Guide Line of the Coil Car for Steel Coil Handling
Are you struggling with the unsafe and inefficient movement of heavy steel coils in your service center? Imagine a streamlined process where steel coils glide effortlessly from rewinder to packing line, enhancing both safety and productivity. It’s not just a dream; it’s achievable with the right coil car system.
Coil cars are specialized industrial vehicles designed to safely and efficiently transport heavy steel coils within manufacturing and service center environments, integrating seamlessly with coil rewinding and packing lines to optimize material flow and reduce handling time. These vehicles come in various types, each tailored to specific operational needs, ensuring smooth material transfer, minimizing downtime, and upholding stringent quality standards in steel coil processing.
This guide will illuminate the path to optimizing your coil handling process. Let’s explore the essential guidelines for implementing coil cars and discover how they can revolutionize your steel coil handling operations.
Coil Car with V-Shape Cradle
Are you tired of juggling different coil sizes and struggling with unstable transport methods? The V-shape cradle coil car offers a robust and adaptable solution. Picture a vehicle specifically engineered to cradle and secure steel coils of varying dimensions, ensuring stability and preventing damage during transit. This is the promise of the V-shape cradle design.
V-shape cradle coil cars are industrial vehicles equipped with a V-shaped structure to securely hold and transport steel coils of different diameters, featuring robust steel frames, wheels for mobility, and often hydraulic systems for lifting and safety mechanisms to prevent coil shifting during movement. These coil cars are essential for integrating coil rewinders with packing lines, offering increased safety, reduced material damage, and enhanced efficiency in coil handling operations within service centers.
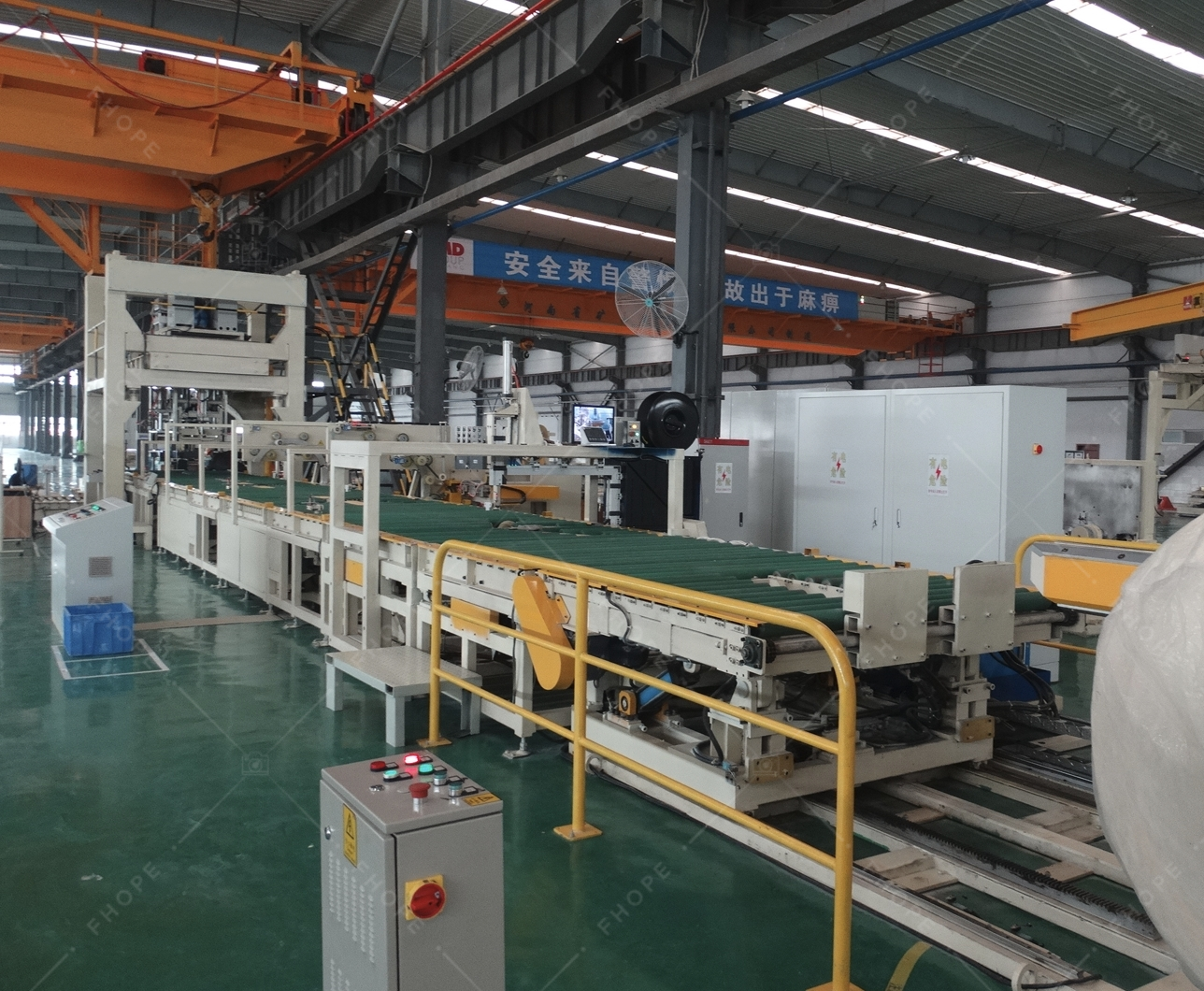
But how do you choose the right V-shape cradle coil car for your specific needs? Let’s dive deeper into the nuances of these systems.
Pit Type Coil Car vs. Loading/Unloading Car: Choosing the Right V-Shape Cradle
V-shape cradle coil cars are not one-size-fits-all. Two prominent types cater to distinct operational requirements: Pit Type and Loading/Unloading Cars. Understanding their differences is crucial for making an informed decision.
Pit Type Coil Car: The Efficiency Enhancer
Pit Type Coil Cars excel in automated systems where floor space optimization is paramount. These cars operate within a pit, allowing the V-shaped platform to descend to floor level for easy coil loading and unloading.
Feature | Description | Advantages | Disadvantages | Best Suited For |
---|---|---|---|---|
Structure | Cylinder beneath V-table, self-contained power unit, 4-wheel drive | Space-saving, efficient vertical lifting, high maneuverability | Requires floor pit installation, potentially higher initial installation cost | Automated lines, space-constrained facilities, systems requiring floor-level access |
Operation | Vertical lifting via cylinder, single-point lubrication, heavy-duty bearings | Minimized downtime, reduced maintenance, enhanced durability | Limited flexibility for non-pit areas | High-throughput environments, integration with automated machinery |
Key Application | Integrating coil rewinder with packing line where pit installation is feasible | Seamless integration, ergonomic loading/unloading, optimized workflow | Installation limitations, pit maintenance | New facility designs, major line upgrades |
Loading/Unloading Car: The Versatile Workhorse
Loading/Unloading Cars offer greater flexibility and are designed for integration with uncoilers and recoilers. Their mast-type elevating assembly and mobility on flanged wheels make them adaptable to various layouts.
Feature | Description | Advantages | Disadvantages | Best Suited For |
---|---|---|---|---|
Structure | Welded steel plate mast, V-platform, anti-friction cam rollers, flanged wheels | Robust construction, secure coil holding, smooth vertical and horizontal movement | More complex structure, potentially higher maintenance than pit type | Versatile layouts, integration with existing lines, varied coil handling points |
Operation | Hydraulic cylinder lifting, hydraulic motor traversal, chain and sprocket drive | Precise coil positioning, controlled movement, reliable operation | May require more space for maneuvering compared to pit type | Flexible manufacturing cells, lines requiring loading/unloading at different points |
Key Application | Receiving, positioning, and loading/unloading coils from uncoilers/recoilers | Adaptable to different machinery, facilitates coil transfer, enhances workflow | Potentially less space-efficient than pit type for specific layouts | Retrofitting existing lines, diverse coil handling needs |
By carefully evaluating your facility layout, production volume, and integration requirements, you can determine whether a Pit Type Coil Car or a Loading/Unloading Car best fits your operational needs, maximizing efficiency and safety in your steel coil handling processes.
AGV Car for Steel Coil
Are you envisioning a factory where coil movement is autonomous and error-free? Step into the future with AGV Coil Cars. Imagine robotic vehicles navigating your facility with precision, transporting heavy steel coils without manual intervention. This is the reality AGV technology brings to steel coil handling.
AGV (Automated Guided Vehicle) coil cars are robotic transport systems designed for autonomous movement of heavy steel coils within industrial environments, utilizing advanced navigation technologies like lasers or sensors to follow predetermined paths, enhancing safety, efficiency, and reducing labor costs. These vehicles optimize material flow, minimize damage risk, and offer scalability for growing operations in service centers and manufacturing plants.
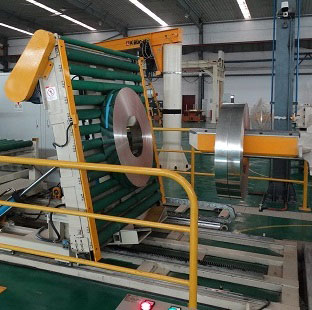
Let’s delve into the specific advantages that make AGV coil cars a game-changer for steel coil handling.
Unveiling the Advantages of AGV Coil Cars: Efficiency, Safety, and Beyond
AGV coil cars offer a transformative approach to steel coil handling, bringing a suite of advantages that significantly enhance operational performance and safety.
- Increased Efficiency: Automation is the cornerstone of efficiency. AGVs operate continuously without breaks, tirelessly transporting coils, significantly speeding up production cycles and minimizing downtime. This 24/7 operation capability ensures a consistent material flow, eliminating bottlenecks and boosting throughput.
- Enhanced Safety: Safety is paramount in heavy industries. By automating coil transport, AGVs drastically reduce the need for manual handling of heavy steel coils. This minimizes the risk of workplace injuries associated with manual lifting and movement, creating a safer working environment for personnel.
- Versatility: AGV coil cars are designed to handle a wide range of coil sizes and weights. Equipped with adjustable supports and robust frames, they can accommodate diverse coil dimensions, offering flexibility for handling various product lines and adapting to changing production needs.
- Damage Reduction: Secure coil cradles and smooth, controlled movement are key to preventing material damage. AGVs ensure coils are held firmly and transported steadily, minimizing the chances of shifting, falling, or collisions. This careful handling reduces material waste and maintains high-quality standards.
- Cost-Effectiveness: While the initial investment in AGV systems may seem significant, the long-term cost benefits are substantial. AGVs reduce labor costs by automating transport tasks, decrease operational expenses by optimizing material flow, and minimize damage-related losses. This combination leads to a significant return on investment and improved profitability.
In essence, AGV coil cars represent a leap towards smart, efficient, and safe steel coil handling. They not only streamline operations but also create a more sustainable and profitable manufacturing environment.
Technical Characteristics of Coil Cars
Are you curious about what makes a coil car tick? Beyond their structure and operation, the technical characteristics of coil cars define their capabilities and adaptability. Understanding these specifications is key to selecting a coil car that perfectly aligns with your operational demands.
Coil car technical characteristics encompass a range of specifications including capacity, dimensions, power supply, speed, drive motors, command systems, wheel types, lifting deck options, operating environment suitability, and safety devices, all customizable to meet specific steel coil handling needs. These features dictate the performance, safety, and integration capabilities of coil cars within diverse industrial settings.
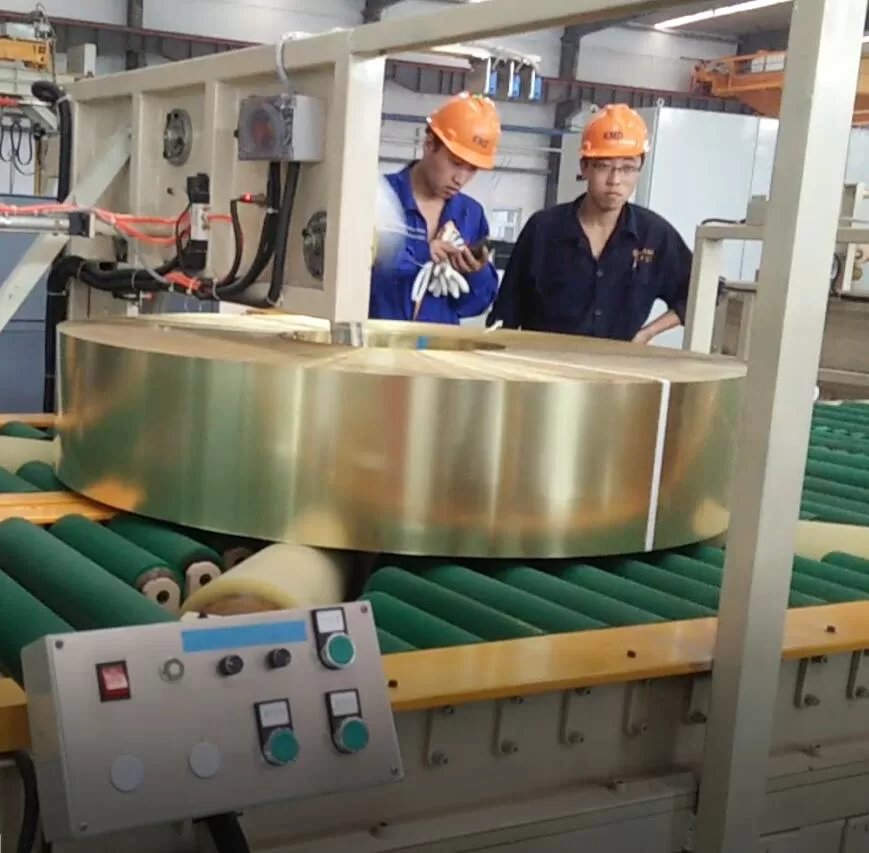
Let’s break down the critical technical characteristics of coil cars, providing a clearer picture of what to consider when choosing the right system.
Decoding Coil Car Specifications: A Technical Deep Dive
Choosing the right coil car involves understanding a range of technical specifications that dictate performance, flexibility, and safety. Here’s a detailed look at these characteristics:
Specification | Range/Options | Key Considerations | Impact on Operation |
---|---|---|---|
Capacity | 1 ton to 50 tons (or more, on request) | Coil weight, material density, safety factor | Determines maximum coil size and weight the car can handle safely and efficiently |
Dimensions | Customizable (on request) | Facility layout, coil size, integration points | Ensures car fits within workspace and can maneuver effectively |
Power Supply | Battery, Electric Grid, Diesel Engine, Hydraulic | Operating environment (indoor/outdoor), duty cycle, power availability, emissions | Influences operational cost, environmental impact, and continuous operation |
Travel Speed | 1 km/h to over 12 km/h (on request) | Production line speed, travel distance, safety regulations | Affects throughput, cycle time, and integration with production flow |
Drive Motors | AC Motors, Hydraulic Motors, Pneumatic Motors | Load weight, speed requirements, environmental conditions, maintenance preferences | Determines power, control precision, and suitability for specific applications |
Command System | Touch Panel, Notebooks, Remote Panel, WMS/ERP | Level of automation, operator interface preferences, integration with existing systems | Influences ease of use, control precision, and integration with factory management |
Kind of Wheels | Steel wheels for rails (customizable) | Floor type, rail system, load distribution, wear resistance | Determines mobility, load capacity, and suitability for different terrains |
Lifting Deck | Optional (lifting stroke from 50 mm, on request) | Integration with machinery height, transfer requirements, coil positioning | Facilitates seamless coil transfer to processing equipment at varying heights |
Operating Environment | Indoor, Outdoor, Offshore | Weather conditions, temperature range, corrosive environments, hazardous areas | Ensures car is suitable for intended operating conditions and environmental factors |
Safety Devices | Laser Scanners, Bumpers, Ultrasonic Sensors | Safety regulations, workplace hazards, obstacle detection needs | Enhances workplace safety, prevents collisions, and protects personnel and equipment |
Industry 4.0 Ready | Depends on specific features | Data integration needs, remote monitoring, predictive maintenance | Enables smart manufacturing, data-driven optimization, and remote management |
Hazardous Area Conformity (EX) | On request | Explosion risk assessment, regulatory compliance, safety requirements | Ensures safe operation in potentially explosive atmospheres |
By meticulously considering these technical characteristics and aligning them with your specific operational needs, you can select a coil car system that delivers optimal performance, reliability, and safety for your steel coil handling processes.
Integrating Coil Cars with Coil Packing Lines
How do you transform a series of machines into a cohesive production powerhouse? The answer lies in seamless integration. Imagine coil cars acting as the vital link, smoothly connecting your coil rewinder and coil packing line into a unified, efficient system. This integration is the key to unlocking optimal productivity.
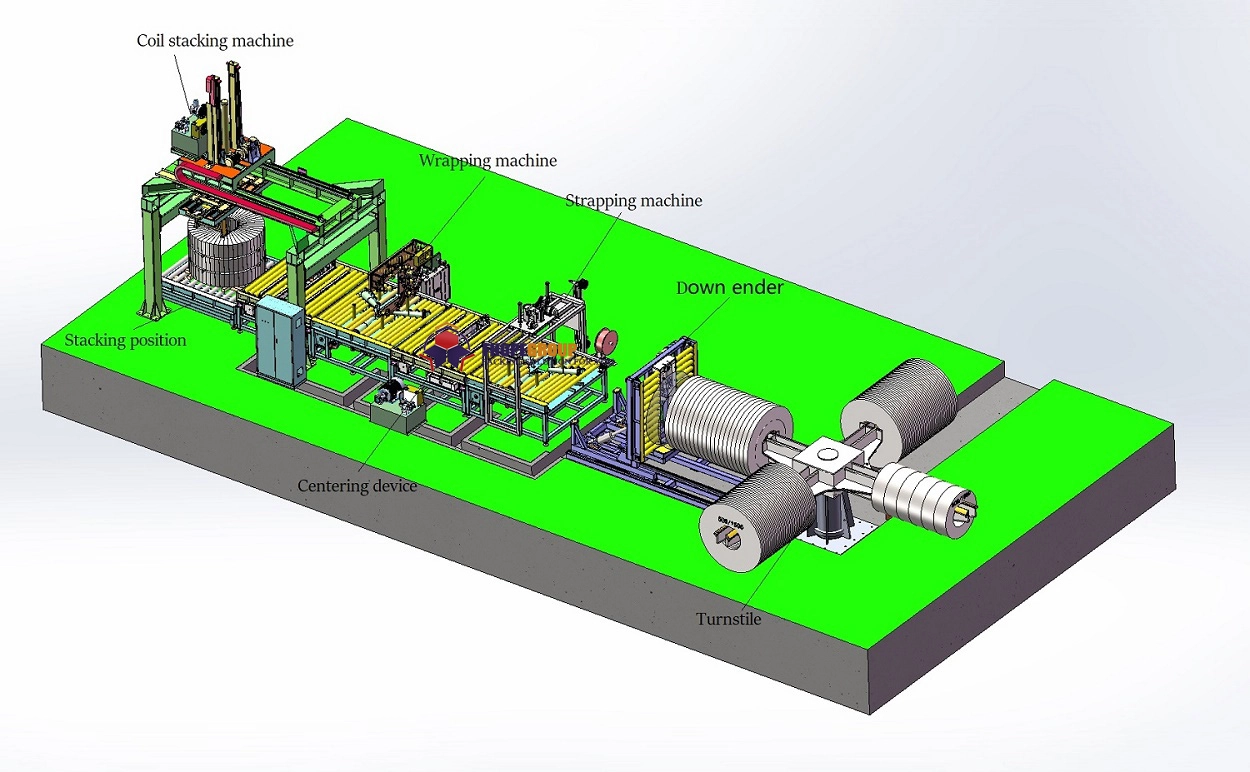
Integrating coil cars into coil packing lines involves strategically implementing these vehicles to automate the transfer of steel coils from the rewinder to the packing station, creating a continuous and streamlined workflow that minimizes manual handling, reduces bottlenecks, and enhances overall production efficiency. This integration optimizes space utilization, reduces material damage, and ensures a safer and faster coil processing operation within steel service centers.
Seamlessly integrating coil cars with coil packing lines offers a multitude of benefits:
- Automated Material Flow: Coil cars automate the transfer of coils, eliminating manual handling and creating a continuous flow from rewinding to packing.
- Enhanced Efficiency: By streamlining the movement of coils, integration reduces cycle times and increases the throughput of the entire packing line.
- Reduced Labor Costs: Automation reduces the need for manual labor in coil transport, leading to significant cost savings and optimized resource allocation.
- Improved Safety: Automated transfer minimizes the risk of accidents and injuries associated with manual handling of heavy coils.
- Optimized Space Utilization: Efficient integration can optimize the layout of the coil packing line, making better use of available space.
- Minimized Damage: Controlled and smooth transport by coil cars reduces the risk of coil damage during transfer.
To achieve successful integration, consider these key factors:
- System Compatibility: Ensure coil cars are compatible with both the coil rewinder and the coil packing line in terms of interface, control systems, and operational parameters.
- Layout Planning: Design the facility layout to accommodate the movement of coil cars efficiently, ensuring clear pathways and smooth transitions between stations.
- Control Integration: Integrate the control systems of the coil cars with the overall line control system for synchronized and automated operation.
- Safety Systems: Implement comprehensive safety systems, including sensors and interlocks, to ensure safe interaction between coil cars, machinery, and personnel.
- Customization: Tailor the coil car specifications and integration plan to the specific needs of your coil packing line, considering coil sizes, throughput requirements, and space constraints.
By thoughtfully planning and executing the integration of coil cars, you can transform your coil packing line into a highly efficient, automated, and safe operation, maximizing productivity and minimizing operational costs.
Conclusion
In conclusion, the guide line of coil car implementation is not merely about adopting a piece of machinery; it’s about embracing a holistic approach to steel coil handling. By strategically selecting and integrating coil cars, particularly within the coil packing line, industries can unlock unprecedented levels of efficiency, safety, and operational excellence. From V-shape cradle designs to automated guided vehicles, the technology is available to revolutionize your material flow and redefine industry standards for steel coil processing.