The Importance of Coil Protection in High-Temperature Environments
Coils of steel, aluminum, and other vital metals form the backbone of countless industries. But expose them to scorching heat, and you face a brutal reality: rapid degradation, compromised integrity, and catastrophic failure. Ignoring this risk invites massive losses and jeopardizes entire production chains. Effective coil protection is not just a luxury; it’s a non-negotiable shield against the destructive forces of high-temperature environments.
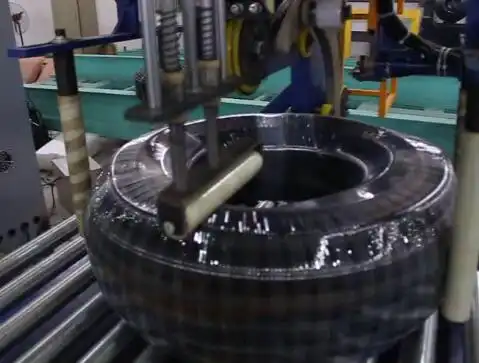
Protecting metal coils in high-temperature environments is crucial because extreme heat accelerates oxidation, reduces material strength, degrades standard protective coatings, and can lead to irreversible deformation. This necessitates specialized coatings and packaging solutions designed to withstand elevated temperatures, preventing corrosion, maintaining structural integrity, and ensuring the longevity and reliability of the coils for downstream manufacturing processes in demanding applications like automotive exhaust systems, industrial furnaces, and power generation.
Metal coils are fundamental components across construction, automotive, manufacturing, and beyond. Their journey from mill to final product often involves exposure to challenging conditions, none more destructive than high temperatures. This article delves into why safeguarding these valuable materials in heat-intensive settings is paramount, exploring the unique challenges and the advanced solutions available to ensure their performance and durability.
The Destructive Power of Heat on Metal Coils
Imagine metal glowing red-hot – that’s an extreme, but even moderately elevated temperatures can have profound negative effects on coil integrity. Understanding these mechanisms is the first step towards effective protection.
High temperatures severely impact metal coils by increasing chemical reactivity, leading to accelerated oxidation and scale formation which depletes material thickness and compromises surface finish. Elevated heat also reduces the metal’s yield strength and tensile strength, making coils more susceptible to deformation and damage under load during handling or storage. Furthermore, standard organic coil coatings are often not formulated to withstand prolonged high-temperature exposure, potentially blistering, cracking, or completely failing, leaving the underlying metal vulnerable to environmental attack. This combined assault from thermal and chemical degradation necessitates specialized protection strategies tailored for heat resistance to preserve the coils’ quality and usability.

Material Degradation Under Thermal Stress
Metals, while robust at ambient temperatures, exhibit altered properties when subjected to heat. High temperatures accelerate chemical reactions, most notably oxidation. Steel, for instance, rapidly forms scale at elevated temperatures, a brittle layer that not only reduces the usable metal thickness but also impairs surface quality, making it unsuitable for precision applications. This accelerated corrosion is a primary concern. Beyond surface effects, heat impacts the bulk material. The yield strength and tensile strength of metals decrease with increasing temperature. This means coils stored or transported in hot conditions become more susceptible to deformation, dents, and kinks under their own weight or external pressures. Stacking heavy coils in a hot warehouse without adequate support or protection can lead to irreversible damage.
Standard protective measures, such as conventional organic coil coatings, which perform excellently at room temperature, often fail spectacularly under heat. These coatings can soften, blister, peel, or even combust, losing their protective barrier function and leaving the metal exposed. Even seemingly innocuous factors like prolonged exposure to direct sunlight on stored coils in a hot climate can raise surface temperatures enough to compromise less robust coatings.
Consider the specific challenges faced by different metal types:
Metal Type | High-Temperature Challenges | Consequences for Coils |
---|---|---|
Carbon Steel | Rapid oxidation, scale formation, decreased strength. | Reduced usable material, poor surface finish, deformation. |
Stainless Steel | Carbide precipitation (sensitization) at certain temperatures, reduced strength at very high temps. | Reduced corrosion resistance in localized areas, deformation. |
Aluminum | Low melting point, rapid oxidation (though self-limiting), reduced strength. | Significant deformation, potential melting in extreme cases. |
Copper | Oxidation (forms black/red oxides), annealing (softening). | Poor surface conductivity, reduced structural integrity. |
Effective coil protection in high-temperature environments must therefore address both the chemical acceleration (oxidation) and the physical changes (reduced strength, coating failure) caused by heat. It requires solutions that maintain their integrity and protective properties even when the mercury rises.
Specialized Protection Solutions for Elevated Temperatures
Standard coil protection, while effective for basic environmental factors, is simply inadequate when heat becomes a significant variable. High-temperature environments demand specialized materials and application techniques to ensure coils remain pristine and functional.
Effective coil protection in high-temperature environments requires the use of specialized coatings, wraps, and handling methods designed to withstand extreme thermal conditions. Unlike standard solutions, these employ heat-resistant materials such as silicone or ceramic-based coatings, fire-retardant or insulating wraps, and strategically designed packaging that prevents direct contact and allows for thermal expansion without inducing stress or deformation on the valuable metal coils during storage and transport.
Coatings Engineered for Heat Resistance
The primary line of defense against heat damage on coils often lies in specialized coatings. These are distinct from conventional coil coatings primarily designed for aesthetics and standard corrosion/UV resistance. High-temperature coatings utilize binder systems and pigments capable of withstanding significant thermal stress without degrading.
- Silicone-Based Coatings: Silicones offer excellent thermal stability and can withstand temperatures up to several hundred degrees Celsius. They provide a flexible, durable barrier that resists cracking and peeling under thermal cycling. Often used for applications like exhaust systems or industrial ovens.
- Ceramic Coatings: These coatings, containing ceramic components, can tolerate extremely high temperatures, often exceeding 1000°C. They provide exceptional hardness, abrasion resistance, and chemical inertness even in harsh, hot environments. Ideal for applications like furnace components or aerospace parts.
- Inorganic Zinc Silicate Coatings: While primarily known for corrosion resistance, some formulations offer decent thermal stability, acting as a primer layer for high-temperature topcoats.
Applying these specialized coatings often requires precise processes. The coil coating line must be adapted to handle the specific curing requirements and film thicknesses of these advanced materials. Quality control focuses on ensuring uniform application and, crucially, verifying the coating’s adhesion and performance after exposure to test temperatures that simulate the target environment.
Beyond coatings, protective packaging plays a supporting role, especially during transport and temporary storage in hot climates. While packaging materials themselves won’t prevent oxidation in a furnace, they can:
- Provide Insulation: Materials like specialized paper or films can offer minor thermal buffering against ambient heat fluctuations.
- Prevent Contact: Separator sheets or protective wraps prevent coils from sticking together if coatings soften or from damaging each other if expansion/contraction occurs.
- Allow Ventilation: Designing packaging that allows some airflow can prevent heat buildup within the coil stack.
- Utilize Heat-Resistant Wraps: Fire-retardant or heat-stabilized films and fabrics can protect against external heat sources or sparks in certain industrial settings.
Combining the right heat-resistant coating with appropriate handling and temporary packaging is key to comprehensive protection in high-temperature scenarios.
Implementing Effective High-Temperature Coil Protection
Implementing effective coil protection in high-temperature environments is not just about selecting the right material; it involves optimizing the entire handling and storage process, leveraging technology, and adhering to rigorous quality standards to ensure sustained performance under thermal stress.
Successfully implementing coil protection in high-temperature environments requires a multi-faceted approach, including selecting heat-resistant coatings and packaging materials, optimizing storage conditions to mitigate heat exposure, utilizing automated handling systems that minimize physical stress on potentially weakened materials, and implementing robust quality control measures, including thermal testing, to verify the protective system’s integrity under expected operational or environmental temperatures. This integrated strategy ensures coils maintain their quality and structural integrity throughout the supply chain.
Process Considerations for Heat-Sensitive Coils
Protecting coils destined for or passing through high-temperature environments requires attention at multiple stages, from initial processing to final use.
- Coating Application: As mentioned, applying high-temperature coatings may require specialized coil coating lines or slower line speeds to ensure proper drying and curing. Adhesion to the substrate is critical, as thermal cycling can cause differential expansion between the metal and the coating, leading to delamination if bonding is insufficient. Surface preparation (cleaning, pre-treatment) is even more critical for high-temp applications to ensure optimal adhesion.
- Handling: Coils that have been exposed to high temperatures, even temporarily, may have reduced structural integrity. Automated handling systems, such as specialized coil cars, overhead cranes with wide slings, or robotic manipulators, are crucial to minimize localized stress points that could cause deformation in heat-weakened material. Avoiding dropping or impacts is paramount.
- Storage: While coils might not be stored at their peak operational temperature, ambient storage temperatures in hot climates or near heat-generating processes can still be problematic. Ventilated storage areas, minimizing direct sunlight exposure, and avoiding stacking excessively high piles can help. Using sturdy, heat-resistant dunnage and blocking prevents crushing and ensures stability.
- Transportation: Transporting coils in hot weather requires consideration. Enclosed, insulated trailers or even climate-controlled transport might be necessary for high-value or particularly heat-sensitive coils. Securing the load properly is vital to prevent shifting and impact damage, which, as noted, is exacerbated by heat-induced material softening.
Rigorous quality control is non-negotiable. Testing must go beyond standard adhesion or corrosion tests. It should include thermal cycling tests that subject samples to repeated heating and cooling cycles to simulate real-world temperature fluctuations. Accelerated aging tests at elevated constant temperatures can help predict long-term performance.
Consider the comparison of standard vs. high-temperature protection strategies:
Factor | Standard Coil Protection | High-Temperature Coil Protection |
---|---|---|
Primary Threat | Corrosion, UV, physical damage (ambient) | Heat-accelerated oxidation, reduced strength, coating failure, physical damage (elevated temps) |
Coating Type | Organic (polyester, epoxy, PVDF) | Inorganic (ceramic, silicone, inorganic zinc) |
Packaging Material | Paper, standard plastic film, wood | Heat-resistant film/fabric, engineered dunnage, potential insulation |
Handling Focus | Preventing dents/scratches | Preventing deformation under load, minimizing impact on weakened material |
Storage Needs | Moisture control, physical security | Temperature mitigation, ventilation, reinforced stacking |
Key Quality Test | Salt spray, UV resistance, adhesion | Thermal cycling, accelerated heat aging, high-temp adhesion |
Implementing these strategies ensures that coils maintain their specified properties and dimensions, arriving at the manufacturing facility or job site in optimal condition, ready for their intended high-temperature application.
Industries Where High-Temperature Coil Protection is Critical
While general coil protection is important across the board, certain industries operate in environments or produce products that inherently involve high temperatures, making specialized heat-resistant protection essential for reliability and safety.
Several key industries critically depend on effective coil protection in high-temperature environments. These include the automotive sector for components like exhaust systems and engine parts, aerospace for crucial structural elements and engine components, power generation for boiler tubes and heat exchangers, and manufacturing of industrial equipment such as furnaces and ovens. In these applications, materials must withstand operational temperatures that would cause standard unprotected or conventionally protected coils to degrade rapidly, leading to premature failure, safety hazards, and significant operational downtime and costs.
The demands of these sectors highlight why investing in advanced, heat-tolerant coil protection is not merely a best practice but a necessity. Without it, components made from these coils would quickly succumb to oxidation, thermal fatigue, and loss of mechanical strength.
- Automotive: Components like exhaust pipes, catalytic converter housings, and certain engine heat shields operate at high temperatures. Coils used to manufacture these parts need protection during transit and storage, but the finished parts themselves require coatings (often applied post-forming, but sometimes starting with pre-coated coil) that can withstand sustained heat and thermal cycling without corroding or failing.
- Aerospace: Aircraft engines, exhaust systems, and certain airframe components experience significant temperature variations. Materials must maintain structural integrity and corrosion resistance under these conditions. Processed steel and superalloy coils for aerospace applications demand protection throughout the supply chain to ensure the raw material quality meets stringent requirements before fabrication.
- Power Generation: Boilers, turbines, heat exchangers, and piping in power plants (especially fossil fuel and nuclear) operate at extremely high temperatures and pressures. Coils and tubes used in these systems must be free from surface defects and maintain precise tolerances. Protection during manufacturing, storage, and assembly is critical to prevent degradation before service.
- Industrial Ovens and Furnaces: Components within industrial heat-treating furnaces, kilns, and ovens operate in severe thermal environments. Coils used for structural elements, liners, or heating elements (in some cases) require specialized protection or inherent high-temperature resistance, necessitating careful handling and storage beforehand.
- Chemical Processing: Reactors, heat exchangers, and piping in chemical plants, particularly those dealing with high-temperature reactions or fluids, utilize alloys processed from coils. These materials need to withstand both high temperatures and often corrosive chemicals, making pristine raw material quality, preserved by effective protection, essential.
In all these industries, the failure of a component due to material degradation caused by heat can have catastrophic consequences, ranging from equipment failure and production stops to safety hazards and environmental damage. Therefore, ensuring that the metal coils used as feedstock are adequately protected from thermal damage throughout their lifecycle before they are even fabricated is paramount. This highlights the far-reaching impact of proper high-temperature coil protection.
Conclusion
The journey of a metal coil from the mill to a finished high-temperature application is fraught with potential hazards, none more insidious than the impact of heat. Effective coil protection in high-temperature environments is indispensable for preventing accelerated degradation, maintaining structural integrity, and ensuring the longevity of vital components across demanding industries like automotive, aerospace, and power generation. By employing specialized heat-resistant coatings, optimizing handling and storage processes, and utilizing technologies like automated systems and rigorous thermal testing, manufacturers can safeguard their valuable materials. This investment in high-quality steel coils protection ultimately translates into reduced waste, enhanced safety, improved product reliability, and significant cost savings throughout the supply chain. Implementing robust strategies for high-temperature coil protection is not just a measure against environmental factors; it is a fundamental requirement for performance and durability in the modern industrial landscape, supported by advanced solutions such as those offered for the coil packing line.