Are you concerned about the environmental impact of packaging? Steel packaging, known for its strength and recyclability, is stepping into a new era of sustainability. Imagine packaging that not only protects your products but also significantly reduces energy consumption. Steel is already a highly recycled material, but what if innovations could make its production and use even more energy-efficient, further minimizing its carbon footprint and boosting its green credentials?
Steel packaging is embracing energy-saving innovations to minimize its environmental impact. From optimizing production processes to utilizing recycled content and lightweighting designs, the steel packaging industry is actively reducing energy consumption and carbon emissions. These advancements enhance sustainability, making steel an even more compelling choice for eco-conscious businesses and consumers seeking environmentally responsible packaging solutions.
This article dives into the cutting-edge energy-saving innovations transforming steel packaging, exploring how these advancements contribute to a greener future and a more sustainable supply chain. Read on to discover how steel packaging is evolving to meet the demands of an environmentally conscious world.
Recycled Steel Revolution: The Cornerstone of Energy Efficiency
Worried about resource depletion? The steel industry has a powerful answer: recycling. Steel is unique in its ability to be recycled endlessly without losing quality. Imagine a packaging material that keeps coming back, reducing the need for virgin resources and slashing energy consumption. Recycled steel is not just a trend; it’s a fundamental shift towards a circular economy in packaging.
Recycled steel dramatically reduces energy consumption in packaging production. Producing steel from recycled scrap requires approximately 75% less energy compared to creating it from virgin raw materials. This significant energy saving translates directly into lower carbon emissions and a reduced environmental footprint for steel packaging, making it a highly sustainable choice.
This section explores the transformative role of recycled steel in revolutionizing the energy efficiency of steel packaging.
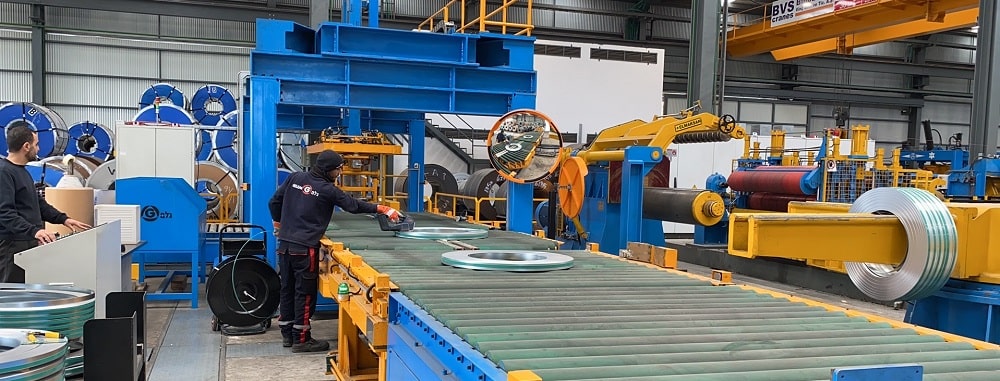
Unpacking the Energy Savings: Virgin vs. Recycled Steel Production
The energy intensity difference between virgin and recycled steel production is staggering. Understanding these differences is crucial to appreciating the environmental benefits of recycled steel. Let’s break down the processes and compare the energy consumption:
Virgin Steel Production: A Resource-Intensive Path
Virgin steel production, primarily through the Basic Oxygen Furnace (BOF) or Blast Furnace-Basic Oxygen Furnace (BF-BOF) route, is a complex and energy-demanding process. It starts with mining iron ore, a resource-intensive activity. This ore is then processed and fed into blast furnaces, which operate at extremely high temperatures, typically exceeding 1500°C (2732°F). These furnaces require vast amounts of energy, primarily from burning fossil fuels like coal, to convert iron ore into molten iron. Further refining in BOFs and subsequent processing steps add to the overall energy consumption.
Recycled Steel Production: An Energy-Efficient Alternative
In stark contrast, recycled steel production, primarily via the Electric Arc Furnace (EAF) route, is significantly less energy-intensive. EAFs utilize electricity to melt steel scrap. Since the scrap is already refined steel, the process bypasses the energy-intensive ore reduction stage of virgin steel production. The melting point of steel is around 1370°C (2500°F), and while EAFs still require substantial electrical energy, the overall energy input is dramatically lower compared to blast furnaces. Furthermore, the EAF route can utilize renewable energy sources for electricity, further reducing its carbon footprint.
Data-Driven Comparison: Energy Consumption per Tonne
To quantify the energy savings, let’s look at typical energy consumption figures for both production routes:
Production Route | Energy Consumption (GJ/tonne) | Energy Consumption (kWh/tonne) |
---|---|---|
Virgin Steel (BF-BOF) | 20 – 25 | 5556 – 6944 |
Recycled Steel (EAF) | 5 – 8 | 1389 – 2222 |
Energy Savings (EAF) | 75% (Average) | 75% (Average) |
Note: GJ = Gigajoules, kWh = Kilowatt-hours. These figures are approximate and can vary based on specific technologies and operational efficiencies.
The table clearly illustrates the remarkable energy savings achieved through recycled steel production. On average, producing steel via the EAF route consumes only 25% of the energy required for the BF-BOF route. This translates to a significant reduction in greenhouse gas emissions and a much smaller environmental impact. The steel packaging industry’s increasing reliance on recycled steel is a major driver in its journey towards sustainability.
Lightweighting Strategies: Doing More with Less Steel
Want to reduce material usage without compromising strength? Lightweighting is the answer. Imagine steel packaging that is just as robust but uses less material, saving energy in production and transportation. Advanced engineering and material science are making this a reality, proving that less can indeed be more when it comes to sustainable steel packaging.
Lightweighting steel packaging designs is a crucial energy-saving innovation. By reducing the amount of steel required for each package, manufacturers lower material consumption, decrease production energy, and reduce transportation weight. This approach maintains packaging strength and product protection while significantly minimizing the overall environmental footprint.
This section explores how innovative lightweighting strategies are minimizing material usage and maximizing energy efficiency in steel packaging.
Engineering Efficiency: Advanced Design and Material Optimization
Lightweighting in steel packaging is achieved through a combination of advanced design principles and optimized material utilization. It’s not just about using less steel; it’s about using steel smarter. Here’s how:
High-Strength Steel Grades: Strength Without the Bulk
The development and application of High-Strength Steel (HSS) grades are fundamental to lightweighting. HSS offers significantly higher yield strength and tensile strength compared to conventional steel grades. This means that less material is needed to achieve the same structural integrity and performance. By switching to HSS, packaging manufacturers can reduce the gauge (thickness) of steel used without compromising the package’s ability to protect the contents. This directly translates to material savings and weight reduction.
Advanced Forming Techniques: Precision and Material Savings
Advanced forming techniques play a vital role in lightweighting. Processes like deep drawing, hydroforming, and precision stamping allow for the creation of complex shapes and intricate designs using thinner gauges of steel. These techniques minimize material waste during manufacturing and enable the production of packaging with optimized structural performance. For example, deep drawing allows for the creation of seamless cans and containers with reduced wall thickness, while hydroforming can produce lightweight, yet strong, structural components for steel drums and pails.
Finite Element Analysis (FEA): Design Optimization Through Simulation
Finite Element Analysis (FEA) is a powerful computational tool used to optimize packaging designs for lightweighting. FEA software allows engineers to simulate the structural performance of different packaging designs under various stress and load conditions. By using FEA, designers can identify areas where material can be removed without compromising structural integrity. This iterative design process, guided by simulation, leads to highly optimized and lightweight packaging solutions. FEA ensures that lightweighting is achieved not at the expense of product protection but through intelligent design and material placement.
Material Optimization: Tailoring Steel to Function
Material optimization goes hand-in-hand with design optimization. It involves selecting the most appropriate steel grade and thickness for each specific packaging application. For example, thinner gauge steel might be suitable for lightweight cans and containers, while thicker, high-strength steel might be necessary for industrial drums or transport packaging. By carefully tailoring the material selection to the functional requirements of the packaging, manufacturers can avoid over-engineering and minimize material usage. This targeted approach to material optimization ensures that steel is used efficiently and effectively, contributing to lightweighting and resource conservation.
Energy-Efficient Manufacturing: Greener Processes from the Factory Floor
Looking for production methods that save energy? Energy-efficient manufacturing processes are transforming steel packaging production. Imagine factories that use less energy, reduce waste, and minimize emissions, all while producing high-quality steel packaging. From optimized heating to smart automation, innovations on the factory floor are driving a new era of sustainable steel packaging manufacturing.
Energy-efficient manufacturing processes are critical for reducing the carbon footprint of steel packaging. Innovations in heating technologies, automation, and waste heat recovery are minimizing energy consumption throughout the production cycle. These advancements not only lower environmental impact but also enhance operational efficiency and reduce manufacturing costs.
This section delves into the energy-saving technologies and practices being implemented in steel packaging manufacturing facilities.
Cutting-Edge Technologies: Minimizing Energy Consumption in Steel Packaging Production
The steel packaging manufacturing sector is actively adopting and developing technologies aimed at significantly reducing energy consumption. These innovations span various stages of the production process, from material processing to forming and finishing. Here’s a closer look at some key technologies driving energy efficiency:
Induction Heating: Precision and Efficiency in Heating Processes
Traditional heating methods in steel manufacturing, such as gas furnaces, can be energy-intensive and less precisely controlled. Induction heating offers a significantly more energy-efficient alternative. Induction heating uses electromagnetic fields to generate heat directly within the steel material. This targeted heating method minimizes energy waste by heating only the necessary areas and reducing heat loss to the surrounding environment. Induction heating is faster, more precise, and more energy-efficient than conventional heating methods, leading to substantial energy savings in processes like preheating for forming and heat treatment.
Automation and Smart Manufacturing: Optimizing Energy Use Across Production Lines
Automation and smart manufacturing technologies are revolutionizing energy management in steel packaging plants. Automated systems can optimize production processes for maximum energy efficiency. Smart sensors and control systems monitor energy consumption in real-time, allowing for adjustments to minimize waste and optimize energy use. For example, automated systems can adjust furnace temperatures based on production volume, optimize machine speeds, and schedule operations to reduce peak energy demand. Predictive maintenance, enabled by smart technologies, also helps prevent equipment failures that can lead to energy inefficiencies and production downtime.
Waste Heat Recovery Systems: Turning Waste into Resource
Significant amounts of heat are generated during steel packaging manufacturing processes, particularly in furnaces and forming operations. Traditional manufacturing facilities often lose this heat to the environment. Waste Heat Recovery (WHR) systems capture and reuse this wasted thermal energy, significantly improving overall energy efficiency. WHR technologies, such as heat exchangers and heat pumps, can convert waste heat into useful energy for other processes within the plant, such as preheating materials, generating steam, or even for heating or cooling plant buildings. Implementing WHR systems reduces the overall energy demand of the manufacturing facility and lowers its carbon footprint.
Continuous Annealing Lines: Streamlining and Energy Reduction in Heat Treatment
Annealing, a heat treatment process used to improve the ductility and reduce the hardness of steel, is traditionally energy-intensive. Continuous Annealing Lines (CALs) offer a more energy-efficient approach compared to batch annealing. In CALs, steel strips move continuously through different heating and cooling zones, optimizing the heat treatment process and reducing cycle times. CAL technology allows for precise temperature control and faster processing, resulting in significant energy savings compared to traditional batch annealing furnaces. CALs also improve material quality and consistency, further enhancing production efficiency and reducing material waste.
Technology | Energy Saving Mechanism | Impact on Sustainability |
---|---|---|
Induction Heating | Targeted heating, reduced heat loss | Lower energy consumption, reduced greenhouse gas emissions |
Automation & Smart Mfg. | Optimized processes, real-time energy management | Minimized energy waste, improved operational efficiency |
Waste Heat Recovery | Reusing waste heat for other processes | Reduced overall energy demand, lower carbon footprint |
Continuous Annealing Lines | Streamlined heat treatment, faster processing, precise control | Energy savings in annealing, improved material quality and consistency |
Life Cycle Thinking: Assessing Steel Packaging from Cradle to Grave
Considering the entire journey of packaging is crucial for true sustainability. Imagine evaluating steel packaging not just from production but from raw material extraction to end-of-life management. Life Cycle Assessment provides a comprehensive view, revealing energy-saving opportunities across the entire value chain and ensuring that steel packaging’s environmental benefits are fully realized.
Life Cycle Assessment (LCA) is essential for holistically evaluating the sustainability of steel packaging. By analyzing the environmental impacts from raw material extraction to end-of-life disposal or recycling, LCA identifies energy consumption hotspots and opportunities for improvement across the entire packaging life cycle. This comprehensive approach ensures that sustainability efforts are targeted and effective.
Life Cycle Assessment (LCA) is a rigorous methodology used to evaluate the environmental impacts of a product, process, or service throughout its entire life cycle – often described as “cradle-to-grave.” For steel packaging, LCA provides a comprehensive understanding of its environmental footprint, encompassing all stages from raw material extraction to manufacturing, transportation, use, and end-of-life management. This holistic approach is crucial for identifying energy-saving opportunities and ensuring that sustainability claims are based on a complete and accurate assessment.
Key Stages in LCA of Steel Packaging:
- Raw Material Extraction and Processing: This stage includes the mining of iron ore and other raw materials, their transportation to processing facilities, and the energy-intensive processes of converting ore into steel. Energy consumption and emissions from mining equipment, transportation, and initial steel production are significant factors in this stage.
- Packaging Manufacturing: This stage covers the energy used in manufacturing steel packaging products, such as cans, drums, or containers. It includes processes like steel forming, welding, coating, and printing. Energy consumption in manufacturing facilities and emissions from these processes are assessed.
- Filling and Packaging: While not strictly steel packaging production, the filling process at the food or product manufacturer’s facility is often included in the LCA, especially for food packaging. This stage accounts for the energy used in filling the steel containers with products.
- Distribution and Transportation: This stage evaluates the energy consumed and emissions generated during the transportation of empty packaging to filling facilities and then filled packaging to retail locations and consumers. Transportation modes, distances, and fuel efficiency are key factors.
- Consumer Use: For steel packaging, the consumer use stage typically has minimal direct environmental impact, as steel packaging is generally inert and requires no special handling during use.
- End-of-Life Management: This stage assesses the environmental impacts of disposal or recycling of steel packaging after its intended use. Recycling steel is a significant energy saver compared to landfill disposal. The efficiency of collection, sorting, and recycling processes is evaluated.
Benefits of LCA for Steel Packaging Sustainability:
- Hotspot Identification: LCA pinpoints the stages in the steel packaging life cycle with the highest environmental impact, allowing manufacturers to focus improvement efforts where they will be most effective. For example, LCA might reveal that raw material extraction or transportation are major energy consumption hotspots.
- Informed Decision-Making: LCA provides data-driven insights for making informed decisions about material selection, design choices, and process improvements. It helps compare different packaging options and identify the most sustainable solutions.
- Performance Benchmarking: LCA allows companies to benchmark the environmental performance of their steel packaging against industry averages or competing materials. This helps track progress over time and identify areas for further reduction in environmental impact.
- Credible Communication: LCA provides a scientifically robust basis for communicating the sustainability benefits of steel packaging to consumers and stakeholders. LCA-backed claims are more credible and transparent, enhancing brand reputation and building trust.
Challenges and Considerations in LCA:
- Data Availability and Quality: Accurate and comprehensive data are crucial for a reliable LCA. Obtaining detailed data for all life cycle stages, especially for upstream processes like raw material extraction, can be challenging.
- System Boundary Definition: Defining the system boundaries for LCA is critical. Decisions about what to include and exclude in the assessment can significantly influence the results. Clear and consistent boundary definitions are necessary for comparability.
- Allocation Methods: In cases where processes produce multiple outputs (e.g., co-products in steel manufacturing), allocation methods are needed to distribute environmental impacts appropriately. Different allocation methods can lead to varying results.
- Interpretation and Improvement Strategies: LCA results need to be carefully interpreted to identify meaningful improvement strategies. LCA is a decision-support tool, and its findings should guide practical actions to enhance sustainability.
By embracing Life Cycle Assessment, the steel packaging industry can move beyond simply promoting recyclability and actively pursue energy-saving innovations across the entire value chain, ensuring a truly sustainable future for steel packaging.
Conclusion
Steel packaging is not standing still; it’s evolving. Through recycled steel, lightweighting, energy-efficient manufacturing, and life cycle thinking, the industry is making significant strides in sustainability. These energy-saving innovations are not just good for the environment; they are smart business moves, enhancing efficiency, reducing costs, and meeting the growing demand for green solutions. As wire packing automation and similar technologies advance, the future of sustainable steel packaging looks brighter than ever.