Improving Coil Stacking Efficiency with Automated Systems
Manual or traditional coil stacking methods are costing your business valuable time and money, creating safety hazards, and limiting growth. Are you struggling with damaged inventory, slow retrieval times, and inefficient use of expensive warehouse space? It’s time to address the bottlenecks holding you back.
Automated systems significantly improve coil stacking efficiency by integrating advanced technology like Warehouse Management Systems (WMS), automated cranes, and robotic handling. This enables precise inventory tracking, optimized storage layouts, and faster, safer material flow, dramatically reducing labor costs, minimizing damage, and maximizing storage density within existing facilities.
Beyond the initial challenges, embracing automation represents a strategic leap forward. Discover how shifting from outdated practices to intelligent, automated solutions can revolutionize your operations, setting a new standard for productivity and safety in heavy material handling.
How Automation Transforms Coil Stacking
Handling heavy, bulky coils with manual methods or basic equipment is inherently slow and prone to error. Automation fundamentally changes this by introducing precision, speed, and intelligence into the process.
Automated systems revolutionize coil stacking by leveraging intelligent software (WMS) and robotic hardware (cranes, robots) to manage and execute storage operations autonomously. A WMS receives production or order data, determines optimal storage locations considering factors like coil dimensions, weight, and retrieval priority, and directs automated cranes or mobile robots for precise placement and retrieval. This eliminates manual decision-making errors, optimizes storage sequences, accelerates material movement, and provides real-time inventory visibility, enabling facilities to operate with unparalleled efficiency and reduced human intervention.
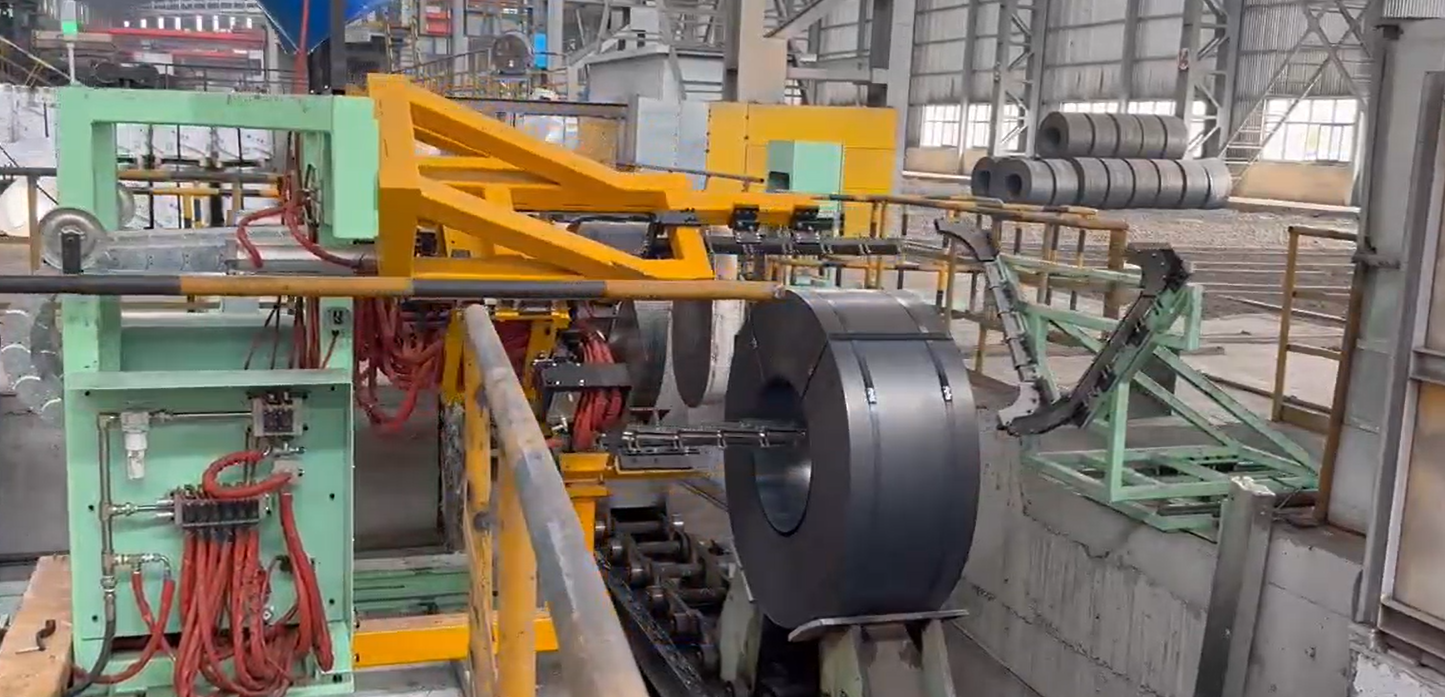
The Core Components and Functions of Automated Coil Storage
Automated coil storage isn’t just about replacing a forklift with a robot; it’s about creating a fully integrated system where software and hardware work together seamlessly. At its heart lies the Warehouse Management System (WMS), acting as the central nervous system, orchestrating all movements based on predefined rules and real-time data.
- Warehouse Management System (WMS): This software is the brain of the automated system. It tracks every coil, its attributes (size, weight, material type, destination), and its exact location. The WMS manages transport orders from host systems (like ERP or MES), optimizes storage assignments based on criteria like retrieval frequency (e.g., FIFO), and plans the movement sequences for the automated equipment. It can even manage complex tasks like "shuffling" – automatically moving blocking coils to temporary locations to access needed coils, as described in the material provided. Advanced WMS modules, like those for Yard Management, Production Management, and Mobile Robot Management, extend automation beyond the main storage area, controlling material flow from receiving (truck/train) through production lines and external logistics.
- Automated Cranes: These are typically overhead cranes equipped with specialized lifting attachments (like C-hooks or mechanical grippers) designed for coils. Directed by the WMS, they execute precise horizontal and vertical movements to pick up, transport, and deposit coils at designated locations. Automation ensures consistent, repeatable movements, minimizing sway and potential collisions. Multi-crane systems require sophisticated WMS logic to coordinate movements and avoid interference on shared runways.
- Mobile Robots (AGVs/AMRs): For material handling outside the main crane-served storage block, mobile robots can automate the movement of coils between the storage area, production lines, and loading docks. The WMS integrates with a Mobile Robot Management Module (MRMM) to direct robot paths, prioritize tasks, and ensure safe navigation, further reducing manual handling steps.
Integrating these components allows for functionalities far beyond manual systems:
- Precise Inventory Tracking: Real-time updates on every coil’s location and status.
- Optimized Storage Strategies: Dynamic assignment of coils to maximize space and minimize future retrieval effort.
- Automated Shuffling: Complex re-organization tasks handled automatically to access blocked coils efficiently.
- Performance Monitoring: Data collection on crane cycles, throughput, and bottlenecks for continuous improvement.
Consider the fundamental differences:
Feature | Traditional Coil Stacking (Manual/Basic Racks) | Automated Coil Stacking Systems (WMS, Cranes, Robots) |
---|---|---|
Inventory | Manual tracking, prone to errors | Real-time, precise WMS tracking |
Location Strategy | Ad-hoc, based on operator decision | WMS optimized, rule-based assignment |
Movement | Manual equipment operation (forklifts, cranes) | Automated cranes, robots directed by WMS |
Retrieval | Manual identification & retrieval, searching | WMS-directed, optimized sequence, no searching |
Shuffling | Manual, time-consuming, risky | Automated, efficient, planned by WMS |
Throughput | Limited by human speed & shift times | 24/7 operation, high-speed cycles |
Error Rate | Higher (manual handling, data entry) | Minimal (machine precision, WMS logic) |
This integrated approach addresses core inefficiencies, enabling businesses to handle higher volumes with greater speed and accuracy than ever before.
Enhanced Safety and Damage Prevention
One of the most significant benefits of automating coil stacking operations is the profound impact on workplace safety and the reduction of material damage. Manual handling of multi-ton coils presents inherent risks that automation is designed to mitigate.
Automated systems significantly enhance safety in coil stacking by minimizing human interaction with heavy loads, reducing the risk of manual handling accidents. Precise machine movements prevent collisions and dropping hazards. Integrated safety sensors and systems monitor operations, ensuring stability and compliance with safety standards, leading to a safer workplace and less material damage.
Reducing Risks Through Automated Handling and Monitoring
Traditional coil storage, relying heavily on manual operation of equipment and the physical handling of chocks and blocks (as mentioned in the material regarding outdated wood timbers), poses serious risks like crushing injuries, tipovers, and equipment damage. Automation tackles these head-on:
- Reduced Human Exposure: Automated systems perform the heavy lifting and precise maneuvering, removing operators from the immediate vicinity of moving loads and high-risk zones. This drastically lowers the probability of accidents related to physical contact with coils or equipment.
- Precision and Stability: Automated cranes and robots execute movements with high precision, controlled acceleration, and deceleration. This contrasts with potential inconsistencies in human operation, reducing the risk of dropping coils, hitting racks, or causing stored coils to shift or roll – common causes of damage and injury. Using secure coil storage cradles (as highlighted in the material on custom racking), paired with automated placement, ensures coils are stable once stored.
- Integrated Safety Features: Modern automated systems incorporate advanced safety features. Load sensors can prevent overloading of racks or equipment. Collision avoidance systems use sensors and software logic to prevent equipment from impacting each other or static structures. Area scanners and safety zones automatically halt operations if personnel enter hazardous areas. These features are built-in and continuously monitored by the system.
- Consistency and Compliance: Automated operations are repeatable and adhere strictly to programmed parameters and safety protocols. This makes it easier to ensure consistent compliance with occupational health and safety regulations compared to relying solely on human adherence, which can vary. Engineered racking systems designed for specific loads (Material 1) are prerequisites, and automation ensures these load capacities are respected.
- Minimized Material Damage: Beyond safety, precise automated handling significantly reduces the risk of damage to the coils themselves. Edge damage, deformation from improper lifting, or damage caused by coils rolling or shifting during storage are minimized with controlled, accurate movements and secure placement. Reducing material damage directly translates to cost savings and preserved product quality.
By implementing automated solutions, businesses create a more predictable and controlled environment, fundamentally improving the safety profile of their coil storage operations while simultaneously protecting their valuable inventory.
Maximizing Space and Streamlining Workflow
Inefficient space utilization and cumbersome workflows are major pain points in traditional coil storage, limiting capacity and slowing down operations. Automated systems offer a powerful solution by enabling denser storage configurations and optimizing material flow.
Automated systems maximize storage space through high-density vertical stacking capabilities enabled by precise handling. The WMS optimizes layouts and retrieval sequences, minimizing unnecessary movement and accelerating access to coils. This streamlines the entire material flow, reduces bottlenecks, and significantly increases storage capacity within the existing footprint.
Achieving High-Density Storage and Faster Throughput
Leveraging vertical space is a core principle of efficient warehouse design, and automated systems take this to the next level in coil storage. While custom racking systems allow for vertical stacking (Material 1), automated cranes can typically stack coils higher and in narrower aisles or tighter configurations than manually operated equipment can safely achieve.
- Vertical Space Optimization: Automated systems excel at high-reach applications. Automated cranes, guided by the WMS, can accurately place and retrieve coils from significant heights, maximizing the use of vertical cube space. This dramatically increases storage capacity within the same facility footprint, potentially delaying or eliminating the need for costly warehouse expansion (as illustrated by the case study in the provided material showing a 30-70% capacity increase).
- Optimized Layouts and Configurations: The WMS can calculate and assign storage locations strategically to optimize density while maintaining accessibility. Modular racking systems (Material 1), like tiered cradles, complement automation by providing the structure for high-density vertical storage, allowing automated systems to place coils securely and independently. The WMS considers coil size, weight, and retrieval patterns to dynamically manage storage locations, ensuring efficient space usage over time.
- Streamlined Material Flow: Automation, particularly guided by an intelligent WMS, inherently streamlines workflow. The system knows where everything is, where it needs to go, and the most efficient sequence to achieve it. This minimizes unnecessary crane or robot movements (reducing travel time and wear) and eliminates time wasted searching for coils or manually re-organizing stacks. Order prioritization features in the WMS (Material 2) ensure critical materials are retrieved first, aligning storage operations with production or shipping demands.
- Faster Retrieval and Placement: Automated equipment operates consistently and often at higher speeds than manual processes allow, particularly for repetitive tasks. The WMS plans optimal paths and sequences, accelerating the time it takes to move a coil from storage to its destination or vice versa. This reduces operational downtime and increases overall throughput capacity.
Comparing traditional manual methods to automated systems highlights the stark contrast in efficiency:
Metric | Traditional Coil Stacking | Automated Coil Stacking |
---|---|---|
Space Density | Limited vertical, wider aisles | High vertical, optimized density |
Accessibility | Requires moving blocking coils | WMS-managed retrieval, less shuffling |
Retrieval Time | Variable, dependent on location/skill | Consistent, fast, optimized |
Workflow | Manual planning, potential bottlenecks | WMS-optimized, streamlined flow |
Throughput | Lower, limited by human capacity | Higher, 24/7 potential |
Shuffling Needs | Frequent, manual | Minimized, automated by WMS |
By implementing automated coil stacking solutions, businesses unlock the potential for significantly higher storage capacity and faster, more efficient workflows, directly impacting productivity and profitability.
Implementing Automated Coil Stacking Solutions
Transitioning to an automated coil stacking system is a strategic investment that requires careful planning and execution to ensure a smooth process and optimal return. It’s more than just purchasing equipment; it involves integrating technology, redesigning workflows, and training personnel.
Implementing automated coil stacking solutions involves assessing current needs, space, and load capacity, then designing a tailored system using WMS, automated handling equipment, and high-density racking. It requires integrating the system with existing operations, conducting simulation and testing, and providing comprehensive training for personnel to ensure a smooth transition and optimal performance.
The implementation journey typically follows several key phases:
-
Needs Assessment and Planning:
- Analyze your current operation: throughput requirements, coil types (dimensions, weights), existing space constraints, safety incidents, material handling costs.
- Define key performance indicators (KPIs) for the new system (e.g., coils stored per hour, space utilization percentage, safety incident reduction).
- Engage with experienced automation providers. They can help assess your facility’s structural capacity and layout suitability.
- Utilize advanced tools like simulation modeling and concept studies (as highlighted in the Konecranes material) to visualize potential system designs, validate performance against your KPIs (e.g., throughput calculations), and optimize the number of cranes, storage strategies, and layout before installation begins.
-
System Design and Engineering:
- Design the layout of automated racking (consider load capacity and coil dimensions as per Material 1). This will likely involve high-density, vertical configurations.
- Select the appropriate automated handling equipment (cranes, robots) based on load requirements, speed needs, and the facility’s physical characteristics.
- Design the WMS functionality, including integration points with your existing ERP or MES, rule configurator settings for storage strategies, and necessary modules (Yard, Production, Mobile Robot management if needed). Customizable designs (Material 1) for specific environmental conditions should be considered if necessary.
- Engineer safety systems, access controls, and maintenance points.
-
Manufacturing and Installation:
- Racking and automation equipment are manufactured.
- Site preparation occurs at your facility.
- Installation of racking, crane runways, cranes, robots, and control systems.
-
Software Development and Integration:
- The WMS software is configured and potentially customized.
- Integration interfaces with host systems are developed and tested.
-
Testing and Commissioning:
- Rigorous testing of all components (racking, equipment, WMS) individually and as an integrated system.
- Conduct interface tests with existing IT systems (Material 2).
- Commissioning involves bringing the system online and ensuring it meets design specifications under operational conditions. Using a digital twin (Material 2) allows for virtual testing and fine-tuning before physical commissioning.
-
Training and Handover:
- Comprehensive training for operators, maintenance personnel, and supervisors on using the WMS, interacting with the automated equipment, safety procedures, and troubleshooting. The digital twin can be an invaluable training tool (Material 2). A WMS chatbot (Material 2) can provide on-demand support and guidance post-training.
- Formal handover of the operational system.
-
Ongoing Support and Optimization:
- Establish preventive maintenance schedules for hardware and software (Material 2).
- Access remote support or on-call services for troubleshooting (Material 2).
- Continuously monitor system performance using WMS data and look for opportunities for optimization (adjusting WMS rules, refining workflows). Scalability features (Material 1) should allow the system to adapt to changing needs.
This structured approach minimizes disruption and ensures that the complex automated system delivers its promised benefits in terms of efficiency, safety, and space utilization.
Conclusion
Improving coil stacking efficiency is paramount for industries handling heavy cylindrical materials. While custom racking systems provide a foundational improvement, integrating automated systems – including WMS, automated cranes, and robotics – represents the cutting edge in optimizing these operations. Automation enables unprecedented levels of precision, speed, and safety, significantly reducing labor costs, minimizing costly material damage, and maximizing the utilization of valuable warehouse space through high-density storage. The journey towards automation involves careful planning, expert system design, robust implementation, and continuous support. Investing in automated solutions for coil stacking is a strategic decision that not only enhances operational performance and safety but also positions your business for future growth and competitiveness in a demanding market.