Are you tired of rust eating away at your steel coils, leading to costly losses and dissatisfied customers? Moisture is the silent enemy of steel, and improper packaging is an open invitation for corrosion. Imagine the frustration of unwrapping a brand-new steel coil only to find it marred by rust and water damage. The solution? Effective moisture protection packaging.
The best way to achieve steel coil moisture protection packaging is by utilizing a coil packing machine that employs stretch film. This method creates a tight, airtight seal around the coil, significantly reducing air and moisture exposure, thereby preventing corrosion and water damage during storage and transit.
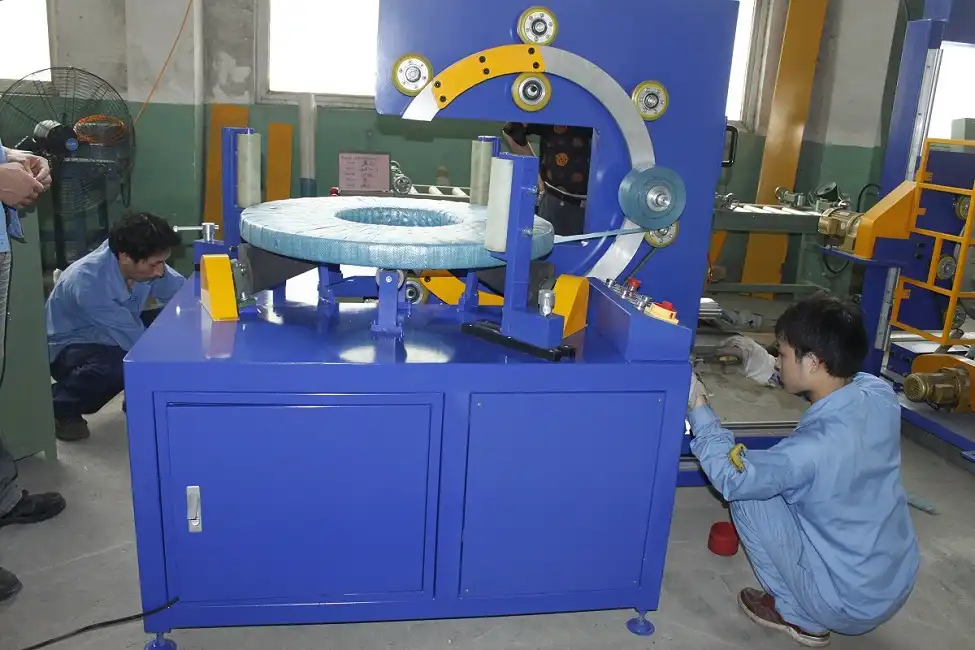
But simply wrapping your steel coils isn’t enough. Choosing the right method and materials is crucial for long-lasting protection and peace of mind. Let’s explore the essential aspects of steel coil moisture protection packaging to ensure your products arrive in perfect condition, every time.
Understanding the Enemy: Moisture and Steel Coil Degradation
Moisture is the primary culprit behind steel coil corrosion. Have you ever wondered why some steel coils develop rust while others remain pristine? The answer lies in understanding how moisture interacts with steel and accelerates degradation. Ignoring this fundamental aspect can lead to significant product damage and financial setbacks.
Steel coil degradation due to moisture occurs through a process called oxidation, commonly known as rusting. When steel, primarily composed of iron, comes into contact with water and oxygen, a chemical reaction takes place, forming iron oxide (rust). This rust weakens the steel, compromises its structural integrity, and diminishes its surface quality.
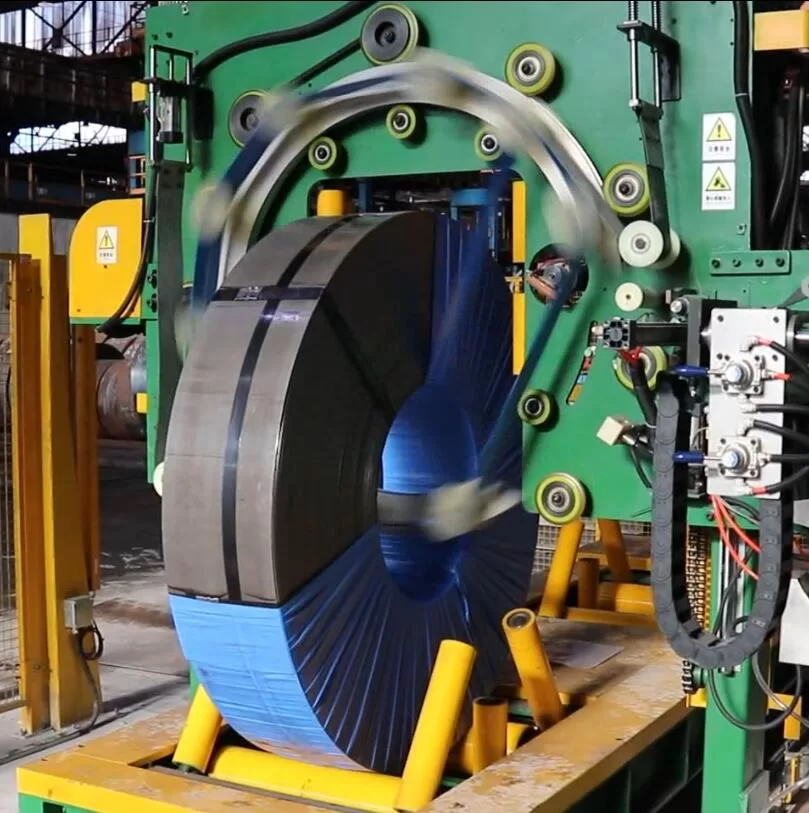
To truly combat moisture damage, we need to dive deeper into the mechanisms of corrosion and the factors that exacerbate it. Understanding these nuances is key to selecting the most effective packaging strategies and ensuring your steel coils remain in top condition.
The Science of Steel Corrosion: A Deeper Dive
Steel corrosion is not a simple surface phenomenon; it’s an electrochemical process. Let’s break down the key elements that contribute to rust formation:
Electrochemical Reactions
Rusting is an electrochemical reaction where iron loses electrons (oxidation) and oxygen gains electrons (reduction) in the presence of water, acting as an electrolyte. This process creates anodic and cathodic areas on the steel surface, leading to electron flow and ion migration, ultimately forming rust.
Factors Accelerating Corrosion
Several factors can accelerate the rate of steel corrosion:
- Humidity: Higher humidity levels mean more moisture in the air, directly increasing the risk of condensation and water exposure on steel surfaces.
- Temperature Fluctuations: Temperature changes can cause condensation. As warm air cools, it loses its capacity to hold moisture, leading to water droplets forming on cooler surfaces like steel coils.
- Contaminants: Airborne pollutants like sulfur dioxide and chlorides can react with moisture to form acidic or corrosive solutions, further accelerating rust. Saltwater environments are particularly aggressive due to high chloride concentrations.
- Exposure Time: The longer steel coils are exposed to humid or moist conditions, the greater the extent of corrosion. Prolonged storage or shipping times without proper protection significantly increase the risk.
Types of Corrosion Affecting Steel Coils
Steel coils can suffer from various types of corrosion, each with distinct characteristics:
Type of Corrosion | Description | Contributing Factors | Impact on Steel Coils |
---|---|---|---|
General Corrosion | Uniform rusting over the entire surface. | Prolonged exposure to humid air and moisture. | Overall weakening and surface degradation. |
Pitting Corrosion | Localized, deep holes or pits form on the surface. | Inhomogeneities in steel, stagnant moisture. | Concentrated weakening, potential structural failure. |
Crevice Corrosion | Corrosion in tight spaces where moisture can become trapped. | Poorly sealed overlaps in packaging, tight coil wraps. | Hidden corrosion, difficult to detect early. |
Galvanic Corrosion | Occurs when dissimilar metals are in contact in the presence of an electrolyte. | Contact with incompatible metals, electrolyte presence. | Accelerated corrosion of the more active metal. |
Understanding these corrosion types and their causes allows for targeted packaging strategies. For instance, in humid climates, preventing general corrosion is paramount, while for coils stored outdoors, preventing pitting and crevice corrosion becomes more critical. By addressing these specific threats, we can significantly enhance the effectiveness of steel coil moisture protection.
Choosing the Right Packaging Materials for Moisture Protection
Selecting the correct packaging materials is paramount in the fight against moisture-induced corrosion. Imagine using a paper bag to protect your valuable electronics from water – it simply wouldn’t work! Similarly, not all packaging materials offer the same level of moisture protection for steel coils. The effectiveness of your packaging directly depends on the materials you choose.
The ideal packaging materials for steel coil moisture protection are those that create a robust barrier against moisture ingress. These materials typically include stretch film, vapor corrosion inhibitor (VCI) paper, and specialized waterproof papers or laminates. The selection depends on factors like storage duration, environmental conditions, and budget.
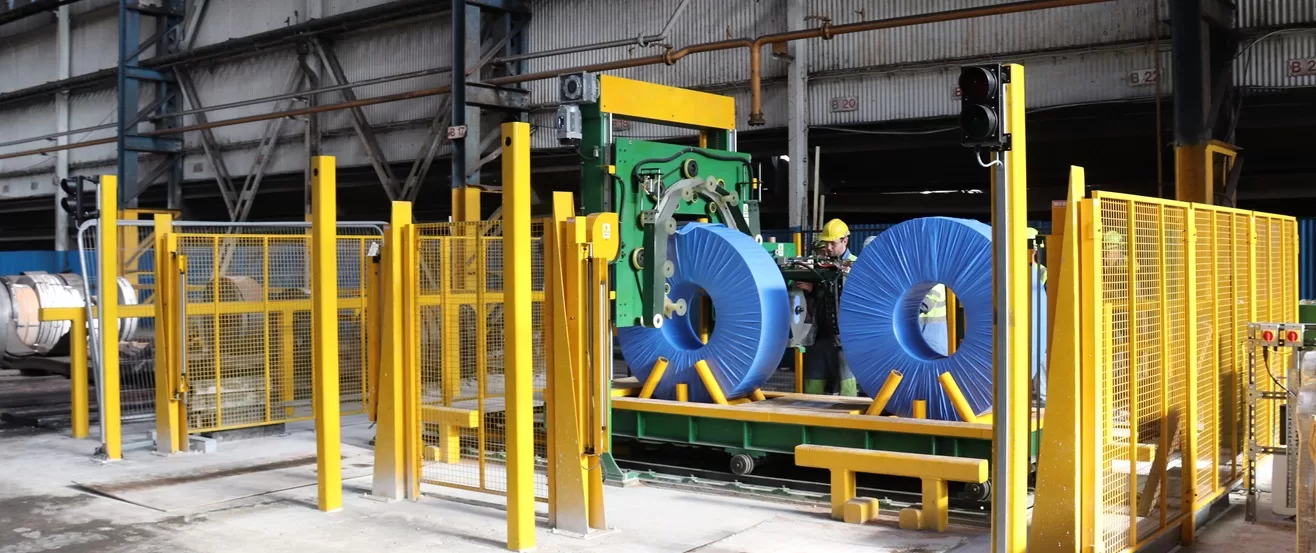
But with so many options available, how do you determine the best fit for your specific needs? Let’s explore the pros and cons of various moisture-resistant packaging materials to make an informed decision.
Moisture Barrier Material Comparison
The market offers a range of materials claiming moisture resistance, but their effectiveness varies significantly. Let’s analyze some common options:
1. Stretch Film (LLDPE)\
- Pros:
- Excellent water resistance when applied correctly with sufficient overlap and tension.
- Cost-effective and readily available.
- Provides a tight, conformable wrap.
- Transparent, allowing for visual inspection.
- Cons:
- Can be punctured or torn if not handled carefully.
- Offers limited long-term moisture vapor barrier properties compared to specialized films.
- UV degradation if not UV stabilized.
2. Vapor Corrosion Inhibitor (VCI) Paper
- Pros:
- Releases VCI chemicals that inhibit corrosion on steel surfaces.
- Provides dry corrosion protection.
- Easy to apply and handle.
- Recyclable options available.
- Cons:
- Effectiveness diminishes over long periods as VCI chemicals deplete.
- May not be sufficient in extremely humid or wet conditions without additional barrier layers.
- Can be more expensive than standard paper.
3. Waterproof Paper/Laminates (PE Coated, Waxed)
- Pros:
- Good water resistance due to coatings or laminations.
- Stronger and more tear-resistant than plain paper.
- Can be combined with VCI for enhanced protection.
- Cons:
- May not be completely impermeable to moisture vapor over extended periods.
- Coatings can be damaged, reducing water resistance.
- Disposal can be more complex than plain paper.
4. Aluminum Foil Laminates
- Pros:
- Excellent moisture vapor barrier properties.
- Provides a complete barrier to moisture ingress.
- Good for long-term storage and harsh environments.
- Cons:
- More expensive than other options.
- Less flexible and conformable than films or papers.
- Can be prone to pinhole leaks if creased or damaged.
Material Selection Guide
The best material choice depends on your specific needs. Here’s a simplified guide:
Protection Level Needed | Storage Duration | Environment | Recommended Material(s) | Cost |
---|---|---|---|---|
Basic Moisture Protection | Short-term | Indoor, Dry | Stretch Film, PE Coated Paper | Low |
Enhanced Protection | Medium-term | Indoor, Humid | VCI Paper + Stretch Film, Waterproof Paper | Medium |
Premium Protection | Long-term | Outdoor, Harsh | Aluminum Foil Laminate + VCI, Heavy-duty Waterproof Laminate | High |
By carefully considering these material properties and your specific requirements, you can select the packaging materials that offer the optimal balance of protection, cost-effectiveness, and practicality for your steel coil moisture protection needs.
Implementing Effective Steel Coil Packaging Techniques
Even with the best materials, improper packaging techniques can undermine your moisture protection efforts. Think of it like building a house – even with the strongest bricks, a poorly constructed foundation will lead to collapse. Similarly, using top-quality moisture barrier materials is only half the battle; correct application is equally crucial.
Effective steel coil packaging techniques focus on creating a complete and secure moisture barrier. This involves proper wrapping methods, ensuring adequate overlap of materials, sealing edges and openings, and considering the coil’s orientation and handling during packaging.
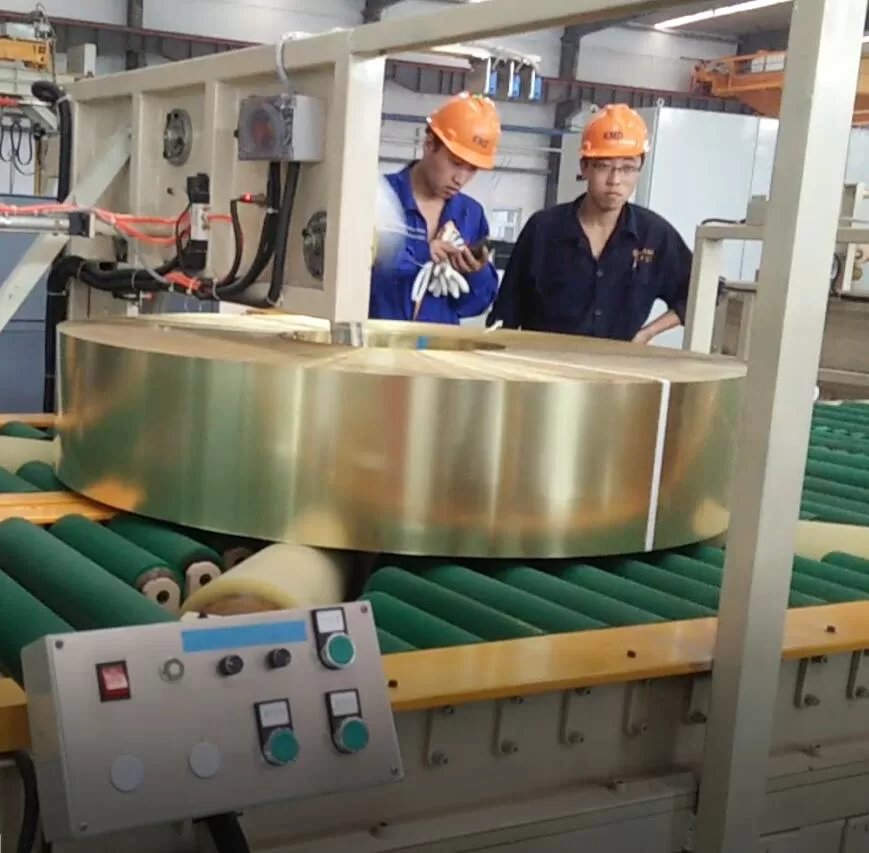
Let’s explore the key techniques that will transform your packaging from simply adequate to truly moisture-proof, safeguarding your steel coils against the elements.
Key Packaging Techniques for Moisture Prevention
Mastering these techniques will significantly enhance your steel coil moisture protection:
1. Eye (Spiral) Wrapping with Coil Packing Machines
- Technique: Wrapping material is applied spirally through the eye (center) of the coil, ensuring complete coverage of both inner and outer surfaces.
- Advantages:
- Provides consistent and uniform wrapping quality.
- Minimizes gaps and openings for moisture ingress.
- Efficient and fast, especially with automated machines.
- Controllable tension for a tight, secure wrap.
- Machine Recommendation: FHOPEPACK Steel Coil Wrapping Machines, Dixing Machinery Coil Wrapping Machine
2. Overlap and Sealing
- Technique: Ensuring sufficient overlap of wrapping material layers (e.g., stretch film) to create a multi-layered barrier. Sealing edges with tape or heat sealing to prevent moisture entry through seams.
- Importance: Overlap doubles or triples the barrier thickness at critical points. Sealing prevents capillary action drawing moisture into overlaps.
- Best Practices: Minimum 50% overlap for stretch film, heat sealing or moisture-resistant tape for paper edges.
3. Vertical vs. Horizontal Wrapping Orientation
- Vertical Wrapping: Coil stands upright, inner diameter facing outwards. Economical, suitable for crane or forklift handling.
- Horizontal Wrapping: Coil lies flat, inner diameter facing upwards. Ideal for automated lines, delicate coils, and small IDs. Provides more uniform wrapping and support.
- Moisture Consideration: Horizontal wrapping often provides better overall moisture protection due to more consistent material tension and coverage across the coil’s broad surfaces.
4. Edge Protection
- Technique: Applying edge protectors (cardboard, plastic, or foam) to coil edges before wrapping to prevent film tearing and concentrate wrapping force on the coil body.
- Benefit: Prevents film punctures at sharp edges, maintaining barrier integrity. Distributes wrapping tension evenly.
- Material Options: Cardboard edge boards, plastic corner protectors, foam profiles.
5. Desiccants and VCI Emitters
- Technique: Placing desiccants (silica gel, clay) inside the package to absorb any trapped moisture. Using VCI emitters (pouches, foams) to release corrosion inhibitors in enclosed spaces.
- Purpose: Desiccants capture residual moisture. VCI emitters provide an extra layer of corrosion protection in enclosed spaces, particularly effective in long-term storage.
- Placement: Desiccants should be placed in multiple locations within the wrap. VCI emitters positioned to ensure vapor distribution.
By meticulously applying these techniques, you move beyond simply enclosing the coil to creating a truly protective environment that actively combats moisture damage, ensuring your steel coils remain corrosion-free.
Automation and Efficiency: Coil Packing Machines
Manual steel coil packaging is labor-intensive, inconsistent, and often falls short of providing optimal moisture protection. Imagine your team struggling to hand-wrap heavy coils, battling uneven wraps and gaps, while production deadlines loom. This inefficient approach not only increases labor costs but also elevates the risk of inadequate packaging and subsequent product damage.
Coil packing machines offer an automated, efficient, and consistent solution for steel coil moisture protection packaging. These machines utilize eye wrapping technology to apply stretch film or other barrier materials tightly and uniformly, minimizing labor, maximizing throughput, and ensuring superior protection against moisture and corrosion.
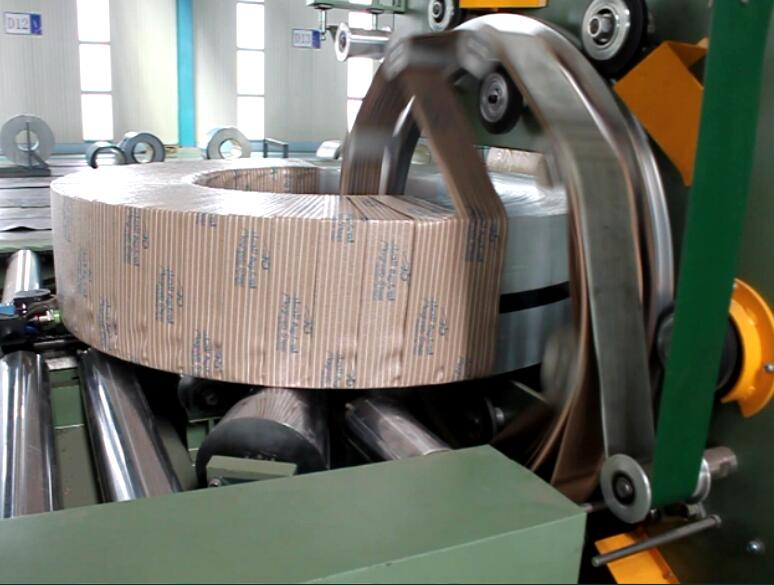
But are coil packing machines a worthwhile investment? Let’s examine the tangible benefits and address common concerns to understand how automation can revolutionize your steel coil packaging process.
- Benefits of Coil Packing Machines: Dive Deeper Paragraph
Quantifiable Advantages of Automated Coil Packing
Investing in a coil packing machine transcends mere automation; it’s a strategic move towards enhanced efficiency, cost savings, and superior product protection. Let’s quantify the advantages:
1. Increased Efficiency and Throughput
- Manual Wrapping: Typically, manual wrapping of a single steel coil can take 15-30 minutes, depending on size and complexity.
- Coil Packing Machine: An automated machine can wrap a coil in just 1-3 minutes.
- Throughput Increase: Machines can increase packaging throughput by 500-1000% compared to manual methods, significantly boosting production capacity.
2. Labor Cost Reduction
- Manual Packaging: Requires 2-3 workers per wrapping station, leading to substantial labor costs, especially for high-volume operations.
- Automated Machine: Often requires only one operator to oversee machine operation and material loading, drastically reducing labor needs.
- Labor Savings: Companies can typically reduce labor costs by 60-80% by switching to automated coil packing.
3. Consistent and Controllable Packaging Quality
- Manual Wrapping: Quality varies greatly depending on worker skill and fatigue, leading to inconsistent overlap, tension, and sealing, and compromised moisture protection.
- Coil Packing Machine: Machines provide precise control over wrapping parameters like tension, overlap, and speed, ensuring uniform and repeatable high-quality packaging every time.
- Quality Improvement: Automated packaging reduces variability and human error, leading to a 99% consistency rate, significantly improving overall packaging quality and reliability of moisture protection.
4. Material Savings
- Manual Wrapping: Tendency to use excess material to ensure coverage, leading to material waste.
- Coil Packing Machine: Optimized material usage through precise tension control and wrapping programs minimizes waste.
- Material Reduction: Machines can reduce material consumption by 15-30% due to optimized application and reduced over-wrapping.
5. Enhanced Safety
- Manual Handling: Heavy coils and manual wrapping tools pose risks of strains, cuts, and other workplace injuries.
- Automated Machines: Reduce manual handling of coils, minimizing worker exposure to heavy lifting and repetitive motions, enhancing workplace safety.
- Injury Reduction: Studies show a 50-70% reduction in packaging-related injuries in facilities using automated coil packing systems.
By transitioning to automated coil packing machines, businesses not only streamline their operations but also gain a competitive edge through enhanced efficiency, reduced costs, and consistently superior steel coil moisture protection, safeguarding their products and reputation.
Conclusion
Protecting steel coils from moisture is not just about wrapping them up; it’s about implementing a comprehensive strategy that considers material science, packaging techniques, and efficient automation. By understanding the science of corrosion, selecting appropriate barrier materials, mastering effective wrapping methods, and leveraging the power of coil packing machines, you can ensure your steel coils remain pristine, corrosion-free, and ready for use, no matter the storage duration or environmental challenges. Investing in robust moisture protection is an investment in product quality, customer satisfaction, and long-term business success.