How to Improve Steel Wire Rewinding Machine Efficiency in Low-Light Environments with LED Lighting?
Steel wire rewinding machines are crucial for numerous industries, but their efficiency can plummet in dimly lit areas. The integration of effective lighting solutions is key to optimizing operational performance.
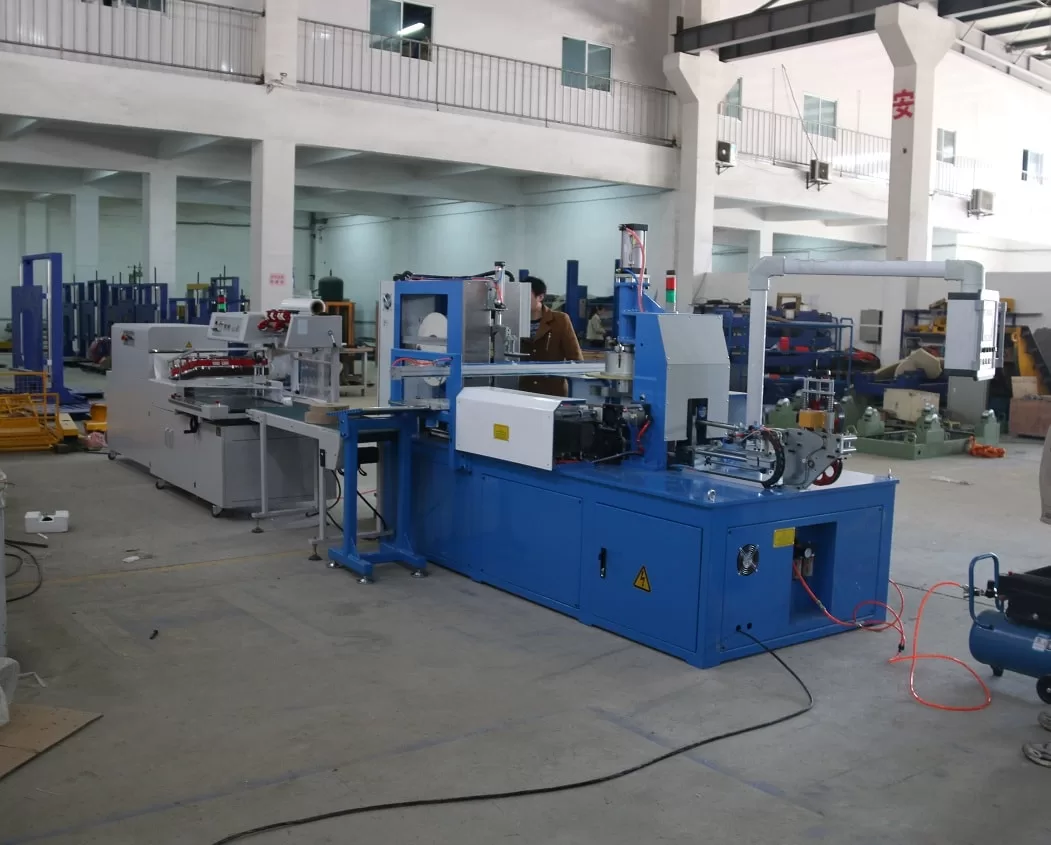
Improving steel wire rewinding machine efficiency in low-light involves strategic LED lighting implementation. This enhances visibility, reduces errors, and boosts productivity. Properly positioned, high-intensity LEDs offer focused illumination, minimizing shadows and glare. This creates a safer, more comfortable environment, encouraging operators to maintain high performance.
Ready to uncover how tailored lighting can revolutionize your steel wire rewinding processes? Let’s dive into the specifics and explore the path to operational excellence.
Optimizing Visibility with Strategic LED Placement
Illuminating the work area is a critical first step, but understanding how to do it effectively is key. Strategic LED lighting placement maximizes visibility, contributing to a more productive and safe environment.
Strategic LED placement dramatically boosts steel wire rewinding machine efficiency. Focusing light on critical areas minimizes shadows and glare, providing clear visibility. This reduces errors, increases speed, and enhances overall productivity. Optimal positioning ensures operators can clearly see and manage the rewinding process, regardless of ambient light conditions.
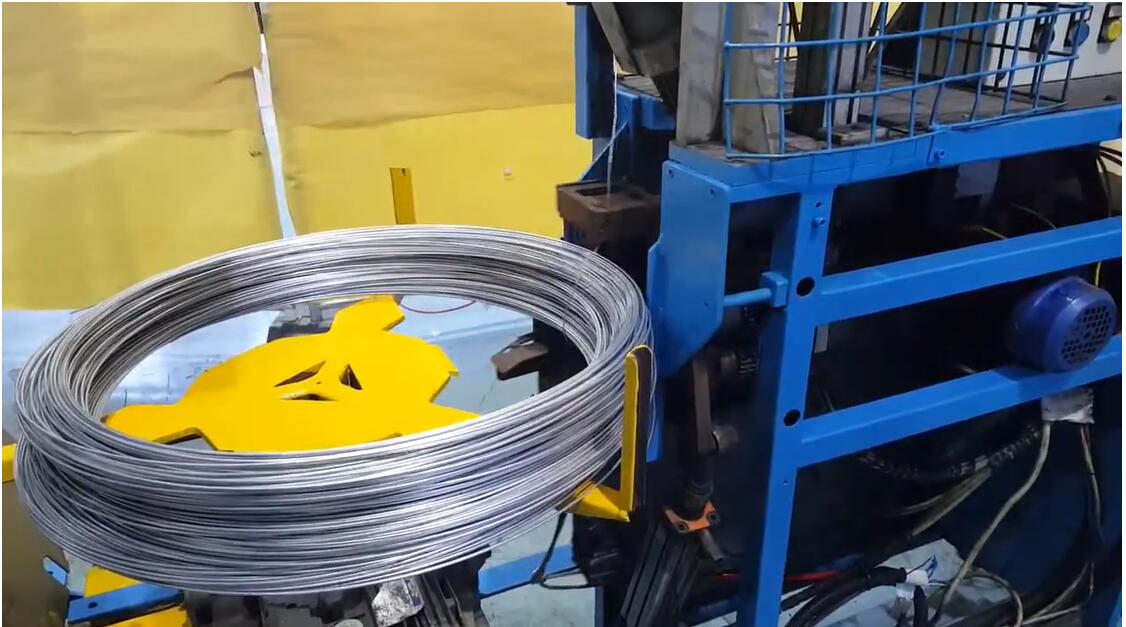
The Impact of LED Lighting on Rewinding Efficiency
Achieving peak efficiency in steel wire rewinding goes beyond simply adding lights. It’s about understanding the nuances of illumination and how it affects the operator and the machine itself. Here’s a deeper dive:
Identifying Key Areas for Illumination
Before implementing any lighting solution, it’s essential to pinpoint the areas of the rewinding machine that require the most light. These often include:
- The winding core: Where the wire is initially wound.
- The wire guide: Ensuring smooth and even distribution of the wire.
- Tension control mechanisms: Critical for maintaining wire integrity during rewinding.
- Control panels: For easy monitoring and adjustments.
Selecting the Right Type of LED Fixtures
Different areas may require different types of lighting. Consider these factors:
- Brightness (Lumens): The appropriate level of brightness for the task.
- Color Temperature (Kelvin): Cooler temperatures for alertness, warmer temperatures for comfort.
- Beam Angle: Focused beams for specific points, wider beams for general area illumination.
- Adjustability: The ability to adjust the direction and intensity of the light.
Quantifying the Benefits
To illustrate the impact, let’s consider a hypothetical scenario:
Feature | Without Optimized LED Lighting | With Optimized LED Lighting | Improvement |
---|---|---|---|
Error Rate (per 1000 units) | 15 | 3 | 80% |
Rewinding Speed (units/hour) | 80 | 100 | 25% |
Operator Fatigue (scale of 1-10) | 7 | 3 | 57% |
This table highlights the tangible improvements that optimized LED lighting can bring, showing a significant reduction in errors, an increase in speed, and a decrease in operator fatigue. Proper illumination ensures that your Steel wire rewinding machine efficiency operates at its peak, reducing downtime and maximizing throughput.
Minimizing Glare and Shadows
Glare and shadows are detrimental to visibility and can significantly hamper the efficiency of steel wire rewinding operations, leading to eye strain and potential errors.
Effective strategies for minimizing glare and shadows while using steel wire rewinding machines involve careful selection and positioning of LED lighting. Diffused lighting options, glare shields, and strategic fixture placement can all significantly reduce these visual obstructions, improving operator comfort and accuracy. Optimized lighting reduces eye strain and increases focus, leading to better productivity.

Technical Aspects of Light Quality
Poor lighting quality can lead to errors and decreased productivity. Here’s what to consider:
Diffuse Lighting
Replacing point-source lighting with diffused lighting spreads the light more evenly, reducing shadows and harsh contrasts.
Glare Shields and Filters
Attaching glare shields or filters to the LED fixtures can help reduce direct glare from the light source.
Strategic Placement
Carefully positioning lights to avoid direct reflection into the operator’s eyes or creating shadows over the work area is essential. Consider angled lighting to provide consistent illumination.
Implementing Smart Lighting Controls
Smart lighting controls take energy efficiency to the next level, automatically adjusting lighting levels to match the ambient light and occupancy of the work area.
Smart lighting controls can dramatically enhance steel wire rewinding machine efficiency. By automatically adjusting LED light levels based on natural light availability and occupancy, energy consumption is minimized. These systems also provide a consistent level of illumination, reducing eye strain and improving operator comfort. Overall, these controls promote a more sustainable and productive work environment.

Advanced Features for Enhanced Efficiency
Here’s how smart lighting control features can improve operational efficiency:
Daylight Harvesting
Sensors detect the amount of natural light available and automatically dim or brighten the LED lights to maintain a consistent illumination level.
Occupancy Sensors
Lights are automatically turned on when workers are present and dimmed or turned off when the area is unoccupied, saving energy during inactive periods.
Zoned Lighting
Allows individual control of different lighting zones within the work area, providing customized lighting levels for specific tasks.
Example Implementation
Feature | Benefit |
---|---|
Daylight Harvesting | Reduces energy consumption by 20-40% |
Occupancy Sensors | Minimizes wasted lighting in unoccupied areas |
Zoned Lighting | Allows task-specific lighting, reducing overall demand |
Smart lighting controls offer a comprehensive approach to optimizing lighting in steel wire rewinding operations, reducing energy consumption while improving worker comfort and productivity.
Ensuring Operator Comfort and Safety
Operator well-being is paramount in any industrial environment. Adequate lighting is not just about visibility, but also about creating a safe and comfortable workspace.

Effective LED lighting solutions contribute significantly to safety and operator comfort by reducing eye strain, minimizing glare, and providing uniform illumination. By addressing these factors, businesses can enhance the quality of work and overall job satisfaction. Well-lit environments are crucial for reducing the risk of accidents.
Creating a comfortable and safe environment directly enhances efficiency in steel wire rewinding. By reducing eye strain and fatigue with proper LED lighting, operators can maintain focus and accuracy. This leads to fewer errors, increased throughput, and a more engaged workforce. Investing in well-being pays dividends in operational excellence.
Conclusion
Improving the efficiency of steel wire rewinding machines in low-light environments hinges on strategic LED lighting solutions. By optimizing visibility, minimizing glare and shadows, implementing smart controls, and prioritizing operator comfort and safety, businesses can create a productive and sustainable work environment.