90 Degree Mold Upender Vs. 180 Degree Mold Upender
Handling massive molds is inherently risky and inefficient. Struggling with manual methods or inadequate equipment leads to potential damage, costly downtime, and worker injuries. Choosing the right mold handling solution is critical, but distinguishing between a 90-degree and a 180-degree upender can be confusing. Which one truly meets your specific needs?

The core difference lies in the rotation angle and purpose. A 90-degree mold upender tilts the mold halfway, primarily changing its orientation from horizontal to vertical (or vice versa) for tasks like crane access or specific maintenance. In contrast, a 180-degree mold flipper performs a complete inversion, flipping the mold fully for accessing the opposite side, splitting mold halves, or comprehensive maintenance procedures requiring full rotation.
Understanding this fundamental distinction is the first step towards selecting the equipment that will optimize your workflow, enhance safety, and boost productivity. Let’s delve deeper into the specifics of each type to help you make an informed decision for your mold handling challenges.
Understanding the 90 Degree Mold Upender: Functionality and Benefits
The need to safely and efficiently rotate heavy molds by 90 degrees is a common challenge across manufacturing, automotive, and die-casting industries. These substantial tools often require reorientation for maintenance, transport, or integration with other processes. A 90-degree mold upender, also known as a mold tilter or tipper, is specifically designed to address this precise requirement, offering a controlled and secure method for this crucial task.
A 90-degree mold upender is a piece of material handling equipment designed to rotate heavy objects, particularly molds and dies, exactly 90 degrees. Its primary function is to change the orientation of the load between horizontal and vertical positions. This is essential for tasks like preparing a mold laid horizontally for lifting vertically by an overhead crane, accessing specific parts for maintenance, or positioning dies correctly for die spotting presses. Key benefits include significantly enhanced operator safety by eliminating manual turning, increased operational efficiency compared to using cranes alone, and preventing damage to expensive molds during handling. They are indispensable auxiliary equipment, especially for medium to large-sized molds.
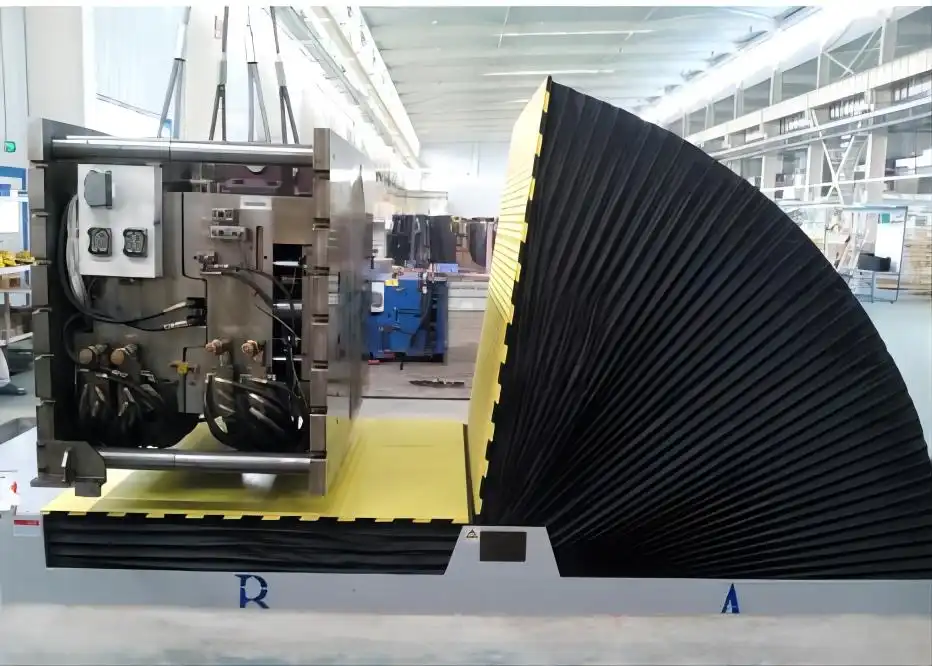
Deep Dive: How 90 Degree Mold Upenders Work and Key Specifications
The operation of a 90-degree mold upender, while conceptually simple, relies on robust engineering to handle significant loads safely and precisely. Typically, the mold is loaded onto a stable platform or table integrated into the upender structure. This platform, often driven by powerful electric motors or hydraulic systems, then rotates the load smoothly through a 90-degree arc.
Mechanism and Drive Systems:
The core mechanism usually involves one or two platforms. In some designs, a single L-shaped platform cradles the load and rotates. In others, two platforms move in concert. The driving force is crucial:
- Electric Motor Driven: Often utilizes gear reducers and heavy-duty chains or direct gear drives. Known for precise control and consistent speed. Requires electrical power supply.
- Hydraulic System Driven: Uses hydraulic cylinders and pumps. Offers immense power for extremely heavy loads and can provide smooth, cushioned stops. Requires a hydraulic power unit.
Control and Safety:
Operator safety and load protection are paramount. Controls are typically managed via a pendant or fixed control panel, often positioned away from the machine’s moving parts. Key safety features include:
- Limit Switches: Automatically stop rotation precisely at the 0 and 90-degree positions.
- Heavy-Duty Brakes: Engage automatically on motors or hydraulic systems to hold the load securely at any point, especially during power loss.
- Robust Structure: Engineered with high safety factors to handle rated capacities without structural fatigue.
- Optional Safety Guards: Physical barriers or light curtains can be added to restrict access during operation.
Table Configurations and Customization:
The platform interfacing with the mold can be adapted:
- Flat Table: Standard for most block-shaped molds or dies.
- V-Shaped Table: Ideal for cylindrical objects or coils (though the focus here is molds).
- Custom Fixtures: Designed for uniquely shaped molds or specific handling requirements.
Some models feature a base that can rotate 360 degrees, allowing the loading/unloading orientation to be changed independently of the 90-degree tilt.
Key Specifications Table:
Feature | Typical Specification Range | Considerations |
---|---|---|
Load Capacity | 1 Ton – 100+ Tons | Must match or exceed the heaviest mold handled. |
Platform Size | Custom based on mold dimensions | Ensure sufficient support for the mold footprint. |
Rotation Angle | Fixed at 90 degrees | Core function definition. |
Rotation Speed | Variable (e.g., 30-90 seconds/cycle) | Balance between speed and smooth, safe handling. |
Drive System | Electric or Hydraulic | Choice depends on load, environment, preference. |
Control Interface | Pendant Control / Fixed Panel | Ease of use and operator safety distance. |
Safety Features | Limit Switches, Brakes, E-Stops | Non-negotiable for safe operation. |
Optional Features | 360° Base Rotation, Conveyors | Enhance integration and workflow flexibility. |
Integrating a 90-degree mold upender streamlines workflows significantly. It drastically reduces the time and risk associated with turning large molds using overhead cranes and manual leverage, transforming a potentially hazardous and lengthy process into a quick, automated, and safe operation. It acts as a vital link, preparing molds efficiently for subsequent maintenance, transport, or production steps.
Exploring the 180 Degree Mold Flipper: Capabilities and Applications
While 90-degree rotation solves many mold handling orientation issues, some maintenance and operational tasks require complete inversion. When access to the bottom or opposite side of a mold is necessary, or when mold halves need to be separated or mated precisely, a 180-degree mold flipper becomes the essential tool, offering capabilities beyond the scope of a 90-degree unit.
A 180-degree mold flipper, sometimes called a mold inverter or flipper lift table, is specifically designed to rotate heavy molds, dies, or other large objects through a full 180 degrees. This complete inversion allows for comprehensive maintenance, inspection, or cleaning on all sides of the mold without needing multiple repositioning steps. It’s particularly crucial in mold production for mating cope and drag sections or during die splitting operations.

Unpacking the 180 Degree Flipper: Mechanism and Use Cases
The mechanism of a 180-degree flipper often differs significantly from a 90-degree upender due to the requirement for secure clamping and full rotation. Common designs involve:
- Dual Platform Clamping: Two opposing platforms securely clamp the mold. The entire assembly then rotates 180 degrees. This is common for dedicated mold flippers. This ensures the mold is held safely throughout the inversion.
- Scissor Lift Inverters: Some designs, often called Load Inverters (like those mentioned by FHOPE), use hydraulic scissor mechanisms with clamping capabilities. These can clamp loads of varying heights and rotate them 180 degrees, often used for inverting stacked goods or loads on pallets, but adaptable for certain mold types.
- Center-Axis Rotation: Simpler designs might rotate the load around a central axis, requiring careful balancing and securement.
Key Use Cases:
The ability to perform a full 180-degree flip opens up specific applications:
- Mold Maintenance: Provides complete access to both halves (cavity and core) of an injection mold or die-casting die for cleaning, repairs, polishing, or component replacement. This is often impossible with only a 90-degree turn.
- Mold Assembly/Disassembly (Die Splitting): Essential for safely and precisely opening (splitting) and closing large molds. The controlled rotation allows for vertical separation and joining after the 180-degree flip.
- Foundry Operations: Used for flipping molding boxes (cope and drag) for mating or sand shake-off processes.
- Load Inversion: While not solely for molds, 180-degree flippers (inverters) are used to invert entire loads, sometimes necessary for specific manufacturing processes or to switch pallets.
Safety and Operational Considerations:
Given the full inversion, ensuring the load is securely clamped is even more critical than with 90-degree rotation. Safety systems often include pressure sensors in clamping systems, robust locking mechanisms, and interlocks preventing rotation unless the load is properly secured. The operational footprint might also be larger to accommodate the full rotation. Machines like the SANTSAI 5 Ton Mold Flipper or FHOPE’s Inject Mold Flipper Table are examples specifically engineered for this secure 180-degree mold handling, emphasizing safe and efficient operation for loads ranging from relatively small to over 100 tons. The complexity and enhanced safety features generally make 180-degree flippers a more significant investment than standard 90-degree upenders.
Key Differences: Choosing Between a 90° Upender and a 180° Flipper
Selecting the wrong mold handling equipment can lead to operational bottlenecks, safety hazards, and wasted investment. While both 90° upenders and 180° flippers rotate heavy molds, their fundamental differences dictate their suitability. Making the right choice requires understanding precisely what your process demands.
The primary distinction is the degree of rotation and the resulting accessibility. A 90° upender provides orientation change, ideal for preparing molds for vertical lifting or accessing one side/top. A 180° flipper offers complete inversion, essential for tasks requiring access to the opposite side, mold splitting, or full inspection/maintenance on both halves. Your specific application is the deciding factor.

Feature-by-Feature Comparison: 90° vs. 180° Mold Handling
To clarify the choice, let’s break down the key differences in a structured way:
Feature | 90° Mold Upender / Tilter | 180° Mold Flipper / Inverter | Key Takeaway |
---|---|---|---|
Rotation Angle | Exactly 90 degrees | Exactly 180 degrees | Defines the fundamental capability. |
Primary Function | Change orientation (Vertical/Horizontal) | Complete inversion / Flipping | Dictates the type of access provided. |
Core Application | Prep for crane lift, side access maint. | Full maint., mold splitting, inversion | Match the machine’s function to your process need. |
Mechanism | Rotating platform(s) (L-shape/dual) | Clamping platforms, Scissor-clamp | 180° often requires secure clamping. |
Complexity | Generally simpler design & operation | More complex due to clamping & rotation | Impacts cost, maintenance, and operation. |
Load Securement | Relies on gravity & platform stability | Requires active clamping mechanism | Critical safety difference for 180° rotation. |
Typical Use Cases | Injection mold service prep, Coil handling | Die splitting, Full mold access, Foundry | Highlights industry-specific applications. |
Cost Indication | Generally lower initial cost | Generally higher initial cost | Reflects complexity and capabilities. |
Footprint | Can vary, some relatively compact | Often requires larger operational space | Consider floor space availability. |
Elaboration on Differences:
- Accessibility: This is the crux of the decision. If your maintenance only requires accessing the sides or top/bottom when oriented vertically or horizontally, a 90° upender is sufficient. If you must work on the side that becomes the bottom after a 90° turn, or if you need to separate mold halves vertically, the 180° flipper is necessary.
- Workflow Integration: A 90° unit is often a preparatory step – turning the mold so a crane can lift it or so technicians can work on the now-accessible side. A 180° flipper might be a more central part of a maintenance process, performing the complete manipulation needed for disassembly or comprehensive servicing.
- Safety Focus: While both prioritize safety, the 180° flipper demands more intricate safety systems due to the load being fully inverted against gravity. Secure clamping and rotation locks are absolutely critical.
- Versatility: Some 90° upenders with rotating bases offer flexibility in loading direction. Some 180° inverters (especially scissor types) can handle a wider range of load heights and types beyond just molds. However, dedicated mold flippers are optimized specifically for that task.
Ultimately, the choice isn’t about which is "better," but which is "right" for the specific job. Over-specifying with a 180° flipper when only 90° rotation is needed incurs unnecessary cost and complexity. Conversely, trying to make do with a 90° unit for tasks requiring full inversion leads to inefficiency and potentially unsafe workarounds.
Factors to Consider When Selecting Your Mold Handling Solution
Choosing between a 90-degree upender and a 180-degree flipper goes beyond just the angle of rotation. A thorough evaluation of several key factors is essential to ensure you invest in equipment that maximizes safety, efficiency, and return on investment for your specific mold handling needs. Misjudging these factors can lead to purchasing equipment that is underpowered, oversized, incompatible with your workflow, or simply unsuitable for the task.
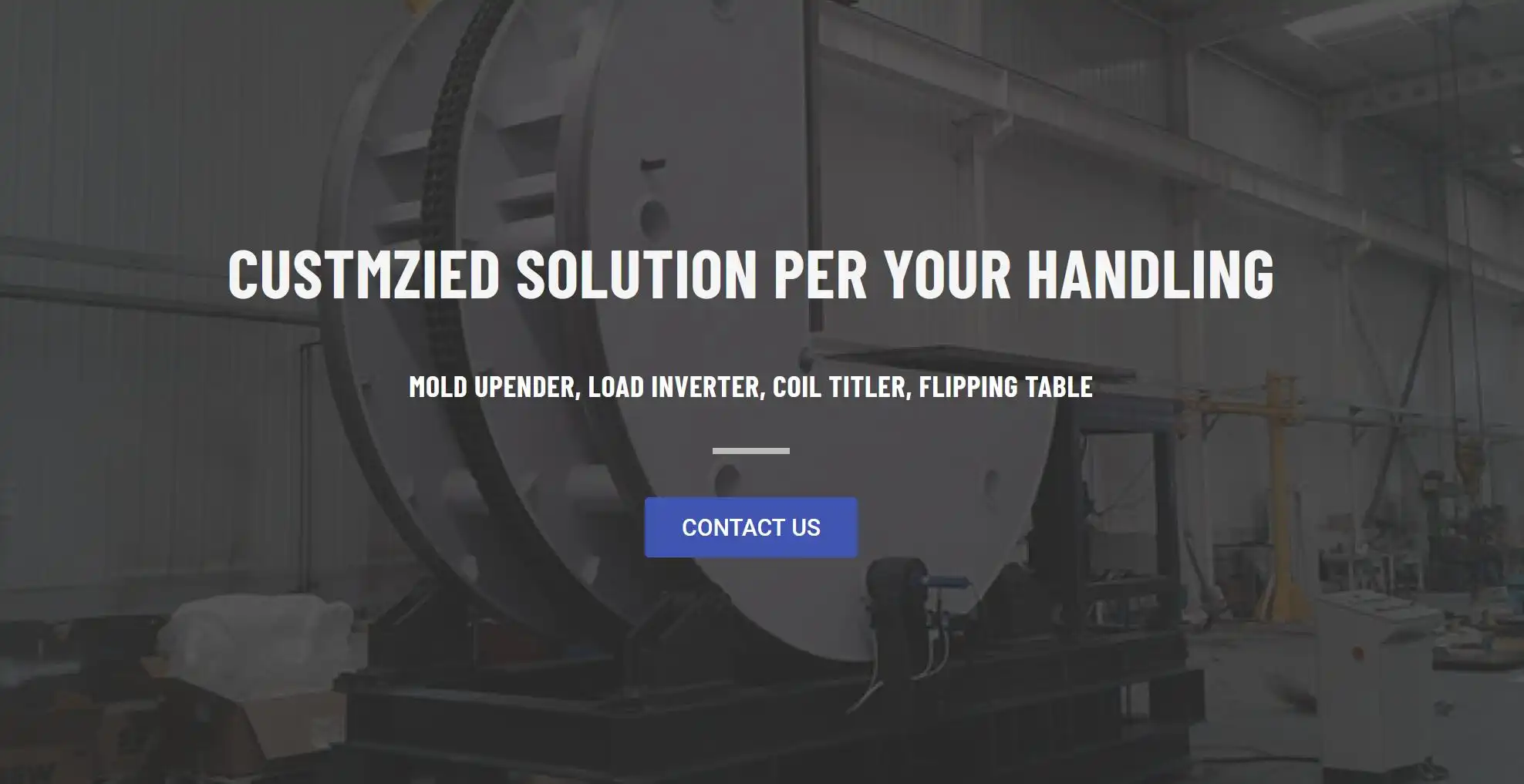
Consider these critical elements:
-
Load Characteristics:
- Weight: What is the maximum weight of the molds or dies you need to handle? The upender/flipper must have a rated capacity significantly exceeding your heaviest load for a safety margin.
- Dimensions: What are the length, width, and height of your largest molds? The machine’s platform(s) must be adequately sized to support the load stably throughout the rotation. Center of gravity also plays a role, especially with tall or irregularly shaped molds.
- Shape: Are your molds standard blocks, or do they have complex geometries, protrusions, or require specific support points? This might necessitate custom table designs or fixtures.
-
Specific Application & Workflow:
- Task Requirement: What is the exact reason for rotating the mold? Is it solely to change orientation for crane access (favors 90°)? Or do you need to open the mold, access the bottom surface, perform maintenance on both halves (favors 180°)? Be precise about the operational goal.
- Frequency of Use: How often will the machine be used? High-frequency operations might justify more robust, faster, or automated solutions.
- Integration: How will the upender fit into your existing workflow? Consider loading/unloading methods (forklift, crane, AGV, conveyor), required positioning accuracy, and cycle time impact. Will it need to interface with other machines like die spotting presses?
-
Operational Environment:
- Space Availability: Measure the available floor space, including height clearance, ensuring enough room for the machine’s footprint and safe operation, including loading/unloading zones. 180° flippers often require more space.
- Utilities: What power sources are available (electrical voltage/phase, hydraulic)? Ensure compatibility.
-
Safety and Ergonomics:
- Operator Safety: What safety features are non-negotiable (e.g., E-stops, interlocks, guarding)? How will operators interact with the machine? Ensure controls are intuitive and safely located.
- Load Security: Re-evaluate the clamping needs, especially for 180° rotation.
-
Budget and Maintenance:
- Initial Cost: 180° flippers are generally more expensive than 90° upenders due to complexity. Factor this into your budget.
- Operating Costs: Consider energy consumption (electric vs. hydraulic).
- Maintenance: Evaluate the ease of maintenance, availability of spare parts, and manufacturer support. Simpler machines often have simpler maintenance needs.
Selecting the right mold upender involves assessing load characteristics (weight, size), the specific task (orienting vs. flipping), available space, safety needs, and budget. Carefully analyze your workflow – do you need 90° reorientation for crane access or 180° inversion for full maintenance? This analysis ensures optimal efficiency and safety, preventing costly errors in equipment choice. Consulting with experienced manufacturers like FHOPE, who offer a wide range of both 90° and 180° solutions and can provide custom designs, is highly recommended to tailor the equipment precisely to your requirements.
Conclusion
Choosing between a 90-degree mold upender and a 180-degree mold flipper boils down to understanding your specific operational requirements. The 90-degree unit excels at changing orientation for accessibility or integration with other handling equipment like cranes. The 180-degree flipper provides complete inversion, essential for comprehensive maintenance, mold splitting, and accessing all surfaces. Both significantly enhance safety and efficiency compared to manual methods. Carefully evaluating load characteristics, the intended task, workflow integration, and safety needs will guide you to the correct solution. Investing in the appropriate [mold upender]() streamlines processes, protects valuable assets, and ensures a safer working environment.