How to Use Steel Coil Handling Equipment to Maximize Efficiency
Are your steel coil handling processes slow, costly, and dangerous? The risks of damage and injury constantly threaten productivity. Inefficient handling not only wastes valuable time and resources but also exposes your workforce to significant hazards. It’s time to transform your operations.
Maximizing efficiency in steel coil handling involves a multi-faceted approach focusing on selecting the right equipment, implementing robust safety protocols, streamlining workflows, and embracing advanced technologies like automation. Proper equipment, such as gantry cranes, coil lifters, and specialized forklifts, combined with rigorous training and optimized storage strategies, minimizes handling time, reduces damage, and creates a safer, more productive environment.
Improving how you handle steel coils is critical for any business working with this material. By understanding and applying best practices in equipment use, safety, and operational flow, you can unlock significant gains in both efficiency and safety, positioning your business for greater success and profitability.
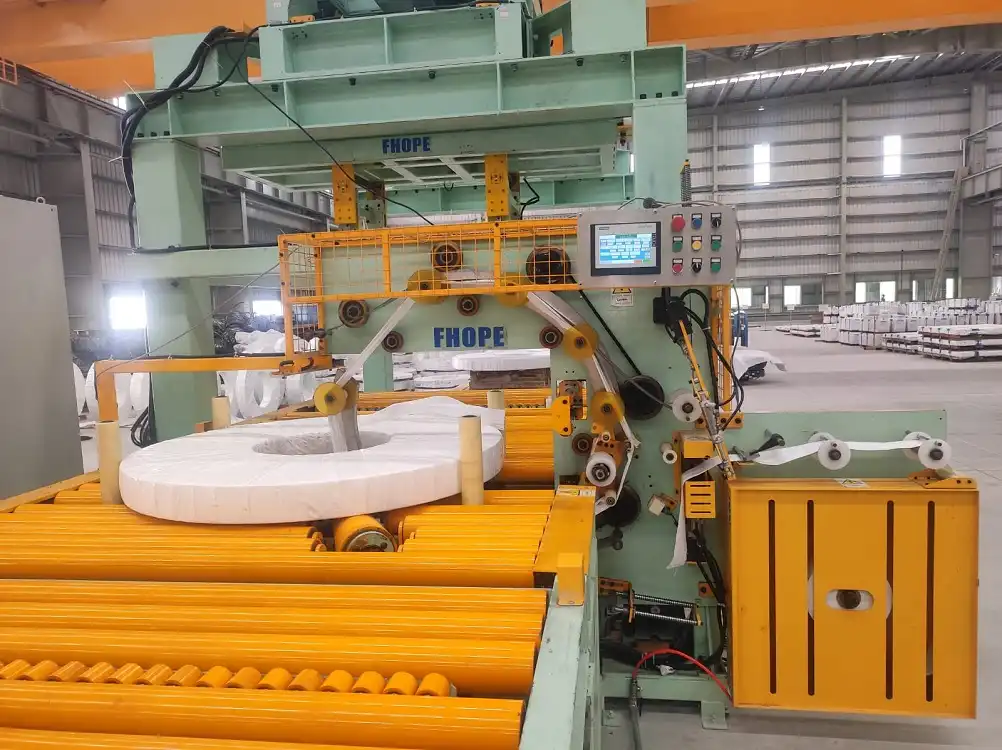
Prioritizing Health and Safety in Coil Handling Operations
Handling heavy steel coils poses significant risks, from crushing injuries to falls and equipment failures. Neglecting safety not only endangers your workforce but also leads to costly accidents, downtime, and legal liabilities, severely hindering operational efficiency.
Ensuring health and safety is paramount in steel coil handling and directly contributes to maximum efficiency by preventing accidents, reducing injuries, and minimizing operational disruptions. Key safety measures include mandatory Personal Protective Equipment (PPE), comprehensive training in safe lifting techniques and equipment operation, proper coil storage to prevent falls, regular equipment inspection, and clear procedures for transport and emergency response.
Building a Robust Safety Culture Around Steel Coil Handling
A safe workplace is inherently more efficient. By making health and safety a top priority, businesses can significantly reduce the likelihood of costly incidents that disrupt workflow and productivity. This involves several key areas, including equipping workers properly, providing continuous training, securing storage areas, and maintaining handling equipment diligently.
Essential Safety Measures for Coil Handling
Worker safety starts with mandatory Personal Protective Equipment (PPE). This includes steel-toed boots to protect against falling objects, heavy-duty gloves to guard against sharp edges, and safety glasses to shield eyes from debris. Beyond basic gear, proper training in manual handling and the correct use of mechanical aids is non-negotiable. Techniques for safe lifting and operating equipment like forklifts, gantry cranes, and specialized coil lifters prevent musculoskeletal injuries and equipment-related accidents. Noise control measures are also crucial in noisy factory environments to protect workers’ hearing.
Secure storage is another critical element. Steel coils, due to their weight and tendency to roll, must be stored on stable, level surfaces. Storing them "eye to the sky" (on their side) or in robust storage racks designed for coil dimensions and weight prevents accidental rolling or falling. Bulk coil racks provide secure vertical storage, minimizing floor space usage while maintaining safety. Clear labeling indicating weight, size, and handling instructions is vital for safe management, alongside well-marked safe pathways and hazard zones.
Regular inspection and maintenance of all handling equipment – cranes, forklifts, coil lifters, tongs, and grabs – are essential preventative measures. Equipment failure due to lack of maintenance can have catastrophic consequences. Using the correct lifting attachments specific to coil size and weight is also crucial to prevent damage or dropping the load. Establishing clear, standardized procedures for loading, unloading, and transporting coils ensures predictable and safe operations, minimizing guesswork and the potential for errors.
Implementing comprehensive safety measures has a direct impact on efficiency by preventing disruptions.
Safety Measure | Direct Efficiency Benefit | Risk Reduction Impact | Implementation Effort |
---|---|---|---|
Comprehensive PPE Use | Reduces minor injuries & lost time. | Protects workers from physical hazards. | Low |
Regular Safety Training | Improves operational speed & reduces errors. | Minimizes accidents due to improper handling. | Ongoing (Moderate) |
Secure Coil Storage Racks | Maximizes vertical space; prevents downtime. | Eliminates risks from falling or rolling coils. | Moderate (Initial) |
Preventive Equipment Maintenance | Ensures equipment reliability & uptime. | Prevents equipment failure & major accidents. | Ongoing (Low) |
Clear Handling Procedures | Streamlines workflow; reduces confusion. | Minimizes errors during complex operations. | Moderate |
Noise Control Measures | Improves communication & focus. | Prevents long-term hearing damage. | Variable |
By making these safety measures integral to daily operations, businesses not only protect their most valuable asset – their people – but also build a foundation for consistent, efficient steel coil handling.
Streamlining Business Processes for Peak Coil Handling Efficiency
Inefficient business processes tied to steel coil handling, such as poor inventory management or convoluted workflows, can lead to bottlenecks, wasted resources, and unnecessary delays. These inefficiencies directly impact profitability and overall operational speed.
Streamlining business processes is fundamental to maximizing efficiency in steel coil handling by optimizing inventory management, designing efficient workflows, enforcing rigorous product inspection, cultivating strong supplier relationships, and maintaining handling equipment proactively. These strategies collectively reduce waste, minimize handling time, prevent delays, ensure material quality, and maintain consistent operational flow.
Optimizing the Flow: Inventory to Production
Beyond the direct act of moving coils, the surrounding business processes play a crucial role in overall efficiency. Effective management systems and strategic relationships ensure that the right coils are available at the right time and moved through the facility with minimal friction.
Key Strategies for Process Efficiency
A robust inventory management system is the cornerstone of efficient coil handling. Tracking coil quantities, specifications (like grade, size, and weight), and precise locations prevents overstocking (reducing storage space and costs) and understocking (avoiding production delays). Implementing a "first-in, first-out" (FIFO) system ensures older coils are used first, preventing material degradation and potential waste, which contributes to better resource utilization and space management.
Workflow design is equally critical. Mapping out the entire coil journey from receiving to storage, processing, and production allows for optimization. The goal is to minimize unnecessary movements and handling steps. This might involve redesigning storage layouts to be closer to production lines or implementing systems that allow coils to be loaded directly from supplier trucks onto storage racks or feed lines. Reducing the number of times a coil is handled directly decreases the risk of damage and saves significant time and labor. For example, using mobile coil pallets or traveling gantry systems allows coils to be moved efficiently through compact or flexible factory layouts.
Rigorous quality control for incoming steel coils is essential. Inspecting coils upon arrival ensures they meet required standards. Detecting defects early prevents delays, rework, and potential damage to machinery caused by substandard material. This also saves the time and space that would be needed to store or process rejected material. Building strong, reliable relationships with suppliers ensures consistent quality and timely delivery, which reduces the need for large buffer inventories and improves overall supply chain predictability, further enhancing efficiency and optimizing storage requirements. Finally, consistently maintaining all handling equipment, as discussed earlier, is a process strategy in itself. Preventive maintenance schedules reduce the likelihood of unexpected breakdowns, minimizing costly downtime and ensuring equipment is always ready for efficient operation.
These process improvements, when integrated, create a synergistic effect, drastically improving the speed and efficiency of steel coil handling operations from end to end.
Leveraging Equipment and Techniques for Space-Efficient Handling
Is your facility cluttered with steel coils, limiting movement and slowing down operations? Inefficient use of space during coil handling directly impacts productivity, creating bottlenecks and increasing the risk of accidents in cramped areas.
Utilizing the right steel coil handling equipment and implementing space-saving techniques are critical for maximizing efficiency by optimizing facility layout, minimizing the required operational footprint, and streamlining material flow. Equipment like vertical coil racks, compact coil pallets, automated gantry systems, and specialized handling attachments enable denser storage and faster, safer movement within limited space.
Strategic Equipment Selection and Operational Mastery
The choice of equipment and the proficiency with which it is used can dramatically alter the space requirements and speed of coil handling. Selecting equipment that not only moves coils safely but also fits the specific constraints and workflow of your facility is key to unlocking efficiency.
Equipment Choices for Optimized Space and Speed
Choosing the right handling equipment goes beyond just lifting capacity; it’s about finding tools that facilitate efficient movement within your available space. Instead of seeking complex, multi-purpose machines, simpler, specialized equipment might be more efficient for specific tasks and occupy less space. Integrated coil handling systems from a single supplier can offer better coordination and space optimization compared to assembling components from various sources.
Efficient operation also involves managing the space required for material flow. For example, while loop space for material slack is necessary for processes like decoiling and straightening, optimizing its size to the minimum required prevents excessive horizontal sprawl. Where vertical space is available, using looping pits or elevated straighteners can stack the material slack vertically, freeing up valuable floor space. Similarly, ensuring adequate service space around equipment is important for maintenance and safety, but planning layouts strategically can minimize the overall footprint required. Securely lagging equipment reduces vibration and misalignment, allowing for potentially tighter layouts.
Beyond basic handling, specialized equipment like double stock reels can minimize coil changeover time, reducing downtime and maximizing throughput in a fixed space. Coil loading cars streamline the process of bringing a coil to the decoiler, reducing the time and space needed for staging. Vertical coil storage racks are perhaps one of the most impactful pieces of equipment for space saving, maximizing cubic warehouse space and drastically reducing the floor area occupied by coils compared to horizontal stacking. For narrow coils prone to telescoping, horizontal pan-type reels can improve handling stability and reduce material waste, optimizing material usage within the space. Implementing techniques like stagger blanking during processing maximizes material yield and minimizes scrap, reducing the space needed for scrap storage.
Effectively combining strategic equipment choices with smart operational techniques directly contributes to maximizing efficiency by optimizing space utilization and streamlining the flow of materials.
Embracing Automation and Specialized Equipment for Next-Level Efficiency
Manual or semi-automated coil handling can be labor-intensive, slower, and prone to human error, limiting throughput and increasing the risk of damage. Relying on general-purpose equipment may not provide the speed, precision, or safety needed for high-volume, efficient operations.
Adopting automated steel coil handling solutions and specialized equipment like coil tippers and upenders is key to achieving maximum efficiency by increasing speed, improving accuracy, reducing labor costs, minimizing coil damage, and enhancing safety through reduced human intervention. Automated systems offer predictable performance, higher throughput, and better data collection, while specialized equipment optimizes coil orientation and integration into automated lines, streamlining the entire process.
Moving towards higher levels of automation and incorporating specialized handling tools marks a significant step in maximizing steel coil handling efficiency. Automated systems can perform repetitive tasks with greater speed and precision than manual operations, reducing cycle times and increasing overall output. They minimize the risk of human error, which is a major cause of coil damage and safety incidents. Automated systems can also operate in tighter spaces with greater consistency once programmed, optimizing material flow and layout. Benefits often include increased uptime due to predictable performance, reduced scrap rates from accurate positioning, lower labor requirements, and improved packaging efficiency. However, the initial investment is higher, and maintenance becomes more specialized.
Specialized equipment such as coil tippers and upenders are crucial for efficiently changing the orientation of coils. Tippers rotate coils from "eye to the sky" to "eye to the side" or vice versa, essential for feeding decoilers. Upenders offer more controlled rotation, often used for inspection or feeding precision cutting tables. These machines minimize risky manual handling and mechanical maneuvers required to change coil orientation, significantly improving safety and speed. Low-profile upenders are particularly useful in areas with limited vertical clearance. Integrating these machines seamlessly into production lines ensures a smooth, continuous flow of material, reducing bottlenecks and maximizing efficiency. Investing in rugged, customized equipment is also vital. Equipment built with heavy-duty components ensures reliability and longevity, reducing downtime for repairs. Customization allows equipment to be precisely designed for specific coil sizes, weights, and facility layouts, ensuring optimal performance and space utilization. Features like intuitive controls and seamless integration capabilities are also important for ease of use and smooth workflow. Thorough analysis of production needs and a cost-benefit analysis justify the investment in such specialized and automated solutions by demonstrating projected improvements in safety, material flow, and return on investment.
Conclusion
Maximizing efficiency in steel coil handling is a comprehensive effort that integrates robust safety measures, streamlined business processes, intelligent equipment selection, and the strategic adoption of automation and specialized tools. By prioritizing the health and safety of workers through training and proper protocols, optimizing inventory and workflow, leveraging space-saving equipment and techniques, and investing in reliable, customized solutions like automated systems and coil handling equipment, businesses can significantly enhance productivity, reduce costs, and ensure a safer work environment. Embracing these best practices is key to unlocking the full potential of your operations.