Managing Coil Packaging Waste: Eco-Friendly Solutions
Coil packaging presents a significant environmental challenge, generating substantial waste from traditional materials. The pressure to adopt sustainable practices is growing. Addressing this waste isn’t just about compliance; it’s about reducing costs, enhancing brand image, and securing the future of manufacturing. Eco-friendly solutions are urgently needed to transform this aspect of the supply chain.
Managing coil packaging waste effectively involves transitioning from traditional, disposable materials to sustainable alternatives like Vapor Corrosion Inhibitor (VCI) technology. VCI papers, films, and covers offer robust protection against rust and corrosion, eliminating the need for messy, hazardous oils and reducing reliance on bulky, non-recyclable packaging layers. This shift minimizes material usage, simplifies disposal, and contributes to a greener supply chain for metal manufacturers.
Transitioning to sustainable coil packaging might seem complex, but innovative solutions exist that simplify the process and offer significant environmental and economic benefits. Let’s explore how modern materials like VCI are revolutionizing the protection and transport of metal coils, offering a win-win for manufacturers and the planet.
The Environmental Burden of Traditional Coil Packaging
Traditional methods for protecting metal coils during storage and transit, often relying on grease, oils, and multi-layer packaging materials, create a substantial environmental burden. These methods not only generate considerable waste requiring complex disposal processes but also introduce hazardous substances into the supply chain, impacting both the environment and worker safety.
Traditional metal coil packaging often involves rust-preventative oils and bulky, non-recyclable materials that contribute significantly to landfill waste and environmental pollution. Applying and removing these oils requires harsh solvents, further compounding the hazardous waste problem. In contrast, VCI packaging eliminates the need for oils entirely, protecting coils with an invisible, non-toxic vapor. This vastly reduces material waste, simplifies recycling, and removes hazardous chemicals from the packaging process, offering a clean, dry, and environmentally superior alternative for long-term corrosion protection and export protection.
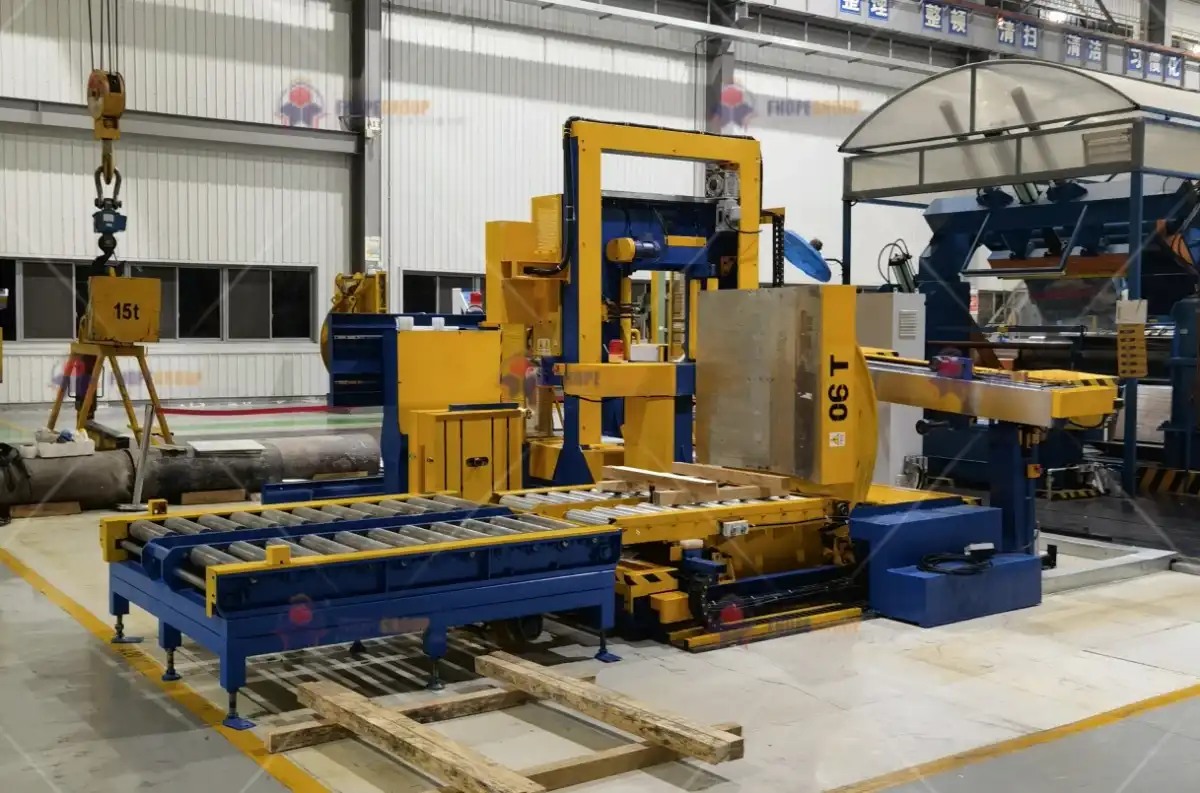
The Hidden Costs of Conventional Corrosion Prevention
Beyond the visible waste, traditional methods carry hidden environmental and economic costs. The widespread use of rust-preventative oils introduces Volatile Organic Compounds (VOCs) into the atmosphere and can contaminate soil and water if not handled and disposed of properly. The materials themselves, often complex laminates or coated papers, can be difficult or impossible to recycle, ending up in landfills. Furthermore, the labor and chemicals required for applying and later removing protective oils add significant operational expenses and safety risks.
Consider the comparison between traditional oil-based protection and modern VCI technology:
Feature | Traditional RP Oils & Packaging | VCI Packaging Solutions | Environmental Impact | Disposal | Cost (Material, Labor, Disposal) |
---|---|---|---|---|---|
Corrosion Protection | Barrier (requires 100% coverage) | Vapor & Contact (reaches all surfaces) | Potential for chemical runoff | Hazardous waste, difficult recycling | High (material, labor, disposal) |
Application/Removal | Messy, labor-intensive (spraying, dipping) | Clean, simple (wrap, bag, cover) | Requires solvents for removal | Easy disposal (recyclable, often biodegradable) | Low (simpler process, less waste) |
Material Composition | Oils, greases, complex laminates/coatings | VCI-impregnated paper, poly film, covers | VOCs, non-recyclable components | Recyclable, non-toxic, often biodegradable | Reduced material use |
Environmental Safety | Hazardous to environment & employees (VOCs, carcinogens, slip hazards) | Non-toxic, nitrite-free, environmentally friendly | Minimal environmental footprint | Simple, safe | Improved safety, lower insurance |
Packaging Waste | High, difficult to recycle | Low, easily recyclable/biodegradable | Significant landfill contribution | Reduced landfill waste | Lower overall waste costs |
Reusability | Oils are single-use; some packaging reusable | Packaging often reusable/recyclable | Limited | Easier re-use/recycling | Potential for re-use savings |
The reliance on outdated practices perpetuates a cycle of waste and environmental concern. Metal parts manufacturers often make common mistakes, such as not properly drying parts, using contaminated cleaning fluids, or allowing parts to come into contact with corrosive packaging materials like untreated wood or cardboard, which can lead to rust and require costly rework or scrapping. These issues are compounded when parts are stored or shipped for extended periods, especially with temperature and humidity fluctuations. Implementing a clean, dry corrosion prevention method like VCI directly addresses many of these pitfalls, preventing rust at the source and significantly reducing waste and associated costs throughout the supply chain.
Introducing VCI: A Cleaner Approach to Coil Protection
The search for more efficient and environmentally responsible methods of protecting metal coils has led to the widespread adoption of Vapor Corrosion Inhibitor (VCI) technology. Unlike traditional methods that create a physical barrier, VCI works on a molecular level, providing comprehensive protection without the mess or environmental hazards associated with oils and greases.
Vapor Corrosion Inhibitor (VCI) technology utilizes specially formulated chemicals impregnated into packaging materials to release protective molecules into the air around metal coils. These molecules bond to the metal surface, forming an invisible, passive layer that prevents corrosive elements like moisture and oxygen from causing rust. This dry, non-toxic process eliminates the need for traditional oils and greases, significantly reducing chemical waste and simplifying handling and disposal of packing materials, making it an ideal eco-friendly solution for coil packaging and export protection.
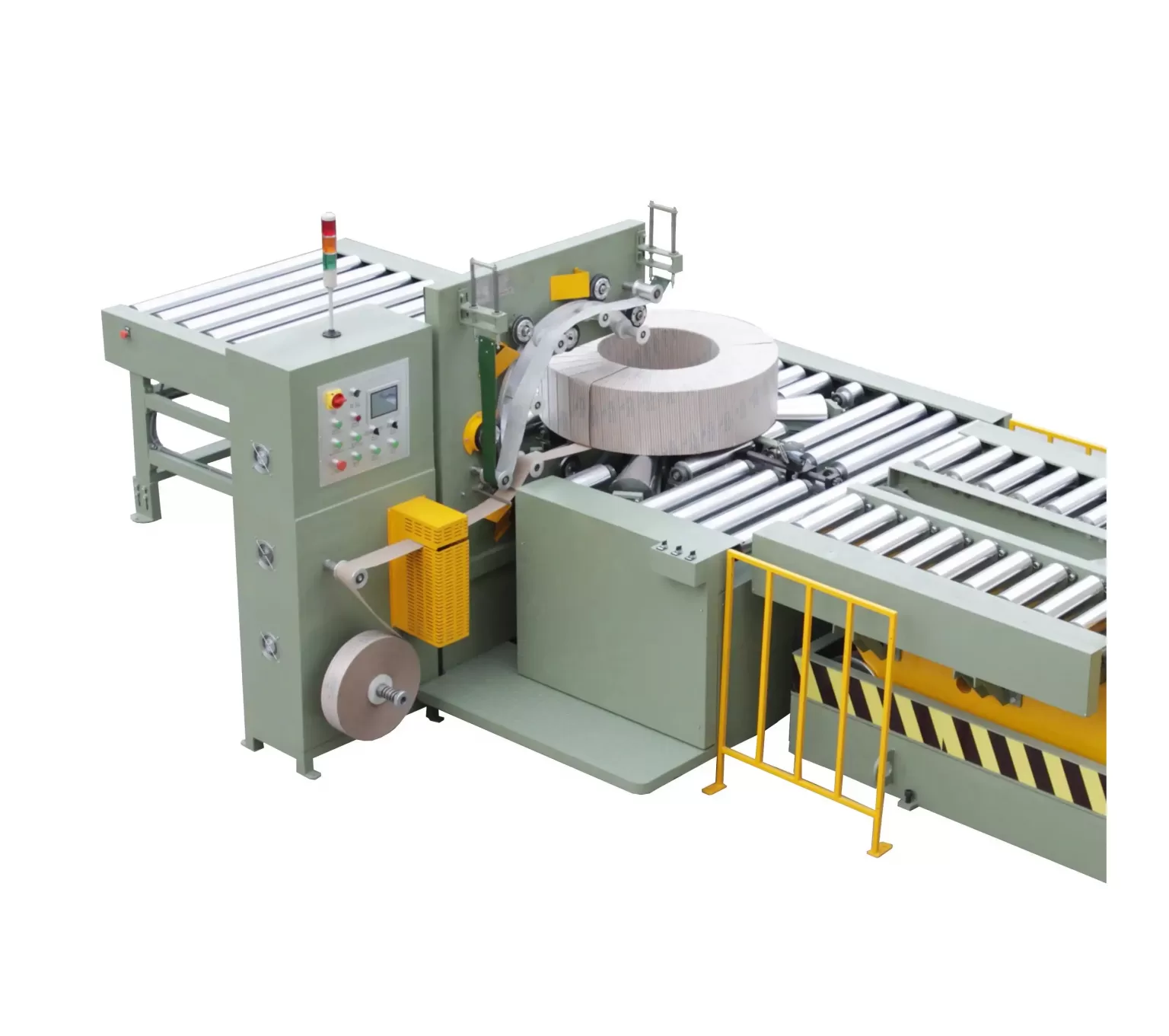
The Science Behind VCI Protection
The effectiveness of VCI technology lies in its unique chemical properties and how it interacts with metal surfaces. VCI compounds have a sufficient vapor pressure at ambient temperatures to sublimate or volatilize from the packaging material into the enclosed atmosphere. These molecules then travel through the air and settle onto all exposed metal surfaces within the packaging.
The key to VCI’s protective action is the polarity of the VCI molecules. Metals in the presence of an electrolyte (like moisture) undergo an electrochemical process where electrons flow from high-energy areas (anodes) to low-energy areas (cathodes), leading to oxidation and the formation of rust. VCI molecules, possessing polar charges, are attracted to the surface of the metal, forming a thin monomolecular layer. This layer effectively passivates the surface, disrupting the electrochemical corrosion cell. It acts as an impenetrable shield, preventing the flow of electrons and blocking corrosive agents like oxygen and moisture from contacting the metal surface.
Furthermore, VCI technology works in both the contact and vapor phases. This means that even areas of the metal not in direct contact with the VCI packaging are protected by the migrating vapors. This capability is particularly crucial for complex or irregularly shaped parts, or in large volumes like metal coils, where achieving complete coverage with traditional barrier methods is challenging. Upon removal from the VCI environment, the VCI molecules simply dissipate from the metal surface, leaving it clean, dry, and ready for immediate use or further processing without the need for cleaning or degreasing. This inherent characteristic eliminates the need for solvent-based cleaning, a major source of hazardous waste and environmental pollution associated with traditional rust prevention methods. The longevity of VCI protection, often extending for years when packaged correctly, further contributes to waste reduction by minimizing product damage and the need for re-packaging or scrapping.
VCI Products for Coil Packaging: Eco-Friendly Options
Selecting the right packaging is critical for both protecting metal coils and minimizing environmental impact. Fortunately, the evolution of VCI technology has yielded a variety of eco-friendly product formats specifically designed for the unique challenges of coil packaging.
Eco-friendly VCI packaging solutions for metal coils come in various formats, including VCI papers, VCI films, and VCI covers. These materials are often made from recycled or bio-based content, are recyclable or biodegradable, and are formulated with non-toxic, nitrite-free VCI chemistry. They replace traditional oils and non-recyclable materials, offering effective, clean, and sustainable corrosion protection for coils during storage and transport, significantly reducing environmental impact and waste.

Choosing the Right Sustainable VCI for Your Coils
The choice between different VCI product formats often depends on the specific needs of the coil, the required duration of protection, and the environmental conditions during storage and transit. VCI papers, typically made from Kraft paper, are excellent for interleaving between coil layers or wrapping the outer surface. Many VCI papers are made from 100% recycled fiber and are fully repulpable and biodegradable, making them a highly sustainable choice. They offer quick VCI release, which is beneficial for metals prone to flash rust.
VCI films, often polyethylene-based, provide the added benefit of a moisture barrier, which is crucial in humid environments or during overseas shipments. Modern VCI films are increasingly available in recyclable formulations. Furthermore, advancements in bioplastics have led to the development of biodegradable and compostable VCI films and bags, offering an even higher level of environmental compatibility. Products like Eco-Corr® and Eco Works® films represent the cutting edge in combining VCI protection with certified biodegradability and compostability. Custom-sized VCI Coil Covers, often made from VCI films like ICT®510-CLHD or other VCI films, provide a convenient and effective way to enclose the entire coil, ensuring comprehensive protection.
Here’s a comparison highlighting the eco-friendly aspects of common VCI formats for coils:
Feature | VCI Paper | VCI Poly Film/Bags | VCI Coil Covers (Film) | Eco-Friendly VCI Films (e.g., Eco-Corr) |
---|---|---|---|---|
Material Base | Kraft paper (often recycled) | Polyethylene (PE) | Polyethylene (PE) | Bio-based polymers, certified compostable |
Corrosion Type | Vapor & Contact | Vapor & Contact | Vapor & Contact | Vapor & Contact |
Moisture Barrier | Limited (unless coated with wax/poly) | Good | Good | Good |
Reusability | Limited | Often reusable | Often reusable | Limited (designed for biodegradation) |
Recyclability | Fully repulpable/recyclable | Recyclable (check local facilities) | Recyclable (check local facilities) | Certified compostable/biodegradable |
Biodegradability | Biodegradable | Not inherently biodegradable (unless specified) | Not inherently biodegradable (unless specified) | Certified biodegradable/compostable |
Non-Toxic VCI | Yes (check formulation) | Yes (check formulation) | Yes (check formulation) | Yes (formulated with eco-friendly VCI) |
Typical Use | Interleaving, wrapping | Wrapping, bagging parts | Covering entire coils | Replacing standard poly film with eco-option |
Environmental Advantage | Made from recycled paper, biodegradable | Reduces material use vs. oils, potentially recyclable | Reduces material use vs. oils, potentially recyclable | Highest level of eco-friendliness (certified) |
When choosing a VCI product, it’s crucial to ensure it uses non-toxic chemistry, free from nitrites, phosphates, or heavy metals. Many reputable VCI suppliers offer formulations that meet stringent environmental standards and are even approved for use by the US military (MIL-PRF-3420). Consulting with a VCI expert can help manufacturers select the most effective and environmentally responsible VCI solution tailored to their specific coil type, size, and transit/storage requirements, ensuring optimal protection while minimizing ecological footprint.
Implementing Eco-Friendly Coil Packaging
Adopting eco-friendly coil packaging is a strategic decision that involves more than just switching materials; it requires integrating sustainable practices throughout the packaging and supply chain process. Implementing VCI technology is a primary step, offering a clean, dry method of corrosion prevention that inherently reduces waste compared to traditional oil-based systems.
Implementing eco-friendly coil packaging starts with replacing traditional rust preventatives and excess materials with streamlined VCI solutions like VCI paper, films, and custom coil covers. These materials offer superior protection with less bulk and complexity. The shift reduces the need for cleaning chemicals, minimizes disposal costs, and lowers the overall environmental impact of packaging metal coils. By adopting VCI year-round and training staff on proper handling techniques (like wearing gloves and keeping parts clean and dry), companies can dramatically decrease rust-related waste and increase efficiency.
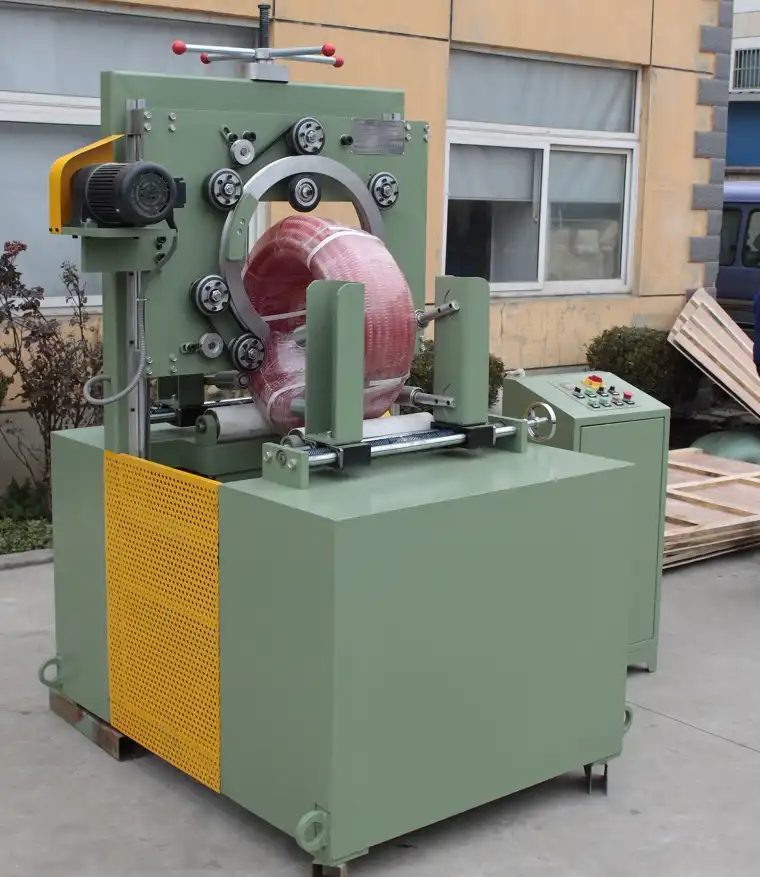
Proper implementation involves training personnel on the correct use of VCI materials, ensuring metal parts are clean and dry before packaging (a key factor in preventing rust, as highlighted in the "Dirty Dozen" list of common mistakes), and using the appropriate type and amount of VCI for the specific metal and packaging volume. Maintaining proper temperature and humidity control in storage and packaging areas, although sometimes costly, further enhances VCI performance and reduces the risk of condensation-induced corrosion. Even simple steps like avoiding direct contact between metal coils and untreated wood pallets or corrugated boxes by using a VCI liner or paper can prevent contact corrosion and eliminate the need to discard damaged coils. Choosing VCI materials that are coated on both sides simplifies application and reduces material waste. By incorporating VCI into standard operating procedures, companies can ensure consistent protection regardless of the season or transit duration. The economic benefits extend beyond reduced material and disposal costs, including fewer returned parts, less labor spent on cleaning and rework, and a stronger reputation with customers who receive rust-free products. Ultimately, eco-friendly coil packaging, centered around VCI technology, aligns environmental responsibility with operational efficiency and cost savings.
Conclusion
Managing coil packaging waste effectively and sustainably is crucial for modern manufacturing. By moving away from outdated, environmentally burdensome practices like using rust-preventative oils and excessive, non-recyclable materials, companies can significantly reduce their ecological footprint. VCI technology, particularly in the form of recyclable and biodegradable VCI paper and films, offers a powerful, clean, and dry alternative for preventing corrosion on metal coils. Embracing these eco-friendly solutions not only addresses the pressing need for sustainability but also leads to reduced costs, improved product quality, and a more streamlined and safer supply chain, benefiting both businesses and the planet. Implementing changes in coil packaging procedures with VCI technology can lead to a cleaner, more efficient future. Learn more about efficient coil packaging solutions that integrate sustainable materials.