Future-Proofing Manufacturing with Innovative Mold Flipper Solutions
In the relentless pursuit of efficiency and safety, modern manufacturing operations are increasingly turning to specialized equipment. Innovative mold flipper solutions are at the forefront, revolutionizing how heavy and cumbersome molds are handled, maintained, and prepared for production, thereby future-proofing facilities against evolving demands and complexities.
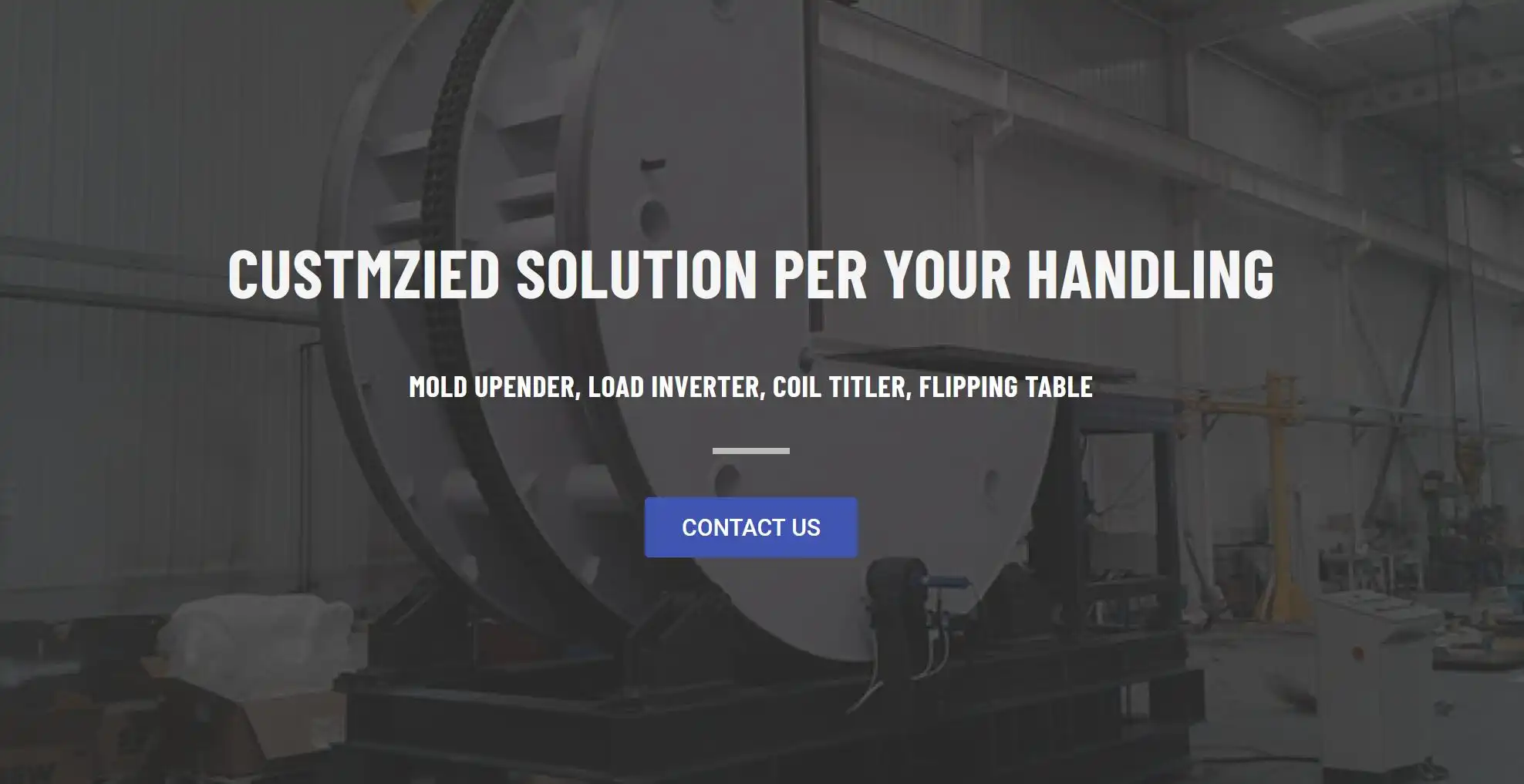
Future-proofing manufacturing with innovative mold flipper solutions involves investing in advanced mold handling technology that enhances safety, boosts operational efficiency, and ensures adaptability to future production needs. These systems, offering precision rotation, customization, and smart features, allow businesses to stay competitive by minimizing downtime, reducing labor costs, and improving overall mold maintenance processes, thus preparing for the evolving landscape of industrial manufacturing and mold flipper technology.
The landscape of manufacturing is in a perpetual state of flux, driven by technological advancements, market demands, and the ever-present need for greater productivity and safety. For industries reliant on medium to large-scale molds—such as automotive, aerospace, and consumer goods—the efficient and safe handling of these critical assets is paramount. Traditional methods often fall short, introducing risks and inefficiencies. This is where innovative mold flipper solutions step in, offering a robust pathway to not just meet current operational requirements, but to strategically future-proof your entire manufacturing ecosystem. By embracing these advanced systems, companies can transform a challenging necessity into a streamlined, value-adding process, paving the way for sustained growth and operational excellence.
Understanding the Core: What are Mold Flippers and Why Do They Matter?
Mold flippers, or mold turners, are specialized industrial machines designed to safely and efficiently rotate heavy molds, typically by 90 degrees. This capability is crucial for mold maintenance, inspection, cleaning, and preparation for die spotting presses, significantly impacting workflow, safety, and the longevity of expensive molding equipment.
Mold flippers are essential handling equipment for medium to large-scale molds, enabling 90-degree rotation for maintenance, repair, and integration with die spotting presses. They matter because they drastically improve safety by eliminating risky manual or crane-based turning, reduce mold damage, and significantly cut down on maintenance time. This directly translates to increased operational uptime, optimized labor utilization, and enhanced overall productivity. Modern mold flippers offer precision control, customizable capacities (from 500kg to over 50 tons), and integration flexibility, making them a cornerstone for efficient and safe mold handling in demanding manufacturing environments. Their adoption is key to streamlining operations and protecting valuable tooling assets, ultimately contributing to a more competitive and resilient manufacturing process.

Deeper Dive into Mold Flipper Mechanics and Benefits
The fundamental purpose of a mold flipper is to reorient a mold, typically from a horizontal to a vertical position, or vice-versa, to allow access to different faces for work. This seemingly simple task is fraught with challenges when dealing with molds that can weigh several tons. Traditional methods involving cranes, chains, and manual effort are not only time-consuming but also carry significant safety risks for personnel and the potential for damage to the mold itself – a costly asset.
Mechanics of Operation:
Most mold flippers utilize a robust structural frame, a tilting platform or arms, and a powerful drive system (hydraulic or electromechanical). The mold is securely placed or clamped onto the flipper’s platform. The drive system then smoothly and controllably rotates the platform to the desired angle, typically 90 degrees. Advanced systems offer variable speed control, soft start/stop, and precise positioning. Some designs incorporate features like movable support tables or integrated conveyor systems for easier loading and unloading.
The 90-degree Mold Rotation System, as highlighted, is specifically designed for seamless integration with vertical die spotting press units. This synergy is critical. Die spotting ensures the perfect alignment and contact between mold halves, a process that requires molds to be in a vertical orientation. A mold flipper automates the transition to this orientation, eliminating bottlenecks and potential misalignments that could occur with manual methods.
Key Benefits Quantified:
Feature | Traditional Method Drawback | Mold Flipper Advantage | Potential Impact (Data from provided material) |
---|---|---|---|
Safety | High risk of crush injuries, drops, strain | Controlled, stable rotation, safety interlocks | Reduce workplace incidents by up to 85% |
Mold Protection | Risk of dents, scratches, misalignment from impacts | Gentle, even handling, secure clamping | Decrease equipment damage by up to 60% |
Efficiency | Time-consuming, labor-intensive setup & execution | Rapid, automated or semi-automated rotation | Up to 45% increase in operational efficiency |
Labor Utilization | Requires multiple operators, specialized riggers | Often operable by a single trained individual | Labor cost reduction of 35-55% |
Accessibility for Maint. | Limited access, awkward working positions | Full access to mold faces in stable orientation | Improved quality and speed of maintenance |
Integration | Manual transfer to other equipment | Seamless integration with die spotting presses, CMMs etc. | Streamlined workflow, reduced handling time |
Space Optimization | Larger clear area needed for crane maneuvers | Compact footprint, defined operational envelope | Better floor space utilization |
Consider the financial implications. A damaged multi-ton mold can cost tens, if not hundreds, of thousands of dollars to repair or replace, not to mention the production downtime. The provided material indicates that initial investments in mold flipper systems range from $30,000 to $150,000, with customization adding 15-25%. While a significant outlay, the ROI is compelling when factoring in a 35-55% reduction in labor costs, 20-30% maintenance savings, and a 40-60% increase in production efficiency over an equipment lifespan of 10-15 years. This moves the mold flipper from a mere piece of equipment to a strategic investment in operational resilience and profitability. The ability to handle loads up to 20 tons (and even 50 tons as per customization notes) caters to a vast range of industrial applications, making this technology versatile and widely applicable.
The Innovation Leap: Advanced Features in Modern Mold Flippers
Modern mold flippers are no longer just about basic tilting. They represent a significant leap in engineering, incorporating advanced control systems, enhanced safety features, and intelligent capabilities. These innovations are transforming mold handling from a rudimentary task into a precise, efficient, and data-driven operation.
The innovation in mold flippers lies in precision rotation control, advanced multi-zone safety systems, customizable handling capacities (up to 50 tons), smart monitoring, and seamless integration flexibility. These features can boost operational efficiency by up to 45% compared to standard solutions, offering features like variable speed control, position memory, automated sequencing, and remote operation for optimized performance and reduced manual intervention.
Exploring Cutting-Edge Technologies and Customization
The evolution of mold flippers mirrors the broader trends in industrial automation and smart manufacturing. Manufacturers are demanding more than just brute strength; they need intelligence, precision, and adaptability.
1. Precision Control Systems:
The heart of modern mold flipper innovation lies in its control system. Gone are the days of simple on/off switches. Today’s systems offer:
- Variable Speed Control: Allows for gentle starts and stops, crucial for handling delicate or complex molds, and enables faster rotation for robust molds when appropriate.
- Position Memory Settings: Operators can pre-program and recall specific rotation angles or sequences, ensuring repeatability and reducing setup time for recurring tasks.
- Automated Sequence Programming: Complex handling routines involving multiple stops or orientations can be automated, minimizing operator error and fatigue.
- Remote Operation Capabilities: Pendants or even wireless controls allow operators to manage the flipper from a safe distance, offering better visibility of the operation.
- Real-time Monitoring Systems: Sensors provide feedback on load status, rotation angle, and system diagnostics, often displayed on an HMI.
These features don’t just add convenience; they deliver tangible benefits: a reported 30% reduction in handling time, a 50% improvement in positioning accuracy, and a 40% decrease in operator fatigue.
2. Smart Safety Integration:
Safety is paramount when dealing with heavy loads. Innovative mold flippers go beyond basic mechanical safeguards:
- Multi-zone Safety Barriers: Light curtains, laser scanners, or pressure-sensitive mats create safety zones that can halt operation if an unauthorized entry occurs.
- Advanced Sensor Systems: Load sensors prevent overloading, while proximity sensors can detect obstacles or ensure correct mold placement before operation.
- Emergency Stop Redundancy: Multiple, easily accessible E-stops and fail-safe control logic are standard.
- Operator Protection Features: Physical guards, interlocked access doors, and controlled access protocols protect operators.
- Load Monitoring Capabilities: Continuous monitoring of the load’s stability and distribution during rotation can prevent accidents.
This comprehensive approach is shown to reduce workplace incidents by an astounding 85% and decrease equipment damage by 60%.
3. Customizable Interface Options:
The Human-Machine Interface (HMI) has become a critical component for ease of use and efficiency:
- Touchscreen HMI Interfaces: Intuitive graphical displays simplify operation, provide diagnostic information, and allow for easy parameter adjustments.
- Mobile Device Integration: Some advanced systems may offer monitoring or even limited control via tablets or industrial smartphones.
- Custom Program Storage: Allows for saving specific mold handling recipes, reducing setup time for different molds.
- Multi-language Support: Essential for global operations.
- User-specific Settings: Different access levels and customized interfaces for operators, maintenance personnel, and supervisors.
These interface improvements can lead to 25% faster operator training and a 35% reduction in operational errors.
4. Design Innovation and Advanced Material Handling:
Beyond controls, physical design innovations include:
- AI-Powered Load Sensing: More sophisticated systems can adapt rotation profiles based on sensed load characteristics for optimal safety and speed.
- Predictive Maintenance Algorithms: By monitoring operational parameters (e.g., motor current, vibration, cycle times), systems can predict potential failures, allowing for proactive maintenance. This aligns perfectly with future-proofing strategies.
- Modular Design Components: Allow for easier upgrades, repairs, and customization, extending the flipper’s useful life and adapting to changing needs.
- Energy Efficiency Features: Optimized drive systems and power management to reduce operational costs.
The emphasis on customization, with dimensional flexibility from 200mm to 3000mm and load capacities from 500kg to 50 tons, means these innovative solutions can be tailored to nearly any application, truly future-proofing the investment.
Strategic Implementation: Choosing and Integrating Your Mold Flipper Solution
Selecting and integrating a mold flipper is a strategic decision that extends beyond the initial purchase. It requires careful planning, consideration of long-term value, and a focus on seamless integration into existing workflows to maximize ROI and truly future-proof your manufacturing operations.
Choosing the right customized mold flipper involves accurately assessing current and future needs, understanding total ownership costs (including installation and training), evaluating supplier support, and considering long-term scalability and Industry 4.0 compatibility. The goal is an optimal balance of functionality, reliability, cost-effectiveness, safety, and future adaptability for your specific manufacturing environment.
ROI, Maintenance, and Long-Term Value: A Fabricator’s Perspective
For any fabricator or manufacturer, an investment in capital equipment like a mold flipper must be justified by a clear return on investment (ROI) and a solid plan for long-term value. This goes beyond the sticker price to encompass operational savings, enhanced safety, and future adaptability.
1. Cost Analysis and ROI Considerations:
A comprehensive cost analysis is the first step. The provided material offers a useful breakdown:
Cost Component | Typical Range/Percentage | Notes |
---|---|---|
Base System Cost | $30,000 – $150,000 | Varies greatly with capacity, features, and brand. |
Customization Fees | 15-25% of base cost | For specific dimensional requirements, controls, or safety features. |
Installation Charges | 8-12% of total cost | Includes site prep, setup, commissioning. |
Training Programs | 5-7% of system cost | Crucial for safe and efficient operation and maintenance. |
Total Initial Cost | Sum of above | Represents the upfront investment. |
Against this initial investment, weigh the long-term value:
- Labor Cost Reduction (35-55%): Fewer operators needed, reduced time per mold turn.
- Maintenance Savings (20-30%): Reduced mold damage, less wear on cranes/other equipment, streamlined flipper maintenance.
- Production Efficiency Increase (40-60%): Faster mold changeovers, reduced downtime for maintenance.
- Equipment Longevity (10-15 years): A well-maintained flipper is a long-term asset.
- Improved Safety: Reduced incidents (85%) leading to lower insurance premiums, less lost time.
- Reduced Equipment Damage (60%): Protects valuable molds and other machinery.
Example ROI Calculation (Simplified):
Assume a mid-range system cost of $100,000 (including customization, installation, training).
If annual labor savings are $40,000 and maintenance/downtime savings are $20,000, the total annual saving is $60,000.
Simple payback period = $100,000 / $60,000 = approx. 1.67 years.
This rapid payback, coupled with ongoing savings and intangible benefits like improved morale and safety culture, makes a strong case for investment.
2. Installation and Implementation Process:
A smooth installation is key to realizing benefits quickly.
- Site Preparation: Requires foundation specifications (can the floor bear the load?), power supply needs, adequate clearance (height, operational envelope, safety zones), and possibly ventilation.
- Integration Timeline:
- Pre-installation assessment: 1-2 weeks
- Site preparation: 2-3 weeks
- Equipment installation: 3-5 days
- Testing and calibration: 2-3 days
- Operator training: 3-5 days
Thorough planning minimizes disruption. Compatibility with existing equipment (e.g., die spotting presses, overhead cranes for loading/unloading the flipper) and workflow optimization are critical considerations.
3. Maintenance and Upkeep Strategies:
To ensure longevity and reliability, a robust maintenance plan is essential.
- Preventive Maintenance Schedule:
- Daily: Visual inspections, check for leaks, debris.
- Weekly: System checks, safety function tests.
- Monthly: Component assessment (belts, bearings, hydraulics).
- Quarterly: Comprehensive service, lubrication.
- Annual: Certification (if required by local regulations), in-depth inspection.
- Common Maintenance Tasks: Lubrication points, belt tension checks, bearing inspection, safety system testing, software updates (for smart systems).
- Spare Parts: Understand lead times for critical spare parts and consider keeping common wear items in stock.
- Supplier Support: Evaluate the supplier’s service capabilities, technical support, and parts availability. A reliable partner is crucial for long-term value.
By focusing on these strategic elements, manufacturers can ensure their mold flipper solution is not just a purchase, but a cornerstone of a more efficient, safer, and future-proof operation.
Future-Proofing in Action: Real-World Applications and Forward-Thinking
Adopting innovative mold flipper solutions is a direct step towards future-proofing manufacturing. It’s about preparing for tomorrow’s demands today by investing in adaptable, efficient, and intelligent technology that can evolve with your business and the broader industry shifts.
Future-proofing with mold flippers means selecting systems with scalability (modular design, upgrade paths), technology adaptation (Industry 4.0, IoT integration, data collection), and the flexibility to handle evolving mold designs and production volumes. This proactive approach ensures the equipment remains a valuable asset, contributing to sustained operational excellence, safety, and competitiveness in a rapidly changing manufacturing landscape, ultimately securing a plant’s ability to meet future challenges.
The concept of future-proofing, as Diana Wu David discusses in "Future Proof: Reinventing Work in the Age of Acceleration," isn’t just for careers; it’s vital for industrial capital. While her focus is on individual adaptation, the principles of experimenting, reinventing, collaborating, and focusing are equally applicable to manufacturing investments. A mold flipper, chosen wisely, embodies these principles.
Scalability Features for Evolving Needs:
The manufacturing world is not static. Product lines change, mold sizes evolve, and production volumes fluctuate. A future-proof mold flipper must accommodate this.
- Modular Design Components: As mentioned, this allows for easier upgrades or modifications. Perhaps a larger platform is needed later, or an automated loading/unloading system. Modularity makes this feasible without a complete replacement.
- Upgrade Possibilities: Control systems that can be updated with new software features, or mechanical components designed for future enhancements (e.g., adding more sensors).
- Expansion Capabilities: Some systems might be designed to integrate with additional automation cells or AGVs (Automated Guided Vehicles) as a facility moves towards greater automation.
- Integration Flexibility: Ensuring the flipper can communicate with other machinery and plant-level MES (Manufacturing Execution Systems) or ERP (Enterprise Resource Planning) systems. This is crucial for Industry 4.0 compatibility.
Technology Adaptation – Embracing Industry 4.0:
The "smart factory" is no longer a futuristic concept. Mold flippers are increasingly part of this connected ecosystem.
- Industry 4.0 Compatibility: This means the flipper can exchange data, be remotely monitored, and potentially controlled as part of a larger, integrated manufacturing system.
- IoT Integration Options: Sensors on the flipper collecting data on usage, cycle times, energy consumption, and potential maintenance needs. This data can be fed into cloud-based analytics platforms.
- Data Collection Capabilities: Essential for performance tracking, predictive maintenance, and process optimization. Understanding how often molds are flipped, the time taken, and any operational issues can highlight areas for improvement.
- Remote Monitoring Potential: Allows maintenance teams or even the equipment supplier to diagnose issues remotely, reducing downtime.
- Predictive Maintenance Algorithms: As seen in the "Plastic lid mold" material discussing ‘smart molds,’ the same principle applies. Sensors can provide real-time data, enabling quicker fault detection and reducing waste, thus improving overall efficiency and sustainability.
Real-World Example – Drawing Parallels:
Consider the UC San Diego development of algae-based flip-flops. Their innovation wasn’t just the material, but the process and the forward-thinking approach to sustainability and scalability. They started with a surfboard, then looked at a higher-volume product (flip-flops), demonstrating a pathway to broader impact. Similarly, a company might initially invest in a mold flipper for a specific, critical mold maintenance task. But a future-proof design allows that same flipper to be adapted for new mold types, integrated into new production lines, or enhanced with smart features as the company’s needs and technological capabilities grow.
Choosing a mold flipper isn’t just about solving today’s handling problem. It’s about selecting a partner and a technology platform that will support your manufacturing operations for the next decade or more, adapting to new challenges and opportunities. This aligns with the "Revolutionary Startups" article’s point on "Timing Is Everything"—investing in such technology now positions a manufacturer to capitalize on shifts towards more automated, data-driven, and safer operations.
Conclusion
Future-proofing manufacturing isn’t a single action but a continuous strategy. Innovative mold flipper solutions are a critical component of this strategy, addressing immediate needs for safety and efficiency while providing a platform for future growth and adaptation. By carefully considering design specifications, customization options, integration capabilities, and long-term value, manufacturers can select a mold flipper that transcends its basic function. It becomes a catalyst for operational excellence, reducing costs, enhancing worker safety, and ensuring the agility needed to thrive in the evolving industrial landscape. The right mold flipper is an investment in resilience, productivity, and a smarter manufacturing future.