Optimizing Coil Yard Management for Better Efficiency
Are cluttered coil yards costing you time, money, and risking safety? Inefficient coil handling is a major bottleneck in steel operations, leading to damaged inventory, delayed production, and increased operational costs. It’s time to transform this critical area.
Optimizing coil yard management for better efficiency involves integrating advanced Warehouse Management Systems (WMS), leveraging automation for tracking and handling, implementing high-density storage solutions, prioritizing stringent safety protocols, and committing to continuous process improvement.
Unlock the full potential of your facility by mastering the principles of modern coil yard management. Read on to discover how strategic improvements can boost your throughput, enhance safety, and drive profitability.
Enhancing Efficiency Through Advanced Equipment and Handling Techniques
Struggling with slow, hazardous coil handling? Outdated equipment and poor techniques are bottlenecks that directly impact efficiency and safety in the coil yard. Selecting the right tools and ensuring skilled operation are non-negotiable for smooth operations.
Enhancing efficiency in coil yard management hinges on adopting specialized lifting equipment like automated cranes with tailored grippers or magnets and ensuring operators are expertly trained in safe, precise handling techniques. This minimizes damage, speeds up movements, and prevents costly accidents.
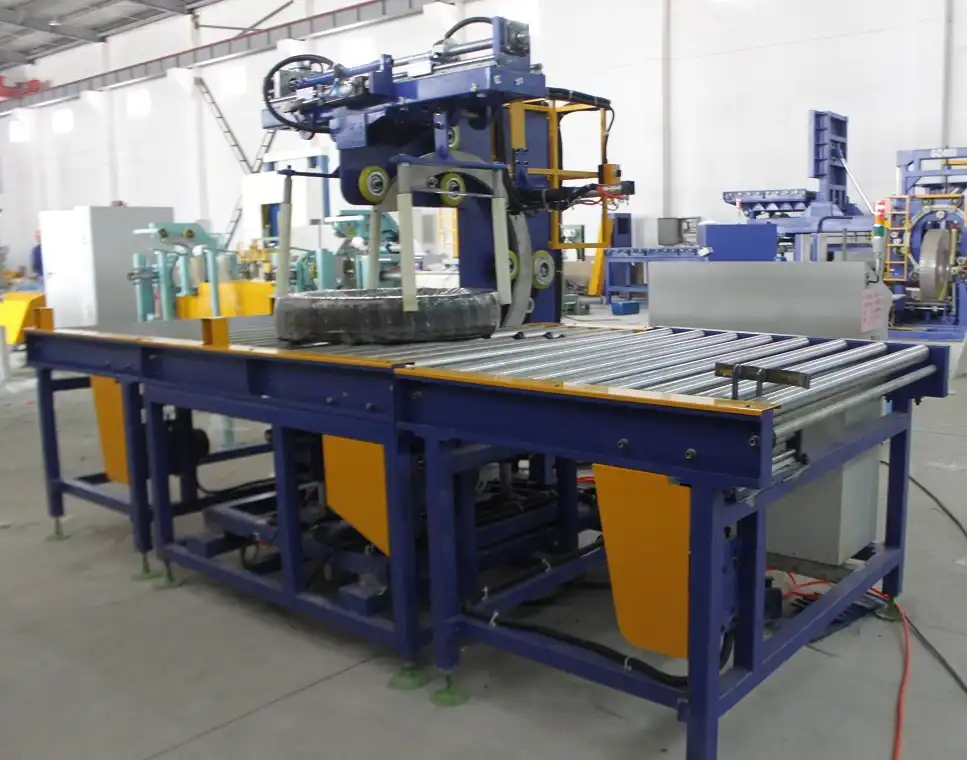
The Synergy of Specialized Equipment and Expert Operation
Efficient handling of heavy steel coils requires a combination of purpose-built machinery and well-trained personnel. Investing in equipment designed for the specific challenges of coil manipulation is the first step. Options range from sophisticated overhead cranes integrated with WMS for automated movements to forklifts fitted with robust coil rams or C-hooks for more manual operations. The choice depends on the scale, volume, and automation level desired. Cranes equipped with features like load stabilization and precise positioning systems drastically improve handling speed and accuracy. Mechanical grippers or strong magnets ensure secure lifting without damaging the coil surface.
Proper training is equally vital. Operators must be proficient in using the chosen equipment safely and effectively. This includes understanding load limits, recognizing potential hazards, and executing lifts with smooth, controlled movements to prevent swinging or dropping, which can cause significant damage or injury. Techniques like lifting from the coil’s core (eye-to-the-sky or eye-horizontal) where possible, rather than the outer edges, are essential to prevent deformation. Regular maintenance and inspection of all lifting gear are paramount to ensure reliable performance and safety compliance. Combining advanced, well-maintained equipment with skilled operators creates a high-performance handling system that minimizes downtime and maximizes throughput.
Here’s a comparison of handling approaches:
Feature | Manual Forklift with Attachment | Standard Overhead Crane w/ Hook | Automated Overhead Crane w/ Gripper/Magnet |
---|---|---|---|
Initial Cost | Low | Medium | High |
Operating Speed | Slow to Medium | Medium | Fast |
Precision | Low | Medium | High |
Risk of Coil Damage | Higher (operator dependent) | Medium (hook swing) | Lower (controlled grip/placement) |
Safety | Moderate (operator dependent) | Moderate (swing hazards) | High (automated, integrated safety) |
Integration with WMS | Limited | Limited | High (direct command & feedback) |
Labor Dependency | High | Medium | Low |
Throughput Potential | Low | Medium | High |
Ideal Application | Low volume, flexible needs | Medium volume, diverse loads | High volume, standardized coils |
Implementing a WMS connected to automatic cranes enables automated transport orders, optimizes operating times, and provides real-time information on crane and system statuses. This allows for streamlined operations, significantly reducing manual intervention and the potential for human error. Coil data is automatically recorded and accessible, further enhancing efficiency.
Revolutionizing Coil Storage Practices for Maximized Space and Accessibility
Is your coil storage a chaotic mess, leading to lost time searching for coils and potential damage? Traditional floor stacking or basic racking solutions are inefficient and hazardous, limiting capacity and complicating inventory management.
Revolutionizing coil storage practices involves transitioning to high-density vertical or horizontal racking systems specifically designed for coils, maximizing space utilization, improving accessibility, and significantly enhancing safety by preventing rolling or tipping.

From Clutter to Clarity: Embracing High-Density Storage Solutions
Moving beyond the limitations of traditional coil storage methods is crucial for achieving high efficiency. Simple floor stacking consumes vast amounts of floor space, restricts access to lower layers (requiring hazardous "digging out" with manual methods), and presents significant safety risks from unstable stacks. Basic pallet racks are often not designed to safely support the concentrated weight and cylindrical shape of coils, leading to structural issues and potential coil damage.
Modern, specialized coil storage systems offer a paradigm shift. These include heavy-duty cantilever racks, vertical "tree" racks, or systems utilizing dedicated cartridges or drawers. These solutions are engineered to support the unique load characteristics of coils and offer key benefits:
- Space Optimization: Vertical designs dramatically reduce the required floor footprint compared to horizontal floor storage, allowing for much higher storage density within the same area. Systems can store coils up to multiple layers high, utilizing vertical space effectively.
- Improved Accessibility: Many modern systems, especially those with independent storage positions (like cartridges in a tiered rack or dedicated cradles), allow for selective retrieval. This means any coil can be accessed directly without moving other coils, streamlining operations and supporting efficient inventory rotation like First-In, First-Out (FIFO).
- Enhanced Safety: Dedicated storage cradles, chocks, and secure racking structures prevent coils from rolling, shifting, or tipping – major hazards associated with floor stacking. Organized storage areas also reduce clutter and improve traffic flow for personnel and equipment.
- Material Preservation: Storing coils on appropriate supports prevents deformation, edge damage, and contact with corrosive floor surfaces. Vertical storage (eye-to-the-sky) is often favored for preventing edge damage.
- Better Inventory Management: Organized storage with clear labeling facilitates accurate inventory tracking and management. This is often integrated with WMS to provide real-time visibility of coil locations and status.
Automated coil warehouses managed by a WMS can store coils automatically up to three layers high and retrieve them on request. The system can even automatically dig out coils not in the uppermost layer by relocating coils above them, a process that is hazardous and slow with manual methods. This level of automation, combined with optimized storage strategies (e.g., based on size, weight, or required retrieval sequence), significantly boosts productivity and safety.
Prioritizing Safety for a Secure and Productive Coil Yard
Overlooking safety protocols in coil yard management is not just a risk to personnel; it’s a direct impediment to efficiency. Accidents cause downtime, damage, and increased costs, disrupting the entire workflow.
Prioritizing steel coil safety requires a multi-faceted approach encompassing mandatory PPE, comprehensive training on handling hazards, rigorously maintained equipment, organized storage areas with proper chocking, and adherence to industry regulations.
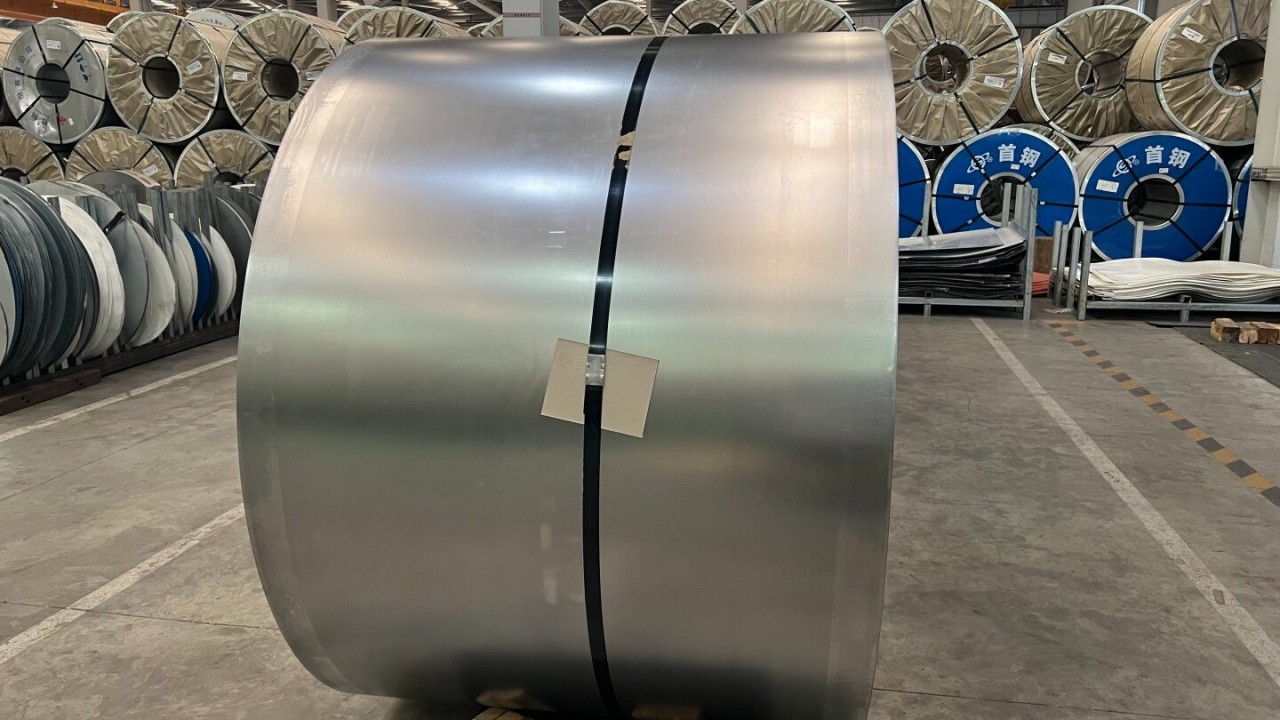
Building a Foundation of Safety in Coil Handling and Storage
A safe coil yard is an efficient coil yard. When operators are properly trained, equipped, and working in a secure environment, they perform their tasks with greater confidence and accuracy, reducing errors and preventing incidents that lead to delays. Establishing a robust safety culture involves addressing three key areas: Personnel, Equipment, and Environment.
Personnel Safety Measures
- Training: Regular, comprehensive training is essential. This includes training on specific equipment use (cranes, forklifts, grippers), safe lifting and placement techniques for coils, hazard recognition (pinch points, unstable loads, slip hazards), emergency procedures, and understanding load capacities.
- PPE: Strict enforcement of Personal Protective Equipment is critical. This typically includes hard hats, safety glasses, heavy-duty gloves, and steel-toed safety boots.
- Communication: Clear communication protocols between operators, ground personnel, and supervisors are vital, especially during complex movements. Use of signals and two-way radios can enhance safety.
Equipment Safety Measures
- Maintenance: Implementing a rigorous preventive maintenance schedule for all handling equipment (cranes, forklers, lifters) is paramount. This ensures equipment is in good working order, reducing the risk of mechanical failure during operation.
- Load Limits: Always adhere to the safe working load limits of equipment and storage systems. Overloading is a major cause of accidents and equipment damage.
- Automated Safety Features: Utilizing equipment with built-in safety features like overload protection, anti-sway systems, and collision avoidance technology significantly enhances safety, especially in automated environments.
Environmental Safety Measures
- Layout & Organization: The coil yard layout should ensure adequate aisle space for safe movement, designated pedestrian walkways, and clear exclusion zones around handling operations. Storage areas must be kept clean, free of debris, and well-lit.
- Secure Storage: Use appropriate chocks, blocks, or engineered racks to prevent coils from rolling. Storage surfaces must be level and capable of supporting the load. Vertical storage is often preferred for stability and space-saving.
- Signage: Clear signage indicating hazards, required PPE, load capacities, and traffic flow directions is essential.
Adherence to relevant industry standards and regulations is not just a legal requirement but a framework for best practices. Examples include:
Standard/Regulation | Focus | Relevance to Coil Yard Safety |
---|---|---|
OSHA 29 CFR 1926.250 | General Storage Requirements | Requirements for safe stacking and storage of materials, aisle width, housekeeping. |
OSHA 29 CFR 1910.179 | Overhead & Gantry Cranes | Safety requirements for design, inspection, maintenance, and operation of cranes used in coil yards. |
ANSI/ASME B30 Series | Safety Standard for Cranes & Lifting Equip. | Provides detailed safety standards for various lifting devices including cranes and hooks. |
ANSI MH16.1 | Industrial Steel Storage Racks | Ensures the structural integrity and safe load capacity of steel racks used for coil storage. |
Local Building Codes | Structural Integrity | Governs the design and construction of the storage facility and rack installations to support heavy loads. |
By embedding these safety measures and fostering a safety-first culture, businesses can drastically reduce incidents, protect their workforce, and create a more reliable and efficient coil yard operation.
Leveraging Automation and Digitalization for Unparalleled Efficiency
Manual processes and poor data visibility cripple coil yard efficiency. Tracking coils on paper, relying on visual inspection, and managing movements without real-time data lead to errors, delays, and suboptimal resource utilization.
Leveraging automation and digitalization with a Warehouse Management System (WMS) is key to unparalleled coil yard efficiency, enabling automated tracking, optimized crane movements, improved inventory accuracy, and seamless integration with production and logistics.
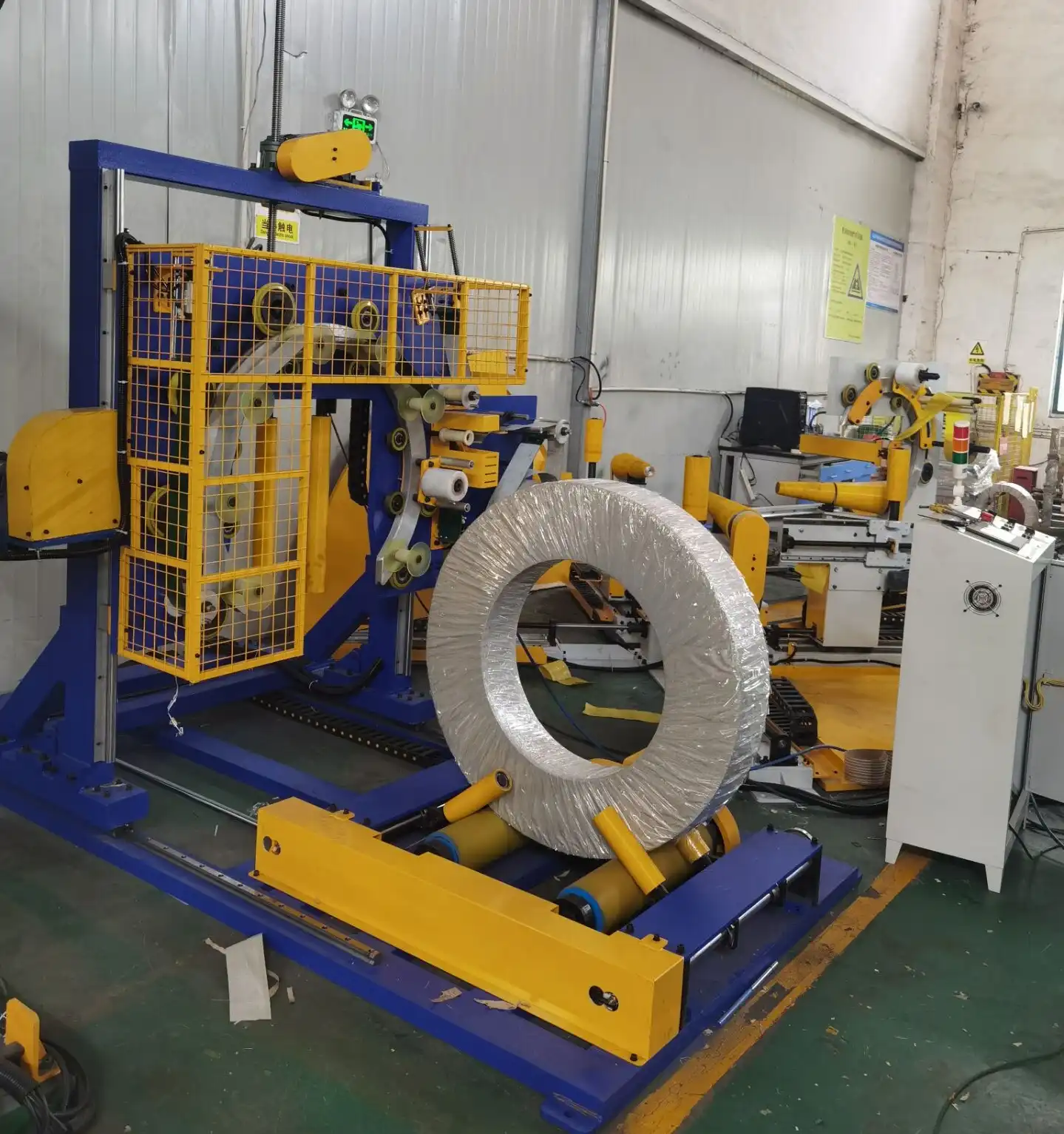
Integrating automation and digitalization solutions like a WMS is transformative for coil yard efficiency. A WMS designed for coil storage manages transport orders, optimizes crane operations, and provides real-time status updates. Steel coil data, often integrated from a host or MES system, is readily accessible, enhancing decision-making. Coils are automatically stored and retrieved based on WMS commands, replacing manual, error-prone processes.
Key modules within an advanced WMS further automate specific functions:
- Yard Management Module (YMM): Controls material flow from arrival points (train, truck) to storage and vice versa. It automates coil registration (often via barcode or vision systems), dimension measurement, and data verification. Operators use mobile devices for data input and location tracking. Automated unloading/loading from trains/trucks, utilizing machine vision to calculate precise pick/deposit positions, significantly speeds up material reception and dispatch.
- Production Management Module (PMM): Manages production orders, priorities, and delivery lines. It ensures the right coils are retrieved from storage and staged for production, automatically managing the retrieval sequence and digging out coils if necessary. This module optimizes the flow of coils to the production line, reducing waiting times.
- Mobile Robot Management Module (MRMM): Manages material flow outside the main storage area using mobile robots. It directs robot movements, tracks their location, ensures safe paths, and integrates with the WMS for inventory updates and routing optimization. This automates material transfer between different areas of the facility, increasing efficiency and safety.
The application of AI and computer vision, as seen in the Primetals Technologies case study at SSAB Hämeenlinna, further enhances efficiency and quality. Systems can automatically identify coils (reading ID numbers, contours) and detect defects (like pickling issues) early in the process. This ensures the correct coils are processed in sequence, preventing production interruptions and scrap. Data from these systems is transmitted to the WMS and automation systems, enabling real-time adjustments and continuous optimization of operations. Simulation models and digital twins are also crucial digital tools. Simulation helps optimize system design, capacity, crane numbers, and operational rules during planning. A digital twin, emulating the physical warehouse, serves as an invaluable tool for identifying bottlenecks, optimizing configurations, and training operators before commissioning, ensuring a smoother startup and ongoing optimization. This suite of digital tools and automation capabilities transforms the coil yard from a potential bottleneck into a highly efficient, data-driven operation.
Continuous Improvement: The Path to Sustained Coil Yard Efficiency
Initial optimizations aren’t the end goal. Sustained efficiency in the coil yard requires ongoing effort, vigilance, and a commitment to refining processes, maintaining equipment, and leveraging data for continuous improvement.
Sustained coil yard efficiency relies on regular inspection and maintenance of storage infrastructure and handling equipment, implementing accurate, real-time inventory tracking, streamlining workflow based on data analysis, and fostering a culture of good housekeeping and proactive problem-solving.
Continuous improvement ensures that the benefits gained from investing in advanced equipment, storage, and automation are maintained and even enhanced over time. This involves establishing routine practices and utilizing the data generated by modern WMS and automation systems. Regular inspections – daily visual checks by operators, weekly checks of equipment and racks, and periodic in-depth audits by experts – are essential to identify wear, damage, or potential issues before they lead to failures, safety hazards, or damage to the stored steel coils. Any issues found must be addressed promptly through documented repair or replacement procedures.
Beyond physical checks, leveraging the data from the WMS is key. Analyzing crane operating data, throughput statistics, retrieval times, and inventory turnover provides insights into potential bottlenecks or areas for optimization. For instance, identifying frequently accessed coil types allows for strategic positioning within the storage system to minimize travel distances. Implementing precise inventory tracking and management systems, ideally integrated with WMS and automated identification (barcode, vision), ensures accurate counts, real-time location data, and supports efficient strategies like FIFO to manage material age and reduce waste. Streamlining workflow involves analyzing the movement of coils from arrival to storage, storage to production, and production to dispatch, identifying and eliminating unnecessary steps or delays. This might involve optimizing routing for cranes or mobile robots, refining picking strategies based on production schedules, or improving staging areas. Finally, maintaining a consistently clean and organized coil yard is fundamental. Good housekeeping reduces slip and trip hazards, prevents equipment blockages, and makes it easier to identify problems during inspections. It also supports efficient navigation and material flow. The collective impact of these ongoing activities ensures the coil yard remains a smooth, safe, and efficient part of the overall operation, directly contributing to the bottom line.
Conclusion
Achieving peak efficiency in your coil yard management is a vital strategic goal that significantly impacts safety, productivity, and profitability. By investing in the right equipment and mastering handling techniques, adopting modern, high-density storage solutions, embedding rigorous safety protocols, and embracing automation and continuous improvement, businesses can transform their coil storage areas. These integrated strategies reduce damage to valuable steel coils, minimize risks to personnel, streamline operational workflows, and ensure faster, more accurate fulfillment, ultimately driving overall manufacturing or processing success.