How to Enhance PVC Pipe Bagging Machine Performance with Advanced Sensors?
Ensuring your PVC pipe bagging machine operates at peak efficiency is crucial for maintaining productivity and minimizing downtime. Utilizing advanced sensors can significantly improve machine performance, providing real-time data and enabling proactive maintenance strategies.
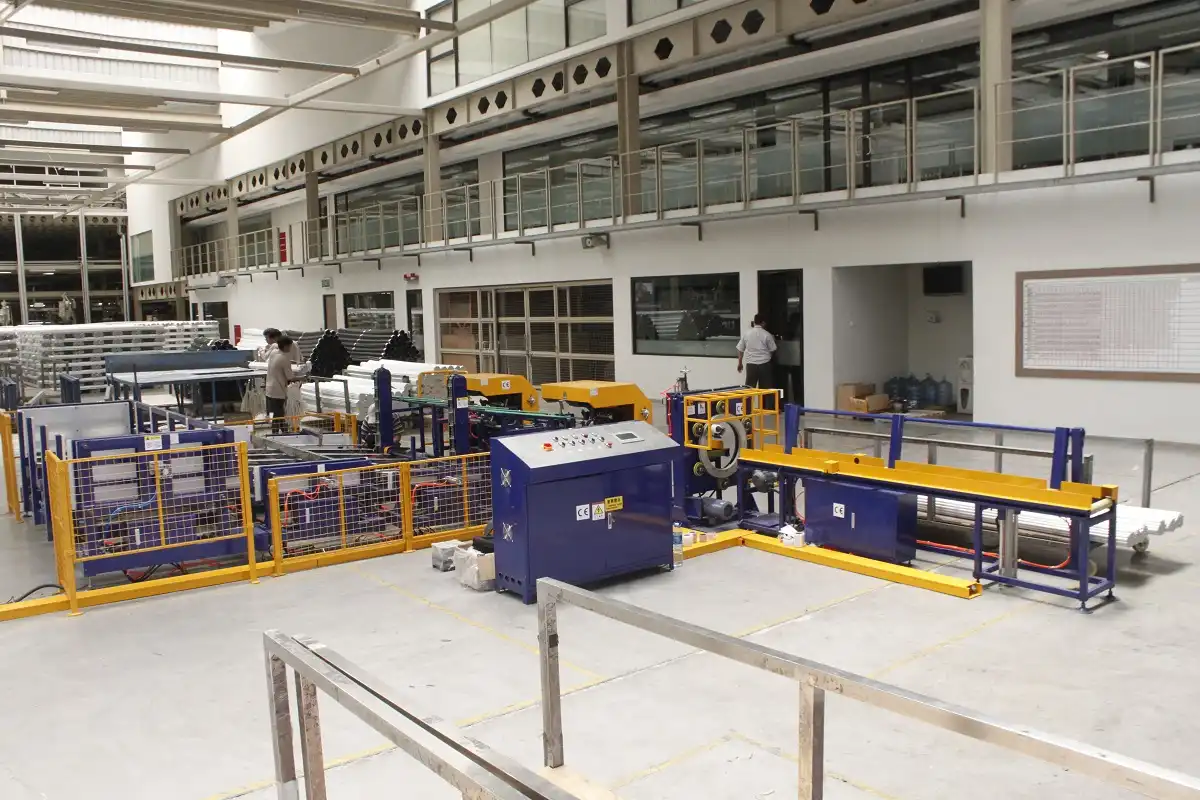
Advanced sensors enhance PVC pipe bagging machine performance by providing real-time monitoring of critical parameters, enabling timely adjustments and predictive maintenance. This proactive approach minimizes downtime, reduces material waste, ensures consistent bag quality, optimizes machine lifespan, and improves overall operational efficiency, leading to increased productivity and cost savings.
Transitioning to sensor-driven performance enhancement requires a comprehensive understanding of available technologies and their strategic implementation. Let’s explore how advanced sensors can revolutionize your PVC pipe bagging operations.
1. Understanding the Role of Sensors in PVC Pipe Bagging Machines
PVC pipe bagging machines rely on precise timing and coordination to ensure efficient and secure packaging. Advanced sensors offer real-time feedback on various machine parameters, allowing for immediate adjustments and preventative actions.
Advanced sensors are critical for real-time monitoring of key parameters in PVC pipe bagging machines, such as temperature, pressure, vibration, material presence, and bag dimensions. This data-driven insight enables precise control, immediate error detection, and informed decision-making, optimizing performance and minimizing potential failures.
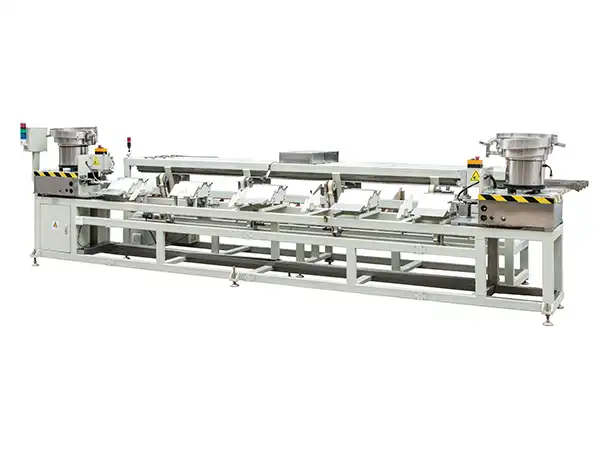
To fully appreciate the impact of sensors, let’s examine how they compare to traditional monitoring methods and understand the distinct advantages they bring to the table.
Sensor-Based Monitoring vs. Traditional Methods: A Detailed Comparison
The table below highlights the key differences between sensor-based monitoring and traditional methods in PVC pipe bagging machines, demonstrating the superior benefits of sensor technology for optimizing performance and reducing downtime. Implementing a proactive approach is more efficient than a reactive one in this industry.
Predictive vs. Preventive vs. Reactive Monitoring
Feature | Reactive Monitoring | Preventive Monitoring | Sensor-Based Monitoring |
---|---|---|---|
Data Source | None (Post-Failure) | Historical Data, Scheduled Checks | Real-time Sensor Data |
Intervention Timing | After Breakdown | Fixed Intervals | Based on Real-Time Condition |
Downtime Impact | Highest (Unplanned) | Medium (Planned) | Lowest (Optimized) |
Waste Reduction | Least Efficient | Moderate Efficiency | Most Efficient |
Suitability | Simple Machines | Machines with Known Wear | Complex, Critical Bagging Machines |
This comparison illustrates the advantages of sensor-based monitoring, particularly for complex systems like PVC pipe bagging machines. By transitioning from reactive or preventive approaches to sensor-driven predictive maintenance, manufacturers can significantly enhance operational efficiency and minimize costly downtime.
2. Types of Advanced Sensors for PVC Pipe Bagging Machines
The effectiveness of sensor-based performance enhancement hinges on selecting the appropriate sensors for monitoring critical machine functions. Here’s a look at some essential sensor types and their applications in PVC pipe bagging machines.
To optimize PVC pipe bagging machine performance, utilize advanced sensors like photoelectric sensors for material detection, load cells for weight measurement, ultrasonic sensors for distance and dimension monitoring, temperature sensors for heat sealing control, and vibration sensors for early detection of mechanical issues.
Let’s delve deeper into the specific applications and benefits of each sensor type, exploring how they contribute to enhanced machine performance and overall efficiency.
Detailed Look into Sensor Technology
Photoelectric Sensors:
These sensors detect the presence or absence of PVC pipes or the bag itself at various stages of the bagging process. By ensuring accurate material positioning, photoelectric sensors prevent misaligned bags and jams.
Load Cells:
Load cells provide precise weight measurements, guaranteeing accurate filling of each bag. This minimizes material waste, prevents overweight bags (which can lead to seal failures), and ensures consistent product output.
Ultrasonic Sensors:
Ultrasonic sensors measure distances and dimensions, ensuring the correct bag size and precise positioning of the sealing mechanism. This results in consistent and reliable seals, preventing leaks and maintaining product integrity.
Temperature Sensors:
Temperature sensors are crucial for monitoring and controlling the heat sealing process. Maintaining the optimal temperature ensures a strong and reliable seal, preventing bag failures and maintaining product quality.
Vibration Sensors:
These sensors detect abnormal vibrations in motors, bearings, and other moving parts. Early detection of unusual vibrations allows for proactive maintenance, preventing costly breakdowns and extending machine lifespan.
Encoders:
Encoders track the position and speed of rotating components, synchronizing the bagging process. Precise control of component movement ensures smooth operation and prevents timing errors.
Pressure Sensors:
Pressure sensors monitor pneumatic or hydraulic systems, ensuring optimal performance. By maintaining correct pressures, these sensors prevent system failures and ensure consistent bagging operations.
By strategically implementing these advanced sensors, manufacturers can gain valuable insights into machine performance and proactively address potential issues before they escalate into major problems.
3. Data Analysis and Interpretation for Proactive Intervention
The wealth of data generated by advanced sensors is only valuable if it can be effectively analyzed and interpreted. This process transforms raw sensor data into actionable intelligence, guiding maintenance actions and optimizing PVC pipe bagging machine performance.
Analyzing sensor data to proactively intervene in PVC pipe bagging machine operations involves identifying patterns and anomalies that indicate potential failures. By setting thresholds and generating alerts, maintenance teams can schedule timely interventions, minimizing downtime and maximizing machine efficiency.
Let’s explore the key steps involved in data analysis and interpretation, demonstrating how actionable insights can be derived from raw sensor data.
From Data to Action: A Step-by-Step Guide
Data Type | Sensor | Potential Issue Indicated | Actionable Insight |
---|---|---|---|
Temperature Data | Thermal Imagers | Overheating sealing element | Check sealing element functionality, adjust settings |
Vibration Data | Accelerometers | Increased vibration in motor | Inspect motor bearings, check alignment |
Pressure Data | Pressure Transducers | Fluctuating pressure in pneumatic system | Check for leaks, inspect compressor |
Material Presence | Photoelectric Sensors | Intermittent material detection | Clean sensor, check alignment, adjust sensitivity |
Bag Dimensions | Ultrasonic Sensors | Inconsistent bag lengths | Calibrate sensor, check film feed mechanism |
Data analytics techniques should include pattern recognition, anomaly detection, and predictive modeling, transforming data into actionable strategies. This allows operators to make informed decisions, optimize performance, and preemptively address potential problems.
Data Collection:
Continuous collection of sensor data from various points on the PVC pipe bagging machine is crucial for a comprehensive overview of its health.
Data Pre-processing:
Raw sensor data often contains noise and inconsistencies. Cleaning and formatting the data ensures accuracy and reliability for subsequent analysis.
Feature Extraction:
Identifying relevant features within the data, such as temperature trends, vibration frequencies, or pressure fluctuations, is essential for understanding machine behavior.
Predictive Modeling:
Using algorithms to create models that predict future machine conditions based on current and historical data enables proactive maintenance planning.
Alert Generation:
Setting thresholds for key parameters that, when exceeded, trigger alerts to the maintenance team ensures timely intervention and prevents potential failures.
By following these steps, manufacturers can effectively leverage sensor data to enhance the performance and reliability of their PVC pipe bagging machines.
4. Implementing a Sensor-Driven Maintenance Strategy
Effectively integrating advanced sensors into a PVC pipe bagging machine maintenance program requires a strategic approach that considers both technology and personnel training.
Implementing a sensor-driven maintenance strategy involves careful planning, technology deployment, data integration, and continuous refinement.
Successfully implementing a sensor-driven maintenance strategy involves:
–Planning & Assessment: Determine which aspects of PVC pipe bagging operations would benefit most from sensor data.
–Deployment: Strategically install sensors.
–Integration: Utilize a platform for data visualization and analysis.
–Training: Teach personnel how to interpret data and address alerts.
Data-Driven Optimization: Continuously monitor performance and refine models.
Transitioning from reactive to sensor-driven maintenance not only enhances machine performance but also requires cultivating a culture of proactive maintenance.
Conclusion
Advanced sensors represent a powerful tool for optimizing PVC pipe bagging machine performance. By providing real-time data and enabling proactive maintenance, these technologies can significantly reduce downtime, minimize material waste, and improve overall operational efficiency. Embracing sensor-driven maintenance positions businesses for sustained success in a competitive market, aligning with the principles of smart manufacturing and Industry 4.0. (100 words)