How to Use Coil Handling Equipment to Prevent Coil Damage During Transport
Are you tired of battling damaged coils arriving at the production line, disrupting your workflow and costing you money? Coil damage during transport is a significant headache for metal fabricators. Imagine the frustration of unusable material and project delays. The solution? Utilizing the right coil handling equipment and mastering proper techniques.
Preventing coil damage during transport hinges on selecting and correctly using specialized handling equipment. This includes coil lifters, forklifts with coil rams, coil tippers, and gantry systems, ensuring coils are properly secured and supported during every stage of movement, from loading to unloading. Investing in the right equipment and training operators is crucial for maintaining coil integrity and operational efficiency.
This article will guide you through the essential equipment and best practices to safeguard your coils during transport, minimizing damage and maximizing productivity. Let’s delve into how to protect your valuable materials and ensure smooth operations.
Selecting the Right Coil Handling Equipment for Transport
Handling metal coils, especially during transport, demands precision and the right tools. Using inadequate equipment or mishandling proper tools can lead to costly damage and safety hazards. Choosing the correct coil handling equipment is the first step to ensuring damage-free transport and maintaining material quality.
The primary equipment for preventing coil damage during transport includes forklifts with specialized attachments like coil rams or booms, C-hooks, coil lifters, and gantry systems. Each piece of equipment offers unique advantages for different transport scenarios, coil sizes, and facility layouts. Selecting the appropriate equipment based on coil specifications and transport methods is crucial for safe and damage-free handling. Understanding the capabilities and limitations of each type of equipment is essential for optimizing your coil handling process.
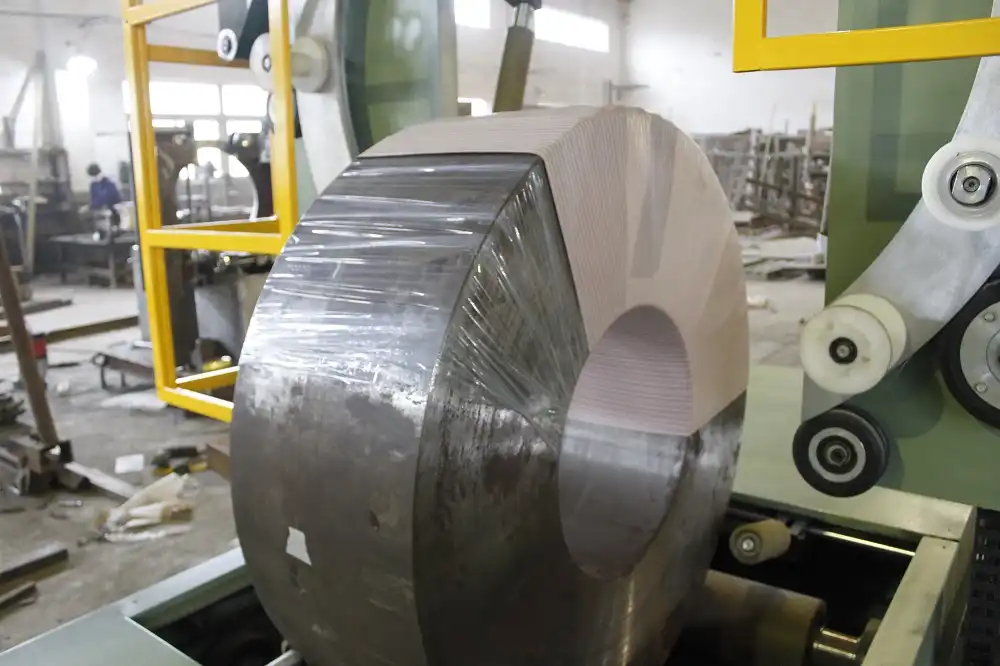
Types of Coil Handling Equipment and Their Applications
Different coil handling equipment is designed for specific tasks and coil orientations. Understanding these differences is key to efficient and safe transport. Here’s a breakdown of common equipment types:
Equipment Type | Description | Ideal Use Cases | Advantages | Disadvantages |
---|---|---|---|---|
Forklifts with Coil Ram/Boom | Standard forklift with a cylindrical ram or boom attachment. | Loading/unloading trucks, short distance transport within a facility. | Versatile, widely available, relatively cost-effective. | Can cause coil damage if not used carefully, limited reach, requires skilled operator. |
C-Hooks (Coil Hooks) | Hook-shaped lifting device suspended from a crane or hoist. | Lifting coils in "eye-vertical" position, loading/unloading in confined spaces. | Simple, robust, good for vertical lifting, less surface contact with coil. | Requires overhead crane or hoist system, can be slower than other methods. |
Coil Lifters (Tongs/Grabs) | Specialized lifting devices with gripping arms designed to secure coils. | Lifting coils in "eye-horizontal" position, precise placement, minimizing surface damage. | Secure grip, minimizes coil surface contact, efficient for horizontal handling. | Higher initial cost, may require specific lifter for different coil sizes. |
Gantry Systems | Overhead crane systems, fixed or traveling, often with coil lifters or C-hooks. | High-volume coil handling, feeding production lines, large warehouses. | Efficient for repetitive tasks, automated options available, excellent load stability. | High initial investment, fixed gantries less flexible, traveling gantries require track space. |
Coil Tippers | Machines that rotate coils from "eye-to-sky" to "eye-to-side" orientation. | Preparing coils for roll forming or processing lines that require "eye-to-side" feeding. | Reduces manual handling, improves efficiency of coil feeding, safer than manual tipping. | Specialized equipment for a specific task, additional equipment cost. |
Multidirectional Forklifts | Forklifts capable of moving in multiple directions (sideways, forward, diagonally). | Transporting long or bulky coils in narrow aisles and confined spaces. | Enhanced maneuverability, ideal for tight spaces, can handle various load types including long materials. | Higher cost than standard forklifts, requires operator training for multidirectional operation. |
Choosing the right equipment depends on your specific needs, coil dimensions, transport distances, and facility layout. Always prioritize equipment that offers the best balance of safety, efficiency, and coil protection.
Best Practices for Safe Steel Coil Transport
Safe transport of steel coils is paramount, not only to prevent material damage but also to ensure workplace safety and regulatory compliance. Neglecting safety protocols can lead to accidents, injuries, and significant financial losses. Implementing best practices in coil transport is a non-negotiable aspect of responsible material handling.
To ensure safe steel coil transport, always begin with equipment inspection and operator training. Establish clear loading and unloading procedures, ensuring coils are properly secured using appropriate tie-downs and blocking. Maintain slow and controlled speeds during transport, especially when maneuvering corners or uneven surfaces. Regular safety audits and refresher training are crucial to reinforce safe practices and prevent accidents. Prioritizing safety in every step of the transport process is essential for a secure and efficient operation.
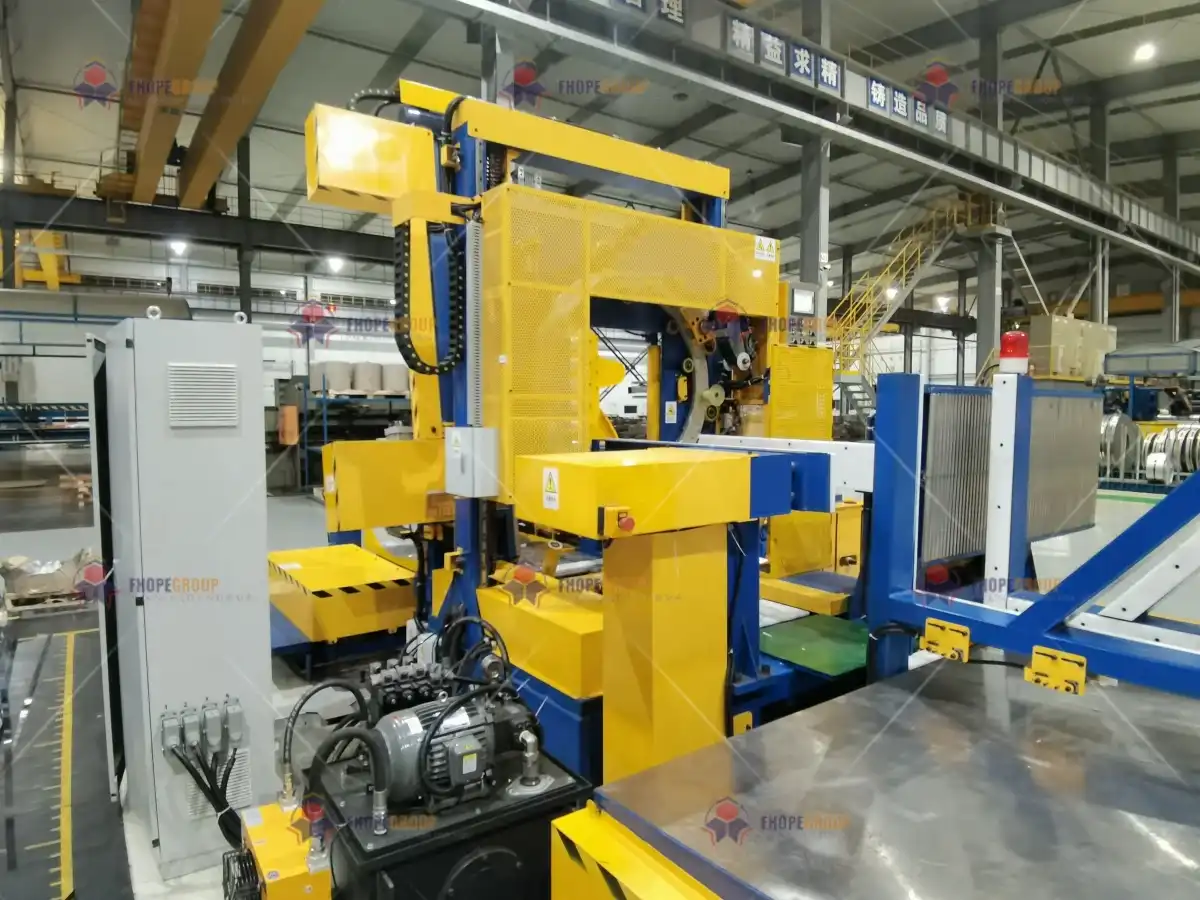
Key Considerations for Safe Coil Transport
Beyond equipment selection, several operational practices contribute significantly to safe coil transport. These practices encompass pre-transport checks, loading and unloading procedures, and in-transit precautions:
-
Pre-Transport Inspection:
- Equipment Checks: Regularly inspect forklifts, coil lifters, cranes, and other handling equipment for wear and tear, ensuring brakes, lifting mechanisms, and safety devices are in optimal working condition. Maintain records of inspections and maintenance.
- Route Assessment: Plan transport routes to avoid obstacles, uneven surfaces, and congested areas. Ensure pathways are clear and capable of supporting the weight of the loaded equipment and coil.
- Trailer/Truck Bed Inspection: Verify the trailer or truck bed is in good condition, free of debris, and capable of securely holding the coil. Check for proper tie-down points and structural integrity.
-
Loading and Unloading Procedures:
- Controlled Lifting: Lift and lower coils smoothly and vertically to prevent swinging or sudden shifts in weight. Avoid jerky movements that can destabilize the load.
- Proper Coil Orientation: Load coils in the correct orientation ("eye-to-sky" or "eye-to-side") as required for transport and subsequent processing. Use appropriate equipment to change coil orientation safely.
- Securement Techniques: Utilize industry-standard tie-down methods, including chains, straps, and coil chocks, to prevent coil movement during transit. Ensure tie-downs are correctly rated for the coil weight and are properly tensioned.
- Qualified Personnel: Only trained and authorized personnel should operate coil handling equipment and supervise loading/unloading operations. Provide ongoing training and certification programs.
-
In-Transit Precautions:
- Speed Limits: Adhere to safe speed limits within the facility and during external transport. Reduce speed when turning, braking, or navigating ramps and inclines.
- Awareness of Surroundings: Operators should maintain full awareness of their surroundings, including pedestrians, other equipment, and obstacles. Use horns and signals to alert others of their presence.
- Load Stability Monitoring: Periodically check load stability during long transports, especially after traversing uneven terrain. Re-tension tie-downs if necessary.
- Emergency Preparedness: Establish emergency procedures and ensure operators are trained to respond to equipment malfunctions, load shifts, or other unforeseen events. Keep emergency contact information readily available.
By diligently following these best practices, businesses can significantly minimize the risks associated with steel coil transport, creating a safer working environment and protecting valuable materials from damage.
Minimizing Coil Damage During Handling and Storage
Coil damage isn’t solely a transport issue; it can occur at any stage of handling and storage. Nicks, dents, and surface scratches can compromise coil quality, leading to scrap and production inefficiencies. Implementing strategies to minimize damage throughout the handling and storage process is crucial for maintaining material integrity and reducing waste.
Preventing coil damage requires a holistic approach encompassing careful handling techniques, appropriate storage strategies, and proactive quality control measures. Minimizing the number of times coils are handled, using protective measures during lifting and placement, and selecting optimal storage orientations are key steps. Regular inspections and employee training further contribute to a damage-free coil handling and storage system. By focusing on preventative measures, businesses can safeguard coil quality and optimize their operations.
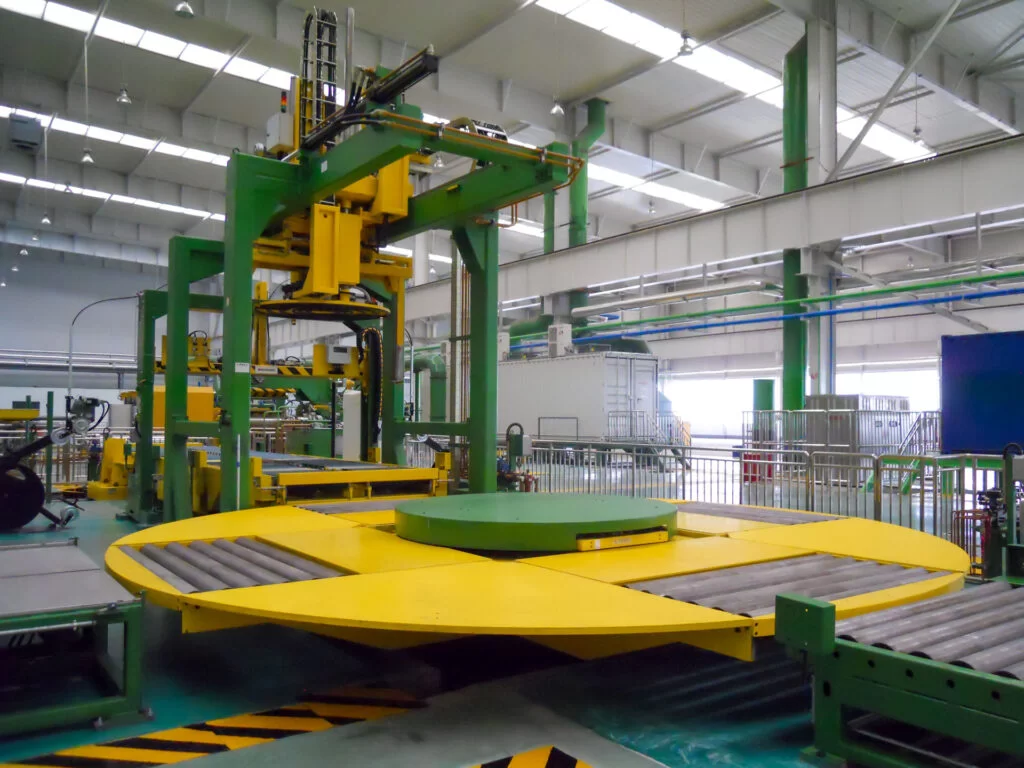
Strategies for Damage Prevention
Damage prevention involves a multi-faceted approach, incorporating handling techniques, storage solutions, and preventative measures. Here’s a detailed look at key strategies:
Strategy | Description | Benefits | Implementation Tips |
---|---|---|---|
Minimize Handling Frequency | Reduce the number of times coils are lifted, moved, or transferred. | Decreases the likelihood of accidental damage from repeated handling, saves time and labor costs. | Optimize workflow to minimize unnecessary movements. Plan storage locations close to processing areas. Utilize gantry systems or automated handling for direct coil feeding to production lines. |
Proper Lifting Techniques | Train operators in gentle lifting and lowering techniques. Avoid dragging or scraping coils against surfaces. | Prevents surface scratches, edge damage, and deformation. Maintains coil integrity and aesthetic quality. | Emphasize smooth, controlled movements. Use coil protectors or padding on lifting equipment contact points. Ensure operators are fully trained on equipment-specific lifting procedures. |
Optimal Storage Orientation | Choose appropriate storage orientation ("eye-to-sky" or "eye-to-side") based on coil type and storage duration. | Prevents water accumulation in "eye-to-sky" storage, maximizes space efficiency in "eye-to-side" storage, reduces surface contact. | Store painted coils "eye-to-sky" to protect surfaces. Store WIP coils "eye-to-side" for easier feeding into decoilers. Use proper racking systems designed for each orientation. Consider climate control in storage areas to prevent corrosion. |
Automated Handling Systems | Implement automated coil handling systems for repetitive tasks. | Reduces human error, increases speed and consistency, minimizes damage through precise machine control. | Evaluate the cost-benefit of automation based on volume and damage frequency. Invest in systems with sensors and safeguards to prevent collisions and damage. Ensure proper maintenance and calibration of automated equipment. |
Quality Control Inspections | Conduct regular inspections of coils upon arrival and during storage. | Early detection of damage allows for timely corrective actions, prevents damaged coils from entering production, reduces scrap. | Establish clear inspection protocols and checklists. Train personnel to identify different types of coil damage. Implement a system for tracking and documenting coil condition throughout the handling and storage process. |
Protective Measures | Use protective materials like rubber mats, edge protectors, and wrapping films. | Shields coils from scratches, dents, and environmental damage. Extends coil lifespan and maintains surface finish. | Use rubber mats on trailers and storage racks. Apply edge protectors during transport and handling. Consider protective wrapping for coils stored outdoors or in harsh environments. Ensure protective materials are compatible with coil materials to avoid reactions or staining. |
By implementing these strategies, businesses can create a comprehensive damage prevention system, safeguarding coil quality and optimizing material utilization.
Leveraging Automation for Efficient Coil Handling
Automation in coil handling is transforming metal fabrication, offering significant advantages in efficiency, safety, and damage reduction. While initial investment costs may be a consideration, the long-term benefits of automated systems often outweigh the upfront expenses. Exploring automation possibilities can lead to substantial improvements in coil handling operations.
Automated coil handling systems, including automated guided vehicles (AGVs), robotic coil lifters, and automated storage and retrieval systems (AS/RS), streamline coil movement, reduce manual handling, and enhance overall efficiency. These systems offer increased speed, precision, and consistency in coil handling, minimizing damage and maximizing throughput. While implementation requires careful planning and investment, the benefits of automation in terms of productivity and safety are compelling. Embracing automation can position businesses for greater competitiveness and operational excellence.
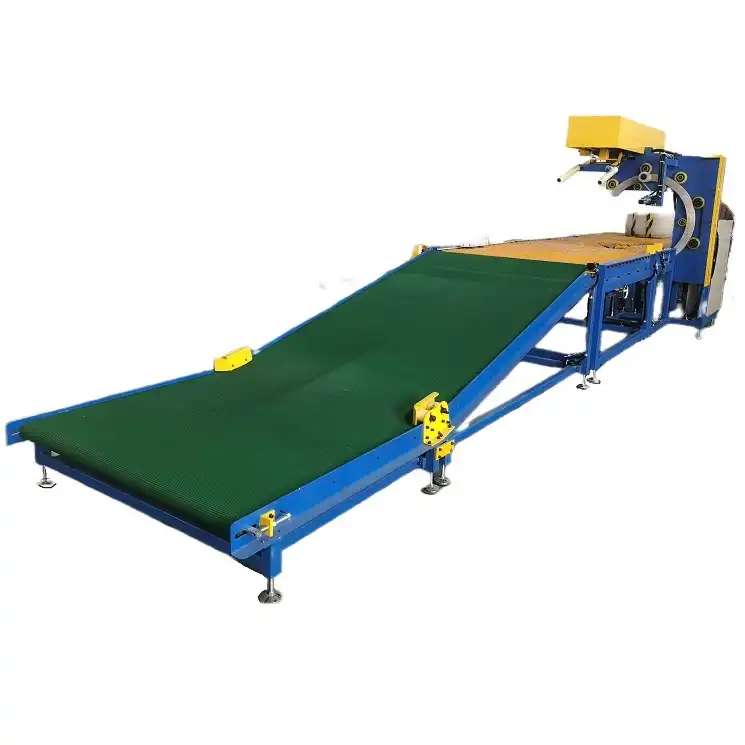
Automated coil handling systems offer a range of benefits, but also present certain challenges. A balanced perspective is crucial when considering automation implementation:
Benefits of Automated Coil Handling:
- Reduced Coil Damage: Automated systems handle coils with consistent precision, minimizing the risk of human error that can lead to dents, scratches, or dropped coils. Programmed movements ensure gentle handling and controlled placement.
- Increased Speed and Throughput: Automated systems operate faster than manual handling, reducing cycle times for coil loading, unloading, and transfer. This leads to higher production throughput and faster order fulfillment.
- Enhanced Safety: Automation removes human operators from close proximity to heavy coils and handling equipment, reducing the risk of workplace accidents and injuries. Safety sensors and interlocks further enhance operational safety.
- Improved Space Utilization: Automated storage and retrieval systems optimize vertical space utilization, increasing storage density and reducing the facility footprint required for coil inventory.
- Lower Labor Costs: Automation reduces the need for manual labor in coil handling, leading to lower labor costs and reduced reliance on skilled operators for repetitive tasks.
- Enhanced Inventory Management: Automated systems can be integrated with inventory management software, providing real-time tracking of coil location, quantity, and status. This improves inventory accuracy and reduces the risk of stockouts or overstocking.
Challenges of Automated Coil Handling:
- High Initial Investment: Implementing automated systems requires significant upfront capital investment in equipment, software, and system integration.
- Longer Lead Times: Customized automated systems may have longer lead times for design, manufacturing, and installation compared to standard equipment.
- Maintenance Requirements: Automated systems require regular maintenance and specialized technical support to ensure continuous operation and prevent breakdowns.
- Potential Safety Issues: While automation enhances safety, improper system design, maintenance, or operation can create new safety hazards. Thorough risk assessments and safety protocols are essential.
- Integration Complexity: Integrating automated systems with existing production lines and IT infrastructure can be complex and require specialized expertise.
- Job Displacement Concerns: Automation may lead to concerns about job displacement for manual coil handling personnel. Retraining and redeployment strategies are necessary to address these concerns.
Conclusion
Protecting steel coils during transport is not just about preventing damage; it’s about ensuring safety, efficiency, and profitability in metal fabrication operations. By carefully selecting and utilizing appropriate coil handling equipment, implementing best practices for safe transport and storage, and exploring the benefits of automation, businesses can significantly minimize coil damage, optimize workflows, and create a safer working environment. Investing in the right tools and knowledge is an investment in the long-term success of any metal forming business.