How to Ensure Steel Wire Rewinding Machine Compatibility with Existing Systems?
Ensuring compatibility is key when integrating a new steel wire rewinding machine. Seamless operation within existing workflows is paramount. This involves careful assessment of system requirements. Consider factors like data formats, control interfaces, and physical integration points.
Ensuring steel wire rewinding machine compatibility involves assessing existing system requirements, using standard communication protocols, conducting thorough testing, and providing adequate training. This minimizes disruptions and maximizes efficiency by ensuring seamless integration guidelines.
Let’s explore in detail how to achieve this compatibility and avoid costly integration problems. Let’s delve deeper into the key strategies for ensuring a smooth and efficient integration.
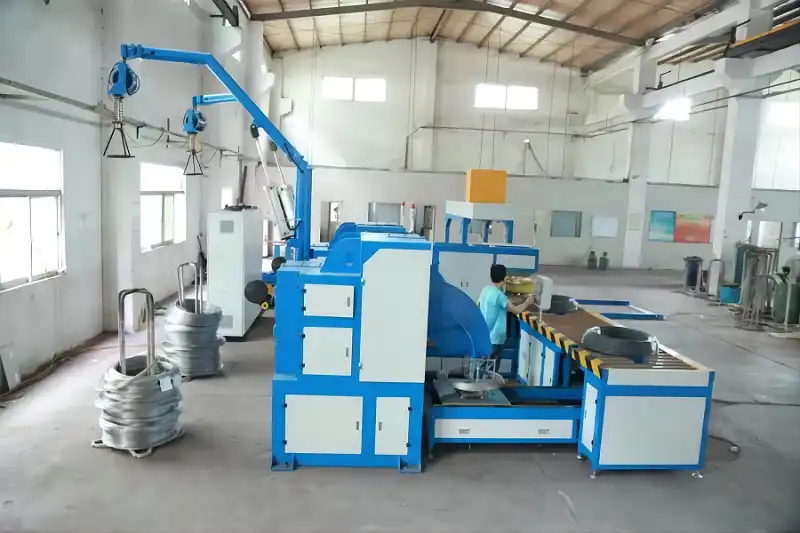
Ensuring Physical and Mechanical Compatibility
Physical integration is the foundation for a functional rewinding system. Size, weight, and mounting options must align with your existing facilities. Careful attention prevents workflow bottlenecks and ensures a safe operating environment.
To ensure physical and mechanical Steel wire rewinding machine compatibility, assess the machine’s dimensions and weight, verify mounting options, check power requirements, and ensure alignment with existing material handling systems. Addressing these aspects guarantees that the new equipment fits seamlessly into your current operations.

Detailed Considerations for Mechanical Integration:
Successfully integrating a steel wire rewinding machine into existing systems requires careful consideration of numerous factors. These can be broadly grouped into mechanical, electrical, and control system aspects. Ignoring even seemingly minor details can lead to significant delays, increased costs, and compromised performance. A proactive approach to identifying and addressing potential compatibility issues is essential.
Mechanical Interface and Alignment
The physical integration of the rewinding machine is the first hurdle. This involves verifying that the machine’s dimensions, weight, and mounting points are compatible with the existing facility and support structures. Misalignment can lead to vibration, premature wear, and even structural damage.
- Dimensions and Weight: Ensure the machine fits within the allocated space and that the floor can support its weight. Consider access for maintenance and material handling.
- Mounting Options: Confirm that the machine’s mounting points align with existing anchor points or that appropriate modifications can be made.
- Material Flow: Analyze the flow of materials into and out of the rewinding machine. Ensure smooth transitions and avoid bottlenecks.
Electrical Integration
Electrical compatibility is critical for safe and reliable operation. Voltage, current, and power requirements must be compatible with the existing electrical infrastructure. Incompatible electrical systems can lead to equipment damage, fire hazards, and downtime.
Control System Integration
The rewinding machine’s control system must be able to communicate effectively with existing control systems. This may involve integrating with PLCs, HMIs, or other automation equipment. Incompatible control systems can lead to data loss, operational inefficiencies, and safety concerns.
To ensure the seamless operation of the system it is important to use standerd interfaces and protocols. Here is a table with some common communication protocols.
Protocol | Description | Advantages | Disadvantages |
---|---|---|---|
Modbus | Serial communication protocol | Simple, widely used, open source | Limited data rate, less secure |
Profibus | Fieldbus communication system | Robust, suitable for harsh environments | More complex configuration, higher cost |
Ethernet/IP | Industrial Ethernet protocol | High bandwidth, supports real-time communication | Requires more sophisticated network infrastructure |
OPC UA | Platform-independent communication | Secure, scalable, supports complex data models | More complex implementation |
Serial Communication | Simple, inexpensive, good for short distances | Low bandwidth, point-to-point only, prone to interference |
By carefully considering these factors and implementing appropriate mitigation strategies, manufacturers can ensure a successful and cost-effective integration of steel wire rewinding machines into their existing systems.
Assessing Data and Communication Protocols
Data exchange is paramount for efficient operation. Ensure compatibility with existing systems by using standard communication protocols. This ensures seamless data transfer for production tracking and process optimization.
To assess data and communication protocols in your steel wire rewinding machine, verify compatibility with existing systems, use standard communication protocols, implement data mapping, and establish robust error handling procedures. These steps facilitate smooth data exchange and system integration.
In-Depth Look at Data and Communication Compatibility:
Effective data and communication are essential for integrating a steel wire rewinding machine seamlessly into your existing systems. This involves more than just physical connections; it requires ensuring that the data formats, communication protocols, and software interfaces are all compatible. Otherwise, you risk creating data silos, hindering automation, and reducing overall efficiency.
Data Format Standardization
The steel wire rewinding machine generates data related to production rates, wire tension, error codes, and more. This data needs to be presented in a format that your existing systems can understand. If the data formats differ, you’ll need to implement data mapping and transformation processes.
- Identify Data Points: Determine the critical data points that need to be transferred between the rewinding machine and your existing systems.
- Compare Data Formats: Analyze the data formats used by both the rewinding machine and your existing systems.
- Implement Data Mapping: Create a data mapping schema that defines how data from the rewinding machine will be translated into the format required by your existing systems.
Protocol Verification
The communication protocol dictates how data is transmitted between systems. Ensure that the protocols used by the rewinding machine are compatible with your existing network infrastructure.
Here is a list of protocols and factors to consider when choosing.
- Physical Media: Copper, Fiber or wireless
- Bandwith/Throughput:
- Latency
- Determinism
- Security
Software Integration
The rewinding machine may come with its own software for monitoring and control. Ideally, this software should integrate seamlessly with your existing manufacturing execution system (MES) or enterprise resource planning (ERP) system.
- API Availability: Check if the rewinding machine’s software provides an application programming interface (API) for integration with other systems.
- Data Exchange: Determine how data will be exchanged between the rewinding machine’s software and your existing MES/ERP system.
Implementing Thorough Testing and Validation
Rigorous testing is essential to validate compatibility. Conduct thorough tests to identify and resolve any integration issues before full-scale deployment. This proactive approach minimizes downtime and ensures reliable operation.
Implement thorough testing and validation for your steel wire rewinding machine by creating a test plan, performing functional tests, conducting performance tests, and validating data integration. This systematic approach ensures that all components work together seamlessly.
Strategies for Robust Testing and Validation:
Integrating a steel wire rewinding machine with existing systems is a multifaceted process. Even with meticulous planning, unforeseen issues can arise during implementation. Thorough testing and validation are crucial to catch these problems early, minimizing disruptions and ensuring a smooth transition.
Defining Testing Objectives
Before starting any testing, clearly define your objectives. What aspects of the integration are you trying to validate? Are you focused on data accuracy, communication speed, or the overall performance of the integrated system? Here is a sample objective and metrics table to consider during test design. |
Objective | Metric | Target Value |
---|---|---|---|
Data Accuracy | Error rate of data transfer | < 0.1% | |
Communication Speed | Time to transfer data between systems | < 1 second | |
System Performance | Throughput of rewinding process | > 95% of max. |
Developing a Comprehensive Test Plan
A well-structured test plan is essential for conducting thorough testing. The test plan should outline the specific tests that will be performed, the data that will be used, and the expected results. It should also define the roles and responsibilities of the testing team.
Testing should include:
- Functional Tests: Verify that all functions of the rewinding machine are working correctly and that the integrated system is performing as expected.
- Performance Tests: Assess the performance of the integrated system under different loads and conditions.
- Stress Tests: Subject the integrated system to extreme conditions to identify potential weaknesses.
- Regression Tests: After any changes or fixes are made, run regression tests to ensure that the changes have not introduced any new problems.
Automation Options
- Automated Testing Tools: Tools help automate repetitive tests, improving efficiency and accuracy.
- Simulation Software: Simulating different scenarios or the overall environment
Providing Comprehensive Training and Support
Effective training empowers operators to maximize system performance. Provide comprehensive training on the rewinding machine and its integration with existing systems. Ongoing support ensures smooth operation and minimizes downtime.
Comprehensive training and support are crucial for your steel wire rewinding machine. Offer initial training, create user manuals, provide ongoing technical support, and establish a feedback mechanism. This approach ensures operators are proficient and any issues are resolved promptly, maximizing system uptime and efficiency.
Ensuring seamless integration requires planning, collaboration, and a commitment to standardization.
Conclusion
Ensuring steel wire rewinding machine compatibility is paramount for seamless operation and optimized productivity. Addressing mechanical, electrical, and data aspects minimizes disruptions. Thorough testing, comprehensive training, and ongoing support contribute to a successful integration, maximizing your return on investment.