Performance anxiety is a common struggle for anyone dealing with mold flipping machines. We all want our machinery to work flawlessly, but without understanding what influences their performance, we’re left guessing. Let’s dive into the key factors that impact the efficiency and outcome of mold flipping.
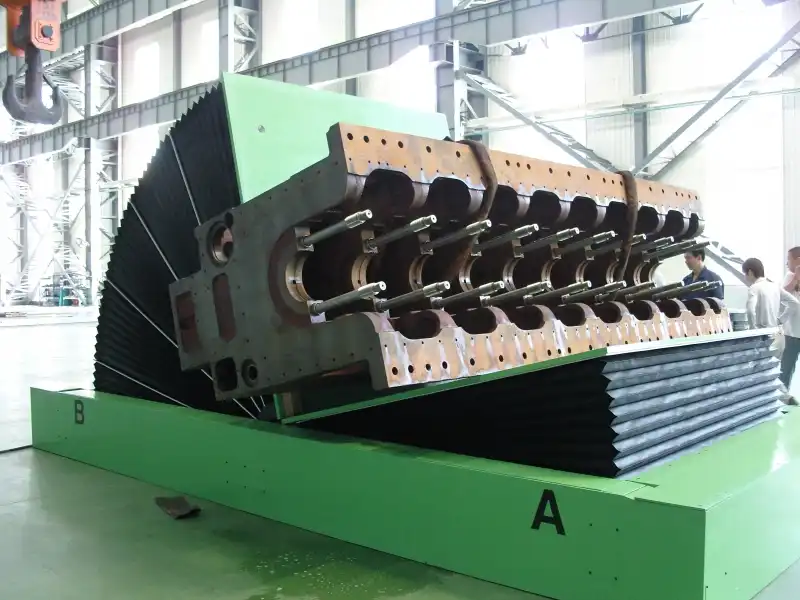
Mold flipping machine performance is determined by multiple factors, including the quality of components, calibration precision, and operating environment. Optimal performance requires regular maintenance and adjustments to ensure efficiency and safety. By understanding these factors, users can enhance mold flipper efficiency, ensuring seamless and effective 180 degree turning.
We’ve all faced those moments where machinery fails us—often at the worst possible time. But it doesn’t have to be that way. By understanding the precise variables affecting mold flipping machine performance, we can pre-empt potential issues and keep our operations running smoothly.
How Does Material Selection Influence Mold Flipping Machine Performance?
Choosing the right materials for your mold flipping machine is like setting the foundation for a successful project. Get it wrong, and you face inefficiencies. Get it right, and everything else falls into place.
Material selection critically influences mold flipping machine performance. The strength, weight, and fatigue resistance of the materials determine the machine’s operational capacity and longevity. Using high-grade alloys or composites can enhance mold flipper efficiency and optimize mechanisms for effective 180 degree turning, ensuring durable and consistent performance in demanding environments.
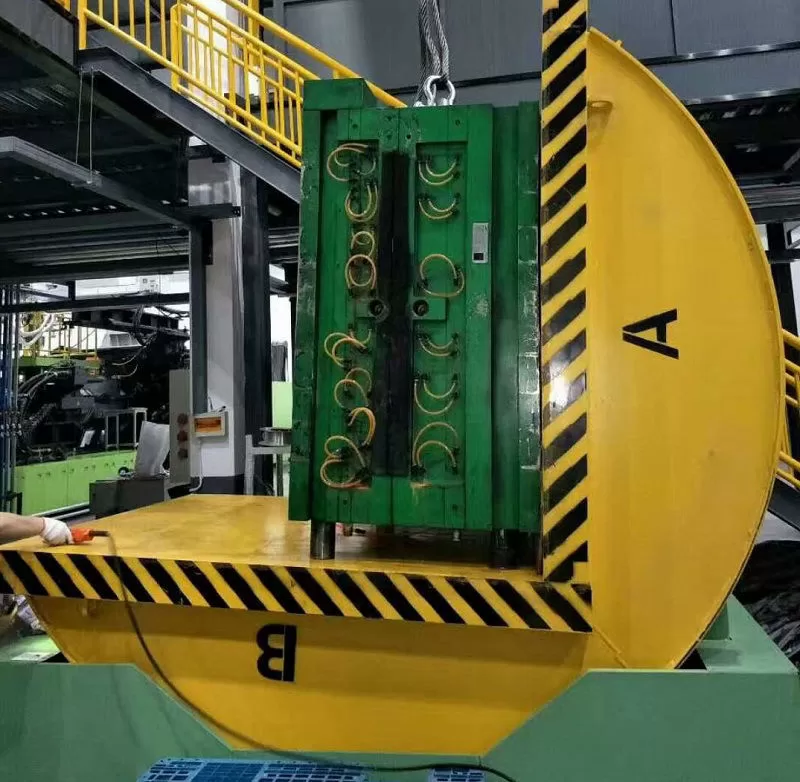
Dive Deeper: Material Impact on Performance
The choice of material used in a mold flipping machine has profound implications on its durability and performance. It’s not just about choosing something strong; it’s about finding a material that meets all the operational demands of mold 180 degree turning. As a seasoned professional who’s seen the evolution of packing and flipping equipment over my four-decade career, I’ve learned that material selection is a science in itself—one often misunderstood by many in the industry.
The fundamental properties such as tensile strength, hardness, and weight come into play when assessing materials. For instance, heavier materials might provide the sturdiness needed but can compromise speed and efficiency. Lighter materials might increase agility but could fall short in durability. Here’s a breakdown of commonly used materials and how they affect mold flipping machine performance:
Material | Pros | Cons |
---|---|---|
Steel Alloys | High strength and durability | Heavier, may reduce speed |
Aluminum | Lightweight and resistant to corrosion | Less strong compared to steel |
Composites | Tailored properties and lightweight | Higher cost and sometimes more brittle |
In the industrial applications I’ve worked in, choosing the right material involves finding a balance. It’s critical to evaluate both the specific requirements of your flipping task and the environmental conditions your machine will face. Industries dealing with heavy loads might favor steel, while those needing high agility might lean toward aluminum or composite materials.
Every decision, from material selection to machine calibration, culminates in a performance that reflects our goals for efficiency and reliability. Remember, the right choice today can save countless hours of downtime and maintenance tomorrow.
This journey into material selection is a testament to the intricacies of engineering and a reminder that sometimes, even the smallest choices can have the most significant impact.
2. What Role Does Machine Design Play in Efficiency?
Packaging industries face a critical challenge: efficiency. Poorly designed machines waste time and money. Mold flipping machines must be designed for peak performance. With 40 years in this industry, I’ve witnessed how smart design makes all the difference. A well-designed machine pays for itself through savings and productivity.
Machine design significantly impacts operational efficiency in mold flipping machines. Factors like stability, ease of maintenance, and energy consumption are crucial in influencing the machine’s efficiency. Designing with these factors in mind ensures faster, safer, and more reliable mold turning, optimizing production and reducing downtime.
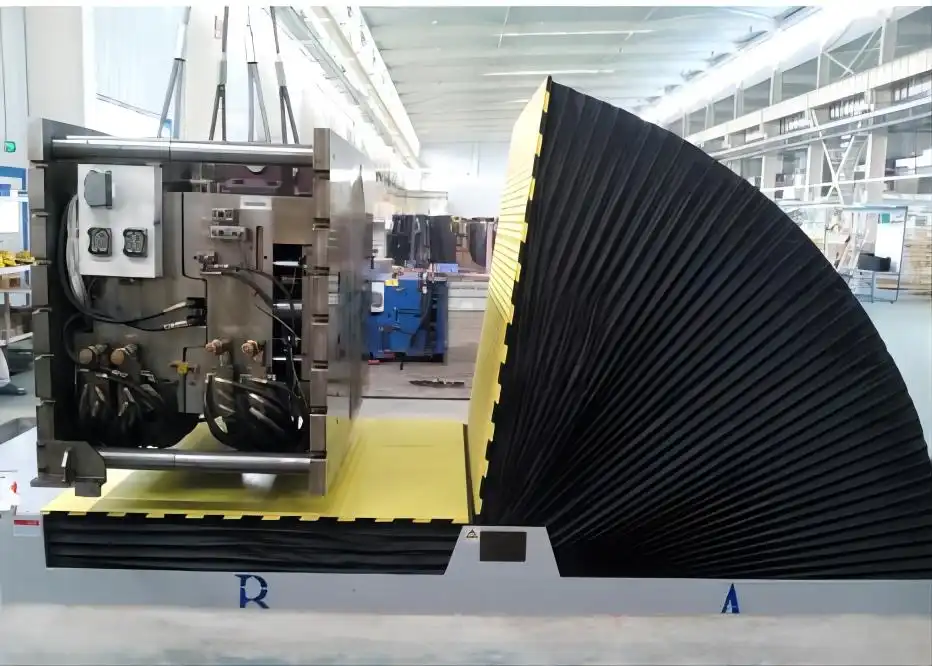
Key Design Elements
Machine design is more than aesthetics; it’s about functionality. Options like automated controls can transform your workflow. Let’s look deeper into the design components that matter.
Design Element | Impact on Efficiency | Real-World Example |
---|---|---|
Stability | Reduces wobble and vibration | Prevents misalignment in 180-degree turns |
Ease of Maintenance | Decreases downtime | Modular components for quick replacements |
Energy Consumption | Lower operational costs | Energy-efficient motors and smart sensors |
Design elements like these aren’t just technical details; they’re practical solutions. For instance, I’ve worked with machines that become unstable due to minor design issues. A small innovation in machine stability can lead to significant gains in production efficiency. Similarly, ease of maintenance cannot be overstressed. Simple-to-replace parts dramatically cut downtime, freeing resources for more productive tasks. By focusing on these core areas, we make machines that are not only efficient but also reliable over the long term.
3. How Do Operational Parameters Affect Performance?
Efficiency isn’t just about the machine; operational parameters play a big role in mold flipping machine performance. I’ve learned that even the best-designed machine can underperform if not operated correctly. Knowing what levers to pull can make or break efficiency.
Operational parameters significantly influence the performance of mold flipping machines. Parameters like speed, load capacity, and cycle time are essential. If optimized, these help in achieving a seamless and consistent mold flipping operation, increasing throughput and minimizing the risk of flaws during the process.
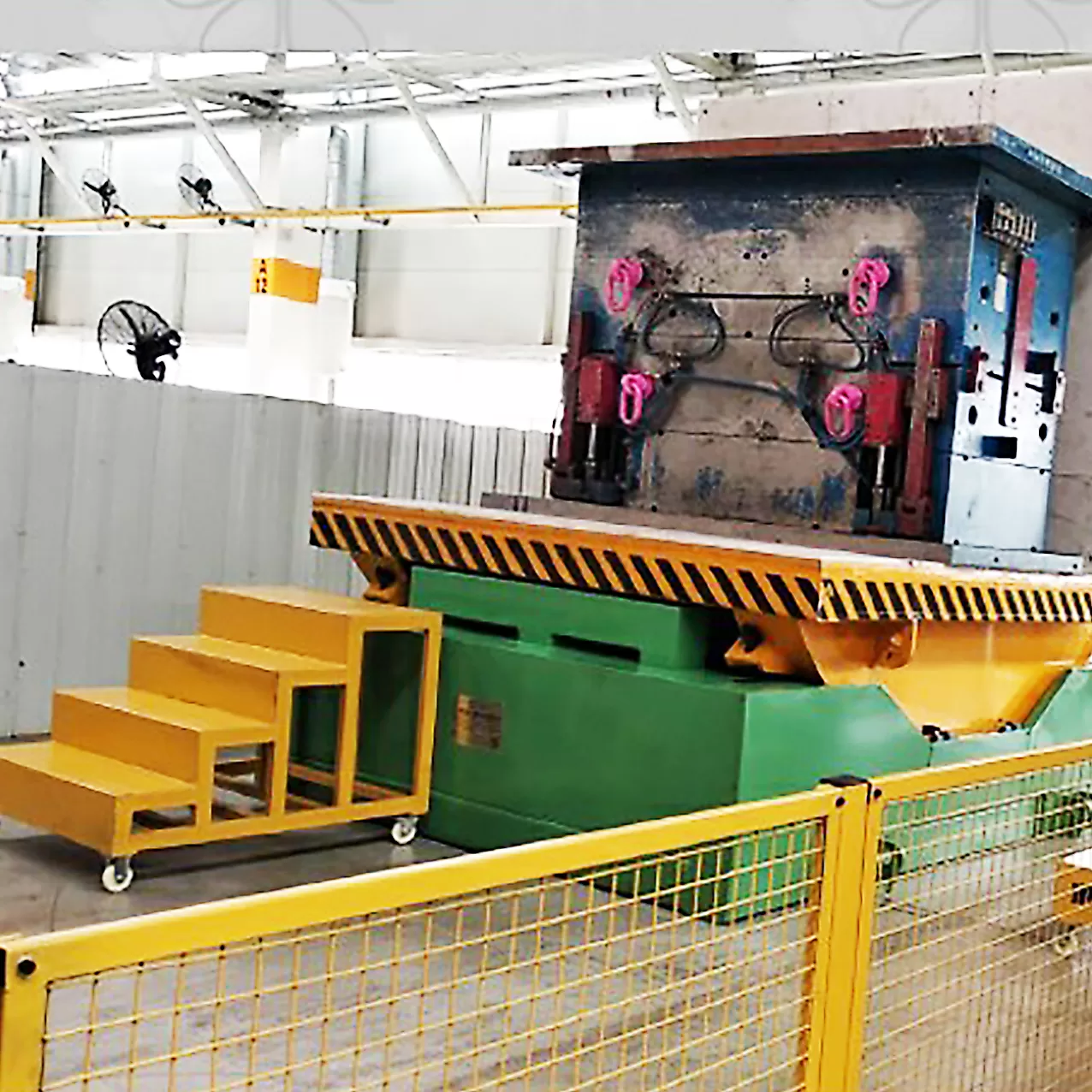
Optimizing Operational Parameters
To understand how to get the best out of your mold flippers, let’s break down the key parameters for efficiency:
Parameter | Impact on Performance | Optimization Tips |
---|---|---|
Speed | Affects cycle time and throughput | Adjust according to mold weight |
Load Capacity | Determines machine’s versatility | Ensure it meets your production needs |
Cycle Time | Impacts overall productivity | Optimize for the shortest safe cycle time |
Speed is not just about getting the job done quickly but also safely. I remember a project where we maximized speed, only to find that ignoring load capacity had serious repercussions. Cycle time is equally crucial; it acts as a bottleneck in mold turning processes. By appropriately adjusting these parameters, businesses see an increase in production rate and a decrease in machine wear and tear. Calibration should balance speed, capacity, and cycle time based on case-specific scenarios, ensuring the efficiency and longevity of mold flipping machines in operation.
Conclusion
In conclusion, the performance of mold flipping machines is significantly affected by material selection, machine design, and operational parameters. By carefully considering these factors, engineers can optimize mold flippers for enhanced efficiency, durability, and overall effectiveness in various industrial applications.