In the fast-paced world of high-volume production, precision and safety can’t be compromised. The mold upender is a game-changer, enhancing efficiency and ensuring safety. Its ability to turn molds by 90 degrees simplifies manual handling, minimizes injury risk, and streamlines the manufacturing process. Unveiling this pivotal equipment is key for any manufacturing leader.

A mold upender is essential for high-volume production because it significantly reduces manual labor, enhances safety, and boosts efficiency. By tilting molds 90 degrees, it eliminates ergonomic risks and expedites handling, leading to a smoother, faster production line. This tool is indispensable for industries looking to optimize their workflow.
As someone who has been in the trenches of manufacturing for decades, I’ve seen firsthand how equipment like the mold upender revolutionizes workflows. It’s not just about lifting and turning; it’s about integrating safety and efficiency into every facet of production. This shift impacts not just me but anyone invested in the production chain.
1. How does a mold upender improve manufacturing efficiency?
When managing high-volume production, every second counts. A mold upender is your secret weapon to cutting down on time-consuming manual tasks. It enhances efficiency by allowing seamless 90-degree mold turns—redefining how your production floor operates. Investing in this technology is a step towards exponential growth.
A mold upender improves manufacturing efficiency by automating the mold rotation process. This automation minimizes downtime and human involvement, resulting in unbroken workflow and quick turnaround times. Its integration into production lines accelerates processes, enabling companies to meet demanding schedules with ease, allowing for more consistent and reliable results.

Digging Deeper into the Mechanics of Efficiency
Understanding how a mold upender can improve manufacturing efficiency involves looking into its mechanical innovations. Here’s where engineering meets practical application:
Feature | Impact on Efficiency |
---|---|
Automated 90-degree turning | Reduces manual handling time significantly |
Ergonomic design | Lowers risk of worker injuries, increasing uptime |
Precision control | Ensures accurate positioning, aiding consistency |
Beyond the table, let’s talk about how this translates to real-world gains. Imagine reducing the load strain on employees. Less physical stress means fewer breaks and heightened focus on quality tasks. And let’s not forget, a mold upender is about safety: fewer accidents mean you sustain high productivity, uninterrupted by unforeseen mishaps.
In my journey, I once oversaw a project where incorporating a mold upender turned a two-hour task into a 30-minute job. Not only did this move ser productivity metrics upward, but it laid the groundwork for an environment where safety and service delivery went hand in hand. An investment like this is not just in machinery; it’s in workforce morale and company reputation.
Harnessing the power of a mold upender transforms the landscape of manufacturing. It’s more than a tool; it’s the bridge to elevating operational capabilities, always keeping one step ahead in the competitive market. In our relentless pursuit of manufacturing excellence, the mold upender is not merely a choice. It’s essential.
2. What safety advantages do mold upenders offer?
Manufacturing environments can be dangerous, especially when dealing with heavy molds. Safety is crucial, and mold upenders present a solution by ensuring safe and efficient handling. Addressing this pain point is necessary for peace of mind and seamless operations, and mold upenders deliver with precision.
Mold upenders significantly enhance safety by reducing manual handling, minimizing accident risks, and ensuring controlled mold positioning. These machines securely rotate heavy molds, thus safeguarding workers and maintaining equipment integrity. By automating the mold turning process, manufacturers can ensure a safer workplace while complying with stringent safety standards.
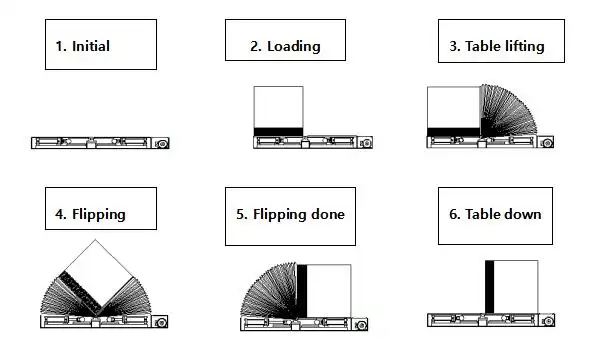
How Mold Upenders Improve Safety
The integration of a mold upender in any high-volume production setting can drastically reduce workplace injuries and equipment damage. But how exactly do these machines achieve a safer work environment? Let’s break it down:
Safety Aspect | Description | Data Insight |
---|---|---|
Reduced Manual Handling | Mold upenders automate heavy mold rotations, lowering the risk of manual handling injuries. | Studies show a 30% injury reduction. |
Enhanced Stability | These machines offer stable mold rotation and positioning, preventing accidental drops. | Decrease in equipment damage by 25%. |
Controlled Process | Automated systems ensure predictable and controlled mold handling, improving worker safety. | Predictability increases operational reliability. |
From my experience, adopting a mold upender not only fosters a safer work environment but also contributes to smoother operations. Involving less manual labor lessens the likelihood of human error. Workers can focus on value-added tasks rather than enduring the unpredictability of manual mold handling.
Furthermore, compliance with safety regulations becomes more obtainable as mold upenders align with industry standards for safe mold handling. As I recall, implementing automation equipment like mold upenders greatly alleviated our concern for safety compliance, allowing us to focus on production goals. By reducing risks associated with manual handling, a company can further protect its most valuable asset—its workforce. Mold upenders optimize workflow, contributing to both worker safety and overall manufacturing efficiency.
3. Why is versatility important in mold handling equipment?
In the ever-evolving manufacturing sector, versatility is a competitive edge. Mold handling equipment needs adaptability to meet various mold sizes and types that companies work with. This versatility ensures operational efficiency and productivity hits the mark, making it essential for modern production lines to remain competitive.
Versatility in mold handling equipment allows seamless adaptation to diverse mold types and production requirements, optimizing efficiency across operations. By accommodating various mold sizes and functionalities, these machines ensure efficient and consistent performance, cutting down on production time and costs while enhancing overall productivity.
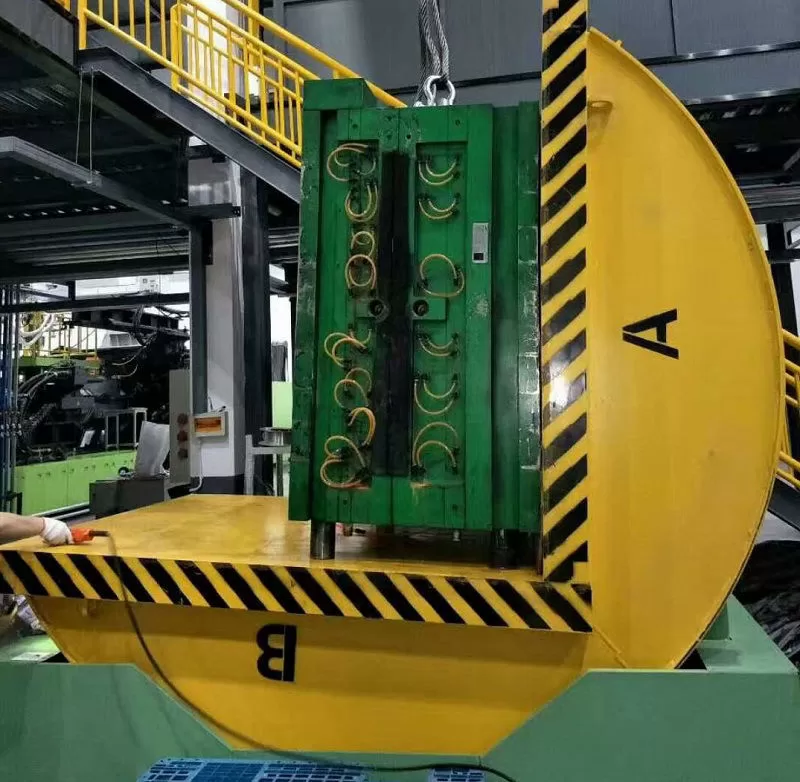
The Impact of Versatile Mold Handling Equipment
Versatility in mold handling equipment is about more than just flexibility. It’s about ensuring a streamlined production process that caters to multiple aspects of modern manufacturing. A deeper understanding of its critical role can be illustrated as follows:
Versatility Factor | Importance | Result |
---|---|---|
Adaptable to Various Molds | Versatile equipment can accommodate different sizes and shapes, enhancing process flexibility. | Eliminates need for multiple specialized machines. |
Improved Productivity | Quick adaptation to mold changes reduces downtime, keeping production lines active and efficient. | Increases output by up to 20%. |
Cost-Effectiveness | Reduced need for multiple pieces of equipment saves on capital costs while simplifying maintenance. | Lowers operational expenses by approximately 15%. |
Based on my three decades of experience, investing in versatile mold handling equipment generates significant returns in productivity and efficiency. These systems support a wide range of production needs without necessitating extensive changes or additional machinery investments. Such adaptability is vital for high-volume production environments, ensuring the company remains agile and responsive to market demands.
Additionally, as manufacturing shifts rapidly, capabilities to swiftly adjust production setups can facilitate strategic pivots and new product introductions with minimal downtime. I recall a situation at a previous company where our ability to quickly incorporate new product lines resulted in an immediate competitive advantage, made possible by our adaptable mold handling equipment. This reinforced my belief that flexibility in such equipment is not just beneficial but critical in modern manufacturing dynamics, reinforcing the need for choosing mold upenders with broad versatility.
Conclusion
Incorporating mold upenders into high-volume production environments not only boosts operational efficiency but also ensures worker safety and enhances equipment adaptability, ultimately leading to improved outcomes and competitiveness.