The Benefits of Using Polyethylene Film for Coil Wrapping
Are you losing valuable metal to costly rust and corrosion? The battle against deterioration during storage and transit can feel endless, impacting both product quality and your bottom line. Imagine a simple, effective barrier that keeps your coils pristine from your facility to your customer’s door.

Polyethylene film, particularly when infused with Vapor Corrosion Inhibitors (VCI), offers robust protection for metal coils. It creates a physical barrier against moisture, dust, and dirt while releasing VCI molecules that prevent rust formation on the metal surface. This dual-action approach preserves coil integrity during storage and transit, significantly reducing damage and losses.
Choosing the right protection for your valuable metal coils is critical. Beyond simple containment, the material you choose can dramatically influence the condition of your product upon arrival and the efficiency of your operations. Let’s delve deeper into why polyethylene film, especially advanced VCI options, is the superior choice for safeguarding your investment.
Maximizing Protection Against Corrosion and Physical Damage
Facing relentless rust issues on your metal coils is a significant challenge, leading to damaged goods and financial strain. Effective corrosion control is paramount to ensuring your coils maintain their value and meet customer expectations upon delivery.
Polyethylene film provides essential protection by acting as a strong physical barrier against environmental threats like moisture, dirt, and handling damage. VCI-treated polyethylene film goes further, releasing specialized molecules that actively prevent rust formation on metal surfaces within the packaging. This multi-layer defense ensures coils remain in excellent condition through storage and transit, preserving their quality.

Technical Superiority: Why Advanced Polyethylene Film Outperforms Standard Options
The real power of modern polyethylene film for coil wrapping lies in its engineered features that surpass basic packaging materials. Understanding these technical advantages reveals why investing in specialized films provides a far more reliable and long-lasting solution.
Polyethylene film can be formulated in various densities and thicknesses, with added features like UV resistance or woven reinforcement for heavy-duty applications. Standard stretch films, typically made from Linear Low-Density Polyethylene (LLDPE), offer basic load containment and limited environmental protection. However, for corrosion-prone materials like steel coils, this is often insufficient. Heavy-duty polyethylene films, particularly those incorporating VCI technology, are specifically designed to address the rigorous demands of industrial environments and long-term storage or transit.
Advanced polyethylene films, such as VCI films, create a micro-environment within the wrap. The VCI molecules released from the film sublimate (turn into vapor) and deposit onto all exposed metal surfaces, even in hard-to-reach areas. This molecular layer disrupts the electrochemical process required for rust to form. This is a fundamentally different approach than barrier-only films, which only protect as long as the barrier remains absolutely intact – a difficult feat during handling and transit.
Consider the comparison between a standard stretch film and a heavy-duty VCI polyethylene film designed for metal protection:
Feature | Heavy-Duty VCI Polyethylene Film | Standard Stretch Film | Benefit for Metal Coils |
---|---|---|---|
Material Composition | Polyethylene Weave with VCI | Linear Low-Density Polyethylene | Enhanced strength, puncture resistance, and active corrosion prevention. |
Thickness | Can be customized (e.g., 0.75 Mil Double Layer or more) | Typically 0.6 – 1 Mil | Provides robust physical protection against abrasion and impacts. |
Tensile Strength | High (e.g., 13 LBS MD / 13 LBS CD) | Variable | Withstands stresses during wrapping, stacking, and transportation without breaking. |
Tear Strength | High (e.g., 13 LBS MD / 13 LBS CD) | Variable | Resists tearing if snagged, maintaining wrap integrity and protective barrier. |
UV Resistance | Available (e.g., 80% Retained @ 2000 HRS) | Limited | Protects film integrity during outdoor storage, preventing premature breakdown. |
Corrosion Protection | VCI Technology (up to 36 months) | None | Actively prevents rust formation, crucial for maintaining metal surface quality. |
Metal Compatibility | Ferrous and Non-Ferrous Metals | Generally compatible with surfaces | Specifically formulated to protect various metal alloys commonly used in coils. |
Application | Long-term storage, Transit | Basic load containment, Short-term | Ideal for complex supply chains and extended storage periods where corrosion is a risk. |
This table highlights the significant performance gap. While standard film offers basic physical containment, advanced polyethylene films, especially those with VCI, provide engineered protection tailored to the specific challenges of metal coil preservation. The woven structure and higher gauge offer superior physical resilience, while the integrated VCI chemistry delivers proactive corrosion defense. This technical leap translates directly into reduced product loss, fewer customer complaints, and greater peace of mind. Choosing the right polyethylene film is a strategic decision that safeguards both your product quality and your reputation.
Reducing Costs Associated with Rust Damage
Rust isn’t just an eyesore; it’s a direct hit to your profitability. Damaged metal coils require costly reprocessing, lead to scrapped material, and can result in dissatisfied customers and chargebacks. Mitigating corrosion before it starts is one of the most effective ways to protect your bottom line.
Utilizing polyethylene film for coil wrapping, particularly VCI-infused types, is a cost-effective strategy to combat rust-related losses. By preventing corrosion, it reduces material waste from unsaleable coils and eliminates expensive rust removal and reprocessing steps. This proactive approach preserves product value, minimizes labor costs, and enhances customer satisfaction, leading to significant overall savings.
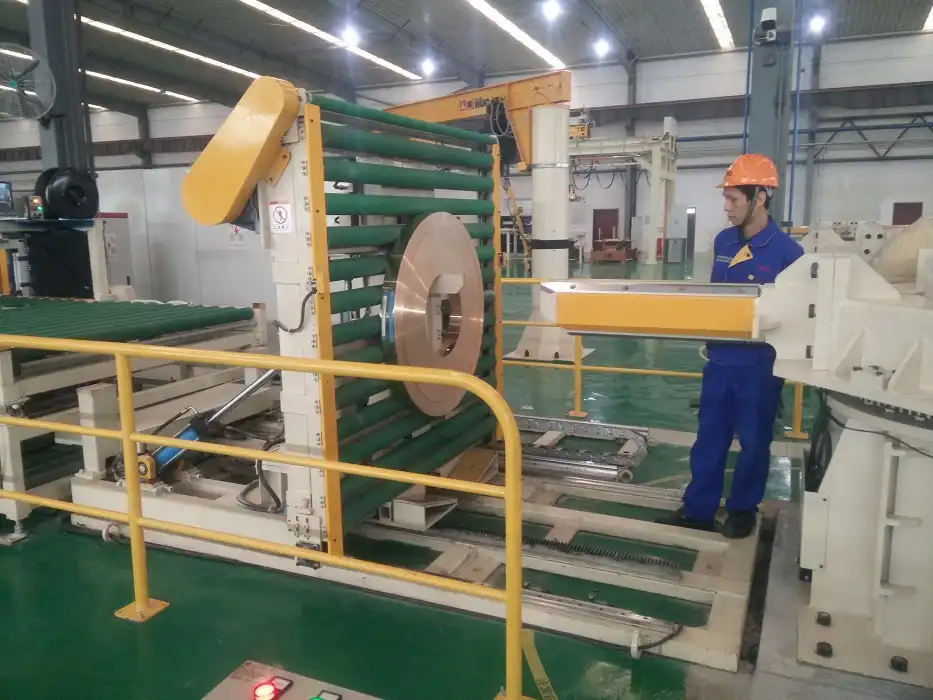
Implementing advanced polyethylene wrapping film presents a clear economic advantage compared to traditional methods like applying rust-preventative oils or relying solely on physical barriers. The initial cost of VCI film may be slightly higher than standard film, but the long-term savings generated through reduced waste, lower labor requirements, and improved product quality offer a compelling return on investment. Consider the hidden costs associated with corrosion: the labor needed to apply and remove messy oils, the environmental impact and disposal costs of oil-soaked materials, the energy and chemicals required for rust removal processes, and the potential loss of future business due to delivering damaged goods. VCI film significantly reduces or eliminates many of these expenses. It’s a clean, dry, and efficient solution that simplifies the entire packaging and processing chain. The transparency often available with polyethylene films also allows for quick visual inspection of the coil condition without unwrapping, further saving time and labor that would otherwise be spent removing and potentially re-applying protection. By minimizing rejections and ensuring products arrive in factory-fresh condition, polyethylene film wrapping directly contributes to increased revenue and reduced operational expenditure, making it a sound financial choice for any business handling metal coils.
Enhancing Efficiency and Ease of Use
Are you tired of wrestling with messy, time-consuming packaging methods that slow down your operation? Streamlining your coil protection process is key to boosting productivity and creating a safer, more efficient workplace.
Polyethylene film, especially VCI-treated options, offers a significantly more efficient and user-friendly method for coil wrapping than traditional alternatives like rust preventative oils. It’s clean, easy to apply manually or with machines, and requires no messy cleanup or degreasing before the coil can be processed further. This simplicity saves labor and time.
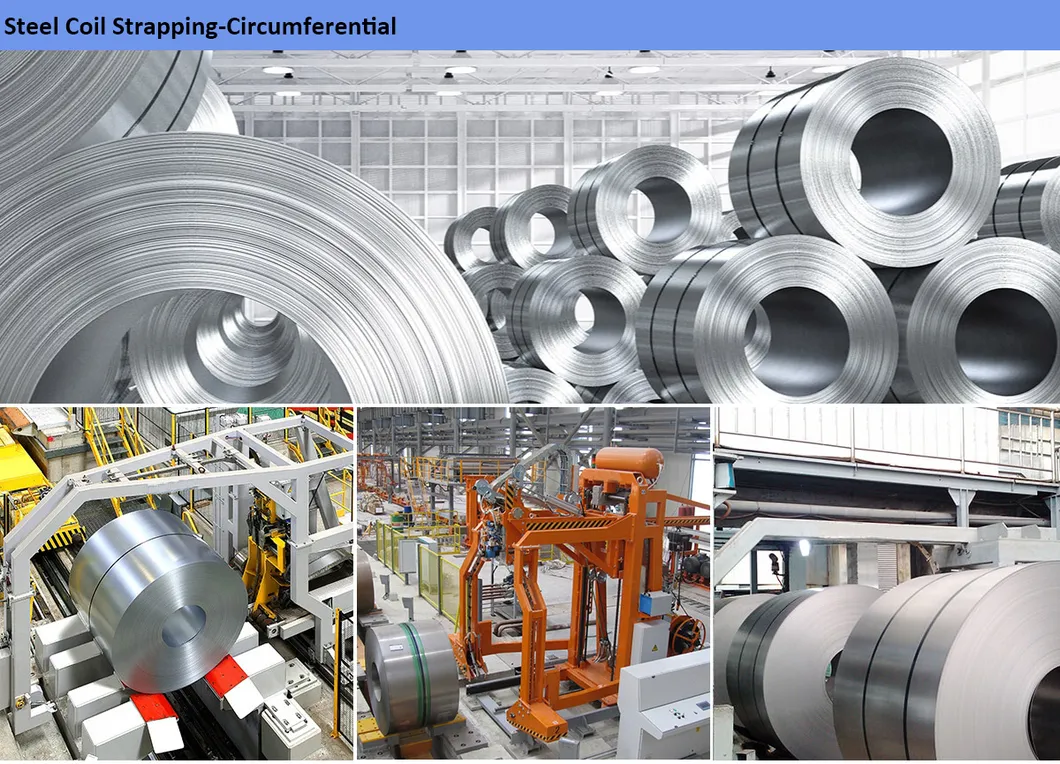
The operational benefits of switching to polyethylene film for coil wrapping extend well beyond just product protection. The inherent properties and application methods of film contribute significantly to improved workflow efficiency and reduced labor costs. Unlike viscous oils that require spraying, dipping, or brushing, often leading to drips and spills, polyethylene film is a dry medium. This eliminates the need for extensive cleanup during the packaging process and, crucially, removes the requirement for degreasing the coil before it can undergo subsequent manufacturing steps like welding, painting, or finishing. This streamlined process saves considerable time, labor, and the cost of cleaning agents and disposal.
Polyethylene film is available in various forms, including hand rolls, machine rolls, and pre-formed bags or covers, offering flexibility to suit different coil sizes, shapes, and production volumes. Hand wrapping is simple and requires minimal training, while larger operations can seamlessly integrate film wrapping into automated packaging lines. This compatibility with automation is a major advantage, allowing for faster throughput and consistent application quality. Furthermore, the lightweight nature of film rolls makes them easier to handle and store compared to drums or tanks of oil. The ability to visually inspect coils through transparent film options without disturbing the protective layer also saves time during inventory checks and quality control. This non-destructive inspection method ensures the VCI protection remains sealed around the coil. The overall impact of adopting polyethylene film is a cleaner, faster, and more efficient packaging process that reduces bottlenecks and improves overall operational flow from production to shipment.
Feature | Heavy-Duty VCI Polyethylene Film | Traditional Rust Preventative Oils | Operational Efficiency Impact |
---|---|---|---|
Application Method | Manual or machine wrapping | Spray, dip, brush | Faster and simpler application, easily integrated into automated systems. |
Cleanliness | Clean, dry application, no residue | Messy application, oily residue requires cleaning | Significantly cleaner working environment, no need for pre-processing degreasing. |
Handling & Storage | Lightweight rolls, easy to handle and store | Heavy drums/tanks, potential for spills | Easier logistics, safer handling, reduced risk of contamination. |
Automation | Compatible with automated wrapping equipment | Difficult/impossible to automate application | Enables high-speed packaging lines, dramatically increasing throughput. |
Inspection | Transparent options allow visual inspection | Requires unwrapping/cleaning for inspection | Saves significant time and labor during quality checks and inventory management. |
Post-processing Prep | No preparation required (clean/dry surface) | Requires degreasing/cleaning before further steps | Reduces manufacturing cycle time by eliminating a cleaning step. |
Labor Requirements | Lower labor costs for application and removal | Higher labor costs for application and removal | Frees up personnel for other value-adding tasks. |
Waste Handling | Minimal waste, often recyclable | Oil waste requires special disposal procedures | Easier and potentially cheaper waste management, aligns with environmental initiatives. |
This table underscores the tangible operational benefits. The ease of application, cleanliness, compatibility with automation, and elimination of post-packaging cleaning steps combine to create a significantly more efficient workflow. These efficiencies translate directly into reduced labor costs, increased throughput, and a safer working environment, all contributing to a more profitable operation.
Versatile Applications for Diverse Metal Coil Types
Managing a variety of metal coil types and sizes demands a flexible and reliable protection method. A one-size-fits-all approach that lacks adaptability can lead to inadequate protection for certain materials or dimensions, undermining your efforts to prevent corrosion and damage across your entire product range.
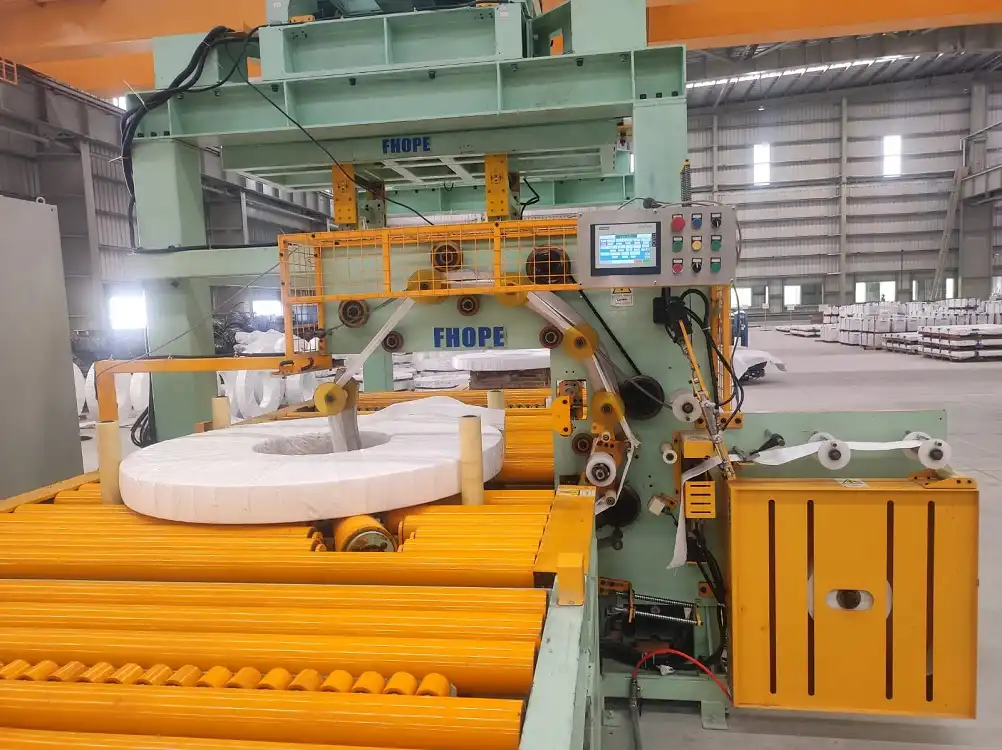
Polyethylene film offers exceptional versatility for protecting a wide array of metal coils. It can be custom-sized to fit diverse coil dimensions and is effective for protecting ferrous, non-ferrous, and multimetal alloys. Whether used for short-term storage or long-distance transit, polyethylene film provides adaptable, reliable protection against environmental factors and corrosion. This adaptability makes it an ideal choice for businesses that handle a mixed inventory of metal products. Unlike specialized coatings or treatments that might only be suitable for one type of metal, VCI polyethylene film is often formulated for multi-metal protection, simplifying inventory management and ensuring consistent results across different product lines. The film can be produced in various widths, lengths, and thicknesses, allowing for tailored solutions for anything from narrow wire coils to massive wide steel coils. It can be applied using hand wrapping, semi-automatic machines, or fully automated steel coil wrapping lines, fitting seamlessly into different operational scales and requirements. This flexibility ensures that regardless of the coil’s material, size, or intended storage/transport duration and conditions, there is a polyethylene film solution that can provide optimal protection. This capability to handle diverse applications effectively minimizes the need for multiple packaging materials and processes, further streamlining operations and reducing complexity.
Conclusion
Choosing the right packaging for your metal coils is a critical decision impacting product quality, costs, and operational efficiency. Polyethylene film, especially advanced VCI options, stands out as a superior solution, offering unparalleled protection against corrosion and physical damage. Its technical advantages, cost-saving benefits, ease of use, and versatility make it a strategic investment for safeguarding your valuable assets during storage and transit. Embrace the power of modern polyethylene film to ensure your metal coils arrive in perfect condition, every time. For enhanced efficiency, consider integrating automated coil packing line solutions.