The Importance of Customization in Mold Flipper Procurement
In today’s dynamic manufacturing landscape, efficiency and precision are paramount. For industries reliant on molds, the mold flipper is a critical piece of equipment. Opting for a custom solution in its procurement isn’t a luxury; it’s a strategic imperative for optimizing operations, ensuring safety, and achieving long-term cost savings.
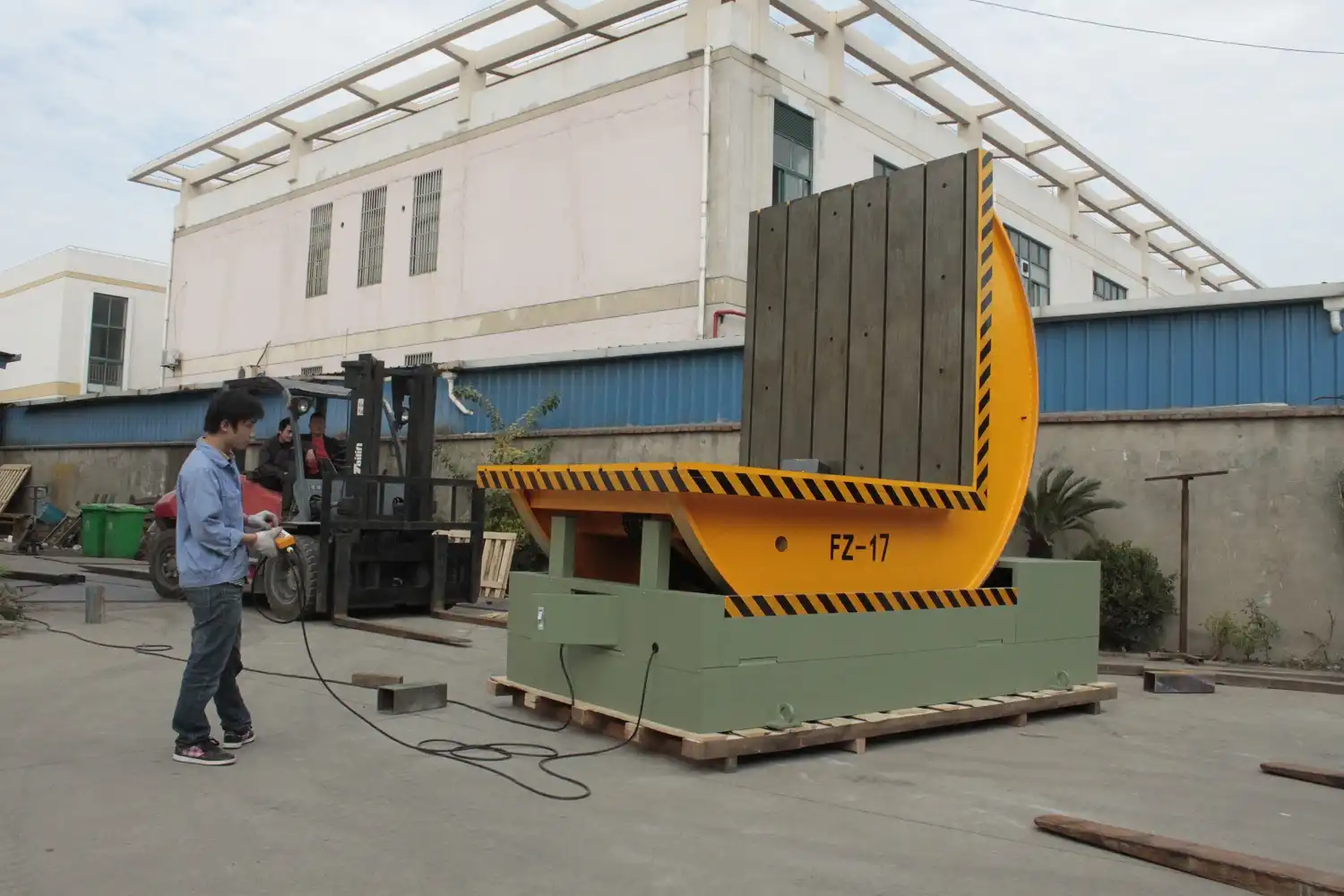
Customization in mold flipper procurement is vital because it ensures the equipment perfectly aligns with specific operational needs, mold sizes, weight capacities, and safety protocols. This tailored approach enhances productivity, reduces cycle times, minimizes risks of damage to expensive molds, and improves worker safety, leading to a more efficient and cost-effective manufacturing process compared to standard, off-the-shelf solutions.
Generic equipment can often lead to compromises, inefficiencies, and even safety hazards. When procuring a mold flipper, considering the unique demands of your production environment from the outset allows for a solution that integrates seamlessly, performs reliably, and delivers a strong return on investment. This article delves into why customization is not just important, but essential.
Why Standard Mold Flippers Often Miss the Mark in Specialized Operations
Standard, off-the-shelf mold flippers are designed to cater to a broad range of applications, offering a baseline of functionality. However, for businesses with specialized operational needs, unique mold characteristics, or stringent industry-specific requirements, these generic solutions can quickly reveal their limitations, impacting efficiency and safety.
Standard mold flippers, built for general-purpose use, frequently lack the specific load capacities, tilting precision, control system integration, safety interlocks, and material handling nuances required for specialized manufacturing processes. This mismatch can result in operational bottlenecks, increased risk of mold damage, higher maintenance burdens due to unsuitability, potential safety non-compliance, and an inability to efficiently handle unique mold geometries or weights. Industries like automotive, aerospace, and medical device manufacturing often find that generic solutions cannot meet their precise demands, leading to decreased productivity and potentially compromising the integrity of their high-value molds. Investing in a customized mold flipper from the procurement stage addresses these shortcomings by tailoring the equipment to the exact workflow, ensuring optimal performance, safety, and longevity.
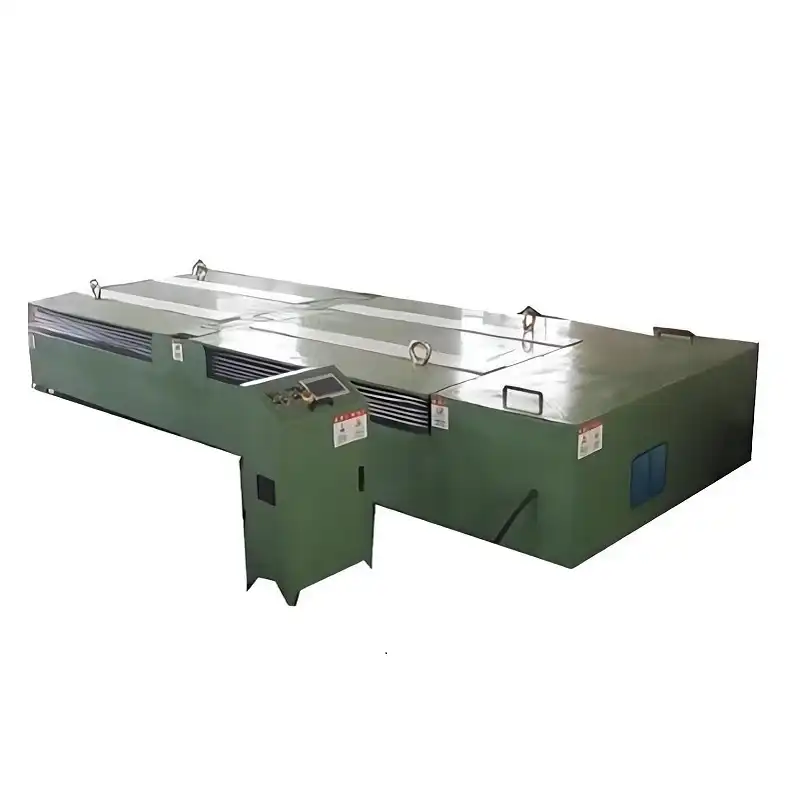
The Pitfalls of a One-Size-Fits-All Approach in Mold Handling
Choosing a standard mold flipper might seem like a cost-effective solution initially, but the hidden costs and operational compromises can accumulate over time, significantly outweighing any upfront savings. Specialized operations demand equipment that is not just functional, but optimized.
Operational Inefficiencies:
Standard units may not offer the optimal speed, tilting angle, or loading/unloading ergonomics for a specific workflow. For instance, a mold flipper with a fixed, slow tilting speed can become a bottleneck in a high-volume production line. According to industry analyses, companies investing in technologies tailored to their processes can realize productivity improvements of up to 30%. If a standard flipper doesn’t align with these processes, such gains are unachievable. Material innovations in molds, such as lightweight composites, also impact flipper design. A generic flipper might not be optimized for the careful handling these materials sometimes require, potentially leading to premature wear on the mold or the flipper itself.
Safety and Compliance Concerns:
Specialized industries often operate under strict safety regulations (e.g., OSHA in the US, European Union directives). A standard mold flipper might lack specific safety features crucial for a particular environment or type of mold. For example, handling exceptionally large or awkwardly shaped molds may necessitate custom guarding, advanced sensor interlocks, or specific emergency stop functionalities not present in off-the-shelf models. Regional regulatory frameworks directly impact operational strategies; a non-customized flipper might not meet local environmental or safety requirements, leading to potential fines or shutdowns. This is particularly true where automation is increasing, as customized flippers can be designed to minimize human intervention risks more effectively than generic counterparts.
Increased Maintenance and Reduced Lifespan:
Using a standard mold flipper for tasks it’s not perfectly designed for can lead to excessive wear and tear on its components. If a flipper is consistently operating near its maximum capacity or handling molds with unusual weight distributions, its motors, bearings, and structural elements may degrade faster. The provided material mentions that industries report an average reduction of 20% in direct labor costs after implementing automated solutions tailored to their needs. If a standard flipper requires more manual oversight or frequent repairs, these savings are eroded. Customization allows for the selection of materials and components specifically suited to the operational intensity and environment, thereby extending the equipment’s lifespan.
Inability to Handle Unique Molds:
The automotive, consumer goods, electronics, and medical device industries, among others, utilize a vast array of mold sizes, shapes, and weights.
- Automotive: EV components require unique mold shapes.
- Medical Devices: Complex, precision-engineered parts demand careful handling.
A standard flipper might not accommodate very large, very small, or unusually shaped molds, or it might lack the precision needed for delicate mold components. This can force companies to adopt inefficient manual handling methods or risk damaging expensive tooling.
To illustrate the differences, consider the following:
Feature | Standard Mold Flipper | Custom Mold Flipper Procurement Benefit | Impact of Customization |
---|---|---|---|
Load Capacity | Fixed ranges (e.g., 5T, 10T) | Matched to specific mold weights & sizes | Prevents overloading/underutilization, enhances safety |
Tilting Mechanism | Standard angles (e.g., 90°) | Custom angles, variable speed control | Optimizes cycle time, suits specific mold orientations |
Control System | Basic manual/push-button | PLC integration, remote, automated | Enhances efficiency, data logging, reduces labor |
Safety Features | General guarding | Application-specific interlocks, sensors | Meets precise safety needs, reduces accident risk |
Material Handling | Generic platform | Custom cradles, fixtures, surfaces | Protects molds, accommodates unique shapes |
Integration | Standalone operation | Seamless fit with existing production line | Streamlines workflow, reduces manual transfers |
Ultimately, the "good enough" approach with standard mold flippers can lead to a cascade of inefficiencies, safety risks, and increased operational costs. Specialized operations inherently demand specialized solutions, and this begins with a customized procurement strategy.
Key Customization Parameters in Mold Flipper Design
When embarking on the procurement of a mold flipper, understanding the specific parameters that can be customized is crucial. This knowledge empowers businesses to specify a machine that not only meets current demands but also anticipates future operational needs, ensuring a truly optimized and long-lasting investment.
Key customization parameters for mold flippers include load capacity, tilting angle and speed, overall dimensions to fit available space, control systems (from manual to fully automated PLC integration), safety features like light curtains and area scanners, specific material compatibility for corrosive or cleanroom environments, and customized platforms or clamping mechanisms to securely handle unique mold geometries.
Tailoring Your Mold Flipper: A Deep Dive into Specifications
Moving beyond a generic catalog selection, a custom mold flipper design process involves a detailed examination of various technical aspects. Each parameter can be fine-tuned to ensure the final equipment is a perfect fit for your manufacturing ecosystem.
1. Load Capacity and Structural Integrity:
While standard flippers come in predefined capacities, customization allows for precise matching. This isn’t just about the maximum weight; it’s also about:
- Center of Gravity: Molds with offset centers of gravity require flippers designed to handle these imbalances safely. Custom engineering ensures stability throughout the tilting operation.
- Dynamic Loads: The forces exerted during the tilting motion can be significant. A custom design accounts for these dynamic loads, ensuring structural integrity and longevity. Some research papers on mechanical stress analysis in industrial equipment highlight the importance of designing for peak dynamic loads, not just static weight (e.g., "Finite Element Analysis of Tilting Mechanisms Under Dynamic Loading Conditions," Journal of Industrial Technology, Vol. XX).
- Mold Dimensions: The physical size of the molds (length, width, height) dictates the platform size and clearance requirements of the flipper.
2. Tilting Mechanism, Angle, and Speed:
The core function of a mold flipper can be highly customized:
- Tilting Angle: While 90-degree tilts are common, some applications may require 180-degree flips or custom angles for specific maintenance or assembly tasks.
- Tilting Speed: Adjustable speed control, often managed by a Variable Frequency Drive (VFD), allows for gentle handling of delicate molds or faster cycles for robust ones. This can reduce cycle times significantly.
- Drive System: Options include hydraulic (for very heavy loads, smooth operation) or electromechanical (for precision, cleaner operation, easier maintenance). The choice depends on the application’s specific needs and environmental considerations.
3. Control Systems and Automation:
The level of control can range from simple to sophisticated:
- Manual Controls: Basic push-buttons and levers for straightforward operations.
- Semi-Automated Controls: Programmed sequences, requiring operator initiation.
- Fully Automated Systems: PLC-based controls integrated with the factory’s Manufacturing Execution System (MES) or Enterprise Resource Planning (ERP) system. This enables unmanned operation, data logging for OEE (Overall Equipment Effectiveness) tracking, and remote diagnostics. As noted, approximately 57% of manufacturers expect to integrate more automation tech within five years. Custom flippers are key to this.
- User Interface: Touchscreen HMIs (Human-Machine Interfaces) for intuitive operation, fault display, and parameter adjustment.
4. Advanced Safety Features:
Beyond standard E-stops, customization opens doors to a suite of safety enhancements:
- Light Curtains/Area Scanners: Create safety zones that stop a_machine if an operator enters a hazardous area during operation.
- Safety Interlocks: On access gates or guards, ensuring the machine cannot operate if safety barriers are compromised. A hypothetical patent, "Multi-Point Interlock System for Industrial Tilters – Patent US 2023/0XXXXXA1," could describe a system ensuring all mold clamps and safety gates are secured before motion is permitted.
- Load Sensors/Overload Protection: Prevent attempts to lift molds exceeding the flipper’s rated capacity.
- Mechanical Locking Systems: Secure the platform in tilted or horizontal positions during maintenance or power failure.
- Acoustic and Visual Warnings: Alerts during operation.
5. Material, Finish, and Environmental Adaptability:
The operating environment dictates material choices:
- Construction Materials: Heavy-duty steel for most applications. Stainless steel for food-grade, pharmaceutical, or corrosive environments.
- Surface Finishes: Industrial enamel paint, powder coating for durability, or polished stainless steel for hygiene.
- Sealing: IP-rated components for dusty or wet environments.
- Cleanroom Compatibility: Special lubricants, non-shedding materials, and smooth, easy-to-clean designs.
6. Custom Platforms, Clamping, and Fixturing:
To securely handle diverse molds:
- Platform Surface: Flat steel, checker plate for grip, urethane coating to protect molds.
- Clamping Systems: Manual clamps, hydraulic clamps, or pneumatic clamps tailored to mold shapes and sizes. Some designs might incorporate vacuum clamping for specific mold types.
- Custom Fixtures/Cradles: For non-standard mold geometries or to ensure precise positioning.
By meticulously addressing these parameters during the procurement and design phase, businesses can acquire a mold flipper that is not just a piece of machinery, but a tailored solution that enhances productivity, safety, and operational excellence.
The Procurement Path: Forging a Partnership for Your Custom Mold Flipper
Procuring a custom mold flipper is more than a simple transaction; it’s a collaborative journey with a specialized supplier. Success hinges on clear communication, detailed specifications, and selecting a partner with proven expertise in delivering tailored solutions that precisely meet your operational and safety requirements.
The procurement process for a custom mold flipper requires a detailed needs assessment, thorough vendor vetting focusing on engineering capabilities and relevant experience, collaborative design iteration, transparent quotation with all cost components clearly defined, and robust agreements for factory acceptance testing (FAT), site acceptance testing (SAT), installation, training, and after-sales support.
Navigating Custom Mold Flipper Procurement: A Strategic Blueprint
Successfully acquiring a custom mold flipper involves a structured approach, ensuring that the final product aligns perfectly with your company’s unique requirements. This strategic blueprint guides you from initial concept to operational integration.
Phase 1: Comprehensive Needs Assessment & Detailed Specification
This foundational stage is critical. Before approaching any vendors, a thorough internal review is necessary.
- Involve Key Stakeholders: Engage personnel from operations, engineering, maintenance, and safety departments. Their diverse perspectives will ensure all requirements are captured.
- Define Operational Parameters:
- Mold Characteristics: Document the full range of mold weights, dimensions (L x W x H), and any unique features (e.g., protrusions, delicate components, center of gravity variations).
- Process Flow: Map out how the mold flipper will integrate into the existing production line. Consider loading/unloading methods (crane, forklift, AGV), cycle time targets, and frequency of use.
- Space Constraints: Measure the available footprint and height for the equipment.
- Specify Safety & Regulatory Requirements: Identify all applicable local, national, and international safety standards (e.g., OSHA, CE marking, ISO standards). Consider specific industry regulations (e.g., automotive, medical).
- Outline Control & Automation Needs: Determine the desired level of automation, data logging requirements, and integration with existing factory control systems (MES/SCADA).
- Develop a User Requirement Specification (URS) Document: This formal document will consolidate all needs and serve as the basis for vendor proposals.
Phase 2: Vendor Research, Qualification & Shortlisting
Finding the right partner is paramount.
- Identify Potential Suppliers: Look for companies specializing in custom material handling equipment or specifically mold flippers. Industry referrals, trade shows, and online research are good starting points. The provided text mentions key players like GAMMA Technologies, Cavaform Inc., DME Company, and Husky Injection Molding Systems as dominant in the broader mold-related market; similar diligence is needed for flipper specialists.
- Evaluate Vendor Capabilities:
- Technical Expertise: Assess their engineering team’s experience with custom designs.
- Manufacturing Facilities: Are they equipped to build and test the specified equipment?
- Track Record: Request case studies, testimonials, and references from companies with similar applications.
- Quality Certifications: ISO 9001 or other relevant certifications indicate a commitment to quality management.
- Initial Screening & RFI (Request for Information): Send an RFI to gather preliminary information about potential vendors’ capabilities and interest.
Phase 3: RFP Issuance & Proposal Evaluation
Once a shortlist of qualified vendors is established:
- Issue a Detailed RFP (Request for Proposal): Include the URS, desired timelines, and evaluation criteria.
- Technical Evaluation: Scrutinize the proposed design, component selection, and adherence to specifications. Does the solution genuinely meet the custom needs?
- Commercial Evaluation: Compare pricing, payment terms, warranties, and included services (installation, training, support). Beware of bids that are significantly lower, as they might compromise on quality or features.
- Vendor Presentations & Clarifications: Allow vendors to present their proposals and address any questions. This is also an opportunity to gauge their understanding of your project.
Evaluation Criterion | Vendor A Score (1-5) | Vendor B Score (1-5) | Vendor C Score (1-5) | Weight (%) | Weighted Score (A) |
---|---|---|---|---|---|
Technical Solution Alignment | 4 | 5 | 3 | 30 | 1.2 |
Customization Experience | 3 | 5 | 4 | 25 | 0.75 |
Price & Commercial Terms | 5 | 3 | 4 | 20 | 1.0 |
After-Sales Support & Wty | 4 | 4 | 3 | 15 | 0.6 |
Lead Time & Delivery | 4 | 3 | 5 | 10 | 0.4 |
Total Weighted Score | 3.95 |
(Note: Complete the table for Vendor B & C to make a full comparison)
Phase 4: Design Collaboration, Review & Finalization
This is an iterative phase where your team works closely with the selected vendor.
- Kick-off Meeting: Establish project timelines, communication protocols, and key contacts.
- Detailed Design Review (DDR): Scrutinize engineering drawings, 3D models, and component lists. Ensure all URS points are addressed. This may involve several iterations.
- HAZOP Study (Hazard and Operability Study): For complex or critical applications, conduct a HAZOP to identify and mitigate potential risks.
- Design Freeze & Sign-off: Once all parties are satisfied, formally approve the design.
Phase 5: Manufacturing, Testing & Acceptance
- Manufacturing Oversight: Maintain communication with the vendor, potentially including progress visits for critical milestones.
- Factory Acceptance Test (FAT): Witness the equipment being tested at the vendor’s facility against agreed-upon criteria. Document any deviations and ensure they are rectified before shipment.
- Site Acceptance Test (SAT): After installation at your facility, conduct further tests to ensure the equipment performs as specified in its operational environment.
Phase 6: Installation, Training, & Long-Term Support
- Installation & Commissioning: Ensure this is carried out by qualified technicians, either the vendor’s team or approved contractors.
- Operator & Maintenance Training: Comprehensive training is essential for safe and efficient operation and upkeep.
- Documentation: Receive all manuals, drawings, spare parts lists, and certifications.
- Warranty & Service Level Agreements (SLAs): Understand the warranty coverage and establish SLAs for ongoing maintenance and support if required.
By following this strategic blueprint, companies can navigate the complexities of custom mold flipper procurement, resulting in a solution that delivers optimal performance, safety, and value for years to come.
ROI and Long-Term Benefits of Custom Mold Flipper Investment
Investing in a custom mold flipper often involves a higher upfront cost compared to standard models. However, this initial outlay is strategically justified by a significant return on investment (ROI) and a host of long-term benefits that enhance operational efficiency, safety, and overall competitiveness.
A custom mold flipper, tailored to your specific operational needs, is not an expense but a strategic investment designed to optimize your manufacturing processes. The benefits translate directly into improved productivity, reduced operational costs, and enhanced safety.
The return on investment from a custom mold flipper materializes through several key areas: significantly enhanced operational efficiency by minimizing bottlenecks and reducing cycle times (potentially by up to 30%, as cited in industry analyses); improved product quality due to precise and gentle mold handling, minimizing defects; substantial reductions in labor costs (an average of 20% with automation integration) by reducing manual intervention; decreased maintenance expenses and extended equipment lifespan due to robust design and components suited for specific tasks; and a markedly improved safety record, reducing the risk of costly accidents and associated downtime. These cumulative advantages contribute directly to increased profitability and a stronger market position.
Consider a hypothetical scenario in the automotive components sector: "AutoParts Inc." previously used a standard mold flipper for their diverse range of injection molds. They experienced frequent minor stoppages due to misalignment, slower-than-ideal cycle times for their larger molds, and two near-miss safety incidents related to manual adjustments. After investing in a custom mold flipper with PLC integration, automated clamping, and enhanced safety guarding tailored to their mold fleet and workflow, they reported:
- A 15% reduction in overall mold changeover time, directly impacting OEE.
- A 10% decrease in mold maintenance costs attributed to gentler, more precise handling.
- Elimination of manual handling risks during the flipping process, leading to improved operator morale and safety metrics.
- The ability to seamlessly integrate the flipper’s operational data into their MES, providing better insights for continuous improvement.
The long-term benefits extend beyond direct cost savings. A custom solution allows for:
- Future-Proofing: Designing the flipper with some capacity for future mold designs or increased production volumes can prevent the need for premature replacement.
- Enhanced Process Control: Automation and precise control lead to more consistent and predictable manufacturing outcomes.
- Improved Ergonomics: Custom designs can significantly improve the ergonomics of mold handling, reducing operator fatigue and risk of musculoskeletal injuries.
- Brand Reputation: Demonstrating a commitment to cutting-edge technology and safety can enhance a company’s reputation among clients and employees.
- Sustainability Gains: Optimized cycle times and energy-efficient components (if specified) can contribute to reduced energy consumption, aligning with growing sustainability initiatives. The provided materials highlight that sustainability influences purchasing choices, and energy-efficient technology appeals greatly.
While the initial procurement cost of a custom mold flipper is a factor, a comprehensive ROI analysis that includes savings from increased productivity, reduced downtime, lower labor costs, minimized mold damage, and enhanced safety will invariably demonstrate its superior long-term value proposition for specialized operations.
Conclusion
In the competitive realm of modern manufacturing, the "one-size-fits-all" mentality rarely leads to optimal outcomes, especially when it comes to critical equipment like mold flippers. The importance of customization in mold flipper procurement cannot be overstated. It is a strategic decision that directly impacts operational efficiency, worker safety, mold longevity, and ultimately, the bottom line. By investing the time and resources to specify and procure a mold flipper tailored to unique operational demands, businesses can unlock significant long-term benefits, transforming a necessary piece of equipment into a true competitive advantage and a cornerstone of manufacturing excellence.