Enhancing Workshop Safety and Efficiency: A Deep Dive into the Mold Flipper Lift Table
Handling heavy and cumbersome molds or dies is a significant challenge in many manufacturing and fabrication environments. Improper handling not only poses serious safety risks to personnel but can also lead to costly damage to valuable tooling. The Mold Flipper Lift Table, also known as a mold upender or die rotator, represents a crucial piece of equipment designed to address these challenges head-on, streamlining maintenance workflows and boosting operational safety. This article explores the design, specifications, benefits, and operational insights of these essential machines, supported by a demonstration video.
The video above showcases a typical mold flipper lift table undergoing testing, clearly illustrating the controlled and secure process of rotating a heavy mold. This operation is fundamental for tasks such as mold inspection, cleaning, repair, and preparation for storage or production.
1. Understanding the Mold Flipper Lift Table: Purpose and Need
A Mold Flipper Lift Table is a specialized piece of industrial equipment engineered to safely rotate heavy objects, primarily molds and dies, typically by 90 or 180 degrees. The core needs driving its adoption in the industry include:
- Enhanced Safety: Eliminates dangerous manual flipping attempts or the use of inadequate lifting gear (e.g., cranes with slings) for rotation, significantly reducing the risk of accidents and injuries.
- Improved Efficiency: Automates and simplifies the mold turning process, drastically cutting down the time and labor required compared to manual methods. This translates to reduced downtime during maintenance or changeovers.
- Tooling Protection: Provides a stable, controlled rotation, preventing shocks, drops, or impacts that could damage sensitive mold surfaces, cavities, or components.
2. Core Functionality: The Mechanics of Rotation
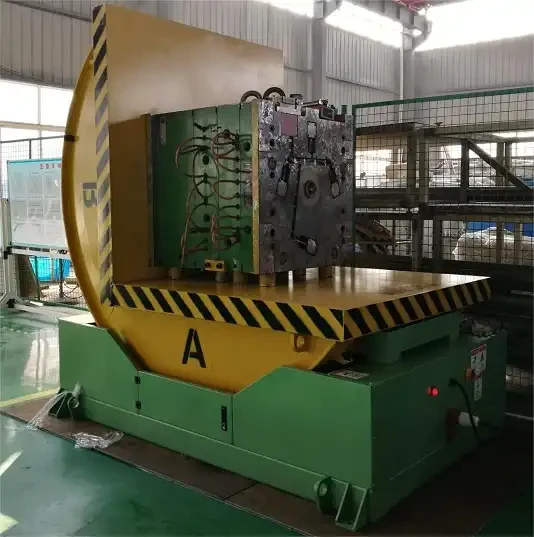
Most mold flippers utilize a robust hydraulic system, though electro-mechanical designs also exist. The typical operation involves:
- Loading: The mold is placed securely onto one of the machine's tables or platforms, often using a forklift or overhead crane.
- Securing (Optional): Depending on the design and load, clamping mechanisms may be engaged.
- Rotation: The operator initiates the flipping cycle via a control panel. Hydraulic cylinders or mechanical drives power the coordinated movement of the tables, rotating the mold smoothly to the desired orientation (usually 90° or 180°).
- Unloading: Once rotation is complete, the mold can be accessed for work or safely removed from the machine.
The video provides a clear visual representation of this controlled hydraulic actuation.
3. Design and Structural Components Analysis
A reliable mold flipper lift table is built for durability and safety, typically featuring:
- Heavy-Duty Steel Frame: Forms the structural backbone, designed to withstand the rated load capacity and the dynamic forces during rotation. Often utilizes welded structural steel profiles (e.g., H-beams, rectangular tubes).
- Rotating Tables/Platforms: Two robust platforms, often with T-slots or specific mounting points, support the mold. One table typically remains stationary or provides linear movement while the other pivots or rotates around it. Surface materials might include checkered plate for grip or smooth steel plate depending on application.
- Hydraulic System: Includes hydraulic power unit (motor, pump, reservoir), cylinders, valves, and hoses. This system provides the high force required for smooth and controlled rotation of heavy loads. Key considerations are cylinder bore size, rod diameter, stroke length, and system pressure ratings.
- Power and Drive Mechanism: Besides hydraulics, some units might incorporate heavy-duty chains, sprockets, gearboxes, or slewing rings driven by electric motors for rotation.
- Control System: An operator panel (push-button pendant or console) allows for safe initiation and control of the flipping process. Includes essential safety features like emergency stops and potentially interlocks. Electrical components conform to relevant industrial standards (e.g., IEC, NEMA).
- Bearings and Pivot Points: High-capacity bearings (e.g., spherical roller bearings, slewing rings) are critical at pivot points to ensure smooth rotation and handle the immense loads.
4. Technical Specifications Deep Dive
Selecting the appropriate mold flipper requires careful consideration of its technical parameters. The table below outlines typical specifications for various models, like the FPFT series:
Parameter | FPFT-05 | FPFT-10 | FPFT-15 | FPFT-20 | FPFT-30 | FPFT-40 | Unit | Description |
---|---|---|---|---|---|---|---|---|
Max Flipping Load | 5 | 10 | 15 | 20 | 30 | 40 | Ton (Metric) | The maximum weight the machine can safely flip. |
Table L Dimension | 3010 | 3440 | 3810 | 4240 | 4640 | 5560 | mm | Length of the primary support table/platform. |
Table W Dimension | 1200 | 1400 | 1600 | 1800 | 2000 | 2400 | mm | Width of the primary support table/platform. |
Table H Dimension | 300 | 350 | 350 | 400 | 450 | 500 | mm | Height of the table surface from the floor. |
Motor Output | 3.7 | 5.5 | 7.5 | 11 | 11 | 15 | kW | Power rating of the hydraulic pump motor. |
Machine Weight | 2 | 3 | 3.5 | 4 | 5 | 7.5 | Ton (Metric) | Approximate overall weight of the machine. |
Oil Reservoir | 10 | 20 | 20 | 40 | 40 | 85 | Liter | Capacity of the hydraulic fluid reservoir. |
Interpreting the Data:
- Load Capacity: This is paramount. Always select a machine rated significantly above the weight of your heaviest mold.
- Table Dimensions (L x W): Must accommodate the footprint of your largest molds. Ensure the mold sits stably within the table area.
- Table Height (H): Influences loading/unloading ergonomics and compatibility with handling equipment like forklifts.
- Motor Output: Correlates with flipping speed and the ability to handle loads smoothly, especially near maximum capacity.
- Machine Weight: Indicates the robustness of construction and influences foundation requirements.
- Oil Reservoir: Larger reservoirs help dissipate heat in the hydraulic system, crucial for continuous or frequent operation.
Comparing models involves matching your specific mold dimensions and weights to the machine's capabilities, considering operational frequency and available floor space.
5. Key Features and Benefits
Investing in a mold flipper lift table offers tangible advantages:
- Dramatically Improved Safety: Minimizes risks associated with manual handling of heavy, awkward loads. Controlled movement prevents sudden shifts or drops.
- Increased Operational Efficiency: Reduces mold rotation time from potentially hours (with manual methods) to minutes.
- Protection of Assets: Gentle, controlled flipping prevents damage to expensive molds and dies.
- Reduced Labor Costs: Frees up personnel typically required for complex manual or crane-assisted turning operations.
- Ergonomic Operation: Simplifies the task, reducing physical strain on workers.
- Versatility: Can often handle various types of heavy objects beyond molds, such as steel coils, large fabrications, or engine blocks.
6. Applications Across the Fabrication and Manufacturing Industries
Mold flipper tables are indispensable in various sectors:
- Injection Molding: For maintenance, cleaning, and changeover of large injection molds.
- Die Casting: Handling heavy dies for repair, servicing, and setup.
- Stamping: Turning large stamping dies for maintenance and inspection.
- Tool and Die Shops: Essential equipment for shops that build, repair, or maintain molds and dies.
- Heavy Equipment Manufacturing: Used for rotating large components or sub-assemblies during production or maintenance.
7. Personal User Experience and Operational Considerations
From an operator's perspective, using a mold flipper lift table generally involves:
- Ease of Control: Modern units feature intuitive controls, often a simple push-button pendant, making operation straightforward after basic training.
- Loading/Unloading Strategy: Requires careful planning with forklifts or cranes to position the mold correctly and safely onto the table. Clear access around the machine is vital.
- Cycle Time: Flipping cycles are typically quick (often under a minute), contributing significantly to workflow efficiency.
- Maintenance: Regular checks are necessary, primarily focusing on the hydraulic system (fluid levels, leaks, filter changes) and lubrication of pivot points and bearings as per manufacturer guidelines.
- Noise Levels: The hydraulic power unit generates some noise during operation, which should be considered in terms of workplace noise exposure.
- Footprint: These are substantial machines requiring dedicated floor space with adequate clearance for operation and access.
8. Critical Safety Considerations
Safety remains paramount when operating mold flippers:
- Operator Training: Only trained and authorized personnel should operate the equipment.
- Load Capacity Adherence: Never exceed the machine's rated load capacity.
- Load Stability: Ensure the mold is positioned correctly and stably on the table before initiating rotation. Use clamps or blocking if necessary.
- Clear Operating Zone: Maintain a safe perimeter around the machine during operation, keeping personnel clear of moving parts.
- Emergency Stops: Ensure E-stops are accessible and functional.
- Regular Inspections: Perform pre-operational checks and follow a regular maintenance schedule to ensure all components are in good working order.
9. Choosing the Right Mold Flipper for Your Needs
Selecting the ideal mold flipper involves assessing:
- Maximum Mold Weight: The primary determining factor.
- Mold Dimensions: Ensure the table size (L x W) is adequate.
- Required Rotation Angle: Most offer 90° or 180°, confirm it meets your needs.
- Operational Frequency: Higher frequency might necessitate a more robust hydraulic system or faster cycle times.
- Available Space and Utilities: Consider the machine's footprint and power requirements (typically 3-phase electrical).
- Budget: Balance features and capacity against cost.
Conclusion
The mold flipper lift table is more than just a handling device; it's a strategic investment in workshop safety, efficiency, and asset protection. By replacing hazardous manual methods with controlled, automated rotation, these machines streamline critical maintenance and handling processes for heavy molds and dies. Understanding their design, capabilities, and operational requirements allows facilities to select and implement the right solution, ultimately contributing to a safer and more productive fabrication environment.
Further Information:
For more details on specific models and technical inquiries:
- Explore the Mold Flipper Lift Table product overview.
- Visit the detailed page: https://www.fhopepack.com/Hydraulic/mold-flipper-table.html
- Contact the technical team directly at info@fhopepack.com