How to Choose the Right Plastic Pipe Bagging Machine for Your Factory?
Selecting the correct plastic pipe bagging machine is crucial for optimizing your factory’s efficiency. It impacts production speed, reduces labor costs, and ensures product protection during handling and transportation.
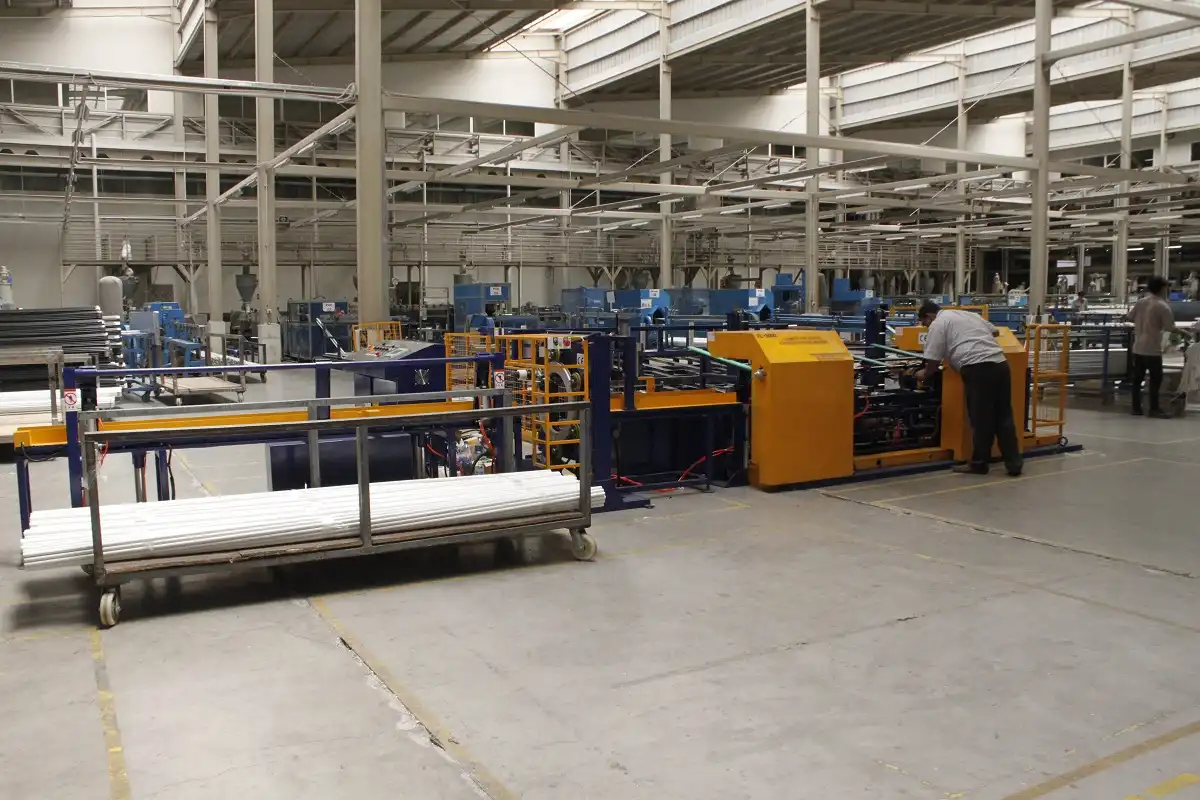
Choosing the right machine involves assessing your production volume, pipe dimensions, material types (PVC, PPR, HDPE), and desired automation level. Consider factors like bagging speed, bag sealing method, and the machine’s integration with your existing production line for seamless operation and maximized output.
Investing in the appropriate plastic pipe bagging machine can significantly improve your operational effectiveness. Let’s delve into the key considerations to make an informed decision and unlock the potential for enhanced productivity and profitability.
1. Understanding Your Pipe Packaging Needs
Choosing the right plastic pipe bagging machine begins with a thorough understanding of your specific requirements. Different pipe dimensions, production volumes, and material types will dictate the features and capabilities you need in a bagging solution.
Before selecting a Plastic pipe bagging machine, analyze your current and projected production output, the range of pipe sizes you manufacture, and the specific bagging requirements for each product. This assessment will guide you in identifying a machine that aligns with your factory’s unique needs and optimizes your packaging process.
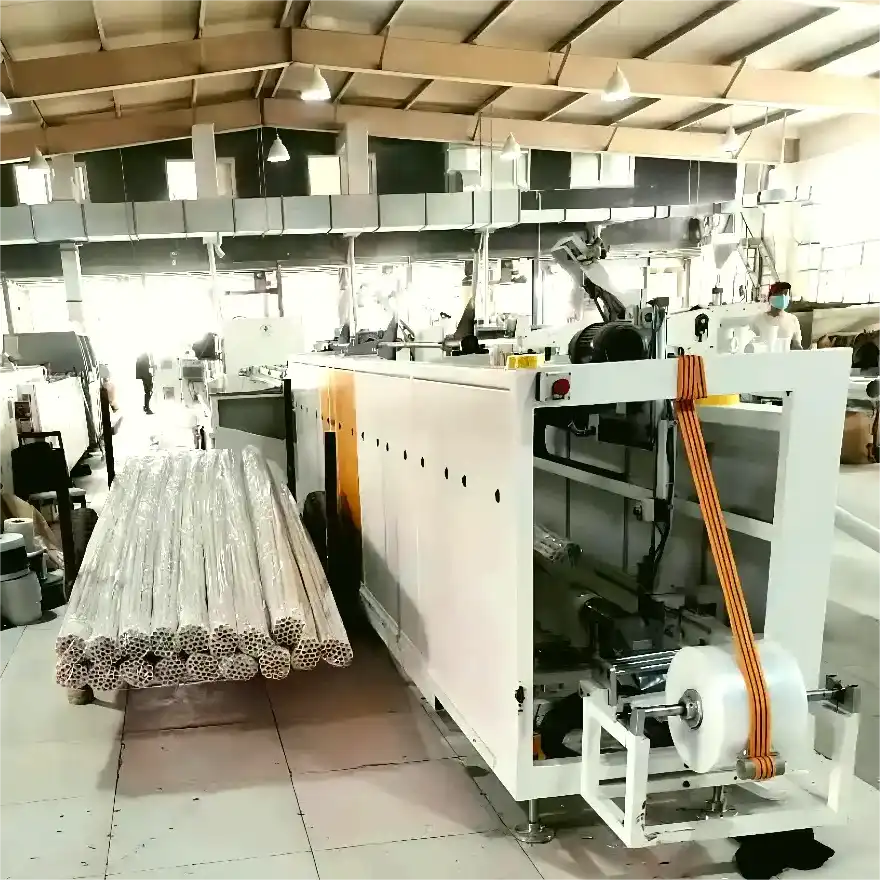
Key Considerations for Pipe Bagging Machine Selection
To select the correct bagging machine you should deep dive into the following three key considerations:
Pipe Dimensions and Material
Production Volume and Speed
Automation and Integration.
To select the correct bagging machine you should deep dive into the following three key considerations:
1. Pipe Dimensions and Material
The dimensions and material of your pipes are fundamental factors in selecting a suitable bagging machine. Different machines are designed to handle specific pipe diameters and lengths. The material composition, such as PVC, PPR, or HDPE, also influences the bagging process. For instance, thicker pipes might require more robust sealing mechanisms. Consider the following:
- Diameter Range: What is the minimum and maximum diameter of the pipes you need to bag?
- Length Range: What is the minimum and maximum length of the pipes?
- Material Type: Are you primarily working with PVC, PPR, HDPE, or a mix of materials?
- Weight: What is the weight range of the individual pipes?
2. Production Volume and Speed
Your production volume directly impacts the required bagging speed and overall machine capacity. If you have high-volume production, you’ll need a machine that can keep pace without creating bottlenecks. Consider:
- Current Production Volume: How many pipes do you need to bag per hour or per day?
- Projected Growth: Do you anticipate an increase in production volume in the future?
- Bagging Speed: What is the required bagging speed (bags per minute or pipes per hour) to meet your production targets?
- Continuous Operation: Does the machine need to operate continuously for extended periods?
3. Automation and Integration
The level of automation and the ability to integrate the bagging machine with your existing production line are crucial for maximizing efficiency. Automation features can reduce labor costs and improve accuracy, while seamless integration streamlines the entire packaging process. Consider:
- Level of Automation: Do you need a fully automatic machine or a semi-automatic one?
- Integration Capabilities: Can the machine be easily integrated with your existing pipe extrusion line or cutting station?
- Automatic Feeding: Does the machine have an automatic pipe feeder to ensure a consistent flow of pipes?
- Bag Sealing: What type of bag sealing is required (heat sealing, tape wrapping, sewing)?
- Control System: Does the machine have a user-friendly control system for easy operation and adjustments?
Feature | Consideration | Impact on Selection |
---|---|---|
Pipe Dimensions | Diameter, Length, Weight | Determines the physical capacity and handling capabilities of the machine. |
Material Type | PVC, PPR, HDPE | Influences the required sealing method and bag material compatibility. |
Production Volume | Current & Projected Output | Dictates the required bagging speed and overall machine throughput. |
Automation Level | Fully Automatic, Semi-Automatic | Impacts labor costs, operational efficiency, and integration with existing production lines. |
Bag Sealing | Heat Sealing, Tape Wrapping, Sewing | Determines the type of sealing mechanism required and the aesthetic appearance of the final packaged product. |
Integration | Existing Production Line Compatibility | Ensures seamless workflow and eliminates potential bottlenecks in the packaging process. |
Control System | User-Friendly Interface, Data Logging | Facilitates easy operation, monitoring, and troubleshooting. |
Budget | Initial Investment, Operating Costs, Maintenance | Balances the desired features and capabilities with the financial constraints of the project. |
2. Evaluating Different Types of Plastic Pipe Bagging Machines
Plastic pipe bagging machines come in various configurations, each designed to meet specific needs. Understanding the different types available will help you narrow down your options and select the best fit for your factory.
There are two primary methods for packaging pipes: bundling and bagging. Bagging involves individually sealing each pipe in a bag. Some machines combine bundling and bagging for added protection and efficiency. Choose a machine that aligns with your production needs.
Diving into the Technical Specifications and Key Components
Understanding the types available is not enough for a purchase. A deep diving into the technical specifications and key components is a must.
Automation Level.
Bagging Material.
Bagging Speed.
1. Automation Level
The automation level is a key differentiator among bagging machines. Options range from manual to fully automatic systems.
- Manual Bagging Machines: These machines require significant manual labor. Operators load pipes into bags and seal them manually. They are suitable for low-volume production or situations where flexibility is needed.
- Semi-Automatic Bagging Machines: These machines automate some aspects of the bagging process, such as bag sealing or pipe feeding, while still requiring manual intervention.
- Automatic Bagging Machines: These machines automate the entire bagging process, from pipe feeding and bag filling to sealing and discharge. They are ideal for high-volume production and minimize labor costs.
2. Bagging Material
The type of material used for bagging is a critical consideration, as it impacts the protection and presentation of your pipes. Common bagging materials include:
- Polyethylene (PE) Film: PE film is a cost-effective and versatile option for general pipe packaging. It provides basic protection against dust and moisture.
- Woven Bags: Woven bags are more durable and resistant to tearing than PE film. They are often used for heavier pipes or those requiring more robust protection.
- Stretch Film: Stretch film can be used to wrap individual pipes or bundles of pipes. It provides a tight and secure packaging solution.
3. Bagging Speed
The bagging speed, measured in bags per minute (BPM) or pipes per hour, is a crucial factor for high-volume production. Choose a machine with a bagging speed that meets or exceeds your production targets. Consider the following:
- Machine Throughput: What is the maximum number of bags or pipes the machine can process per hour?
- Real-World Performance: What is the actual bagging speed you can expect under typical operating conditions?
- Adjustability: Can the bagging speed be adjusted to accommodate different pipe sizes and production volumes?
Machine Type | Automation Level | Bagging Material Options | Bagging Speed | Advantages | Disadvantages |
---|---|---|---|---|---|
Manual Bagging Machine | Manual | PE Film, Woven Bags | Low | Low initial cost, high flexibility | High labor costs, low throughput |
Semi-Automatic Machine | Semi-Automatic | PE Film, Woven Bags | Medium | Lower labor costs, increased throughput | Still requires some manual intervention |
Automatic Bagging Machine | Automatic | PE Film, Woven Bags, Stretch Film | High | Lowest labor costs, highest throughput, consistent packaging quality | Higher initial cost, less flexibility |
3. Key Features and Technical Specifications to Look For
Selecting the appropriate plastic pipe bagging machine necessitates focusing on essential features and technical specifications. These determine the machine’s efficiency, reliability, and suitability for your factory’s needs.
When evaluating machines, pay attention to features like automatic feeding, precise cutting units, reliable sealing mechanisms, and user-friendly control systems. Consider the power and air supply requirements, as well as the machine’s overall dimensions to ensure it fits within your factory layout. A machine that incorporates these features is able to increase efficiency and accuracy
Evaluating Essential Machine Features
These can often get overlooked when purchasing equipment that is expensive so here is what we will look at:
Automatic Feeding and Collection
Precision Cutting Unit
Reliable Sealing Mechanism
1. Automatic Feeding and Collection
An automatic feeder ensures a continuous and consistent supply of pipes to the bagging machine, minimizing manual handling and maximizing throughput. A collection system efficiently gathers the bagged pipes for further processing or storage. Key considerations include:
- Feeder Capacity: How many pipes can the feeder hold at a time?
- Feeding Speed: Can the feeding speed be adjusted to match the bagging speed?
- Pipe Alignment: Does the feeder ensure proper alignment of the pipes before bagging?
- Collection Method: How are the bagged pipes collected (e.g., conveyor belt, stacking system)?
2. Precision Cutting Unit
A precise cutting unit ensures that the bags are cut to the correct length, minimizing material waste and creating a neat and professional-looking package. Key considerations include:
- Cutting Accuracy: What is the accuracy of the cutting unit (e.g., +/- 1mm)?
- Cutting Method: What type of cutting mechanism is used (e.g., blade, hot wire)?
- Adjustability: Can the cutting length be easily adjusted to accommodate different pipe sizes?
3. Reliable Sealing Mechanism
A reliable sealing mechanism ensures that the bags are securely sealed, protecting the pipes from dust, moisture, and damage. Different sealing methods are available, each with its own advantages and disadvantages:
- Heat Sealing: Heat sealing uses heat to fuse the bag material together. It is a common and cost-effective sealing method.
- Tape Wrapping: Tape wrapping uses adhesive tape to seal the bag. It is a quick and easy sealing method, but it may not be as secure as heat sealing.
- Sewing: Sewing uses thread to sew the bag closed. It is a very secure sealing method, but it is also more time-consuming and expensive.
Feature | Consideration | Impact on Machine Performance |
---|---|---|
Automatic Feeding | Capacity, Speed, Alignment | Maximizes throughput, minimizes manual handling, ensures consistent pipe presentation |
Precision Cutting | Accuracy, Method, Adjustability | Minimizes material waste, creates neat and professional-looking packages, accommodates different pipe sizes |
Reliable Sealing | Method (Heat, Tape, Sewing), Seal Strength | Protects pipes from dust, moisture, and damage, ensures package integrity |
Control System | User-Friendliness, Programmability | Facilitates easy operation, monitoring, and troubleshooting, allows for customization and optimization of the bagging process |
Power and Air Supply | Voltage, Consumption, Pressure | Ensures compatibility with your factory’s infrastructure, minimizes energy costs, guarantees sufficient power for operation |
Machine Dimensions | Footprint, Height, Weight | Ensures the machine fits within your factory layout, allows for easy installation and maintenance |
Safety Features | Emergency Stops, Guards, Sensors | Protects operators from injury, prevents damage to the machine |
4. Installation, Maintenance, and Support
Proper installation is vital for optimal performance. Look for manufacturers offering comprehensive support, including training and readily available spare parts. Regular maintenance extends machine life. Choose a supplier providing reliable technical assistance to minimize downtime.
Selecting a Plastic pipe bagging machine requires a complete understanding of the process and you are one step closer to that. The decision to purchase a bagging machine will give your Factory Efficiency a great boost!
Conclusion:
Choosing the right plastic pipe bagging machine is a strategic decision that can significantly impact your factory’s efficiency and profitability. By carefully assessing your specific needs, evaluating different machine types, considering key features and technical specifications, and prioritizing reliable support, you can select a machine that aligns with your goals and delivers long-term value.