How to Use Coil Handling Equipment to Optimize Space Utilization
Are you struggling with coils dominating your facility, turning valuable space into a storage nightmare? Inefficient coil handling isn’t just a space issue; it’s a drain on productivity and a safety hazard. Imagine a workspace where every inch is maximized, operations flow smoothly, and safety is paramount.
This article reveals how coil handling equipment can revolutionize your space utilization. Optimizing your facility means smart storage, the right equipment choices, and best practices. Unlock space-saving strategies and transform your operations today.
Health and Safety Optimization in Coil Handling for Space Efficiency
Thinking space optimization means sacrificing safety? Think again. In coil handling, maximizing space and prioritizing health and safety are two sides of the same coin. Strategic planning in coil handling creates a safer and more efficient environment simultaneously.
Optimizing space utilization in coil handling goes hand-in-hand with enhanced safety, focusing on worker protection through PPE and training, implementing safe coil storage, and correctly using handling equipment. Prioritizing these measures minimizes workplace accidents, reduces liabilities, and creates a more organized, space-efficient facility by clearing clutter and ensuring safe pathways. A safe workspace is fundamentally a more efficient workspace.
Let’s explore detailed safety measures that not only optimize your space but also create a healthier and safer work environment.
Detailed Safety Measures for Space-Optimized Coil Handling
Optimizing space while ensuring top-notch safety in coil handling requires a comprehensive approach. Meticulous storage planning, consistent equipment maintenance, and thorough personnel training are crucial pillars. Let’s break down the specifics:
Personal Protective Equipment (PPE) and Safe Lifting Techniques
Worker safety begins with proper PPE. Gloves shield hands from sharp coil edges, safety glasses protect eyes from debris, and steel-toed boots prevent foot injuries from heavy loads. Protective clothing adds another layer of safety. Crucially, training in safe lifting techniques and the correct operation of equipment like gantry cranes, forklifts, and coil lifters is non-negotiable. Proper training drastically reduces strain injuries and accidents, fostering a safer, more productive workspace even in compact areas.
Steel Coil Storage and Safety Protocols
Efficient coil storage is the cornerstone of both space optimization and safety. Store coils on level surfaces, either "eye to the sky" or in designated racks. Racks must be robust enough to handle coil weights. Clear labeling of coils with weight and handling instructions is vital, alongside safety signage for pathways and hazard zones. Bulk coil racks and coil pallets are invaluable for vertical storage and mobile handling, especially in space-constrained areas. These methods guarantee stability, prevent coils from rolling or falling, and maximize vertical space utilization while maintaining safety.
Equipment Inspection and Safe Transport
Regular inspection and maintenance of all lifting equipment—gantries, cranes, forklifts, coil lifters—are essential to prevent equipment failure and accidents. Using the correct lifting attachments for coil dimensions and weight prevents damage and ensures secure handling. Clear loading/unloading procedures and secure coil transport within the facility are also crucial. Gantry systems, fixed or traveling, are key to safe, efficient material handling, minimizing downtime and maximizing space by streamlining coil movement and reducing maneuvering space.
To illustrate the impact, consider this comparison of safety measures:
Safety Measure | Space Optimization Benefit | Safety Enhancement | Implementation Cost |
---|---|---|---|
Vertical Coil Storage Racks | Maximizes vertical space; reduces floor clutter. | Prevents coil rolling/falling; improves stability. | Moderate |
Mobile Coil Pallets | Enables flexible storage and movement in tight spaces. | Reduces manual handling; safer transport within facility. | Low to Moderate |
Regular Equipment Maintenance | Ensures equipment reliability; prevents breakdowns. | Minimizes accident risk; extends equipment lifespan. | Low (Ongoing) |
Comprehensive Safety Training | Promotes safe handling practices in all areas. | Reduces worker injuries; fosters safety culture. | Low (Ongoing) |
Automated Gantry Systems | Streamlines material flow; reduces handling space. | Minimizes manual intervention; enhances precision. | High |
By thoughtfully implementing these safety measures, facilities can achieve both enhanced safety and optimized space utilization in their coil handling operations.
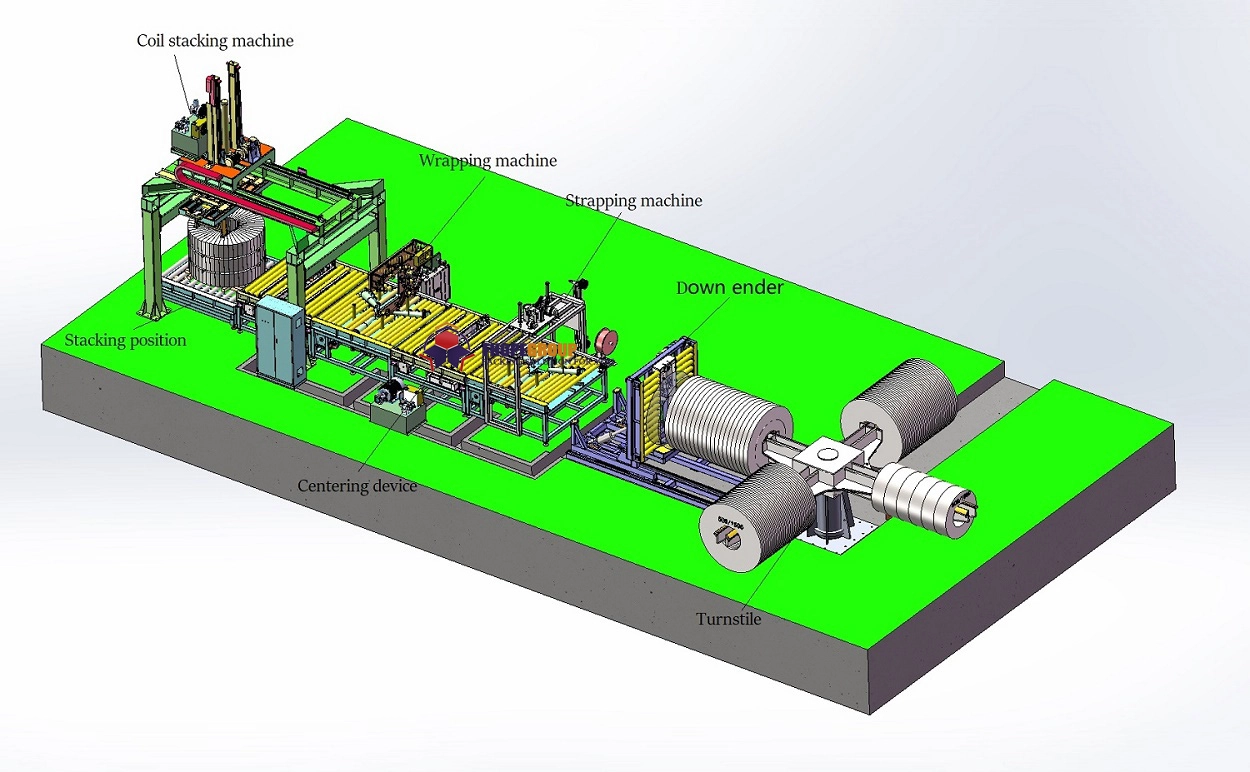
Streamlining Coil Handling for Business Efficiency and Space Saving
Beyond safety, optimizing coil handling equipment dramatically boosts business efficiency and unlocks valuable space. Efficient workflows, smart inventory management, and strong supplier relationships are key to maximizing productivity and spatial efficiency.
Streamlining steel coil handling business processes is vital for operational efficiency and maximizing space. This includes optimizing inventory to reduce unnecessary storage, designing efficient workflows to minimize coil movement, and maintaining equipment to prevent downtime. Focusing on these areas significantly improves productivity and space utilization.
Let’s explore strategies to streamline your coil handling processes, boosting both your bottom line and your available space.
Strategies for Efficient Coil Handling and Space Utilization
To achieve streamlined coil handling and optimal space utilization, businesses need to concentrate on key strategies:
Inventory Management and Workflow Design
A robust inventory management system is the foundation. Tracking coil quantities, locations, and specifications minimizes waste and prevents overstocking, directly reducing storage space needs. Simultaneously, designing efficient workflows is crucial. Optimizing storage and work area layouts to minimize unnecessary coil movement streamlines material transfer from storage to production. This reduces handling time, minimizes potential damage, and frees up valuable floor space previously used for staging or excessive movement.
Product Inspection, Supplier Relations, and Maintenance
Rigorous quality control for incoming coils ensures materials meet standards, preventing production delays and rework that consume time and space. Building strong relationships with reliable suppliers ensures timely delivery of quality coils, reducing the need for large on-site inventories and freeing up storage space. Finally, regular maintenance of coil handling equipment is essential. Preventive maintenance minimizes breakdowns, reduces downtime, and extends equipment lifespan, ensuring continuous, efficient operation within the optimized space.
Consider how these strategies impact business efficiency and space utilization:
Strategy | Business Efficiency Improvement | Space Optimization Benefit | Implementation Effort | Cost Savings Potential |
---|---|---|---|---|
Inventory Management System | Reduces waste; prevents overstocking; ensures material availability. | Minimizes storage space; reduces clutter. | Moderate | High |
Optimized Workflow Design | Streamlines material transfer; reduces handling time and costs. | Reduces material movement area; optimizes layout. | Moderate to High | High |
Rigorous Product Inspection | Prevents delays and rework; ensures consistent quality. | Reduces space for rework/rejected materials storage. | Moderate | Moderate to High |
Reliable Supplier Relations | Ensures timely delivery; improves supply chain reliability. | Reduces need for large buffer stock; optimizes storage planning. | Moderate | Moderate |
Preventive Maintenance | Minimizes downtime; extends equipment lifespan. | Reduces downtime-related space inefficiencies; ensures throughput. | Low (Ongoing) | Moderate to High |
By strategically implementing these business improvement strategies, companies can significantly enhance operational efficiency and maximize space utilization in coil handling.
101 Tips for Space-Saving Production with Coil Handling Equipment
Drawing on deep industry knowledge, numerous practical tips can boost production and save space using coil handling equipment. These range from equipment selection and installation to operational processes and material protection.
Optimizing production with coil handling equipment involves equipment selection, installation, and processes like uncoiling, straightening, and feeding. Many tips maximize space by streamlining operations and reducing unnecessary equipment or movement. Implementing these best practices significantly improves productivity and space efficiency.
Let’s dive into key tips, categorized for clarity, to truly maximize space and boost production.
Key Tips for Optimizing Space and Production
Equipment Selection and Installation for Space Efficiency
- Tip 3. Do not seek “catch-all” equipment: Avoid overly complex, universal coil lines. Simpler, specialized lines are often more efficient and space-saving for specific tasks.
- Tip 4. Select a system: Opt for integrated coil handling systems from a single source for better coordination and space optimization compared to piecemeal setups.
- Tip 8. Allow loop space, but optimize it: Provide adequate loop space for material slack, but avoid excessive horizontal loop areas that waste space.
- Tip 9. Allow service space, strategically: Ensure sufficient service space around equipment, but plan for compact layouts that minimize overall footprint.
- Tip 11. Lag equipment securely: Securely anchored equipment reduces vibration and misalignment, allowing for tighter layouts and safer operation in less space.
- Tip 15. Double stock reels: Utilize double stock reels to minimize coil changeover time, reducing downtime and maximizing throughput in a given space.
- Tip 16. Coil loading cars: Implement coil loading cars to streamline coil loading, reducing handling time and space needed for staging coils.
- Tip 17. Coil storage racks: Employ vertical coil storage racks to maximize vertical space utilization and minimize floor space occupied by coils.
Operational Tips for Space and Production Gains
- Tip 25. Hold-down peelers: Use hold-down peelers for efficient threading, reducing setup time and material waste, contributing to faster production cycles within the same space.
- Tip 33. Paddle loop control: Consider paddle loop controls for powered reels in space-constrained areas, minimizing horizontal loop space.
- Tip 38. Horizontal reels: For narrow coils prone to telescoping, horizontal pan-type reels can improve handling and reduce material waste, optimizing material usage within the space.
- Tip 54. Shorten loop area: Optimize the horizontal loop area to the minimum required for material slack, reclaiming valuable floor space.
- Tip 55. Use of looping pit or Tip 56. Elevating straighteners: Where vertical space is available but horizontal space is limited, consider looping pits or elevated straighteners to maximize slack accumulation vertically rather than horizontally.
- Tip 95. Stagger blanking: Implement stagger blanking techniques to maximize material utilization and minimize scrap, reducing material storage needs and waste disposal space.
- Tip 96. Coil-equipped dies: Utilize coil-equipped dies to streamline production and reduce material handling, improving efficiency within the existing footprint.
- Tip 98. Continuous running: Aim for continuous running of uncoiling and straightening equipment to minimize energy consumption and wear, maximizing throughput and efficiency within the space.
Here’s a table illustrating the impact of these tips:
Tip Category | Tip Description | Space Optimization Impact | Production Improvement Impact | Cost Implication |
---|---|---|---|---|
Equipment Selection | Specialized vs. Catch-all Lines | Reduced equipment footprint. | Higher efficiency for specific tasks. | Potentially Lower |
Installation | Optimized Loop Space | Reclaimed floor space. | Maintained material slack for feeding. | No Significant Change |
Storage | Vertical Coil Racks | Maximized vertical storage; reduced clutter. | Improved coil accessibility & organization. | Moderate Investment |
Operation | Hold-down Peelers | Faster threading; reduced setup space. | Minimized downtime for coil changes. | Low |
Material Usage | Stagger Blanking | Reduced material waste; smaller scrap. | Higher material utilization. | Low to Moderate |
Implementing these tips strategically allows manufacturers to significantly optimize coil handling, leading to substantial space savings and production improvements.
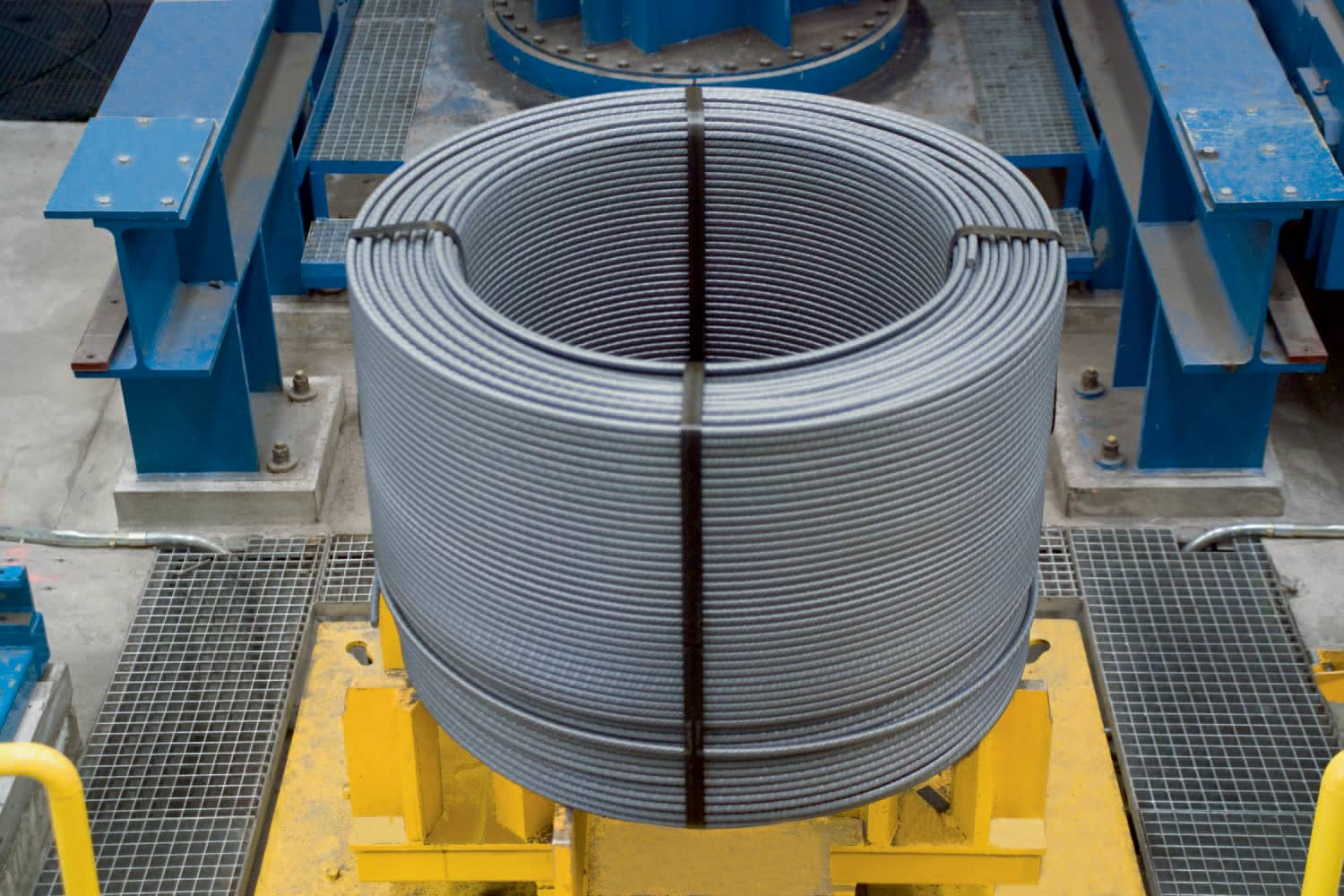
Optimizing Coil Tipper and Upender Handling for Space-Efficient Coil Rotation
Coil tippers and upenders are specialized equipment for efficient, safe coil rotation. Optimizing their use is crucial for maximizing space and streamlining material flow, especially when coils need processing in different orientations.
Coil tippers and upenders are vital for optimizing coil handling, offering controlled coil rotation methods. These machines are critical for space maximization, enabling efficient coil positioning for processes like decoiling, slitting, and stacking, minimizing manual handling and optimizing workflow in limited spaces.
Let’s explore how to effectively leverage coil tippers and upenders for space optimization.
Leveraging Coil Tippers and Upenders for Space and Efficiency
Applications and Types of Tippers and Upenders
Coil tippers excel at rotating coils from vertical to horizontal or vice versa, facilitating connections to decoilers or straighteners and adjusting coil orientation for processing tables. Upenders offer finer control for gradual rotation for inspection, precise tilting for cutting tables, and integration with downstream equipment. Types include rotary upenders for 360-degree rotation, tilting upenders for 90-degree tilts, and low-profile upenders for tight spaces. Choosing the right type for specific applications is key to space-efficient handling.
Features and Integration for Optimized Space Utilization
Standard features like heavy-duty construction, precise rotation mechanisms, and customizable controls ensure reliable, safe operation. Portable tippers offer flexibility across multiple lines, while custom-engineered solutions allow seamless integration within existing layouts, optimizing space within current facility constraints. Upenders with variable-speed drives and cradle assemblies tailored to coil sizes further enhance control and safety in space-optimized setups. Proper integration and feature selection ensure tippers and upenders significantly contribute to workflow efficiency and space savings.
Here’s a comparison of coil tippers and upenders:
Feature/Type | Coil Tipper | Coil Upender | Space Optimization Benefit | Application Focus |
---|---|---|---|---|
Rotation Type | Vertical to Horizontal (and vice versa) | Vertical to Horizontal (and 360° Rotary options) | Versatile orientation changes; optimizes material flow. | General orientation changes; decoiling; feeding lines. |
Control Precision | Standard Tipping Action | Finer Tilt Control; Variable Speed Options | Precise coil positioning; minimizes handling space. | Inspection; precision cutting; automated lines. |
Portability | Stationary and Portable Options | Primarily Stationary (some low-profile mobile designs) | Portable tippers offer flexible space utilization. | Flexible production layouts; serving multiple stations. |
Space Footprint | Moderate | Moderate to Larger (Rotary Upenders) | Tippers compact; Upenders offer vertical rotation advantages. | Compact layouts (Tippers); controlled rotation (Upenders). |
Integration Focus | Decoiler/Straightener Connection; General Handling | Integration with Straighteners, Feed Tables, Stackers | Streamlined in-line processes; reduced material staging. | Automated production lines; integrated systems. |
Carefully selecting and integrating coil tippers and upenders leads to significant space optimization and enhanced efficiency in coil handling.

Rugged and Customized Equipment for Space-Efficient Coil Handling
Investing in rugged, customized coil handling equipment is vital for long-term space optimization. Durable, low-maintenance equipment ensures consistent performance and reduces downtime, maximizing throughput within available space. Customization allows tailored solutions precisely fitting facility layouts and operational needs, further enhancing space efficiency.
Rugged and customized coil handling equipment is essential for maximizing space and long-term efficiency. This includes considering construction, maintenance, controls, and seamless integration. Durable, low-maintenance equipment ensures continuous operation, while customization optimizes integration and space utilization, addressing unique layout challenges and enhancing overall efficiency.
Let’s explore the critical aspects of rugged and customized equipment.
Investing in rugged, customized equipment means considering these key features:
-
Rugged Construction and Low Maintenance: Equipment built with structural steel frames, large-diameter bearings, and precision-cut gears ensures durability and long service life. Features like external lubrication ports and waterproof controls simplify maintenance and minimize downtime, maximizing operational uptime and throughput within the available space.
-
Intuitive Controls and Seamless Integration: User-friendly controls, including pendant stations, radio remotes, and programmable options like PLCs, simplify operation and reduce setup times. Seamless integration with existing lines through dimensional drawings, material flow modeling, and on-site support minimizes disruption and ensures optimized equipment placement within the facility’s layout.
-
Detailed Analysis and Data-Driven Decisions: A thorough assessment of coil parameters, production line requirements, and space constraints is crucial for selecting the right equipment. Cost-benefit analysis, including projected improvements in material flow, safety, and ROI, ensures informed decisions and justifies investments in space-optimizing solutions.
Consider the benefits of these features:
Feature | Benefit for Space Optimization | Benefit for Efficiency | Example Customization |
---|---|---|---|
Rugged Construction | Reduced downtime; consistent throughput. | Lower maintenance; extended lifespan. | Heavy-duty frames for high-capacity coils in limited space. |
Low Maintenance | Less space for maintenance and equipment storage. | Increased uptime; reduced labor costs for maintenance. | Self-lubricating bearings for hard-to-reach areas. |
Intuitive Controls | Faster setup and changeovers; less operator error in tight spaces. | Reduced handling time; improved precision and safety. | Touchscreen HMI for automated sequences in compact lines. |
Seamless Integration | Optimized equipment placement within existing space. | Streamlined material flow; minimized bottlenecks & congestion. | Custom risers and platforms for specific floor layouts. |
Detailed Analysis | Right-sized equipment; avoids over/under-sizing for space. | Data-driven decisions for maximum ROI and gains. | Optimized layout recommendations based on time studies. |
Focusing on rugged, customized equipment and data-driven decisions leads to truly space-efficient and highly productive coil handling operations.
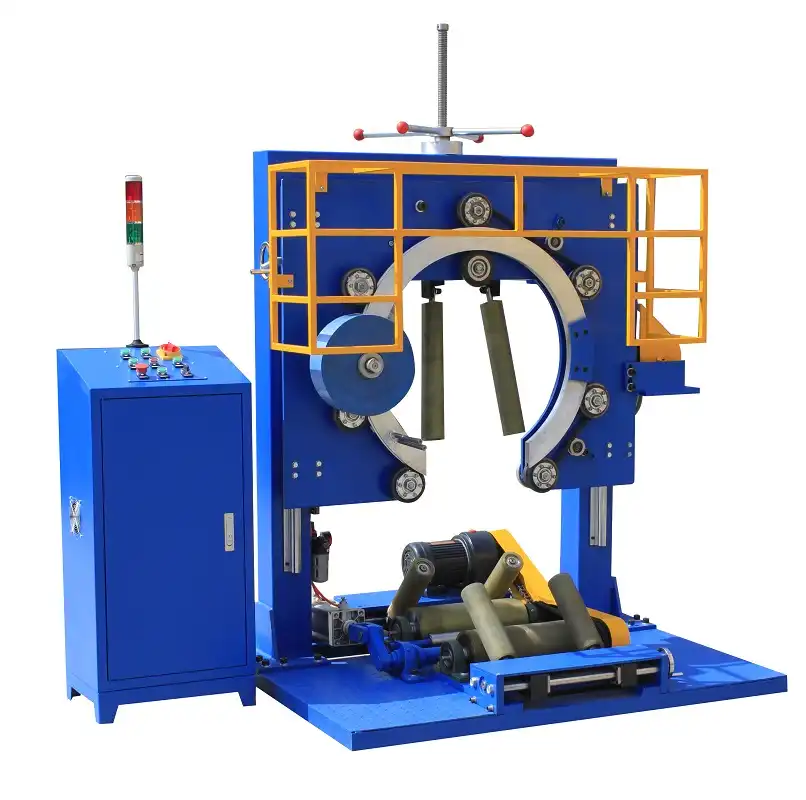
Conclusion
Optimizing coil handling equipment is more than just saving space; it’s about creating a safer, more efficient, and more profitable operation. Prioritizing health and safety, streamlining processes, implementing practical tips, and leveraging specialized equipment like coil tippers and upenders transforms space constraints into productivity opportunities. Investing in rugged, customized solutions ensures long-term efficiency and maximizes ROI in coil handling systems. Explore how these strategies can revolutionize your facility and unlock its full potential with advanced coil packing line solutions.