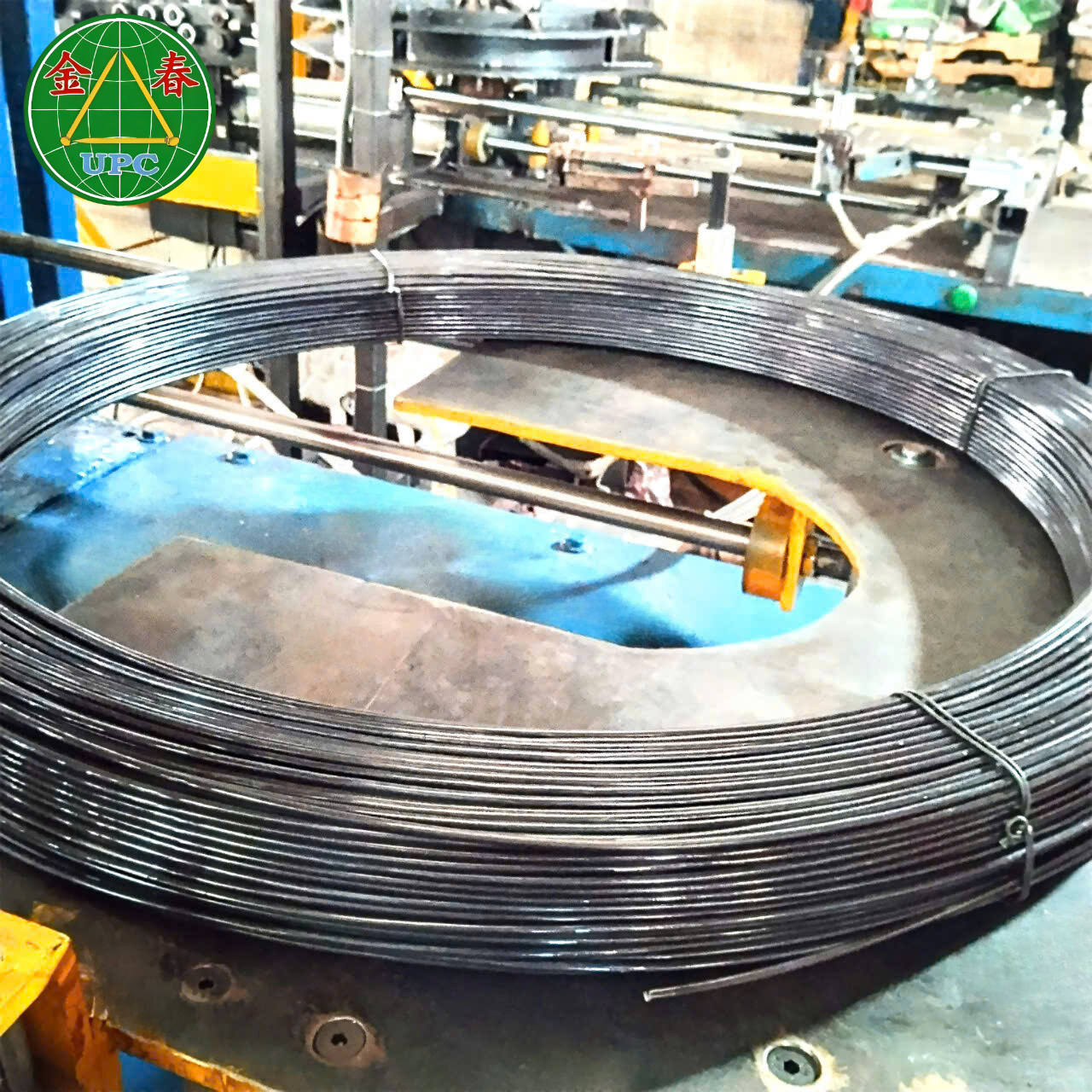
Implementing steel wire drawing machines in small-scale industries faces hurdles like high initial costs for equipment and training. Limited space in smaller facilities poses layout and workflow challenges. Securing skilled operators and technicians and consistent material quality and supply can be difficult, impacting overall productivity and profitability.
Transitioning to steel wire drawing can be a game-changer for small businesses. But what exactly makes this upgrade so tricky? Let’s break down the key challenges and explore ways to navigate them.
1. Financial Constraints and Investment Justification
Small-scale industries often struggle with limited capital. Investing in steel wire drawing machines requires a significant upfront expenditure. Justifying this investment becomes a critical hurdle.
The primary financial challenge is the high cost of machinery. This includes not only the purchase price but also installation, maintenance, and operational expenses. Small businesses must carefully evaluate the return on investment (ROI) and explore financing options.
Navigating the Financial Landscape: A Detailed Breakdown
Investing in a steel wire drawing machine implementation requires careful financial planning. Small businesses need to consider various cost factors and explore strategies to mitigate financial risks. A detailed cost-benefit analysis is essential.
Initial Investment Costs
The initial investment encompasses several components, including the machine itself, auxiliary equipment, installation, and initial training.
Cost Component | Description | Example Costs (USD) |
---|---|---|
Wire Drawing Machine | The cost of the machine itself, which can vary based on capacity, automation level, and features. | $50,000 – $200,000 |
Auxiliary Equipment | Includes items like wire feeders, spoolers, and quality control instruments. | $10,000 – $30,000 |
Installation | Costs for setting up the machine, including transportation, assembly, and calibration. | $5,000 – $15,000 |
Initial Training | Training for operators and maintenance personnel on the operation and maintenance of the machine. | $2,000 – $5,000 |
Operational Costs
Operational costs are ongoing expenses that impact the long-term profitability of the investment.
Cost Component | Description | Example Costs (Annual) |
---|---|---|
Raw Materials | The cost of steel wire rods, which is a major factor in overall operational costs. | Varies with market |
Energy Consumption | Electricity costs for running the machine, which can be significant depending on the machine’s power requirements. | $5,000 – $15,000 |
Maintenance | Regular maintenance, including replacement of worn parts, lubrication, and servicing. | $2,000 – $5,000 |
Labor | Salaries for machine operators, maintenance personnel, and quality control staff. | $40,000 – $80,000 |
Strategies for Overcoming Financial Hurdles
Small-scale industries can employ several strategies to mitigate the financial burden:
- Leasing Options: Leasing allows businesses to use the equipment without a large upfront investment. Lease payments are typically lower than the cost of purchasing the machine outright.
- Government Grants and Subsidies: Many governments offer grants and subsidies to encourage technological upgrades. Researching and applying for these programs can significantly reduce costs.
- Cost-Benefit Analysis: A thorough cost-benefit analysis helps determine whether the investment is financially viable. This includes assessing the potential increase in production, reduction in waste, and improvement in product quality.
- Phased Implementation: Implementing the technology in phases can spread out the costs over time. Starting with a smaller, more affordable machine and gradually scaling up as the business grows can make the investment more manageable.
- Collaborative Partnerships: Partnering with other small businesses or industry associations can provide access to shared resources and reduce individual costs. This can include joint purchasing of equipment or shared training programs.
By carefully considering these financial aspects and employing strategic mitigation measures, small-scale industries can successfully implement steel wire drawing machines and reap the benefits of improved efficiency and product quality.
2. Space Limitations and Facility Layout
Limited space can pose a significant challenge. Steel wire drawing machines, along with necessary storage and workflow areas, require a certain amount of square footage that may not be readily available.
Space limitations impact the layout and workflow. Cramped conditions can lead to inefficiencies, safety hazards, and difficulties in material handling. Optimizing the facility layout is crucial for maximizing productivity and minimizing disruptions.
Optimizing Space: A Comprehensive Approach to Facility Design
Successfully integrating a steel wire drawing machine into a small-scale industry requires thoughtful space optimization. Overcoming space limitations involves strategic planning and efficient layout design to maximize productivity and ensure safety.
Understanding Space Requirements
Before implementing the machine, a thorough assessment of available space is essential. This assessment should consider not only the machine’s footprint but also the space needed for material storage, movement, and maintenance. A detailed space analysis helps in creating a practical and efficient layout.
Area | Description | Minimum Space Requirement |
---|---|---|
Machine Footprint | The physical space occupied by the steel wire drawing machine. | 200-400 sq. ft. |
Material Storage | Space for storing raw materials (steel wire rods) and finished products. | 100-200 sq. ft. |
Workflow Area | Space for operators to move around the machine, perform maintenance, and conduct quality control checks. | 50-100 sq. ft. |
Maintenance Access | Space for accessing machine components for maintenance and repairs. | 50-100 sq. ft. |
Strategies for Efficient Space Utilization
- Vertical Storage Solutions: Utilizing vertical storage systems can maximize the use of available space. This includes installing shelving units, racks, and vertical carousels for storing raw materials and finished products. Vertical storage reduces the footprint needed for storage and frees up valuable floor space.
- Modular Machine Design: Opting for modular machines allows for flexible configuration and easy adaptation to available space. Modular designs can be reconfigured to fit into tight spaces or expanded as the business grows.
- Lean Manufacturing Principles: Applying lean manufacturing principles can streamline workflows and eliminate unnecessary steps. This includes organizing the workspace to minimize movement and reduce clutter, improving overall efficiency.
- Multi-Purpose Areas: Designing areas that can serve multiple functions helps in maximizing space utilization. For example, a maintenance area can also be used for training or quality control checks, optimizing the use of available space.
- Strategic Machine Placement: Positioning the machine strategically can improve workflow and reduce congestion. This includes considering the flow of materials, the location of power sources, and the proximity to other equipment.
Case Study: Space Optimization in a Small Workshop
Consider a small workshop with limited floor space. By implementing vertical storage solutions and reorganizing the workflow, the workshop can accommodate a steel wire drawing machine without compromising safety or efficiency.
- Initial Layout: A cramped workshop with inefficient material storage and cluttered pathways.
- Proposed Solution: Implementing vertical storage racks for raw materials and finished products, streamlining the workflow, and reorganizing the machine layout.
- Outcome: Improved space utilization, reduced congestion, and enhanced workflow efficiency, allowing the workshop to accommodate the new machine while maintaining safety and productivity.
By adopting a comprehensive approach to space optimization, small-scale industries can overcome the challenges of limited space and successfully integrate steel wire drawing machines into their operations.
3. Skill Gaps and Training Requirements
Operating and maintaining steel wire drawing machines requires specialized skills. Small-scale industries often face challenges in finding and retaining qualified personnel.
Skill gaps can lead to operational inefficiencies, increased downtime, and higher maintenance costs. Investing in training programs and skill development is crucial for bridging these gaps and ensuring the successful operation of the machines.
Building a Skilled Workforce: Strategies for Training and Development
Addressing skill gaps and training requirements is paramount for the successful implementation of steel wire drawing machines in small-scale industries. A well-trained workforce ensures optimal machine operation, reduces downtime, and enhances overall productivity.
Identifying Skill Gaps
The first step in building a skilled workforce is to identify the specific skills required for operating and maintaining the machines. This includes technical skills, such as machine operation, maintenance, and troubleshooting, as well as soft skills, such as problem-solving and teamwork.
Skill Category | Specific Skills | Importance |
---|---|---|
Machine Operation | Operating the steel wire drawing machine, setting parameters, and monitoring performance. | Essential for producing high-quality wire products, maximizing machine efficiency, and minimizing waste. |
Maintenance | Performing routine maintenance, troubleshooting mechanical issues, and repairing machine components. | Critical for preventing breakdowns, extending machine lifespan, and reducing downtime. |
Quality Control | Conducting quality checks, identifying defects, and ensuring compliance with industry standards. | Necessary for maintaining product quality, meeting customer requirements, and minimizing rework. |
Safety | Following safety protocols, using personal protective equipment (PPE), and responding to emergencies. | Vital for preventing accidents, ensuring worker safety, and complying with regulatory requirements. |
Strategies for Training and Development
- In-House Training Programs: Developing comprehensive in-house training programs tailored to the specific needs of the machines and the workforce can effectively address skill gaps. These programs should cover all aspects of machine operation, maintenance, and safety.
- Apprenticeship Programs: Partnering with local vocational schools and technical colleges to offer apprenticeship programs can provide a structured pathway for developing skilled workers. Apprenticeship programs combine classroom instruction with on-the-job training.
- Online Training Resources: Utilizing online training resources, such as webinars, tutorials, and e-learning platforms, can provide flexible and cost-effective training options. Online training can supplement in-house programs and offer ongoing professional development.
- Vendor Training: Engaging with machine vendors to provide training on the operation and maintenance of their equipment can ensure that the workforce is proficient in using the machines. Vendor training often includes hands-on instruction and access to technical support.
Case Study: Successful Training Program Implementation
Consider a small-scale industry that implemented a comprehensive training program for its workforce after investing in a steel wire drawing machine. The program included:
- Initial Assessment: Conducted a thorough assessment of the workforce’s existing skills and identified specific training needs.
- Customized Training Modules: Developed customized training modules covering machine operation, maintenance, quality control, and safety.
- Hands-On Training: Provided hands-on training on the machine, allowing workers to practice operating and troubleshooting the equipment.
- Ongoing Support: Offered ongoing support and mentorship to workers, ensuring they had access to the resources and guidance needed to succeed.
As a result of the training program, the company experienced improved machine efficiency, reduced downtime, and enhanced product quality. The workforce became more skilled and confident in operating and maintaining the steel wire drawing machine, contributing to the company’s overall success.
4. Material Sourcing and Quality Control
Small-scale industries may face challenges in sourcing high-quality steel wire rods at competitive prices. Maintaining consistent material quality is essential for producing high-quality drawn wire.
High-quality materials are crucial for CNC machining to produce superior parts. At 3ERP, we ensure that materials are not only of high grade but are also handled and stored correctly to prevent any damage or degradation before machining begins.
Inconsistent material quality can lead to defects in the final product, increased waste, and higher production costs. Establishing reliable sourcing channels and implementing rigorous quality control measures is crucial for addressing these challenges and ensuring the consistent production of high-quality steel wire.
- Sourcing raw materials: A small-scale industry might require high-quality steel wire rods, which are sourced at competitive prices to maintain consistent material quality.
- Quality control: Implement quality control measures by inspecting incoming materials, conducting in-process checks, and performing final product testing to ensure that the steel wire meets the required specifications.
Implementing steel wire drawing machines in small-scale industries presents a series of complex challenges. Addressing these challenges effectively is essential for improving productivity and profitability in the long run.
Conclusion
Implementing steel wire drawing machines in small-scale industries presents unique challenges, including financial constraints, space limitations, skill gaps, and material sourcing issues. By strategically addressing these hurdles, small businesses can enhance their capabilities and improve their competitive edge. Careful planning, investment in training, and optimization of resources are key to successful implementation and long-term growth,and using wire drawing machine can achieve great efficiency and quality.