Automatic Air Tube and Nylon Tube Coiling & Tying Machine: Enhancing Efficiency in Industrial Operations
In modern manufacturing and distribution environments, efficiency, consistency, and cost reduction are paramount. Handling materials like air tubes, nylon tubes, PU tubes, and other flexible conduits often involves coiling and securing them for packaging, storage, or further processing. Manual methods for these tasks can be time-consuming, inconsistent, and physically demanding. The Automatic Air Tube and Nylon Tube Coiling and Tying Machine addresses these challenges directly, offering a streamlined, automated solution for industrial applications. This article delves into the technical aspects, operational benefits, and practical considerations of deploying such equipment.
1. Core Functionality: From Extrusion to Bundled Coil
At its heart, this automated system is designed to take continuous lengths of tubing—typically fed directly from an extruder line or an unwinding spool—and precisely coil it to predefined lengths and diameters. Once the desired length is reached, the machine automatically cuts the tube (if required) and securely ties or bundles the coil using materials like plastic ties or adhesive tape. The entire process is orchestrated by a central control system, minimizing manual intervention.
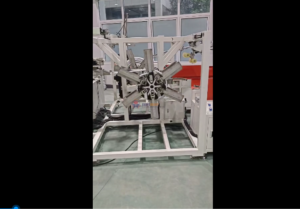
2. Key Components and Structural Design
Understanding the machine's structure provides insight into its capabilities and reliability. Key components typically include:
- Infeed and Guiding System: Ensures the tube enters the coiling mechanism smoothly and without twisting or kinking. Often includes sensors to detect material presence and regulate tension.
- Coiling Mechanism: Usually consists of a rotating drum or formers. The diameter and width are often adjustable to accommodate different coil sizes. Servo motors typically drive the rotation for precise speed and length control.
- Length Measurement System: Employs encoders or sensor wheels to accurately measure the length of the tube being coiled. This data is fed back to the control system to trigger cutting and tying.
- Cutting Unit (Optional): For applications requiring specific lengths, an integrated cutting unit (e.g., pneumatic shear, rotary blade) provides a clean, automated cut.
- Tying/Bundling Unit: This is a critical component for securing the coil. Common mechanisms include:
- Twist Tying: Uses wire-reinforced plastic ties.
- Strapping: Applies plastic straps (PP or PET).
- Taping: Wraps adhesive tape around the coil.
The choice depends on the required holding strength, cost, and downstream handling processes.
- Control System (PLC): The brain of the operation. A Programmable Logic Controller (PLC) manages all sequences, motor speeds, sensor inputs, and timing. It often features a Human-Machine Interface (HMI) touchscreen for parameter input, diagnostics, and operational monitoring.
- Ejection System: Automatically discharges the finished, tied coil onto a conveyor, collection bin, or packaging station.
- Frame and Safety Guarding: A robust frame provides stability, while interlocked safety guards protect operators during operation, adhering to industrial safety standards.
3. Technical Specifications: A Comparative Overview
While specifications vary significantly between models and manufacturers, typical parameters for an automatic tube coiling and tying machine might include:
Parameter | Typical Range / Type | Importance |
---|---|---|
Applicable Tube OD | 4mm - 30mm (Model Dependent) | Defines the range of tube sizes the machine can handle. |
Coil Inner Diameter (ID) | 100mm - 500mm (Adjustable) | Determines the core size of the finished coil. |
Coil Outer Diameter (OD) | 200mm - 800mm (Adjustable) | Impacts the overall size and stability of the coil. |
Maximum Coil Width | 50mm - 200mm (Adjustable) | Affects coil density and handling ease. |
Coiling Speed | 30 - 150 meters/minute (Variable) | Directly impacts production throughput. |
Length Accuracy | ± 0.1% - 0.5% | Critical for consistent product delivery. |
Tying Cycle Time | 2 - 5 seconds per tie | Influences overall machine cycle time. |
Tying Material | PE Twist Tie, PP/PET Strap, Tape | Depends on application needs and machine config. |
Control System | PLC with HMI Touchscreen | Ease of operation, setup, and diagnostics. |
Power Supply | 220V/380V, 50/60Hz, 3-Phase | Standard industrial power requirements. |
Compressed Air | 0.5 - 0.7 MPa (If pneumatic used) | Required for cutting, tying, or ejection units. |
Machine Dimensions (LxWxH) | Varies (e.g., 2.5m x 1.5m x 1.8m) | Important for floor space planning. |
Note: Always consult specific manufacturer datasheets for precise specifications.
4. Operational Advantages and ROI
Investing in automated coiling and tying offers tangible benefits:
- Increased Throughput: Machines operate significantly faster and more consistently than manual methods, drastically boosting production output.
- Consistent Coil Quality: Automation ensures every coil meets predefined length, diameter, and tightness specifications, improving product quality and customer satisfaction.
- Reduced Labor Costs: Frees up personnel previously engaged in manual coiling/tying for more value-added tasks. Reduces reliance on manual dexterity and minimizes repetitive strain injuries.
- Improved Safety: Enclosed mechanisms and safety interlocks reduce operator exposure to moving parts compared to manual coiling.
- Material Savings: Precise length control minimizes waste associated with manual cutting inaccuracies. Optimized tying reduces consumption of bundling materials.
- Enhanced Packaging Readiness: Uniform coils are easier to handle, stack, and package, streamlining downstream logistics.
5. Industry Applications
These machines find application across various sectors involved in manufacturing or distributing flexible tubing:
- Pneumatics Industry: Coiling air hoses and pneumatic tubing (PU, PA/Nylon).
- Automotive: Handling fuel lines, brake lines (non-metallic), and air conditioning tubes.
- Appliance Manufacturing: Coiling water lines, drainage tubes for washing machines, dishwashers.
- Medical Device Manufacturing: Coiling medical-grade tubing (requires specific material handling considerations).
- Telecommunications: Bundling smaller conduits or fiber optic inner ducts.
- General Manufacturing: Handling coolant lines, low-pressure hydraulic hoses, and various industrial tubes.
6. User Experience and Integration Considerations
From a practical standpoint, operating these machines involves:
- Setup and Changeover: Modern machines often feature user-friendly HMIs allowing operators to quickly input parameters (length, diameters, tie points). Changeover time between different tube sizes or coil specifications is a key performance indicator. Quick-change tooling can significantly reduce downtime.
- Material Loading: Ensuring a smooth, continuous feed of tubing is crucial. Integration with upstream processes like extrusion lines requires careful synchronization.
- Maintenance: Routine maintenance involves checking belts, blades (if applicable), tying mechanisms, sensors, and lubrication points. Easy access to components simplifies upkeep.
- Troubleshooting: HMIs usually provide diagnostic information to help identify and resolve issues like material jams, sensor faults, or tying errors.
- Integration: Consider how the machine fits into the overall production flow. Does it need to communicate with upstream extruders or downstream packaging equipment? Compatibility with factory network protocols (e.g., Ethernet/IP, Profinet) might be necessary for Industry 4.0 initiatives.
7. Choosing the Right System
Selecting the appropriate automatic coiling and tying machine requires evaluating:
- Production Volume: Match machine speed and capacity to your output needs.
- Tube Characteristics: Consider the range of materials, diameters, and flexibility you need to handle.
- Coil Specifications: Define the required ID, OD, width, and length accuracy.
- Tying Requirements: Determine the necessary strength and type of bundling (tie, strap, tape).
- Level of Automation: Assess needs for features like automatic ejection, integration capabilities, and advanced diagnostics.
- Budget and ROI: Balance initial investment against projected savings in labor, material, and improved quality.
- Vendor Support: Consider manufacturer reputation, service availability, spare parts, and training.
Conclusion: A Strategic Investment in Efficiency
The Automatic Air Tube and Nylon Tube Coiling and Tying Machine represents a significant upgrade from manual processes. By automating the coiling, cutting, and bundling operations, businesses can achieve substantial improvements in productivity, product consistency, operational safety, and cost-effectiveness. Careful consideration of technical specifications, application requirements, and integration needs will ensure the chosen system delivers maximum value and contributes to a more streamlined and efficient manufacturing or distribution operation. Evaluating your current tube handling processes against the capabilities of these automated systems is a worthwhile step for any operation looking to enhance competitiveness.