What Are the Common Causes of Steel Wire Coiling Machine Breakdowns?
Steel wire coiling machines are vital for numerous industries, ensuring efficient cable handling. However, breakdowns can occur, leading to costly downtime. Understanding the common causes is crucial for maintaining smooth operations and maximizing the lifespan of these machines. Proactive measures can prevent these issues.
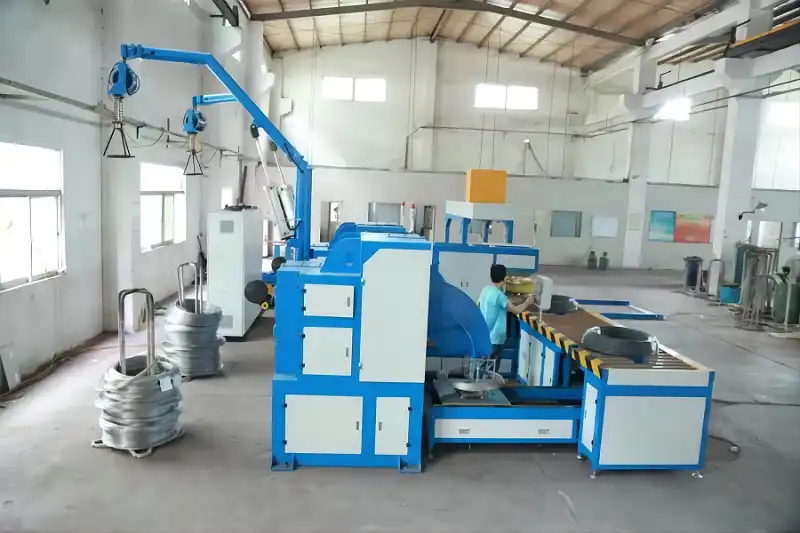
Steel wire coiling machine breakdowns often stem from issues like lubrication failure, wear and tear on critical parts, electrical faults, and improper tension control. Addressing these potential problems through regular maintenance and proactive troubleshooting can significantly reduce downtime and improve machine reliability.
Let’s dive into the typical culprits behind steel wire coiling machine failures. Knowing these issues can help you keep your machinery running smoothly and efficiently, extending its life.
1. Inadequate Lubrication and Fluid Maintenance
Proper lubrication is paramount to the smooth operation of steel wire coiling machines. Reduced friction preserves mechanical parts and protects the quality of the wound cable. Neglecting this essential task can lead to significant problems.
Inadequate lubrication is a primary cause of steel wire coiling machine breakdowns. Without proper lubrication, friction increases, leading to accelerated wear and tear on critical components like bearings, gears, and drive shafts. This results in overheating, increased energy consumption, and ultimately, machine failure.

The Critical Role of Lubrication in Preventing Breakdowns
Why is lubrication so crucial, and what specific challenges arise from neglecting it? Let’s break down the problem and explore effective solutions.
Types of Lubricants and Their Applications
Different parts of a steel wire coiling machine require specific lubricants. Using the wrong type can be as detrimental as using none at all. Here’s a quick guide:
- Bearings and Gears: High-quality grease is typically required to handle heavy loads and reduce friction.
- Tension Systems: Lightweight oils are often necessary for smooth operation and precise control.
- Hydraulic/Pneumatic Systems: Specialized hydraulic fluids are essential for maintaining pressure and preventing leaks.
Establishing a Lubrication Schedule
Over-lubrication can attract debris, leading to sticky residues, while under-lubrication causes accelerated wear. A balanced schedule is key.
Component | Lubricant Type | Frequency | Notes |
---|---|---|---|
Bearings | Grease | Weekly/Bi-Weekly | High-speed machines may require more frequent checks |
Gears | Grease | Weekly/Bi-Weekly | Inspect for wear and contamination |
Drive Shafts | Grease | Weekly/Bi-Weekly | Ensure proper application to prevent slippage |
Tension Systems | Lightweight Oil | Weekly | Monitor for leaks and maintain appropriate levels |
Hydraulic Systems | Hydraulic Fluid | Monthly | Check fluid levels, inspect seals, and identify leaks |
Pneumatic Systems | Pneumatic Oil | Monthly | Monitor pressure and check for leaks |
Recognizing the Symptoms of Lubrication Problems
Early detection of lubrication issues can prevent catastrophic failures. Here are some telltale signs:
- Unusual Noises: Screeching, grinding, or rattling sounds often indicate insufficient lubrication.
- Overheating: Components running hotter than usual can be a sign of increased friction due to lack of lubrication.
- Visible Wear: Inspect parts for excessive wear, scoring, or discoloration.
- Decreased Performance: Reduced speed, inconsistent tension, or jerky movements can indicate lubrication problems.
By understanding the importance of proper lubrication, establishing a consistent schedule, and recognizing the early warning signs, you can significantly reduce the risk of steel wire coiling machine breakdowns and extend the lifespan of your equipment.
2. Electrical Failures and Control System Issues
Electrical problems and control system malfunctions can halt production. Understanding the causes and implementing preventive measures are essential for maintaining reliable operation.
Electrical failures in steel wire coiling machines can arise from loose connections, damaged wiring, or faulty sensors. These issues can lead to erratic machine behavior, complete shutdowns, or even safety hazards. Regular inspection and maintenance of electrical components are crucial for preventing these breakdowns.
Delving into Electrical System Vulnerabilities
Let’s examine the common causes of electrical system failures and explore effective troubleshooting strategies.
Identifying Common Electrical Faults
Electrical faults in steel wire coiling machines can manifest in various ways. Here are some of the most common:
- Loose Connections: Vibration and movement can cause connections to loosen over time, leading to intermittent or complete circuit failures.
- Damaged Wiring: Abrasion, heat, or chemical exposure can damage wiring insulation, causing short circuits or open circuits.
- Faulty Sensors: Sensors are critical for monitoring machine parameters like tension and speed. Failure can result in incorrect data and improper machine operation.
- Control System Malfunctions: Software glitches, hardware failures, or communication errors can disrupt the machine’s control system, leading to unpredictable behavior.
Implementing Preventive Measures
Preventive maintenance is crucial for minimizing the risk of electrical failures. Consider the following:
- Regular Inspections: Conduct routine visual inspections of wiring, connections, and control panels.
- Tightening Connections: Periodically tighten all electrical connections to ensure secure contact.
- Replacing Worn Components: Replace any damaged or worn wiring, sensors, or other electrical components.
- Software Updates: Keep the machine’s control software up to date to address bugs and improve performance.
Troubleshooting Electrical Problems
When electrical problems arise, a systematic approach is essential for efficient troubleshooting:
- Isolate the Problem: Identify the specific component or system that is malfunctioning.
- Check Power Supply: Verify that the machine is receiving adequate power.
- Inspect Wiring and Connections: Look for loose connections, damaged wiring, or signs of corrosion.
- Test Sensors: Use a multimeter or other testing equipment to check the functionality of sensors.
- Consult the Manual: Refer to the machine’s manual for troubleshooting guidance and wiring diagrams.
By addressing potential electrical issues proactively and implementing effective troubleshooting strategies, you can minimize downtime and maintain the reliable operation of your steel wire coiling machine.
3. Mechanical Wear and Tear
Mechanical components inevitably wear down over time. Recognizing and addressing this wear is essential for preventing breakdowns and maintaining optimal performance of wire coiling machines.
Mechanical wear and tear is a common cause of steel wire coiling machine breakdowns. Continuous operation leads to the degradation of critical components like rollers, guides, and gears. Regular inspection, timely replacement of worn parts, and proper alignment are essential for preventing these issues.
Strategies for Combating Mechanical Degradation
What are the most vulnerable components, and how can you proactively manage their wear to prevent unexpected failures?
Identifying High-Wear Components
Certain components are more susceptible to wear and tear due to their constant use and exposure to friction. These include:
- Rollers: These components guide the wire through the machine and are subject to constant abrasion.
- Guides: Similar to rollers, guides experience wear as they direct the wire.
- Gears: Gears transmit power and are prone to wear due to friction and load.
- Bearings: Bearings support rotating components and can fail due to contamination or lack of lubrication.
- Cutting Tools: These tools are used to cut the coiled wire and require periodical sharping or replacing.
Implementing a Preventive Replacement Program
A proactive approach to replacing worn parts can significantly reduce the risk of breakdowns. Consider the following:
- Establish Replacement Intervals: Based on manufacturer recommendations and historical data, establish replacement intervals for high-wear components.
- Maintain a Spare Parts Inventory: Keep a stock of critical spare parts readily available to minimize downtime.
- Track Component Lifespan: Monitor the lifespan of components to refine replacement intervals and identify potential issues.
Addressing Misalignment Issues
Misalignment can accelerate wear and tear on mechanical components. Here’s what to do:
- Regular Alignment Checks: Periodically check the alignment of rollers, guides, and other critical components.
- Proper Adjustment: Make necessary adjustments to ensure proper alignment.
- Vibration Analysis: Use vibration analysis to detect misalignment issues early.
Examples of Wear and Tear
Here are a few examples of machine part failure due to wear and tear:
Component | Failure symptoms | Action Required |
---|---|---|
Rollers | Uneven coiling, surface defects on wire | Replace worn rollers, adjust alignment |
Guides | Wire slippage, inconsistent tension | Replace worn guides, check alignment |
Gears | Unusual noises, jerky movements | Replace worn gears, ensure proper lubrication |
Bearings | Overheating, excessive vibration | Replace worn bearings, check lubrication |
Cutting Tools | Incomplete wire cutting, rough cutting edges | Resharpen cutting tools, or replace with new one. |
By understanding the mechanisms of mechanical wear and tear, implementing a proactive replacement program, and addressing misalignment issues, you can significantly extend the lifespan of your steel wire coiling machine.
4. Improper Tension Control
Improper tension control leads to inconsistent coiling, cable stretching, or kinking. Accurate tension ensures quality and prevents production halts. Regular calibration is vital for preventing breakdowns.
Maintaining consistent tension is key to high-quality coiling, especially in high-speed machines. Regular checks using gauges or load cells are essential. Calibration should start with the machine idle, adjusting components incrementally. Documenting results helps track changes over time. This ensures minimal defects and smooth operations.
Conclusion
Maximizing the lifespan of your steel wire coiling machine hinges on understanding its mechanics and conducting meticulous maintenance. Regular inspections, proper lubrication, and calibration are crucial. Training personnel thoroughly and keeping accurate service records are also essential. A proactive approach ensures years of dependable service, safeguarding product integrity and profits.