How Can Custom Mold Upenders Double Output for a Plastic Manufacturer?
Struggling with sluggish plastic mold handling? Time-consuming changeovers and risky manual maneuvering eat into production time, hindering output and profitability. Imagine slashing that downtime, enhancing safety, and unlocking significant productivity gains. Custom mold upenders offer a targeted solution to these critical bottlenecks, potentially doubling your manufacturing output.
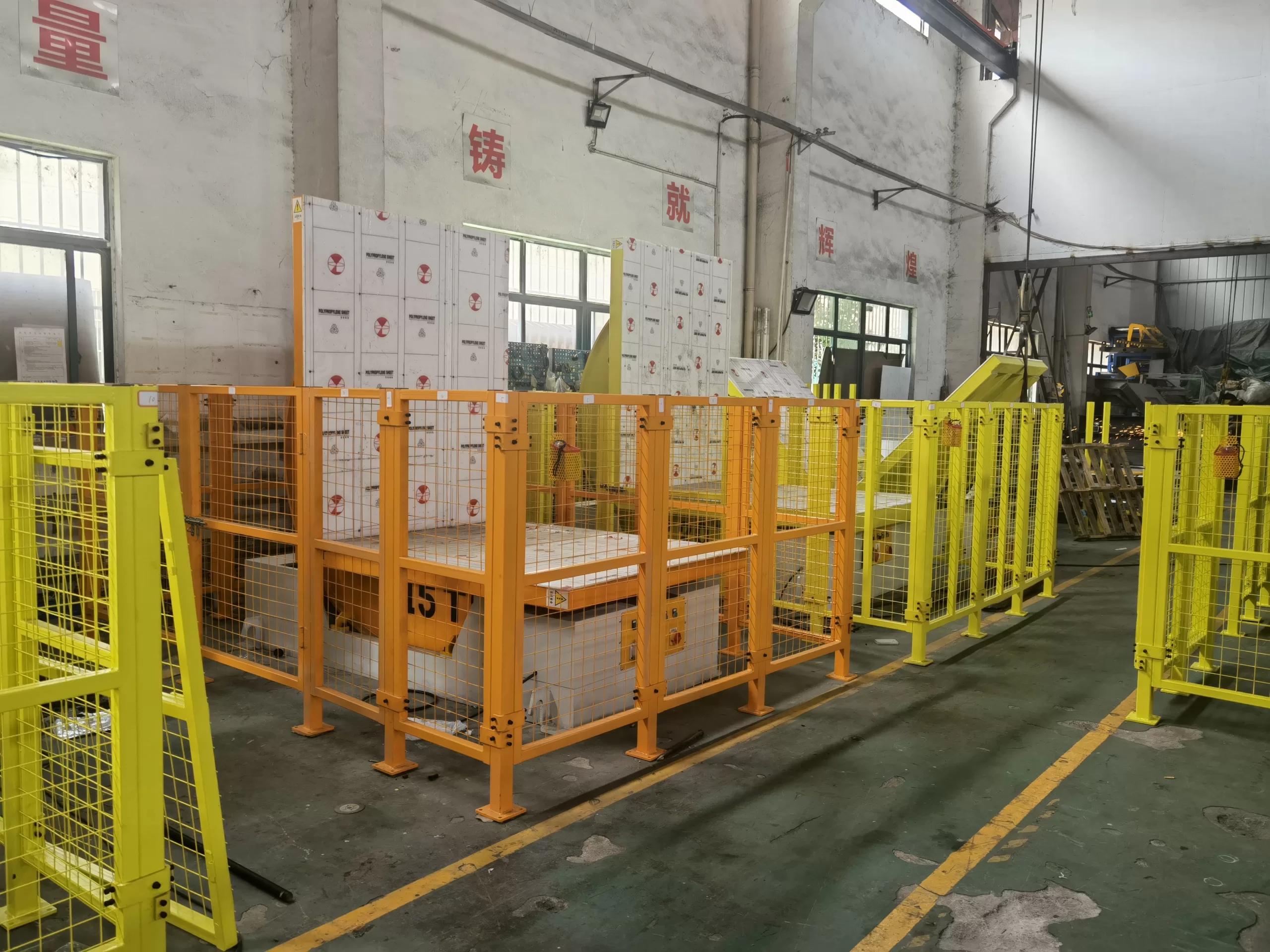
Custom mold upenders can double output by drastically reducing non-productive time associated with mold handling. They achieve this through faster, safer 90-degree mold rotation for changeovers and maintenance, minimizing machine downtime. This enhanced efficiency directly increases operational uptime, allowing for significantly more production cycles within the same timeframe, effectively boosting overall throughput and potentially doubling the units produced.
This transformative potential stems from addressing the often-overlooked inefficiencies inherent in traditional mold handling methods. Let’s delve deeper into the specific challenges faced by plastic manufacturers and how custom mold upenders provide a powerful, engineered solution.
The Bottleneck Beyond Molding: Traditional Handling Challenges
In the high-stakes world of plastic manufacturing, the focus is often on optimizing the molding cycle itself. However, significant productivity drains frequently occur in the ancillary processes, particularly the handling of large, heavy molds. These traditional methods present persistent challenges that directly impede efficiency, safety, and ultimately, output. Ignoring these bottlenecks means leaving substantial performance improvements untapped within the facility.
Traditional mold handling methods act as a major constraint on plastic manufacturing output due to inherent inefficiencies and risks. Relying on manual labor with forklifts or cranes using slings and chains is notoriously slow, labor-intensive, and poses significant safety hazards (dropped molds, worker injuries). Changeovers and maintenance access are prolonged and difficult, leading to extended machine downtime. This limited access can also compromise thorough cleaning and repair, potentially shortening mold lifespan and impacting part quality. Furthermore, these methods often require excessive floor space, contributing to workplace congestion.
Deep Dive: Why Legacy Mold Handling Holds Back Production
To fully appreciate the impact of modern solutions, it’s crucial to dissect the specific limitations imposed by conventional mold handling techniques still prevalent in many plastic manufacturing plants. These methods create friction points across multiple operational facets:
Time-Consuming Changeovers and Maintenance
Mold changeovers are a necessary part of flexible production, but traditional methods turn them into lengthy ordeals. Maneuvering multi-ton molds using cranes or forklifts requires careful coordination, multiple lifts, and precise positioning, often involving manual adjustments with pry bars or blocks. Accessing different sides of the mold for cleaning, inspection, or component replacement (like heater bands or core pins) can necessitate multiple repositioning steps. Each minute spent wrestling with the mold is a minute the injection molding machine sits idle, directly reducing potential output. Maintenance tasks suffer similarly; inadequate access can make thorough cleaning difficult or even impossible, leading to residue buildup that affects part quality or hinders mold function over time.
Inherent Safety Hazards
The manual or semi-manual handling of heavy, often irregularly shaped molds is fraught with risk. The potential for catastrophic failure, such as a dropped mold due to sling slippage or crane malfunction, poses a severe threat to personnel and equipment. Even routine handling involves risks like pinched fingers, back strains from awkward positioning, and crush injuries. The reliance on operator skill and constant vigilance adds a human error element that engineered solutions aim to minimize. High insurance premiums and the cost of workplace accidents are hidden drains associated with these outdated practices.
Limited Mold Access and Potential Damage
Beyond the time factor, traditional handling often restricts access to critical mold areas. When suspended by chains or supported precariously, technicians may struggle to reach certain surfaces or internal components effectively. This can lead to incomplete maintenance or inspections. Furthermore, the very act of lifting and maneuvering with chains, slings, or forklift tines creates opportunities for accidental damage. Gouges, scratches, or impacts on critical sealing surfaces or mold cavities can lead to costly repairs and further downtime, diminishing the lifespan of these valuable assets.
Space and Labor Inefficiencies
Maneuvering large molds with forklifts or overhead cranes requires significant clear floor space around the molding machine and maintenance areas. This can lead to inefficient plant layouts and congested work zones. Moreover, these tasks typically demand skilled operators (crane operators, forklift drivers) and often require spotters or additional personnel for safety and guidance, increasing labor costs associated with non-value-added activities.
Comparative Overview: Traditional Handling vs. Engineered Solutions
Feature | Traditional Mold Handling | Custom Mold Upenders |
---|---|---|
Safety | High risk of accidents, worker strain, mold drops | Significantly reduced risk, controlled movement, safety interlocks |
Speed | Slow changeovers & maintenance due to complex maneuvers | Much faster rotation, streamlined access |
Labor | Requires skilled operators, often multiple personnel | Reduced manual effort, often single operator |
Mold Damage Risk | Higher due to instability, potential impacts | Minimal risk due to gentle, stable handling |
Access | Often limited, difficult to reach all areas | Excellent 360-degree or 90-degree access |
Ergonomics | Physically demanding, high risk of musculoskeletal injury | Greatly improved, minimizes physical strain |
Footprint | Requires large maneuvering area | More compact, optimized space utilization |
Productivity | Lower due to significant downtime & inefficiencies | Significantly higher due to increased uptime |
These cumulative drawbacks clearly illustrate why traditional mold handling is a prime target for optimization in plastic manufacturing facilities seeking to enhance productivity and competitiveness.
Custom Mold Upenders: The Engineered Solution for Peak Productivity
Faced with the inherent risks and inefficiencies of traditional methods, plastic manufacturers need a dedicated solution. Custom mold upenders emerge as precisely that: robust, purpose-built machines designed to tackle the specific challenge of rotating heavy molds safely and efficiently, unlocking significant operational advantages.
Custom mold upenders are specialized material handling machines engineered to safely grip and rotate heavy plastic molds, dies, or tooling, typically through 90 degrees. This controlled rotation provides effortless access to different mold faces for maintenance, cleaning, or changeover procedures. Unlike generic lifting gear, they are tailored to specific mold dimensions, weights, and factory workflows, ensuring optimal performance and integration.
Key Features and Transformative Benefits
The impact of custom mold upenders goes far beyond simple rotation; they represent a fundamental shift in how mold handling is approached, delivering tangible benefits across safety, speed, and asset protection.
Precision Engineering for Safety and Control
At the heart of a custom mold upender is its drive system, typically hydraulic or electromechanical. These systems are designed for smooth, controlled, and predictable rotation, eliminating the sudden starts, stops, and potential instability associated with crane or forklift handling. Heavy-duty construction ensures stability even with multi-ton molds. Integrated clamping mechanisms securely grip the mold before rotation begins. Standard safety features often include emergency stop buttons, safety guarding or light curtains, and mechanical or hydraulic locking systems to prevent unintended movement, drastically reducing the risk of accidents and mold damage during the handling process.
Ergonomics and Enhanced Worker Safety
By automating the strenuous task of mold rotation, upenders significantly improve workplace ergonomics. They eliminate the need for workers to manually push, pull, or strain to position heavy molds, minimizing the risk of back injuries, sprains, and other musculoskeletal disorders. This creates a safer working environment, boosting morale and reducing costs associated with workplace injuries and lost time. The operator typically controls the rotation via a simple push-button pendant or control panel from a safe distance.
Accelerating Changeovers and Maintenance Cycles
This is where the productivity gains become most apparent. A custom mold upender can rotate a large mold 90 degrees in a matter of minutes, compared to the potentially hour-long (or longer) process using traditional methods. Once rotated, the mold is held securely, providing unobstructed access to all necessary surfaces. Technicians can perform cleaning, inspections, repairs, or component replacements far more quickly and efficiently. This dramatic reduction in time spent on changeovers and maintenance directly translates into increased uptime for the molding machines, paving the way for higher production output.
Protecting Assets: Improved Mold Longevity
Plastic injection molds are significant capital investments. The gentle, controlled handling provided by a custom upender minimizes the risk of accidental damage – scratches, dents, or impacts – that can occur during manual or crane-based maneuvering. Furthermore, the easy access facilitated by upenders allows for more thorough and consistent cleaning and preventative maintenance. Removing residual plastic, cleaning vents, and lubricating components becomes easier, contributing to optimal mold performance and extending its operational lifespan, maximizing the return on investment.
The Power of Customization (Tailored Fit)
The "custom" aspect is critical. Reputable suppliers don’t offer a one-size-fits-all solution. They work closely with the manufacturer to design an upender specifically suited to their range of mold sizes, weights, shapes, and handling interfaces (e.g., compatibility with existing overhead cranes or forklifts for loading/unloading onto the upender). Platform size, load capacity, rotation mechanism, control integration, and even paint color can be tailored. This bespoke approach ensures the upender integrates seamlessly into the existing workflow and optimally handles the specific molds used by the facility, maximizing its effectiveness.
Quantifying the Gains: How Doubled Output Becomes Reality
The claim that custom mold upenders can double output might sound bold, but it’s rooted in the tangible, cumulative impact of eliminating wasted time and optimizing workflows. It’s not magic; it’s the result of targeted efficiency improvements compounding over every production cycle.
Doubling output is achievable because custom mold upenders attack the primary sources of non-productive time in mold handling. By drastically cutting mold changeover durations (often by 50% or more) and significantly reducing maintenance downtime through faster, safer access, they substantially increase the available production time (uptime) for molding machines, enabling more parts to be produced per shift.
Data-Driven Impact Analysis
Let’s break down how these time savings translate into substantial output increases using a realistic, albeit illustrative, scenario.
Slashing Non-Productive Time
Consider mold changeovers. If a traditional changeover takes 4 hours (including mold removal, transport, potential manual flipping/positioning, cleaning/prep, and installation), implementing a custom upender can streamline the rotation and access part of this process significantly. The upender might reduce the time needed for safe rotation and access from, say, 1.5 hours down to 15-30 minutes. Combined with other process optimizations often implemented alongside new equipment, it’s feasible to cut the total changeover time in half, perhaps from 4 hours to 2 hours. Similarly, routine maintenance that required extensive maneuvering and positioning might be halved in duration due to easy, stable access provided by the upender.
Maximizing Machine Uptime
Every hour saved during a changeover or maintenance cycle is an hour gained for production. If a facility performs several mold changes per week and regular maintenance, these savings accumulate rapidly. Let’s look at a hypothetical week:
- Before Upender: 3 changeovers/week @ 4 hours each = 12 hours downtime. Monthly major maintenance = 8 hours downtime. Total = 20 hours non-productive time related to handling per period considered.
- After Upender: 3 changeovers/week @ 2 hours each = 6 hours downtime. Monthly major maintenance = 4 hours downtime. Total = 10 hours non-productive time related to handling per period.
This reduction of 10 hours of downtime per week/period translates directly into 10 more hours of potential production time for the molding machine. Over a month or year, this represents a significant increase in available operating hours.
Optimizing Labor Resources
While not directly doubling output itself, optimizing labor contributes to overall efficiency. Tasks that previously required multiple skilled personnel (e.g., crane operator + spotters + technicians maneuvering) might now be handled more safely and quickly by fewer people, often a single operator controlling the upender. This frees up skilled labor to focus on value-added tasks like process monitoring, quality control, or performing maintenance on other equipment, further boosting overall plant productivity.
Illustrative Example: Productivity Boost with Custom Mold Upenders
Metric | Before Upender Implementation | After Upender Implementation | Improvement |
---|---|---|---|
Average Mold Changeover Time | 4 hours | 2 hours | 50% Reduction |
Average Maintenance Downtime per Mold (Monthly) | 8 hours | 4 hours | 50% Reduction |
Molding Machine Uptime per Week (Illustrative) | 100 hours | 110+ hours | 10%+ Increase |
Potential Production Output per Week | X Units | Approaching 2X Units | Potential Doubling |
Note: Doubling output relies on handling being a primary bottleneck. The table illustrates how significant uptime gains (e.g., 10 hours/week saved) directly increase production capacity. If a machine was running 100 hours/week and now runs 110 hours, that’s a 10% immediate capacity increase from saved time alone. If the original bottleneck was severe enough that uptime effectively doubles (less likely but possible in extreme cases), or if faster cycles are enabled by better maintenance, output can approach or reach double.
This data-driven perspective shows that doubling output isn’t just hyperbole; it’s a quantifiable outcome achievable through strategic investment in eliminating critical inefficiencies with custom mold upenders.
Choosing the Right Partner: The Importance of Customization Expertise
Realizing the full potential of a mold upender hinges critically on selecting a solution truly tailored to your specific operational needs. Generic, off-the-shelf equipment might seem cheaper initially but often fails to adequately address the unique dimensions, weights, handling requirements, and workflow integration needed in a busy plastic manufacturing environment. Partnering with a supplier specializing in custom material handling solutions is paramount.
A qualified custom mold upender supplier doesn’t just sell equipment; they provide an engineered solution. They conduct thorough site assessments, analyze mold fleets and processes, and design a machine precisely matched to requirements, utilizing robust components and proven safety features. Crucially, they offer expert installation, commissioning, training, and ongoing support to ensure maximum performance, reliability, and return on investment.
What to Look For in a Custom Mold Upender Supplier
Selecting the right partner involves evaluating several key capabilities and characteristics:
- Thorough Needs Assessment: A reputable supplier will begin by deeply understanding your operation. This includes analyzing your current mold handling methods (identifying pain points), cataloging your mold inventory (sizes, weights, shapes, center of gravity considerations), mapping your workflow (machine layout, maintenance areas, transport paths), and discussing your specific goals (safety improvement, downtime reduction targets).
- Engineering and Design Capabilities: Look for suppliers with in-house engineering expertise. They should be able to translate your needs into a detailed design proposal, specifying the appropriate load capacity, platform dimensions, rotation mechanism (hydraulic, mechanical), clamping system, control interface (pendant, integrated panel), and necessary safety features (interlocks, guarding, sensors). They should be adept at designing for durability using heavy-duty steel construction and high-quality components.
- Proven Track Record and Build Quality: Ask for case studies, references, or examples of similar projects they have completed, particularly within the plastics industry. Assess the build quality of their equipment – look for robust welds, reliable hydraulics/mechanics, durable finishes, and attention to detail in wiring and assembly. Reliability is key; the upender itself should not become a source of downtime.
- Safety Standards Compliance: Ensure the supplier designs and builds equipment that meets or exceeds relevant safety standards (e.g., ANSI, CE). They should be knowledgeable about integrating safety features effectively.
- Installation, Training, and Support: The supplier’s responsibility shouldn’t end at delivery. They should offer professional installation and commissioning services to ensure the upender is set up correctly and safely. Comprehensive operator and maintenance training is essential for proper use and longevity. Furthermore, inquire about their after-sales support, including warranty terms, availability of spare parts, and responsiveness for service or technical assistance. A strong support network minimizes potential disruptions.
By carefully evaluating potential suppliers based on these criteria, plastic manufacturers can forge a partnership that delivers a truly optimized custom mold upender solution, paving the way for the significant productivity and safety gains promised by this technology. Investing time in choosing the right partner is as crucial as investing in the equipment itself.
Conclusion
Custom mold upenders represent a strategic investment for plastic manufacturers seeking a competitive edge. By directly addressing the significant inefficiencies and safety hazards inherent in traditional mold handling, these engineered solutions unlock substantial gains. They dramatically reduce costly downtime associated with mold changeovers and maintenance, directly increasing machine uptime and paving the way to potentially double production output. Enhanced worker safety, improved ergonomics, and extended mold lifespan through gentle handling and better access are further crucial benefits. Investing in Custom machinery like tailored upenders is not merely an equipment upgrade; it’s a fundamental step towards a more efficient, safer, and profitable future in plastic manufacturing.