Steel Wire Coil Packing Line Solutions and Price Analytics
Executive Summary
Efficient steel wire coil packing lines are indispensable in the contemporary metals industry, profoundly influencing product integrity, operational efficiency, and overall profitability. These systems, ranging from semi-automated components to fully integrated, robotic lines, are critical for protecting steel wire coils during transit and storage. The primary cost drivers for these lines include the level of automation, handling capacity, and the degree of customization required to meet specific operational needs. A comprehensive financial assessment necessitates looking beyond the initial capital outlay to consider the Total Cost of Ownership (TCO), which includes ongoing operational and maintenance expenses, and the Return on Investment (ROI), which quantifies the financial benefits derived from enhanced efficiency, reduced damage, and labor savings. Key market trends indicate a significant push towards greater automation, the integration of smart features such as the Internet of Things (IoT) and Artificial Intelligence (AI) for process optimization and predictive maintenance, and an increasing emphasis on sustainable packaging materials and practices. This report provides a detailed analysis of steel wire coil packing line solutions, covering technological aspects, price analytics, market dynamics, and offers strategic considerations for stakeholders contemplating investments in this critical area of operations.
I. Introduction to Steel Wire Coil Packing Lines

Definition, Purpose, and Importance
A steel wire coil packing line is an integrated system of machinery and processes dedicated to the automated or semi-automated packaging of metal coils, primarily steel wire, but also applicable to materials such as aluminum and copper coils.1 The fundamental purpose of such a line is to provide robust protection to the coils against a variety of detrimental factors. These include environmental damage such as rust, moisture, and dust accumulation, as well as physical damage that can occur during handling, storage, and transportation.1 By ensuring the coils reach their destination in optimal condition, these packing lines play a direct role in maintaining product integrity and preserving aesthetic appeal, which are crucial for customer satisfaction.1
The importance of steel wire coil packing lines extends beyond mere product protection. They are pivotal in enhancing overall storage efficiency within a facility and bolstering transportation safety. As key components of modern factory intelligent logistics systems, particularly in the steel, metallurgy, and metal processing sectors, these lines contribute significantly to streamlined logistical performance.1 The efficiency and reliability of the packing line directly impact the flow of materials, the utilization of storage space, and the safety of personnel and products throughout the supply chain.
Challenges Addressed
Steel wire coil packing lines are engineered to address a multitude of challenges inherent in the handling and distribution of metal coils:
- Product Protection: A primary challenge is safeguarding coils from corrosion, water spots, and physical damage like scratches and deformation, which can occur during the often-rigorous journey through storage and transit.2 This is especially critical for high-value or sensitive products, such as cold-rolled, pickled, oiled, or galvanized coils, where surface quality is paramount.3
- Handling Efficiency: The manual handling of steel coils, which are typically heavy, bulky, and potentially unwieldy, is a significant operational challenge. It is labor-intensive, time-consuming, and inherently inefficient, often leading to bottlenecks in production flow.4 Automated packing lines mitigate these issues by mechanizing or fully automating these handling processes.
- Safety: Manual handling of heavy coils presents substantial safety risks to personnel, including musculoskeletal injuries and accidents.4 Automated packing lines drastically reduce these risks by minimizing direct human interaction with the coils during the packing stages.
- Cost Reduction: The implementation of efficient packing lines contributes to cost reduction on multiple fronts. It curtails labor costs associated with manual packing, diminishes financial losses from product damage claims, and optimizes the consumption of packaging materials through precise application.4
- Consistency: Achieving uniform packaging quality is a difficult task when relying on manual methods, which are prone to variability. Automated lines ensure that each coil is packaged to the same standard, enhancing predictability and reliability.3
- Throughput: Modern steel production facilities, especially those with high-speed processing lines like slitters, require packing solutions that can keep pace without creating downstream bottlenecks. Efficient packing lines are essential for maintaining overall plant throughput.4
The strategic value of a steel wire coil packing line extends considerably beyond its immediate protective function. While safeguarding the product is a primary objective, these lines are integral to the overall efficiency and productivity of a manufacturing or processing plant. An inefficient packing system can become a significant bottleneck, impeding the output of upstream processes, such as slitting or rolling, and causing delays in downstream activities like warehousing and shipping.1 For instance, a slitting line may sit idle if the subsequent banding and removal of coils cannot keep pace with its output.4 This underscores that the packing line is not merely an ancillary cost center but a critical node in the plant’s material flow and value chain. The design, level of automation, and integration capabilities of the packing line directly influence the efficiency of these interconnected processes. Therefore, when evaluating an investment in a packing line, decision-makers should adopt a holistic perspective. The assessment should encompass not only the direct costs and protective benefits of the line itself but also its potential to optimize material flow, enhance overall plant throughput, and integrate seamlessly with existing and future production systems. This broader viewpoint can reveal additional, often substantial, drivers of return on investment that might be overlooked if the packing line is considered in isolation.
II. Core Processes and Technologies in Steel Wire Coil Packing

A typical automated or semi-automated steel wire coil packing line involves a sequence of distinct operations, each employing specific technologies and equipment to prepare the steel wire coils for storage and shipment. The seamless execution and integration of these stages are paramount for achieving efficiency, product protection, and cost-effectiveness.
A. Coil Reception and Handling
The initial stage of any coil packing line involves receiving coils from upstream manufacturing or processing units, such as slitters or rolling mills, and preparing them for the subsequent packaging steps. This phase often includes the critical task of reorienting the coil.
Key equipment in this stage includes:
- Coil Cars: These are specialized vehicles used to transport coils to the entry point of the packing line. They often collect coils from the recoiler of a processing line or from a turnstile that acts as a buffer.4
- Turnstiles: These are rotary devices, typically with multiple arms, designed to receive and temporarily store several slit coils. They act as an interface and buffer between the upstream process (e.g., slitting line) and the packing line, feeding coils individually into the packaging process. Coils can be loaded onto or removed from turnstiles using C-hooks, coil cars, or downenders.4
- Upenders/Downenders (Tilters): These machines are crucial for changing the orientation of the coil. For instance, a coil might arrive with its central axis vertical ("eye-to-sky") and need to be tilted so its axis is horizontal ("eye-to-horizontal") for wrapping or other packaging processes, or vice-versa for specific shipping or storage requirements.4 Companies like ADS Machinery offer upenders and downenders that utilize either hydraulic or mechanical systems for this purpose.5 Bushman AvonTec, for example, provides Pick & Place downenders designed to enhance productivity and minimize coil damage, as well as fixed position downenders suitable for heavy gauge coils, where a pusher arm on the turnstile assists in moving the coil onto the downender.6
- Conveying Systems: A variety of conveying systems are employed to transport coils smoothly and efficiently between the different stages of the packing line. The choice of conveyor depends on factors like coil weight, size, the required path, and the level of automation.
- Roller Conveyors: These are commonly used for moving palletized loads or items with a flat bottom. In the context of coil packing, they might be used for transporting coils on pallets or specialized carriers.7 AMOVA, for instance, offers pallet conveying systems specifically designed for hot-rolled coils.8
- Chain Conveyors: Suitable for handling heavy loads, chain conveyors can be configured to follow specific paths within the packing line.7 Sund Birsta lists chain conveyors as an option for their unloading stations.9
- Walking Beam Conveyors: These conveyors provide intermittent, linear transfer of heavy items like steel coils. They are often used for controlled movement through processing, cooling, or accumulation stages within a line.9 Brilex is a provider of walking beam coil transfer systems10, and Sund Birsta also includes walking beams as an unloading option.9 Ingeniería TPI mentions the use of walking beams in conjunction with their COILFORM equipment designed to prevent telescopicity in coils.11
- Shuttle Cars: These are used for transferring coils, particularly in scenarios where minimal sorting is required, serving as an alternative to more complex sortation tables.6
- Automated Guided Vehicles (AGVs): AGVs offer a flexible and automated solution for transporting coils between various points within a facility, including to and from the packing line.6
B. Coil Compacting
For many types of wire rod coils, a compacting stage is essential. This process involves applying pressure to the coil to reduce its overall volume, creating a denser and more stable package. Proper compaction is crucial for effective strapping, handling, and preventing issues like ring damage or coil collapse during subsequent operations and transit.9
- Mechanisms:
- Hydraulic Compactors: These machines use hydraulic systems to generate the high forces required for compaction. Hydraulic power allows for precise control over the applied pressure, which can be beneficial for various coil types and densities.12 The use of hydraulic fluid also means that attention must be paid to potential heat generation and fluid maintenance.13
- Mechanical Compactors: These typically utilize a flywheel and mechanical linkages (e.g., crankshafts, cams) to achieve compaction.12 Mechanical presses can offer faster cycle times and may be preferred for high-volume, repetitive tasks.12 While Signode’s Wire Rod Compactor is a notable example in this category, the specific internal mechanism (hydraulic or mechanical) is not always detailed in general product literature.14 Primetals Technologies offers both horizontal and vertical compactors with advanced mechatronic solutions for automation, though the fundamental drive mechanism isn’t explicitly stated as exclusively hydraulic or mechanical in the provided information.15 Sund Birsta’s PCH Alfa compactor, for instance, features an efficient pump control system, which often implies a hydraulic mechanism.9
- Types:
- Horizontal Compactors: These units are commonly interfaced with horizontal hook carrier systems. The coil is oriented with its eye horizontal and is compacted along its axis.15
- Vertical Compactors: These compactors operate with the coil typically positioned on a vertical stem pallet ("eye-to-sky"). The compaction occurs in a smooth vertical motion, which is designed to minimize disturbance to the coil package and prevent damage to the wire rings.15 Sund Birsta is a provider of such vertical compactors (e.g., PCVA model).9
Compacting stations are very often integrated directly with strapping systems, allowing the coil to be secured immediately after compaction while it is still under pressure, ensuring the package retains its dense form.15
C. Strapping
Strapping is the process of applying high-tensile bands, made of either steel or plastic (typically PET – polyester), around the coil to secure it, maintain its compacted form, prevent unwinding, and facilitate easier and safer handling during storage and transport. Straps can be applied circumferentially (around the outer diameter of the coil) or radially (through the eye of the coil).4
- Strapping Materials:
- Steel Strapping: Known for its high tensile strength and low elongation, steel strapping is ideal for very heavy, stable loads, and for applications involving long-distance transportation or multiple handling cycles. However, it is generally more expensive than plastic alternatives, has sharp edges that can pose safety risks, and can be more challenging to recycle.16
- PET (Polyester) Strapping: This is the most rigid type of plastic strapping, offering good tension retention, high strength, and resistance to nicks. It is also easier to recycle compared to steel. While it has less elongation than polypropylene (PP) strapping, it is a common choice for securing coils.16 Signode, for example, offers its Tenax® PET strapping.17
- Automation Levels:
- Manual Tools: These are the most basic method, involving hand-operated tensioners, sealers, and cutters. This method is slow, labor-intensive, and relies heavily on operator skill for consistent tension and seal quality.16
- Semi-Automatic Machines: These machines automate parts of the strapping cycle, such as tensioning, sealing (welding for plastic, crimping for steel), and cutting, but typically require the operator to manually feed the strap around the coil and initiate the cycle.18 Signode’s Wire Rod Compactor, for instance, integrates a semi-automatic strap feeder.14 This level offers a cost-effective step up from purely manual methods.
- Fully Automatic Machines: These systems perform the entire strapping operation without manual intervention. Coils are automatically positioned, and the machine feeds, tensions, seals, and cuts the strap. Such machines can be integrated into fully automated packing lines and offer the highest throughput and consistency.19 SHJL Pack and Fhopepack are among the suppliers emphasizing fully automatic PLC-controlled strapping solutions, often integrated with compactors.4
- Equipment:
- Strapping Heads: The core component of any strapping machine, responsible for tensioning, sealing, and cutting the strap. Different heads are designed for steel or plastic strapping and vary in their sealing technology (e.g., friction weld for PET, notch or seal-less for steel).19 Signode offers a range of strapping heads like the KLS, M410N, and M247 for steel, and the Z-20 and Z32 for plastic.19 AMOVA produces strapping heads that can create 2-, 4-, or 6-point weld seals, depending on the application’s security requirements.20
- Circumferential Strapping Machines: These machines apply straps around the outer circumference of the coil. They are available for coils oriented either horizontally ("eye to wall") or vertically ("eye to sky").19
- Radial (Eye) Strapping Machines: These machines feed the strap through the eye of the coil and secure it radially. This method is common for many coil types.19 Packing lines from Novastilmec, for example, often include radial strapping of coils.21
D. Wrapping
Wrapping involves applying one or more layers of protective material around the strapped coil. This serves multiple purposes: shielding the coil from environmental factors like moisture, dust, and corrosive agents; providing additional physical protection against scratches or impacts during handling; and often enhancing the stability of the packaged coil.1
- Wrapping Materials:
- Stretch Film (LLDPE/PE): Widely used for bundling and securing loads due to its elasticity and cling properties. For steel coils, stretch film can be infused with Vapor Corrosion Inhibitors (VCI) to provide anti-rust protection.22 Examples include EXCOR VALENO VCI stretch film23, RUSTX VCI Power Stretch film24, and ZERUST ICT VCI Stretch Film.25
- VCI Paper/Film: These materials are impregnated with VCIs that volatilize and form a protective molecular layer on the metal surface, preventing corrosion. VCI paper can be plain kraft, creped for better conformability, or reinforced with scrim for added strength. VCI films offer both corrosion protection and a moisture barrier.2 RUSTX provides VCI Crepe Paper26, and VCI Crepe Paper is also listed on Alibaba.27 Pesmel’s TEW (Through Eye Wrapping) technology notably uses a combination of crepe paper and PE film for superior rust prevention.28
- Crepe Paper: Often used in conjunction with VCI agents or as a standalone layer for cushioning, moisture absorption, or to improve the grip of subsequent wrapping layers. Its creped texture allows it to conform well to the coil’s shape.26
- Compound Paper/Fabric: Some packing lines utilize composite materials, which might be laminates of paper, film, and/or fabric, to provide a multi-functional protective layer.29
- HDPE (High-Density Polyethylene): Can be used as a robust wrapping material, sometimes also VCI-infused, offering good moisture resistance and toughness.26
- Ancillary Protective Materials: Beyond the main wrap, additional protective elements are often used, such as Outside Diameter (OD) and Inside Diameter (ID) protectors made from cardboard, plastic, or steel, as well as side wall protectors and belly wrap materials to guard vulnerable areas of the coil.2
- Wrapping Technologies:
- Horizontal Orbital Stretch Wrappers: These machines are designed for wrapping elongated products or coils by having a film carriage orbit around the product as it passes horizontally through the wrapping ring.30 SHJLPack offers various models in their GG series.30
- Rotary Ring/Arm Stretch Wrappers: Typically used for palletized loads, where either a ring carrying the film carriage or a rotating arm dispenses the film around a stationary pallet.30
- Through-Eye Wrapping (TEW): A specialized technique, often employing orbital wrappers, that passes the wrapping material (commonly film and/or paper) through the eye of the coil. This method creates a very well-sealed package, offering excellent protection against moisture ingress and corrosion.3 Pesmel is a key proponent and provider of TEW technology.28
- General Coil Wrapping Machines: Various manufacturers offer machines specifically designed for wrapping coils. For example, Suntechmach produces the GS-300 model suitable for wrapping steel, wire, copper, and pipe coils with materials like stretch film, knit tape, and paper tape.22 Dixin Machinery also offers models like the DP-series for wire coil film winding.31
E. Weighing Systems
Accurate weight determination is a critical step in the coil packing process, essential for inventory management, logistics planning, customer invoicing, and compliance with shipping regulations.
- Process: Weighing systems are integrated into the packing line to measure the weight of individual coils or, more commonly, the final packed bundles or palletized stacks. This can be done on a net basis (product only) or gross basis (product plus packaging and pallet).
- Equipment: Dedicated weighing stations or scales are incorporated at appropriate points in the line. These can range from static scales where a coil or pallet is placed for weighing, to dynamic in-motion weighing systems integrated into conveyor lines.4 Packing lines from Novastilmec and Metiz.tw, for example, explicitly include weighing stations as part of their automated coil packing solutions.29 Signode also mentions that their comprehensive coil packing lines can incorporate both net and gross weighing stations.17 The process described by Arcon-Metals for skidded coil stacks includes weighing the final skidded stack.6
- Integration: The data captured by weighing systems is often a crucial input for labeling systems, allowing for the printing of accurate weight information on shipping labels. Furthermore, this weight data is typically transmitted to higher-level plant management systems like MES (Manufacturing Execution Systems) or ERP (Enterprise Resource Planning) for inventory control, shipping documentation, and billing purposes.2
F. Marking and Labeling Systems
Once coils are packed and weighed, they must be accurately marked and labeled for identification, traceability, and information purposes throughout the supply chain.
- Process: This involves applying various forms of identification, such as human-readable text, barcodes (1D or 2D), and other tracking information, directly onto the coil, the packaging material, or on applied tags/labels.
- Technologies:
- Automated Tagging Systems: These systems employ robots or other automated machinery to print information onto durable tags (often metal tags for heat resistance in steel mill environments) and then securely attach these tags to the coils or bundles.4 Pannier Corporation (with its PolyTAG BLE for billets/slabs and PolyTAG FC for bundles/coils, using heat-resistant metal barcode tags printed without ink32) and Tebulo Robotics33 are notable specialists in this area. Sund Birsta also offers an Automatic Labelling Station for wire rod coils9, and Danieli provides the Q-ROBOT ROLL, an anthropomorphic robot station for long product finishing and labeling.34
- Paint Marking: For direct marking on the coil surface, some systems use specialized paint, often applied robotically for precision and consistency, especially in harsh mill environments or on hot products.33 Tebulo Robotics highlights its highly reliable paint systems with features like no paint clogging and safe refilling during operation.33
- Label Applicators: These are automated or semi-automated systems that print and/or apply pre-printed adhesive labels onto the packed coils or pallets.2 Signode offers Robotic Label Applicators as part of their coil packing line solutions.17 Cable coiling and wrapping machines from S&A Automation can feature automatic label application.35
- Integration: Marking and labeling systems are frequently linked with weighing systems to include accurate weight data on labels. They are also commonly integrated with plant-level data systems (MES/ERP) to receive coil-specific information for printing and to send back confirmation of processed and labeled coils for inventory and tracking updates.2 This ensures data accuracy and facilitates end-to-end traceability.
G. Stacking and Palletizing of Packed Coils
The final stage in many steel wire coil packing lines is the stacking or palletizing of the individually packed coils into larger, unitized loads suitable for efficient storage and transport.
- Process: This involves arranging the packed coils, which may be individual or bundled, onto pallets, skids, or directly into stacks in a stable and organized manner. The goal is to create a load that is easy to handle with forklifts or cranes and maximizes space utilization in warehouses and during shipping.
- Equipment:
- Automatic Coil Stackers: These machines automate the process of stacking coils, significantly increasing productivity and reducing the need for manual labor. They can be designed to work with sortation tables, which allow for segregating coils based on order or other criteria, or with shuttle car systems for simpler transfer to stacking positions.4 SHJL Pack mentions coil stackers as part of their automatic slit coil packaging systems.4 Packing lines from Metiz.tw also incorporate stacking systems.29 S&A Automation offers an optional automatic stacking and palletizing system for their cable coiling and wrapping machines.35
- Robotic Palletizers: Industrial robots equipped with specialized grippers can be used to pick up packed coils or cartons containing coils and precisely place them onto pallets according to pre-programmed patterns. This offers high flexibility in handling different coil sizes and stacking configurations.35 Imanpack, for example, utilizes robotic palletizers in their systems for welding wire coils, allowing for horizontal or vertical arrangement of cartons.36
- Sortation Tables: These are often powered, multi-position rotary tables that receive coils from the packing line and allow operators or automated systems to sort and direct them to different stacking locations or pallets, facilitating the processing of multiple customer orders from a single master coil.6
- Pallet Dispensers: In fully automated lines, pallet dispensers are used to automatically supply empty pallets to the stacking or palletizing station as needed, ensuring a continuous flow of operation.4
- Coil Racks: While not directly part of the active packing line machinery, specialized coil racks are an important downstream consideration for the safe and efficient storage of packed and palletized coils. These racks are designed to handle the heavy weight of coils, maximize vertical storage space, protect coils from damage, and allow for easy accessibility.37
The following table provides a summary of the key equipment involved in a steel wire coil packing line:
Table 1: Key Equipment in a Steel Wire Coil Packing Line
Process Stage | Equipment Type | Primary Function | Key Considerations (e.g., capacity, material compatibility, automation level) | Example Suppliers (from research) |
---|---|---|---|---|
Coil Reception & Handling | Coil Cars, Turnstiles, Upenders/Downenders | Receive, buffer, and orient coils for packaging. | Coil weight/dimensions, throughput, orientation change requirements, level of automation. | ADS Machinery, Bushman AvonTec, AMOVA, Brilex, Sund Birsta |
Conveying Systems (Roller, Chain, Walking Beam) | Transport coils between stations. | Load capacity, speed, layout constraints, coil temperature (for hot coils). | AMOVA, CTI Systems, Brilex, Sund Birsta | |
Coil Compacting | Horizontal/Vertical Compactors | Reduce coil volume for stable packaging. | Coil type (wire rod), required compaction force, cycle time, integration with strapping. | Signode, Primetals Technologies, Sund Birsta |
Strapping | Manual, Semi-Auto, Fully-Auto Strapping Machines | Secure coils with steel or PET straps. | Strap material, coil size, number of straps, tension requirements, automation level. | Signode, AMOVA, Novastilmec, SHJL Pack, Fhopepack, Metiz.tw |
Wrapping | Orbital Wrappers, TEW Systems, Stretch Wrappers | Apply protective materials (film, paper, VCI). | Coil dimensions, required protection level (moisture, corrosion), wrapping material, speed. | SHJLPack, Suntechmach, Dixin Machinery, Pesmel, Fhopepack |
Weighing | Integrated Weighing Stations/Scales | Determine coil/package weight. | Accuracy, capacity, integration with labeling/MES. | Novastilmec, Signode, Metiz.tw, Fhopepack |
Marking & Labeling | Automated Tagging, Paint Marking, Label Apps. | Apply identification and tracking information. | Durability of mark/label, data requirements (barcode, text), coil temperature, automation. | Pannier Corp, Tebulo Robotics, Signode, Sund Birsta, Danieli, Fhopepack |
Stacking & Palletizing | Automatic Stackers, Robotic Palletizers | Arrange packed coils onto pallets/skids. | Stack pattern, pallet size, load stability, throughput, level of automation. | SHJL Pack, Metiz.tw, S&A Automation, Imanpack |
The various stages within a steel wire coil packing line are not merely sequential but are highly interdependent. The output quality and efficiency of one stage directly influence the performance and requirements of the next. For example, the effectiveness of the compaction process (Stage B) has a direct bearing on how well strapping (Stage C) can be applied and how stable the final coil package will be. If a coil is poorly compacted, it may be difficult to achieve adequate strap tension, potentially leading to loose straps and an unstable load. Similarly, the choice of wrapping materials (Stage D), such as the use of VCI-infused films or papers for corrosion protection23, might influence the handling procedures or the need for additional protective layers depending on the expected storage duration or transit conditions.
This interconnectivity is further amplified in automated systems. Sensors and control systems often link operations to ensure smooth transitions, synchronize speeds, and allow for real-time adjustments based on feedback from different points in the line.1 For instance, a vision system detecting an improperly oriented coil at the reception stage might signal the handling robot to adjust its grip, or an issue detected during wrapping could flag the coil for inspection before it proceeds to stacking.
Consequently, a holistic system design approach is paramount when planning or upgrading a steel wire coil packing line. Attempting to optimize a single component or stage in isolation without considering its impact on the overall line can lead to unforeseen bottlenecks, compatibility issues, or a suboptimal final package. Decision-makers must therefore evaluate the entire line as an integrated system. This ensures that all components work harmoniously to achieve the desired levels of efficiency, package quality, and cost-effectiveness. This perspective also extends to supplier selection; preference should be given to suppliers who can demonstrate expertise in system integration or who can ensure seamless compatibility if equipment is sourced from multiple vendors. The goal is a balanced and synchronized line where each stage effectively prepares the product for the next, culminating in a securely and appropriately packaged steel wire coil.
III. Automation Levels and System Integration

The degree of automation is a primary determinant of a steel wire coil packing line’s efficiency, throughput, cost, and operational complexity. Solutions range from largely manual operations to highly sophisticated, fully automated lines integrated with plant-wide management systems.
A. Comparison of Manual, Semi-Automatic, and Fully Automatic Packing Lines
- Manual Lines:
- Description: These lines rely predominantly on human operators for the majority of tasks. This includes manually feeding coils, operating individual machines (if any), applying packaging materials by hand, and manually handling coils between stages. Strapping, for example, might be done using basic hand tools.16
- Advantages: The principal advantage is the significantly lower initial capital investment compared to automated alternatives.38 Manual lines can also offer flexibility for very low volume production, highly customized or non-standard packaging tasks, or in situations where capital for automation is severely restricted.
- Disadvantages: Manual operations are inherently slower, leading to low throughput. They are labor-intensive, resulting in high ongoing labor costs. Packaging quality and consistency can vary significantly depending on operator skill and fatigue. Furthermore, manual handling of heavy steel coils poses a greater risk of workplace injuries and product damage.4 Scaling up production with manual lines is also challenging and costly.
- Semi-Automatic Lines:
- Description: Semi-automatic lines introduce mechanization and automation to specific stages of the packing process, while still requiring considerable operator involvement for tasks like loading and unloading machines, positioning coils, and initiating machine cycles. For example, a semi-automatic strapping machine might automatically tension, seal, and cut the strap, but the operator would first need to manually feed the strap around the coil.18 Signode’s Wire Rod Compactor is an example of a semi-automatic machine that integrates compaction with a semi-automatic strap feeder.14 This level offers a cost-effective step up from purely manual methods.
- Advantages: These lines offer a balance between cost and performance. The initial investment is lower than for fully automatic systems, yet they provide improvements in packaging consistency, speed, and safety compared to purely manual methods. They are often a good solution for businesses transitioning towards automation or for those with medium production volumes.18
- Disadvantages: Throughput is still limited by the manual steps involved and can create bottlenecks if not properly balanced with the automated sections. Labor costs, while reduced compared to manual lines, remain higher than in fully automated setups.38
- Fully Automatic Lines:
- Description: Fully automatic packing lines are designed to operate with minimal human intervention. They integrate all packaging stages—coil handling, compacting, strapping, wrapping, weighing, labeling, and stacking/palletizing—into a continuous, synchronized flow, typically controlled by PLCs (Programmable Logic Controllers).1 Suppliers like SHJLPack and Fhopepack specialize in such fully automatic, PLC-controlled lines.4
- Advantages: These lines offer the highest levels of throughput and operational efficiency. Packaging quality is highly consistent, and material utilization is optimized. Labor costs are significantly reduced, and workplace safety is greatly enhanced by minimizing manual handling of heavy loads. Fully automatic lines are also highly scalable to meet increasing production demands.4
- Disadvantages: The primary drawback is the substantial initial capital investment required. These complex systems also necessitate skilled personnel for operation, maintenance, and troubleshooting. The setup and integration of fully automatic lines can also be more time-consuming and intricate.16
The following table provides a comparative analysis of these automation levels:
Table 2: Comparative Analysis of Automation Levels in Steel Wire Coil Packing Lines
Feature | Manual | Semi-Automatic | Fully Automatic |
---|---|---|---|
Initial Cost | Low | Medium | High |
Labor Requirement | High | Medium | Low (Supervisory) |
Throughput Capacity | Low | Medium | High |
Packaging Consistency | Low to Medium (Operator Dependent) | Medium to High | Very High |
Safety | Lower (Higher risk of manual handling injury) | Medium | Higher (Reduced manual intervention) |
Material Utilization | Variable, potential for waste | Improved, more controlled | Optimized, minimal waste |
Maintenance Complexity | Low (for tools) | Medium (for individual machines) | High (for integrated system) |
Scalability | Poor | Moderate | Excellent |
Typical Applications | Very low volume, specialized tasks | Low to medium volume, transitioning to automation | Medium to high volume, mass production, high consistency requirements |
B. Integration with MES/ERP Systems and Industry 4.0
Modern automated steel wire coil packing lines are increasingly designed not as standalone islands of automation but as integral parts of a connected manufacturing ecosystem. This involves sophisticated integration with higher-level plant management systems and the adoption of Industry 4.0 principles.
- MES/ERP Integration: The ability to connect the packing line’s control system with Manufacturing Execution Systems (MES) and Enterprise Resource Planning (ERP) systems is becoming standard for advanced lines.1 This integration facilitates a seamless flow of data. For example, the packing line can receive coil-specific data (e.g., dimensions, grade, customer order) from the MES/ERP, which can then be used to automatically adjust machine parameters or print correct labels. Conversely, the packing line can send data back to these systems, such as production counts, material consumption, weight information, and quality control status, enabling real-time production tracking, accurate inventory management, efficient order fulfillment, and informed business decision-making.3 Fhopepack explicitly mentions the compatibility of their lines with MES and ERP systems2, and Signode notes that their lines can integrate with IT Level 2 systems.17
- Industry 4.0 Concepts: The principles of Industry 4.0 are being actively applied to steel coil packing lines to enhance intelligence, connectivity, and autonomy:
- Internet of Things (IoT): Packing lines are being equipped with a multitude of sensors (e.g., for temperature, pressure, position, vibration) that collect vast amounts of operational data. Through IoT connectivity, this data can be transmitted to cloud platforms or local servers for real-time monitoring of equipment health, tracking of coil movement through the line, and analysis of key process parameters.3 This enables remote diagnostics, proactive maintenance scheduling, and provides valuable insights into operational bottlenecks or areas for improvement. An example is Wirepas technology, which uses IoT asset tags for smart tracking of steel coils within a facility.39
- Artificial Intelligence (AI) & Machine Learning (ML): AI and ML algorithms are being leveraged to analyze the data collected via IoT sensors. Applications include:
- Predictive Maintenance: AI models can predict potential equipment failures by identifying subtle anomalies in sensor data, allowing maintenance to be scheduled proactively, thus minimizing unplanned downtime and associated costs.3 ThyssenKrupp Steel, for instance, reported a 20% reduction in unplanned downtime using an AI-based predictive maintenance system in broader steel production.40
- Quality Control Automation: AI-powered vision systems can inspect coils for surface defects, dimensional inaccuracies, or packaging flaws with greater speed and accuracy than human inspectors.3
- Process Optimization: ML algorithms can identify optimal operating parameters for various stages of the packing line (e.g., wrapping tension, conveyor speeds, compactor pressure) based on historical performance data and coil characteristics, leading to improved efficiency and reduced material waste.3
- Enhanced Robotics: AI can improve the intelligence and adaptability of robotic systems used in packing lines, enabling them to handle a wider variety of tasks and adapt to unforeseen circumstances more effectively.3
- Digital Twins: This technology involves creating a virtual, dynamic replica of the physical packing line. Digital twins can be used for various purposes, including simulating different operational scenarios to test new configurations or process parameters without disrupting actual production, optimizing line performance, conducting predictive analytics on equipment health, and providing a safe environment for operator training.3 Pesmel, for example, utilizes simulation models (digital twins) extensively in the design, validation, commissioning, and ongoing optimization of their material flow solutions.41
C. Robotics in Coil Packing Lines
The integration of industrial robots is a significant trend in the automation of steel wire coil packing lines, bringing precision, speed, and flexibility to various tasks that were traditionally manual or handled by dedicated, less flexible machinery.
- Applications:
- Coil Handling: Robots, typically 6-axis articulated arms, are employed for precise lifting, moving, positioning, and orienting heavy steel coils. This can include transferring coils between conveyors, loading them into machines (e.g., compactors, wrappers), and orienting them for specific packaging steps.36 Danieli’s Q-ROBOT ROLL is an example of an anthropomorphic robot used for long product finishing and labeling, showcasing robotic capabilities in handling and processing.34
- Packaging Material Application: Robots can be tasked with placing intermediate protective layers (e.g., VCI paper sheets between coil layers or on pallets), accurately applying labels to coils or packages, and in some cases, even operating specialized wrapping or strapping end-effectors.36
- Palletizing and Stacking: Robots are highly effective for picking up finished, packed coils (either individually or in cartons) and stacking them onto pallets or skids according to predefined patterns. This ensures stable and optimized pallet loads.35 Imanpack, for instance, incorporates robotic palletizers in their packaging systems for welding wire coils, offering flexibility in how cartons are arranged on the pallet.36
- Marking and Tagging: Automated robotic systems are used to apply identification marks or attach durable tags to coils. These systems often combine robotic manipulation with specialized marking technologies like paint spraying or tag welding.20 Pannier Corporation’s PolyTAG systems32 and solutions from Tebulo Robotics33 exemplify this application. A WIPO patent also describes a robotic system specifically for coil packaging, indicating ongoing innovation in this area.42
- Autonomous Mobile Robots (AMRs) / Automated Guided Vehicles (AGVs): While not always part of the fixed packing line, AMRs and AGVs represent a robotic approach to the flexible and autonomous transport of coils, packaging materials, or finished pallets between the packing line, storage areas, and dispatch zones.3
- Benefits: The use of robotics in coil packing lines offers numerous advantages, including increased precision and repeatability in handling and packaging operations, higher operational speeds leading to greater throughput, and enhanced consistency in package quality. Robots can operate continuously in demanding environments, reducing labor costs and significantly improving workplace safety by taking over tasks that are physically strenuous, repetitive, or hazardous for human operators. Their programmability also allows for greater adaptability to different coil sizes, weights, and packaging configurations compared to fixed automation.43
The convergence of advanced automation with sophisticated data management and smart technologies like IoT and AI marks a pivotal shift in steel coil packing. It moves beyond simply mechanizing physical tasks to creating intelligent, self-optimizing systems. While basic automation primarily targets labor reduction and increased speed4, the real competitive differentiator in modern packing lines lies in this "automation-data nexus." The data generated by sensors on automated equipment, when captured and analyzed effectively, unlocks a new tier of operational excellence. IoT connectivity enables real-time visibility into machine health and process performance, facilitating proactive maintenance strategies that minimize costly unplanned downtime.3 AI and machine learning algorithms can then leverage this data to dynamically optimize packing parameters, enhance quality control to levels unattainable by human inspection alone, and predict potential failures before they occur.3 Furthermore, seamless integration with plant-wide MES and ERP systems ensures that the packing operation is not an isolated silo but a responsive and integral part of the overall business strategy, aligning its output with broader objectives such as inventory control, order fulfillment, and supply chain efficiency.1 Consequently, companies investing in new steel coil packing lines should look beyond the immediate benefits of physical automation. The strategic imperative is to build systems capable of generating, processing, and acting upon data. This implies that suppliers offering robust data integration capabilities, advanced analytics, and smart features will provide greater long-term value. It also signals a growing need for a workforce equipped with the skills to manage, interpret, and leverage the insights derived from these increasingly intelligent packing operations.
IV. Price Analytics: Cost Factors, TCO, and ROI

Understanding the financial aspects of investing in a steel wire coil packing line is crucial for strategic decision-making. This involves analyzing the factors that influence the initial purchase price, calculating the Total Cost of Ownership (TCO) over the equipment’s lifecycle, and projecting the Return on Investment (ROI).
A. Factors Influencing Price
The price of a steel wire coil packing line or its individual components can vary significantly based on a confluence of factors:
- Machine Type and Operational Mechanism: The fundamental design and technology of the equipment play a major role. For instance, horizontal versus vertical wrappers or compactors will have different cost structures. Specialized technologies, such as Through-Eye Wrapping (TEW) systems, may also command a premium due to their advanced capabilities.44
- Coil Handling Capacity (Physical Dimensions and Weight): Lines designed to handle larger and heavier coils necessitate more robust construction, larger motors, and more substantial engineering, all of which contribute to higher costs.45
- Packing Speed and Throughput Efficiency: Equipment engineered for higher speeds and greater throughput typically incorporates more powerful drives, sophisticated control systems, and precision components, leading to an increased price point.45
- Level of Automation: This is one of the most significant price differentiators. Fully automatic lines are considerably more expensive than semi-automatic or manual systems due to the complexity of automation, robotics, sensors, and control software involved.38
- Customization: Standard, off-the-shelf machines are generally less expensive than lines that require significant customization to fit specific coil dimensions, unique factory layouts, or particular packaging protocols. Custom engineering and manufacturing add to the overall cost.1
- Brand and Manufacturer Origin: Well-established brands with a reputation for quality, reliability, and advanced technology may have higher prices.45 Similarly, equipment manufactured in regions known for high engineering standards, such as "Made in Germany" technology, might carry a price premium, often associated with perceived higher quality and durability.46
- Materials of Construction: The use of high-quality, durable materials, such as stainless steel for components in corrosive environments or heavy-duty steel for structural frames, increases the manufacturing cost and thus the price.14
- Control Systems and Software Sophistication: Advanced Programmable Logic Controllers (PLCs), intuitive Human-Machine Interfaces (HMIs), seamless integration capabilities with MES/ERP systems, and the inclusion of smart features like IoT connectivity and AI-driven analytics contribute to a higher system price.1
- Safety Features: Comprehensive safety systems, including light curtains, safety interlocks, physical guarding, and emergency stop systems, are essential for operator protection but add to the equipment’s cost.4
- Ancillary Equipment: The inclusion of auxiliary equipment such as turnstiles, coil cars, specific types of conveyors (e.g., walking beam vs. roller), automated pallet dispensers, or specialized labeling systems will impact the total price of the packing line.
- Packaging Method Complexity: The chosen packaging method itself influences cost. Simple packaging (e.g., a single layer of stretch film) is inherently cheaper than more complex, multi-layer export packaging involving VCI materials, edge protectors, and robust crating, especially if these additional steps are not fully automated.47
B. Indicative Price Ranges
Providing precise price ranges for steel wire coil packing lines is challenging due to the high degree of variability based on the factors mentioned above. However, available data offers some general indications:
- General Spectrum: Prices can range from a few thousand US dollars for very basic manual or semi-automatic individual machines to several hundred thousand, or even millions, for complex, fully integrated, and highly automated packing lines.45
- Proxy for Complexity (Wire Drawing Machines): While not directly packing equipment, the price tiers for wire drawing machines illustrate the impact of automation: manual machines might range from $3,000 to $20,000; semi-automatic from $15,000 to $50,000; and fully automatic from $50,000 to $500,000.45 This demonstrates the significant cost escalation associated with increasing automation levels.
- Individual Coil Wrapping Machine Examples (from Fhopepack44):
- A horizontal coil wrapper with a 2000kg capacity was indicated around ₹290,000 (approximately $3,500 USD).
- CE certified medium-sized horizontal wrappers were noted in the $7,900-$7,950 range.
- Vertical wrapping machines with motorized ring up/down systems were priced around ₹270,000 (approximately $3,250 USD).
- Other automatic vertical machines for various coil types (tyre, plastic tube, steel coil) were listed between $3,720 and $4,290.
- Radial reel stretch wrappers showed a broader range from ₹600,000 to ₹1,000,000 (approximately $7,200 – $12,000 USD).
- Fully Auto Steel Wire Coil Packing Machine (Dixin Machinery31): An indicative price of US$2,800.00 – $6,550.00 was listed, with a Minimum Order Quantity (MOQ) of 5 sets. This price seems relatively low for a "fully auto" system and might pertain to a specific machine module or reflect pricing from a particular manufacturing region or tier of supplier, rather than a complete, integrated line.
- Illustrative Price Tiers by Automation Level (from Fhopepack44):
- Manual Systems: <$5,000 – $10,000
- Semi-Automatic – Basic: $10,000 – $30,000
- Semi-Automatic – Advanced: $25,000 – $70,000
- Fully Automatic – Standalone Machine: $50,000 – $150,000
- Note: These are indicative ranges for standalone machines or basic systems. Fully integrated lines incorporating multiple automated stages (handling, compacting, strapping, wrapping, weighing, labeling, palletizing) will command substantially higher investments, potentially reaching into the high hundreds of thousands or millions of US dollars, depending on scale and complexity.
The following table provides an overview of indicative price ranges, emphasizing the influence of automation:
Table 3: Indicative Price Ranges for Steel Coil Packing Equipment by Automation Level
Equipment/System Type | Automation Level | Indicative Price Range (USD) | Key Features Influencing Price |
---|---|---|---|
Individual Strapping Machine | Manual/Semi-Automatic | $500 – $15,000 | Strap type (steel/PET), power source, basic automation features. |
Individual Wrapping Machine | Manual/Semi-Automatic | $3,000 – $20,000 | Coil size capacity, wrapping material type, basic automation. |
Standalone Compactor | Semi-Automatic | $20,000 – $80,000 | Compaction force, coil size, cycle time, basic integration. |
Basic Semi-Automatic Line | Semi-Automatic | $30,000 – $100,000 | Limited automation, operator involvement for transfers, basic handling and packing functions. |
Fully Automatic Standalone | Fully Automatic | $50,000 – $250,000+ | Single automated process (e.g., wrapping or strapping station with conveyors), PLC control. |
Fully Integrated Packing Line | Fully Automatic | $200,000 – $2,000,000+ | Multiple automated stages, robotics, MES/ERP integration, advanced sensors, high throughput. |
Disclaimer: These price ranges are highly illustrative and subject to significant variation based on specific project requirements, supplier, and market conditions. Detailed quotations from suppliers are necessary for accurate budgeting.
C. Total Cost of Ownership (TCO) Analysis
The Total Cost of Ownership (TCO) provides a comprehensive financial estimate of the direct and indirect costs associated with a steel wire coil packing line throughout its entire operational lifespan. It extends far beyond the initial purchase price and is a critical metric for making sound long-term investment decisions.48
- Definition: TCO includes all expenditures from acquisition through operation, maintenance, and eventual disposal.48 It is a long-term perspective on cost.49
- Key Components of TCO:
- Acquisition Costs (Capital Costs): These are the upfront, typically one-time expenses incurred to procure and install the packing line. They include:
- The purchase price of all machinery and equipment.48
- Software licenses for control systems, HMI, and any specialized applications.48
- Installation and commissioning fees, which can be substantial for complex lines.48
- Costs for any necessary facility modifications to accommodate the new line (e.g., foundations, utilities).48
- Initial training costs for operators and maintenance staff.48
- Operational Costs: These are recurring expenses associated with running the packing line on a day-to-day basis:
- Energy consumption (electricity, compressed air for pneumatic systems).48
- Labor costs, including wages and benefits for operators, supervisors, and quality control personnel (even for automated lines, some supervision is typically needed).48
- Consumable materials, such as strapping (steel or PET), stretch film, VCI paper/film, labels, ink, and other packaging sundries.48
- Software maintenance fees or upgrade costs.48
- Insurance costs for the equipment.
- Maintenance Costs: These are ongoing expenses required to keep the machinery in optimal working condition and prevent unexpected breakdowns:
- Downtime Costs: While not a direct expenditure, the cost of lost production due to equipment downtime (both planned for maintenance and unplanned due to failures) can be a significant component of TCO. This is an imputed cost representing lost revenue or opportunities.3 For example, one hour of downtime on a critical production line could result in losses of $10,000 or more, depending on the value of output.44
- Depreciation: The accounting charge for the decrease in the value of the equipment over its useful life.49
- Opportunity Cost: The potential return that could have been earned if the capital invested in the packing line had been used for an alternative investment.49 This is more of a theoretical financial consideration.
- Disposal Costs: Expenses associated with decommissioning, removing, and disposing of the old equipment at the end of its useful life.49
- Acquisition Costs (Capital Costs): These are the upfront, typically one-time expenses incurred to procure and install the packing line. They include:
- Importance of TCO: Relying solely on the initial purchase price can be misleading. A machine with a lower upfront cost might incur higher TCO due to frequent breakdowns, excessive energy consumption, high consumable usage, or extensive maintenance requirements.44 A thorough TCO analysis helps in identifying the most economically viable solution over the long term.50
The following table outlines key components for calculating TCO:
Table 4: Key Components for Calculating Total Cost of Ownership (TCO) of a Steel Coil Packing Line
Cost Category | Specific Cost Items | Considerations/Notes |
---|---|---|
Acquisition Costs | Purchase price (equipment, software), installation, commissioning, facility modifications, initial training. | One-time, upfront expenses. Can vary greatly with automation and customization. |
Operational Costs | Energy, labor (operators, supervisors), consumables (straps, film, labels, ink), software fees, insurance. | Recurring costs. Labor and consumables can be significant. Automation level heavily impacts labor costs. |
Maintenance & Support | Preventive maintenance, corrective repairs, spare parts, wear parts, service contracts, technical support. | Ongoing costs. Reliability of equipment and availability of support are key. |
Downtime Costs | Lost production/revenue due to planned and unplanned equipment stops. | Imputed cost, can be very high. Directly related to equipment reliability and speed of repair. |
End-of-Life Costs | Decommissioning, removal, disposal/recycling of old equipment. | Occur at the end of the equipment’s useful life. Environmental regulations for disposal can impact these costs. |
D. Return on Investment (ROI) Analysis
Return on Investment (ROI) is a performance measure used to evaluate the efficiency or profitability of an investment. For a steel wire coil packing line, it compares the financial benefits gained from the investment against its total cost.50 A common formula is: (ROI = \frac{(Net\ Profit\ or\ Gain\ from\ Investment) – (Cost\ of\ Investment)}{Cost\ of\ Investment} \times 100\%)49.
- Key Benefits to Quantify (Gain from Investment):
- Labor Savings: Automation significantly reduces the need for manual labor in packing operations, leading to direct savings in wages, benefits, and associated overheads.2
- Increased Throughput/Production Capacity: Automated lines operate at higher speeds and can run continuously for longer periods, increasing the number of coils packed per shift and potentially enabling higher overall plant output.2 For instance, some ASRS systems have reported up to a 70% increase in order picking speed, which is analogous to throughput gains.51
- Reduced Material Waste: Precision application of packaging materials (straps, film, paper) by automated systems minimizes overuse and scrap, leading to savings on consumables.2 Pesmel’s TEW technology, for example, is claimed to offer 20-30% savings in packing materials.28
- Improved Product Quality/Reduced Damage: Consistent and appropriate packaging reduces the incidence of product damage during handling, storage, and transit. This translates into fewer customer claims, less rework, and reduced scrap material.2
- Enhanced Safety: A reduction in manual handling tasks leads to fewer workplace injuries. This results in lower costs associated with workers’ compensation, medical expenses, and lost workdays, alongside improved employee morale.4
- Reduced Downtime (if new system is more reliable): Investing in a new, more reliable packing line can decrease unplanned downtime compared to an older, problematic system, leading to increased operational uptime and more consistent production.16
- Costs to Consider (Cost of Investment & Annual Costs):
- Case Study Insights & Examples:
- A case study by SHJLPack highlighted that a customized steel coil packing line led to a 30% reduction in downtime. This resulted in significant cost savings, increased productivity, and improved workforce morale, ultimately justifying the initial investment in customization.53
- Fhopepack suggests that for some automated systems, the ROI can be realized within a relatively short period, often cited as 2 to 3 years, depending on the scale of benefits achieved.44
- An analogous example from the portable roll forming industry showed that if a machine costing $160,000 generated savings of $2.25 per square foot, approximately 71,000 square feet of panel production would be needed to recoup the initial investment.54 This illustrates how volume and per-unit savings contribute to payback.
- Framework for ROI Calculation: A structured approach is essential for a credible ROI analysis.
Table 5: Framework for ROI Calculation of an Automated Steel Coil Packing Line
Step | Components to Consider / Calculation |
---|---|
A. Calculate Initial Investment (Cost of Investment) | Sum of: Equipment purchase price, installation & commissioning costs, initial training costs, facility modification costs. |
B. Calculate Annual Operational Costs (New System) | Sum of: Energy consumption, labor (operators, supervisors for new system), consumables (straps, film, labels, etc.), routine maintenance, spare parts, software/license fees. |
C. Estimate Annual Benefits/Savings (Compared to Baseline/Old System) | Quantify savings in: – Labor (reduced FTEs or hours) – Material (reduced waste of film, straps) – Throughput (value of increased production/sales) – Damage Reduction (cost of fewer claims/rework) – Safety (reduced injury-related costs) – Downtime (value of increased uptime) |
D. Calculate Net Annual Benefit | Total Annual Benefits/Savings (from Step C) – Annual Operational Costs of New System (from Step B). |
E. Calculate ROI & Payback Period | ROI (%) = (Net Annual Benefit / Initial Investment) x 100. Payback Period (Years) = Initial Investment / Net Annual Benefit. |
The initial purchase price of a steel coil packing line is only one facet of a complex investment decision. A comprehensive financial evaluation must consider the Total Cost of Ownership (TCO) over the equipment’s entire lifecycle and the potential Return on Investment (ROI) it can deliver. These two metrics are strategically intertwined.50 A system with a low initial acquisition cost might appear attractive at first glance. However, if this lower price comes at the expense of reliability, efficiency, or build quality, it could lead to higher ongoing maintenance expenses, increased operational costs (e.g., higher energy or consumable use), and more frequent or prolonged downtime. Such factors would inflate the TCO significantly over time. As noted in one analysis, the financial repercussions of machine downtime, potentially amounting to thousands of dollars per hour, can far outweigh any initial savings on a cheaper machine, rendering it a "false economy".44
A high TCO, driven by these ongoing issues, will inevitably erode the "Net Profit" or "Gain from Investment" component used in the ROI calculation. This could result in an initially less expensive machine yielding a poorer long-term ROI compared to a system with a higher upfront cost but superior reliability and lower operating expenditures. The case study from SHJLPack, where a customized (and likely more expensive initially) packing line led to substantial long-term savings and a 30% reduction in downtime, supports this principle.53 Therefore, decision-makers should resist the temptation to prioritize solely on the initial price tag. A diligent TCO analysis is crucial for accurately forecasting long-term costs. This, in turn, provides the foundation for a more realistic and reliable ROI projection. The optimal investment choice is typically one that strikes a balance between an acceptable TCO and a strong, sustainable ROI, aligning with the company’s broader strategic objectives for operational efficiency, product quality, and workplace safety. This often translates to investing more upfront in robust, highly automated systems from reputable suppliers who offer excellent long-term support and proven reliability.
V. Market Landscape and Key Solution Providers
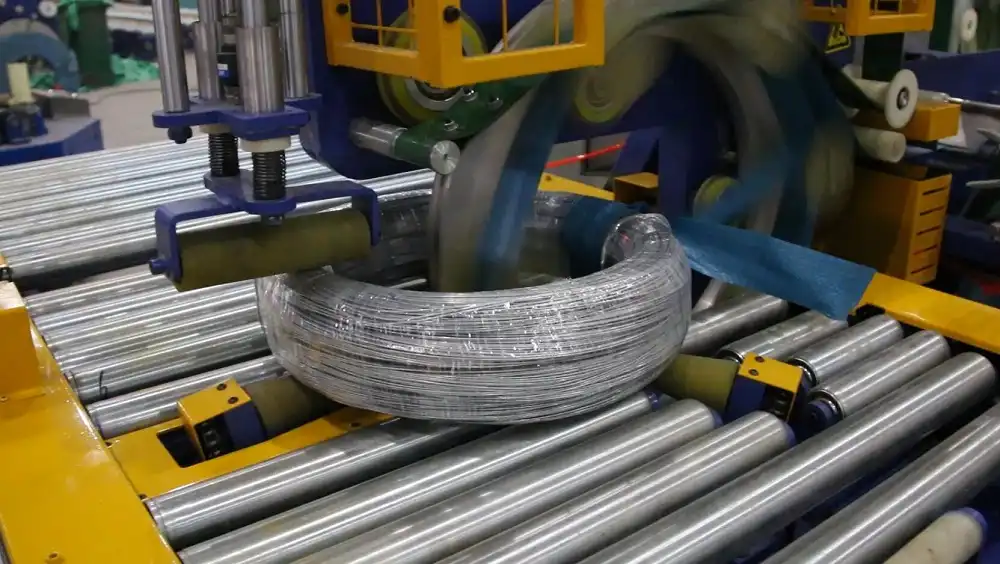
The market for steel wire coil packing lines is diverse, featuring a range of global and regional manufacturers. These providers offer solutions varying from individual specialized equipment components to fully integrated, turnkey packing lines. Their technological focus, scale of operations, and geographical reach also differ, catering to the varied needs of the steel and metals processing industries.
Overview of Key Solution Providers
An examination of the market reveals several prominent players known for their comprehensive offerings or specialized expertise in steel coil handling and packaging:
- Pesmel: This Finnish company is recognized for its "Material Flow How®" concept, which integrates in-mill logistics, advanced packing solutions, and automated high-bay storage systems for a variety of metal products, including coils and wire rods.28 A key technology is their Through-Eye Wrapping (TEW) system, often utilizing a combination of crepe paper and film, which is lauded for excellent rust prevention and potential savings in packing material consumption (20-30%).28 Pesmel emphasizes high levels of automation, Warehouse Management System (WMS) control, and tailored solutions to optimize material flow and minimize bottlenecks.55
- Sund Birsta: A Swedish company with a strong focus on handling and packing solutions specifically for the wire rod and bar industry. Their product portfolio includes the SUNDCO coil handling concept, coil collecting stations, various compactors (PCH-2 horizontal, PCVA vertical, and the fast, energy-efficient PCH Alfa, which likely uses hydraulics due to its pump control system), robust strapping machines (like the SMC for high-temperature applications and the Accumulator for strap management), automatic labeling stations, and diverse unloading stations (options include storing racks, walking beam conveyors, and chain conveyors).9
- Fives Group: A global industrial engineering group, Fives offers a broad range of solutions for the steel industry.56 While their explicit "wire coil" packaging lines are not extensively detailed in the provided research, their expertise in custom-engineered pickling lines (NeoPik®)57, advanced strip processing lines (NeoKoil®)56, and comprehensive tube finishing lines—which include sophisticated packaging systems like Robopack (robotic) and Taylor-Wilson—demonstrates significant capabilities in automation, material handling, and packaging for metal products. Their focus on advanced high-strength steels (AHSS) and integrated automation is notable.
- Danieli: An Italian plant builder for the metals industry, Danieli provides extensive solutions for long products.34 This includes drawing plants58, the innovative K-SPOOL system for producing large (up to 8-ton), twist-free spooled coils with automated strapping and weighing59, K-BUNDLING systems to prevent tangled bars60, tying optimization systems60, and the Q-ROBOT ROLL anthropomorphic robot stations for product finishing and labeling.34 Danieli’s solutions are geared towards high-speed, high-capacity, and highly automated operations.
- SMS group (incorporating AMOVA technology): This German company offers comprehensive logistics systems under the AMOVA brand for the metals industry.20 Their portfolio includes coil packaging lines61, slit-coil packaging lines62, sheet metal packaging solutions62, a variety of strapping machines (for steel, PP, and PET straps)63, advanced marking and labeling systems (often incorporating 6-axis industrial robots)20, and a wide array of conveying systems (pallet conveyors for hot coils8, high-speed cars64, Automatic Coil Transporters – A.C.T.®).64 They emphasize modular design, high levels of automation, and integration with customer manufacturing control systems.20
- Signode: A well-known name in industrial packaging, Signode offers a range of equipment pertinent to coil packing.17 This includes wire rod compactors (e.g., RHC-4H, RVC-4H semi-automatic models with integrated strapping)14, numerous application-specific strapping machines (for circumferential and radial/eye strapping of coils using steel or their Tenax® PET strap)19, various strapping heads19, the XYZ CoilMaster® protective wrapping system17, robotic label applicators17, and other handling equipment.17 Their core strength lies in strapping and protective packaging solutions.
- Primetals Technologies (Morgan): This company provides coil handling systems (utilizing horizontal hooks or vertical stem pallets)15 and compacting systems (both horizontal and vertical types, compatible with wire binding or strapping).15 They highlight their mechatronic solutions for automation and offer various coil cooling options integrated within their handling lines.15
- Fhopepack (FHOPE): A manufacturer of automatic steel coil packing machines and complete coil packaging lines.2 Their offerings cover slit coil handling2, various wrapping techniques (TEW is mentioned)3, strapping2, and stacking2. Fhopepack emphasizes automation, compatibility with IoT, MES/ERP integration2, and the ability to provide customized solutions.2 They also provide indicative pricing for different types of coil packing machines, suggesting a range of solutions for different budgets and needs.44
- SHJL Pack (Shanghai Jinglin Packaging Machinery): This Chinese manufacturer offers custom-built automatic steel coil packing lines, available in both horizontal and vertical coil packing configurations.1 Their systems are PLC controlled and can integrate various modules such as turnstiles1, downenders1, weighing stations4, wrapping machines1, strapping machines1, and stacking machines.4 They also produce wire coil compactors4, copper coil packing lines4, and specialized lines like those for hose coiling and wrapping.4
- Metiz.tw: This Taiwanese supplier provides automatic horizontal steel coil packing lines that primarily use compound paper as the wrapping material.29 Their lines typically include coil picking and tilting systems29, net/gross weighing stations29, PP/PET strapping machines29, wrapping machines29, and stacking systems.29
- S&A Automation (wirecable-solution.com): Focuses on the cable industry, offering automatic cable coiling and wrapping machines (models TP 460, TP 600)35. These machines can be optionally equipped with automatic stacking and palletizing systems, indicating solutions for end-of-line automation for wire products.35
- Suntechmach (cnsuntech.com): Offers wire coil packing machines like the GS-300, designed for compacting and wrapping coils using materials such as stretch film, knit tape, and paper tape.22
- Dixin Machinery: Another China-based supplier, offering fully automatic steel wire coil packing machines (DP-series) primarily focused on film winding and wrapping applications.31
- Imanpack Packaging: An Italian company specializing in packaging solutions, including complete systems for welding wire coils.36 Their lines can feature shrink film wrapping (using their Venus Plus machine and shrink tunnel)36, cartoning (MCTN2000 intermittent horizontal cartoner)36, and robotic palletizing with custom picking heads.36
The following table summarizes key offerings from some of these providers:
Table 6: Overview of Key Steel Wire Coil Packing Solution Providers
Provider Name | Key Offerings/Specialization | Target Coil Types | Noteworthy Technologies/Features | Geographical Focus (if known) |
---|---|---|---|---|
Pesmel | Integrated material flow, packing (TEW), automated high-bay storage. | Coils (steel, aluminum), wire rods, sheets, strips. | Material Flow How® concept, TEW (crepe paper + film), WMS control, high automation. | Global |
Sund Birsta | Coil handling, compacting, strapping, labeling, unloading for wire rod. | Wire rod coils. | SUNDCO handling, PCH-2/PCVA/PCH Alfa compactors, SMC strapping, Automatic Labelling Station, walking beam/chain conveyors. | Global |
Fives Group | Pickling, strip processing, tube finishing & packaging. | Carbon, stainless, silicon steels (strip/tube). | NeoPik®/NeoKoil® lines, Robopack, Taylor-Wilson packaging, AHSS processing, automation. | Global |
Danieli | Long product solutions, drawing plants, coil handling & packaging. | Wire rod, bars (round, square, flat, hex). | K-SPOOL (heavy spooled coils), K-BUNDLING, Q-ROBOT ROLL (labeling), high-speed automation. | Global |
SMS group (AMOVA) | Comprehensive logistics: transport, storage, packaging. | Hot/cold rolled strip, slit coils, sheet metal. | Modular packaging lines, robotic marking/labeling, pallet/HSC/A.C.T.® conveyors, WMS. | Global |
Signode | Strapping systems, compactors, protective wrapping. | Wire rod coils, general steel coils. | Wire Rod Compactor, steel/PET strapping machines (circumferential, radial), XYZ CoilMaster®, robotic label applicators. | Global |
Primetals (Morgan) | Coil handling and compacting systems for rod mills. | Rod coils, bar-in-coil. | Horizontal hook & vertical stem pallet handling, horizontal/vertical compactors, mechatronic automation, cooling options. | Global |
Fhopepack (FHOPE) | Automatic steel coil packing machines and lines. | Steel coils, slit coils. | TEW wrapping, MES/ERP/IoT integration, customizable lines. | Global (China-based) |
SHJL Pack | Custom automatic coil packing lines (horizontal/vertical). | Steel coils, copper coils, wire coils, hoses. | PLC control, turnstiles, downenders, weighing, wrapping, strapping, stacking. | Global (China-based) |
Metiz.tw | Automatic horizontal steel coil packing lines. | Slit steel coils. | Compound paper wrapping, PP/PET strapping, weighing, stacking. | Taiwan-based |
Imanpack Packaging | Packaging and palletising systems for welding wire. | Welding wire coils. | Shrink film wrapping (Venus Plus), cartoning (MCTN2000), robotic palletizing. | Global (Italy-based) |
The landscape of suppliers for steel coil packing solutions is characterized by a broad spectrum of offerings, ranging from highly specialized components to fully integrated, plant-wide logistics systems. At one end, major engineering firms like Pesmel28, SMS Group (through its AMOVA technology)20, Danieli34, and Primetals Technologies15 provide large-scale, often bespoke, solutions that can encompass not only the packing line itself but also upstream and downstream material handling, automated storage and retrieval systems (AS/RS), and sophisticated plant-level control and management software. These are typically suited for new plant constructions (greenfield projects) or major overhauls of existing facilities where a high degree of integration and automation is required.
At the other end of the spectrum, companies may specialize in particular types of equipment or consumables. For instance, Signode is well-known for its strapping systems and materials14, while Sund Birsta has a strong focus on compactors and handling systems for wire rod.9 Smaller manufacturers, such as Dixin Machinery31 or Suntechmach22, often provide specific machine types like wrappers or basic compactors, which might be integrated into lines by other system providers or purchased by end-users for standalone applications or smaller-scale upgrades.
This diversity in supplier offerings reflects the varied needs of the steel industry. Large, high-throughput mills often require comprehensive, turnkey solutions that minimize manual intervention and maximize efficiency. Smaller processors or service centers, on the other hand, might look for modular upgrades to specific parts of an existing line or cost-effective semi-automated solutions to address particular bottlenecks or quality issues. The complexity of integration, especially with existing plant MES/ERP systems and emerging Industry 4.0 technologies, also dictates supplier choice, with larger, more technologically advanced providers often better equipped to handle such intricate projects.
This varied landscape implies that there is no "one-size-fits-all" supplier. Businesses seeking coil packing solutions must first clearly define the scope of their project, their current and future capacity needs, the level of automation desired, and their integration requirements. Understanding whether the need is for a standalone specialized machine, a modular upgrade to an existing line, or a complete greenfield installation with full system integration is crucial for identifying and shortlisting the most appropriate vendors. It also suggests that collaborations and partnerships between specialized equipment manufacturers and larger system integrators are likely common in delivering comprehensive solutions to the end-user.
VI. Innovations and Future Trends in Coil Packaging

The steel wire coil packaging sector is continually evolving, driven by demands for greater efficiency, enhanced product protection, improved sustainability, and smarter operations. Several key innovations and trends are shaping the future of this industry.
A. Smart Packaging Solutions
The concept of "smart packaging" is extending into industrial applications like steel coil packing, leveraging sensor technology, IoT, and data analytics to create more intelligent and responsive systems.
- Sensor Integration: Modern packing lines are increasingly equipped with a variety of sensors that monitor not only the machine’s performance but also the condition of the package and the coil itself. These can include sensors for humidity, temperature, and shock, providing real-time data during transit and storage.3 For instance, Wirepas technology utilizes IoT asset tags for smart tracking of steel coils, enabling real-time location and condition monitoring.39
- IoT and Data Analytics: The Internet of Things (IoT) facilitates the collection and transmission of vast amounts of data from these sensors. This data can be analyzed remotely to diagnose issues, predict maintenance needs (predictive maintenance), and optimize packaging processes. Artificial Intelligence (AI) and Machine Learning (ML) algorithms are applied to this data to identify patterns, improve quality control (e.g., AI-powered vision systems for defect detection), and enhance overall operational efficiency.3
- Digital Twins: The creation of digital replicas, or "digital twins," of physical packing lines is an emerging trend. These virtual models allow manufacturers to simulate different scenarios, test new packaging configurations, optimize line parameters, conduct predictive analytics on equipment health, and train operators in a risk-free environment before implementing changes on the actual line.3 Pesmel, for example, uses simulation modeling extensively in their system design and optimization processes.41
B. Advancements in VCI Technology and Protective Materials
Vapor Corrosion Inhibitor (VCI) technology remains a cornerstone of protecting steel coils from rust, and innovations continue to enhance its effectiveness and safety.
- New VCI Formulations: There is ongoing development of more advanced VCI formulations. This includes a shift towards nitrite-free VCI products to address health and environmental concerns, as well as bio-based VCIs derived from renewable resources. Multi-metal VCIs that can protect a wider range of ferrous and non-ferrous metals are also becoming more common, offering greater versatility.3
- High-Strength VCI Films and Papers: To withstand the rigors of handling and transport, manufacturers are developing VCI-impregnated films and papers with improved mechanical properties, such as higher tear resistance and puncture strength. ZERUST, for instance, offers products like ICT® VCI Scrim Paper and Plastic Scrim, which are reinforced for durability.25
- Combined Functionality Materials: Packaging materials are being designed to offer multiple protective functions in a single product. This includes VCI agents integrated directly into stretch films23, VCI papers laminated with polyethylene or wax coatings for enhanced moisture barrier properties65, or VCI papers reinforced with scrim layers for added strength and durability.65 This simplifies the packaging process and can reduce the number of different materials required.
C. Sustainable Packaging Materials and Methods
Sustainability is a major driver of innovation in the steel coil packaging industry, influencing material choices, packaging design, and operational practices.
- Eco-Friendly Materials: There is a significant trend towards adopting packaging materials with a lower environmental impact. This includes the development and use of biodegradable or compostable films and coatings, an increased focus on paper-based solutions as alternatives to conventional plastics, and a push for higher recycled content in plastic packaging components like edge protectors and strapping.3 GWP, for example, offers Bio VCI corrugated packaging made from FSC certified materials, highlighting a move towards renewable and responsibly sourced options.66
- Recyclability and Circular Economy: Designing packaging for easy disassembly and recycling of its components is crucial for supporting a circular economy. This involves selecting materials that are readily recyclable and avoiding combinations of materials that hinder the recycling process.3 The high recyclability of steel itself is an advantage, and packaging should not impede this.67
- Material Minimization (Source Reduction): Optimizing packaging designs to use the least amount of material necessary while still ensuring adequate product protection is a key sustainability goal. Automated application systems play a vital role here by ensuring precise and consistent use of materials like stretch film and strapping, thereby reducing waste.3 Pesmel’s TEW technology, for example, is cited as offering 20-30% savings in packing materials.28
- Reusable Packaging Systems: For closed-loop supply chains or internal transfers, the use of durable, reusable packaging systems, such as custom-designed steel containers or specialized frames, can drastically reduce the consumption of single-use packaging materials and associated waste.3
- VCI as an Environmentally Preferable Alternative to Oils: The use of VCI packaging is often promoted as a more sustainable alternative to traditional rust-preventative oils and greases. VCI protection eliminates the need for oil application and subsequent messy, costly, and often environmentally problematic degreasing processes at the recipient’s end.65
D. Further Evolution of Robotics and AI in Packing Operations
Robotics and Artificial Intelligence are set to play an even more significant role in future steel coil packing lines, driving further improvements in efficiency, flexibility, and intelligence.
- Enhanced Robotic Capabilities: Future robotic systems are expected to feature more sophisticated sensing capabilities (e.g., advanced vision systems, tactile sensors), greater adaptability to varying tasks and coil types, and easier programming interfaces, possibly including teach-less programming or AI-assisted path planning. This will enable robots to handle more complex and less structured packaging tasks.3
- AI-Driven Optimization and Decision-Making: AI algorithms will become more deeply embedded in the control systems of packing lines. They will be used for real-time decision-making, such as dynamically optimizing material usage based on coil characteristics, adjusting line speeds to match upstream or downstream capacities, and proactively adapting to variations in production schedules or material availability.3
- Human-Robot Collaboration (Cobots): The development and deployment of collaborative robots (cobots) may increase in packing applications. Cobots are designed to work safely alongside human operators, combining human dexterity and problem-solving skills with robotic strength, endurance, and precision for tasks that are difficult to fully automate or require a degree of flexibility.
- Predictive Quality Assurance: AI, particularly when combined with advanced sensor data, will move beyond simple defect detection to predictive quality assurance. By analyzing process parameters and material characteristics, AI systems could predict potential quality issues before they manifest, allowing for preemptive adjustments to the packing process.
The drive towards sustainability in steel coil packaging is not merely a trend focused on "greener" materials; it represents a multi-faceted approach to minimizing environmental impact while enhancing operational and economic efficiency. This broader perspective encompasses resource efficiency in material usage, as demonstrated by Pesmel’s TEW technology which claims 20-30% material savings.3 It also includes the reduction of waste through optimized packaging designs and precise automated application3, and improving the energy efficiency of the packaging machinery itself.3 Furthermore, the lifecycle impact of the packaging, from raw material sourcing to end-of-life disposal or recycling, is a critical consideration.67
Automation plays a significant role in this sustainable paradigm. Automated systems, by their nature, allow for more precise control over the application of packaging materials, thereby minimizing overuse and scrap.3 Intelligent control systems can optimize energy consumption per unit packed. Regulatory pressures, such as Extended Producer Responsibility (EPR) schemes and carbon pricing, are increasingly compelling companies to adopt these sustainable practices.3 Concurrently, market demand is shifting, with customers, particularly in sectors like automotive, showing a preference for suppliers who can demonstrate a commitment to lower environmental footprints.3
This convergence of regulatory, market, and economic drivers implies that future investments in steel coil packing lines will be increasingly scrutinized for their sustainability credentials. This evaluation will extend beyond the choice of packaging materials to include the energy efficiency of the equipment, the intelligence of its control systems in minimizing waste, and the overall design’s compatibility with circular economy principles. Suppliers who can offer solutions that are both economically attractive (through TCO and ROI) and environmentally responsible will undoubtedly possess a significant competitive advantage. This also suggests that traditional ROI calculations may evolve to incorporate "return on sustainability" metrics, reflecting either direct cost savings from resource efficiency or indirect benefits such as enhanced brand reputation, improved market access, and greater resilience against future environmental regulations.
VII. Recommendations for Solution Selection

Selecting the optimal steel wire coil packing line is a significant capital investment that requires a strategic and thorough evaluation process. To ensure the chosen solution aligns with operational needs, financial goals, and future growth, several key considerations should be addressed.
A. Assessing Needs and Defining Requirements
Before engaging with suppliers, a comprehensive internal assessment is crucial:
- Production Volume and Coil Characteristics: Accurately evaluate current and projected future production volumes. Detail the range of coil types to be handled, including dimensions (ID, OD, width), weight, and material composition (e.g., specific grades of steel wire, susceptibility to damage or corrosion).1
- Packaging Specifications: Clearly define the required packaging specifications. This includes the types of protective materials needed (e.g., VCI paper, stretch film, strapping type), the number of layers, specific wrapping or strapping patterns, and any customer-mandated packaging standards, especially for export or long-term storage.
- Operational Pain Points and Objectives: Identify existing bottlenecks in the current packing process (if any), sources of product damage, safety concerns related to manual handling, and areas where labor costs are high. Define clear objectives for the new packing line, such as desired throughput rates, target automation levels, and specific improvements in efficiency or quality.
- Facility and Integration Constraints: Consider the physical layout of the facility, the available floor space for the new line, ceiling height restrictions, and the location of utility connections. Crucially, map out the integration points with upstream processes (e.g., output from slitters or drawing lines) and downstream operations (e.g., warehousing, dispatch areas).1
B. Key Criteria for Evaluating Suppliers and Quotations
Once requirements are defined, a structured approach to evaluating suppliers and their proposals is necessary:
- Technical Suitability and Robustness: Assess whether the proposed solution comprehensively meets all defined technical requirements. Evaluate the robustness of the equipment design, the quality of materials used in construction, the proven reliability of key components (e.g., motors, drives, control systems), and the overall technological sophistication of the line.1
- Supplier Experience and Reputation: Investigate the supplier’s experience specifically within the steel coil or wire industry. Look for a proven track record of successful installations of similar scale and complexity.9 Request references, case studies, and potentially site visits to see their equipment in operation.53
- Level of Automation and Integration Capability: The supplier’s ability to deliver the desired level of automation is critical. For highly automated lines, assess their expertise in system integration, including interfacing the packing line with existing plant Manufacturing Execution Systems (MES), Enterprise Resource Planning (ERP) systems, and potentially IoT platforms for data exchange and smart factory initiatives.1
- Customization vs. Standard Solutions: Determine if a standard, off-the-shelf solution from the supplier will suffice or if significant customization is required to meet unique needs. Evaluate the supplier’s willingness and capability to provide tailored engineering and design modifications.1
- Total Cost of Ownership (TCO) and Return on Investment (ROI) Projections: Do not focus solely on the initial purchase price. Request detailed TCO calculations from potential suppliers, covering acquisition, operational, and maintenance costs over the expected lifecycle of the equipment. Similarly, ask for support in developing realistic ROI projections, and carefully scrutinize all assumptions made in these financial analyses.44
- After-Sales Support and Maintenance: Evaluate the supplier’s provisions for after-sales service. This includes the availability and cost of spare parts, the responsiveness and expertise of their technical support teams, the terms of warranty, and the availability of service contracts and operator/maintenance training programs.61
- Safety Standards and Compliance: Ensure that the proposed packing line design adheres to all relevant local and international safety regulations and standards for industrial machinery.
- Sustainability Features: Consider the environmental impact of the proposed solution. This includes the energy efficiency of the equipment, its ability to minimize packaging material waste, and its compatibility with sustainable or recyclable packaging materials.
C. Considerations for Future-Proofing Investments
Investing in a steel wire coil packing line is a long-term commitment. Therefore, it is essential to consider factors that will ensure the system remains effective and adaptable in the years to come:
- Scalability and Modularity: Opt for systems that offer a degree of scalability to accommodate future increases in production volume or changes in product mix. Modular designs, where components or sections of the line can be upgraded or added relatively easily, provide greater flexibility for future expansion or adaptation.20
- Technological Adaptability: Favor solutions built on open or widely adopted control architectures and communication protocols. This makes it easier to incorporate new technologies, such as advanced sensors, AI-driven optimization tools, or updated software, as they become available and economically viable. Avoid proprietary systems that may limit future upgrade paths or integration with third-party technologies.
- Data Management and Analytics Strategy: Ensure the system is equipped to capture, store, and transmit relevant operational data. A well-thought-out data management strategy is crucial for leveraging the benefits of Industry 4.0, enabling continuous improvement, predictive maintenance, and deeper integration with broader smart factory initiatives.
The selection of a steel wire coil packing line is a complex decision that goes beyond comparing technical specifications and prices. Given the significant capital outlay and the long-term operational impact, adopting a partnership approach with potential suppliers is highly recommended. Many suppliers in this field emphasize the need for customized or tailored solutions to meet the unique demands of each client’s facility and product range.1 For instance, Fhopepack explicitly mentions working closely with clients to assess their specific packaging requirements44, and Pesmel highlights their strength in engineering individual solutions.41 The SHJLPack case study, which detailed a 30% reduction in downtime through a customized packing line, powerfully illustrates the benefits of a solution designed with a deep understanding of specific operational needs and challenges.53
Standard, "off-the-shelf" solutions, while potentially less expensive upfront, may not always deliver optimal performance or adequately address all the nuances of a particular production environment.53 Achieving the best possible TCO and ROI often hinges on implementing a solution that is precisely aligned with the user’s operational context, production goals, and integration requirements. This level of alignment typically requires a collaborative engineering effort and an open dialogue between the buyer and the supplier.
Therefore, businesses should seek suppliers who are willing to act as long-term partners rather than mere equipment vendors. Such partners invest the time to thoroughly understand the client’s specific challenges and objectives, offer transparent and detailed cost-benefit analyses for proposed solutions, demonstrate flexibility in design and customization, and commit to robust after-sales support, including training, maintenance services, and future upgrade paths. The evaluation process should, consequently, place significant weight on a supplier’s consultative capabilities, their proven experience in similar applications, and their demonstrated willingness to co-create an optimized packing solution that delivers sustained value.
VIII. Conclusion

The implementation or upgrade of a steel wire coil packing line represents a strategic undertaking with far-reaching implications for product quality, operational efficiency, cost management, and workplace safety within the steel and metals processing industries. As this report has detailed, the solutions available range from basic semi-automated components to highly sophisticated, fully integrated lines incorporating robotics, advanced sensor technology, and smart data management systems.
The choice of technology and the level of automation are primary determinants of both the initial investment and the long-term operational benefits. While manual and semi-automatic systems offer lower upfront costs, fully automatic lines, despite their higher initial price, typically deliver superior throughput, consistency, labor savings, and safety, leading to a more favorable Total Cost of Ownership and Return on Investment over the equipment’s lifecycle. The critical financial analyses of TCO and ROI must therefore extend beyond a simple comparison of purchase prices to encompass all lifecycle costs and quantifiable benefits.
Key trends shaping the future of steel wire coil packaging include the relentless drive towards greater automation and system integration, the incorporation of Industry 4.0 principles (IoT, AI, Digital Twins) for enhanced intelligence and predictive capabilities, and a growing imperative for sustainable packaging solutions. Innovations in protective materials, particularly advanced VCI formulations and eco-friendly alternatives, alongside the evolution of robotics and AI, promise to further optimize packing operations.
Ultimately, the selection of a steel wire coil packing solution demands a thorough assessment of specific operational needs, a clear definition of objectives, and a careful evaluation of supplier capabilities. A partnership approach with suppliers who can offer tailored, future-proof solutions and robust long-term support is crucial. By making well-informed, strategic decisions, companies can leverage advanced steel wire coil packing technology not just as a means of product protection, but as a significant contributor to overall productivity, profitability, and competitive advantage in a dynamic global market.
Works cited
-
How To Choose The Right Coil Packing Line, accessed May 29, 2025, https://www.shjlpacking.com/info/how-to-choose-the-right-coil-packing-line-102896431.html
-
Coil Packing Line Showcase and Technical Information -Fhope, accessed May 29, 2025, https://www.fhopepack.com/coil-packing-line/
-
Steel Coil Packing Future Trends – FHOPEPACK, accessed May 29, 2025, https://www.fhopepack.com/zh/steel-coil-packing-future-trends/
-
Products / Automatic Packing Line / Coil Packing Line – SHJLPACK, accessed May 29, 2025, https://www.shjlpack.com/products-and-production/coil-packing-line/
-
Upender/Downender – Metal Processing Machinery-ADS Machinery, accessed May 29, 2025, https://adsmachinery.com/upender/
-
www.arcon-metals.sk, accessed May 29, 2025, https://www.arcon-metals.sk/MediaLibrary/arcon-metals/arcon-metals/Pdf/pdf30.pdf
-
Handling and Transport Systems – Steel reels/coils, accessed May 29, 2025, https://www.ctisystems.com/reels-coils-steel/handling-and-transport-systems-en/
-
Pallet conveyor system for hot-rolled coils – Amova, accessed May 29, 2025, https://www.amova.eu/en/references/detail/pallet-conveyor-system-for-hot-rolled-coils
-
Wire – Sund Birsta, accessed May 29, 2025, https://www.sundbirsta.com/productcategories/wire/
-
Material Handling Products – Brilex Industries, accessed May 29, 2025, https://www.brilex.com/capabilities/engineering/material-handling-products/
-
Equipment for the prevention of telescopicity in coils (COILFORM) – Ingeniería TPI, accessed May 29, 2025, https://ingenieriatpi.com/en/projects/equipment-for-the-prevention-of-telescopicity-in-coils-coilform/
-
Hydraulic Press vs Mechanical Press: Which is Better? – HARSLE, accessed May 29, 2025, https://www.harsle.com/docs/hydraulic-press-vs-mechanical-press/
-
PRE-LOAD COMPACTOR OPERATION AND SERVICE MANUAL – Oregon Metro, accessed May 29, 2025, https://www.oregonmetro.gov/sites/default/files/2019/01/14/Metro_TS-SSI_Compactor_Services_Manual.pdf
-
Wire Rod Compactor | Signode, accessed May 29, 2025, https://www.signode.com/en-us/productslist/wire-rod-compactor/
-
www.primetals.com, accessed May 29, 2025, https://www.primetals.com/fileadmin/user_upload/content/01_portfolio/4_hot-rolling-long/rod-mill/COIL_HANDLING_AND_COMPACTING_SYSTEMS.pdf
-
Poly & Steel Strapping Guide – Packaging Equipment Automation and Damage Prevention, accessed May 29, 2025, https://info.ipack.com/guide/definitive-strapping-guide
-
Coil Packing Lines | Signode, accessed May 29, 2025, https://www.signode.com/en-us/industries/metals/coil-packing-lines/
-
Semi-automatic strapping machines – Linder Strapping, accessed May 29, 2025, https://linder-strapping.com/en/strapping-machines/semi-automatic-strapping-machines
-
Application-Specific Strapping Machines – Signode, accessed May 29, 2025, https://www.signode.com/en-us/products/strapping-systems/application-specific-strapping-machines/
-
Logistics systems for the metals industry – SMS group GmbH, accessed May 29, 2025, https://www.sms-group.com/plants/logistics-systems
-
Packing lines for coils – Products – Novastilmec – Novastilmec S.p.A., accessed May 29, 2025, https://www.novastilmec.com/en/products/packing-lines/
-
Compacting And Wrapping 200-300mm Wire Coil Packing Machine …, accessed May 29, 2025, https://www.cnsuntech.com/quality-13730510-compacting-and-wrapping-200-300mm-wire-coil-packing-machine-for-wire-coil
-
VCI stretch film, VCI wrapping film, VCI machine stretch film – EXCOR, accessed May 29, 2025, https://www.excor.com/products/vci-films/vci-stretch-film
-
VCI Power Stretch – RUSTX, accessed May 29, 2025, https://rustx.net/shop/vci-power-stretch/
-
Heavy-Duty, High-Strength VCI Packaging Solutions for the Metal Coil Industry – Zerust, accessed May 29, 2025, https://www.zerust.com/industries/vci-metal-coil/
-
Steel Coil Packaging – RUSTX, accessed May 29, 2025, https://rustx.net/product-category/steel-coil-packaging/
-
Vci Paper For Steel Coils(78+) – Alibaba.com, accessed May 29, 2025, https://www.alibaba.com/showroom/vci-paper-for-steel-coils.html
-
pesmel.com, accessed May 29, 2025, https://pesmel.com/wp-content/uploads/2022/01/ENG_Metal_brochure_v3_Spreads_S.pdf
-
Automatic horizontal steel coil packing lines – taiwan metiz alliance, accessed May 29, 2025, https://metiz.tw/packing-horizontal-steel-coil.html
-
Coil packing machines & Automatic coiler | Shjlpack, accessed May 29, 2025, https://www.shjlpack.com/products-and-production/
-
Fully Auto Steel Wire Coil Packing Machine Metal Wire Coil Film Winding Wrapping Packaging Machine – Steel Wire Packing Machine, Wire Wrapping Machine | Made-in-China.com – Anhui Dixin Machinery Technology Co., Ltd, accessed May 29, 2025, https://dixinmachine.en.made-in-china.com/product/hxiUJTwCOSrG/China-Fully-Auto-Steel-Wire-Coil-Packing-Machine-Metal-Wire-Coil-Film-Winding-Wrapping-Packaging-Machine.html
-
Automated Steel Labeling Systems | Pannier Corporation, accessed May 29, 2025, https://www.pannier.com/tags/attaching-systems/automatic/polytec-steel-tagging-systems/
-
Coil Marking & Labelling – Tebulo Robotics, accessed May 29, 2025, https://www.tebulorobotics.com/products/coil-marking-labelling/
-
Products › Long › Drawing Plants High-speed chain track drawing …, accessed May 29, 2025, https://www.danieli.com/en/products/products-processes-and-technologies/slab-continuous-casting_26_9.htm
-
Automatic Cable Coiling and Wrapping | Cable Packaging Machine …, accessed May 29, 2025, http://wirecable-solution.com/3-5-automatic-cable-coiling-and-wrapping-machine.html
-
Advanced packaging and palletising line for welding wire coils – Imanpack, accessed May 29, 2025, https://www.imanpack.com/en/news/advanced_packaging_and_palletising_line_for_welding_wire_coils
-
Everything You Need to Know About Coil Racks: Specialty Storage Solutions for Coils, accessed May 29, 2025, https://www.wprpwholesalepalletrack.com/everything-you-need-to-know-about-coil-racks-specialty-storage-solutions-for-coils/
-
How to Do Steel Coil Packing: A Comprehensive Guide – FhopePack, accessed May 29, 2025, https://www.fhopepack.com/zh/how-to-do-steel-coil-packing-a-comprehensive-guide/
-
D4 Industry and Tosyali Toyo: Optimizing steel coil handling with smart tracking – Wirepas, accessed May 29, 2025, https://wirepas.com/cases/optimizing-steel-coil-handling-with-smart-tracking/
-
The AI Revolution: Transforming the Steel Industry Through Automation, Robotics, and Smart Manufacturing, accessed May 29, 2025, https://steelindustry.news/the-ai-revolution-transforming-the-steel-industry-through-automation-rohttps://steelindustry.news/the-ai-revolution-transforming-the-steel-industry-through-automation-robotics-and-smart-manufacturing/botics-and-smart-manufacturing/
-
Metal industry – Pesmel Oy, accessed May 29, 2025, https://pesmel.com/solutions/metal-industry/
-
20240051692 Robot system and method for coil packaging – WIPO Patentscope, accessed May 29, 2025, https://patentscope.wipo.int/search/ar/detail.jsf;jsessionid=F77B36FA0D8FEF710C5988A58DBBB3F2.wapp2nB?docId=US422367886&_cid=P21-LSW7WG-46460-56
-
Advanced Automation in Steel Coil Packing Lines – wrapping …, accessed May 29, 2025, https://www.shjlpack.com/info/advanced-automation-in-steel-coil-packing-lines/
-
Decoding the Determinants of Coil Packing Machine Price: A …, accessed May 29, 2025, https://www.fhopepack.com/zh/decoding-the-determinants-of-coil-packing-machine-price-a-manufacturers-analysis/
-
What Are the Factors Affecting the Price of Steel Wire Drawing Machine?, accessed May 29, 2025, https://www.wiremachinecn.com/factors-affecting-the-price-of-steel-wire-drawing-machine.html
-
Pallet changer machine & systems | inline & stationary | Baust, accessed May 28, 2025, https://www.baust.de/en/products/material-flow-systems/pallet-changers/
-
Color Coated Steel Coil Price: Factors Affecting – POWERSON METAL, accessed May 29, 2025, https://www.xzpowerson.com/color-coated-steel-coil-price-factors-affecting/
-
Understanding the Total Cost of Ownership in Packaging – Paramount Global, accessed May 29, 2025, https://www.paramountglobal.com/knowledge/total-cost-ownership-packaging/
-
A Quick Guide to Calculating ROI and TCO – Premier Tech Chronos, accessed May 29, 2025, https://www.ptchronos.com/blog/how-to-calculate-tco-and-roi
-
How to Calculate the Total Cost of Ownership (TCO) for Packaging Lines and Machinery, accessed May 29, 2025, https://www.bwpackaging.com/blog/post/blog/2022/01/21/tco-packaging-lines–machinery
-
Evaluating the ROI of ASRS: A Data-Driven Approach for Supply Chain Professionals, accessed May 29, 2025, https://www.streamliners.us/evaluating-the-roi-of-asrs-a-data-driven-approach-for-supply-chain-professionals/
-
Calculating a Strong ROI for Packaging Equipment – InkJet, Inc., accessed May 29, 2025, https://inkjetinc.com/blogs/default-blog/calculating-a-strong-return-on-investment-for-packaging-equipment
-
Case Study: How We Reduced Downtime by 30% with a Customized Steel Coil Packing Line – wrapping machine manufacturer – SHJLPACK, accessed May 29, 2025, https://www.shjlpack.com/info/case-study-how-we-reduced-downtime-by-30-with-a-customized-steel-coil-packing-line/
-
What is the ROI On a Portable Metal Roof Panel Machine? – New Tech Machinery, accessed May 29, 2025, https://newtechmachinery.com/learning-center/what-is-the-roi-for-a-portable-metal-roof-panel-machine/
-
Pesmel supplies packing lines to Baosteel Group — Trade Fair – METEC, accessed May 29, 2025, https://www.metec-tradefair.com/en/Media_News/News/Pesmel_supplies_packing_lines_to_Baosteel_Group
-
Innovative technologies and solutions for the steel industry, accessed May 29, 2025, https://www.fivesgroup.com/steel
-
Pickling lines for environmentally responsible operation – Fives Group, accessed May 29, 2025, https://www.fivesgroup.com/steel/strip-processing/pickling-lines
-
accessed December 31, 1969, https://www.danieli.com/en/products/long-products/drawing-plants/drawing-plants_79_66.htm
-
k-spool – Danieli, accessed May 29, 2025, https://www.danieli.com/en/news-media/news/k-spool_37_411.htm
-
Technological packages – Danieli, accessed May 29, 2025, https://www.danieli.com/en/products/technological-packages.htm
-
Coil packaging lines – Amova, accessed May 29, 2025, https://www.amova.eu/en/steel-industry/products/detail/coil-packaging-lines
-
accessed December 31, 1969, https://www.sms-group.com/plants/logistics-systems/transport-storage-and-packaging-systems/packaging
-
accessed December 31, 1969, https://www.sms-group.com/plants/logistics-systems/transport-storage-and-packaging-systems/packaging/
-
Products – Amova, accessed May 29, 2025, https://www.amova.eu/en/products/metals-industry
-
Coil Packaging Materials: What You Need to Know – FhopePack, accessed May 29, 2025, https://www.fhopepack.com/zh/coil-packaging-materials-what-you-need-to-know/
-
VCI Packaging | Cost-effective alternative to VCI bags and films – GWP Group, accessed May 29, 2025, https://www.gwp.co.uk/coatings/vci-packaging/
-
Steel Industry Packaging Best Practices for Sustainability – EOXS, accessed May 29, 2025, https://eoxs.com/new_blog/steel-industry-packaging-best-practices-for-sustainability/