What are the Pros and Cons of Using Lightweight Materials in Modern Upenders?
Struggling with heavy, energy-hungry industrial equipment? Modern upenders face increasing demands for efficiency and performance. Utilizing lightweight materials seems like a promising solution, offering potential benefits but also introducing new complexities. Understanding this trade-off is crucial before investing in or designing next-generation upending equipment for improved operations.
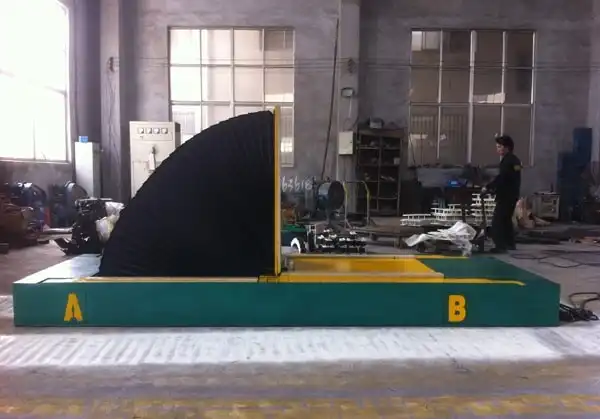
Using lightweight materials like advanced high-strength steel, aluminum alloys, or composites in modern upenders offers pros such as reduced energy consumption, faster cycle times due to lower inertia, and easier installation or relocation. However, the cons include significantly higher initial material and manufacturing costs, potential challenges in joining dissimilar materials, possible compromises in long-term durability or fatigue life if not properly engineered, and more complex repair procedures.
While the allure of enhanced performance and efficiency is strong, the practical implications of cost, manufacturing adjustments, and long-term reliability require careful consideration. This article delves into the specific advantages and disadvantages of integrating lightweight materials into the demanding world of industrial upenders, helping you make informed decisions.
The Upside: Performance and Efficiency Gains
In the quest for optimized industrial operations, lightweighting upenders presents compelling advantages. Reducing the overall mass, particularly of moving components, directly translates into tangible performance improvements. This isn’t just about marginal gains; it can redefine operational efficiency, speed, and energy usage, offering a significant competitive edge in high-throughput manufacturing and logistics environments where cycle time and energy costs are paramount.
The primary benefits of employing lightweight materials in upenders center on enhanced equipment performance and reduced operational costs. Lighter structures, especially rotating or tilting platforms, possess lower inertia, enabling faster acceleration and deceleration. This leads to quicker cycle times, boosting productivity. Reduced mass also decreases the energy required for movement, lowering electricity consumption per cycle. Furthermore, lighter overall weight can simplify transportation and installation, potentially reducing foundation requirements and handling equipment needs. Materials like aluminum alloys and advanced steels offer excellent strength-to-weight ratios, while design optimization techniques like topology optimization, often facilitated by advanced software, can further minimize material usage without sacrificing structural integrity.
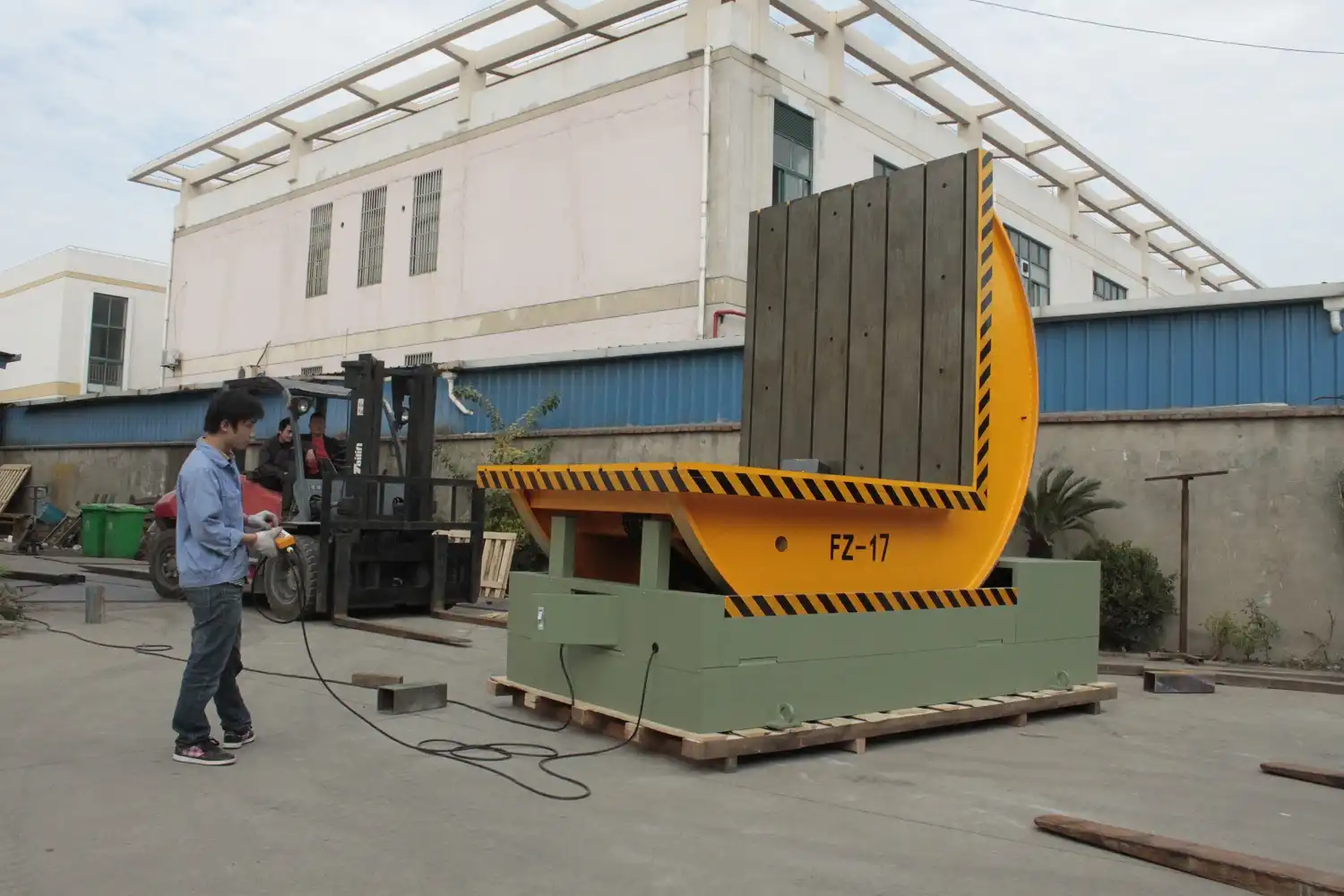
Deep Dive into Lightweighting Advantages
Exploring the benefits further reveals how lightweighting impacts various aspects of upender operation and ownership:
Energy Savings Breakdown
Reducing the mass that needs to be moved directly cuts down on the energy required by motors and drive systems. While exact savings depend heavily on the specific design, duty cycle, and extent of lightweighting, the principle remains constant: less mass requires less energy to accelerate, decelerate, and lift against gravity. This is particularly impactful in applications with frequent start/stop cycles.
Material Substitution | Typical Weight Reduction vs. Mild Steel | Estimated Energy Saving Potential (High Cycle) | Notes |
---|---|---|---|
Advanced High-Strength Steel | 15-25% | 5-10% | Moderate cost increase, compatible joining |
Aluminum Alloys | 40-60% | 15-25% | Higher cost, joining challenges |
Carbon Fiber Composites | 50-70% | 20-35%+ | Very high cost, complex manufacturing |
Note: Energy savings are estimates and vary greatly based on application specifics.
Enhanced Speed and Cycle Times
Lower inertia is a direct consequence of reduced mass. For an upender’s tilting or rotating mechanism, this means the drive system can achieve target speeds and positions faster, with less energy input and potentially less overshoot. Shaving seconds off each cycle can accumulate into significant productivity increases over a shift or production run, directly impacting throughput and profitability.
Improved Handling and Installation
A lighter upender is inherently easier to transport, maneuver into position, and install. This can lead to lower shipping costs, reduced need for heavy-duty lifting equipment during installation, and potentially less robust foundation requirements. For facilities where equipment might be relocated periodically, the ease of handling a lighter machine is a distinct advantage, minimizing downtime and associated labor costs.
Reduced Wear on Components
Moving less weight puts less strain on drive components like motors, gearboxes, bearings, and actuators. This can translate to longer component life, reduced maintenance requirements, and lower replacement costs over the lifespan of the upender. The smoother acceleration and deceleration profiles possible with lower inertia systems also contribute to reduced mechanical stress.
Navigating the Challenges: Cost and Complexity
While the performance benefits are attractive, adopting lightweight materials in upender construction is not without significant hurdles. The transition from traditional heavy steel fabrication involves navigating increased costs, mastering new manufacturing techniques, and carefully engineering designs to ensure long-term reliability. These challenges represent the primary barriers to widespread adoption, particularly in cost-sensitive industrial applications.
The main drawbacks of using lightweight materials in upenders revolve around increased costs and manufacturing complexity. Materials like aluminum, magnesium, and especially carbon composites are inherently more expensive than traditional steel. Fabricating and joining these materials often requires specialized equipment, techniques (like friction stir welding for aluminum or adhesive bonding for composites), and skilled labor, further driving up manufacturing costs. Ensuring long-term durability and fatigue resistance comparable to steel structures also demands sophisticated engineering analysis and potentially thicker sections, partially offsetting weight savings.
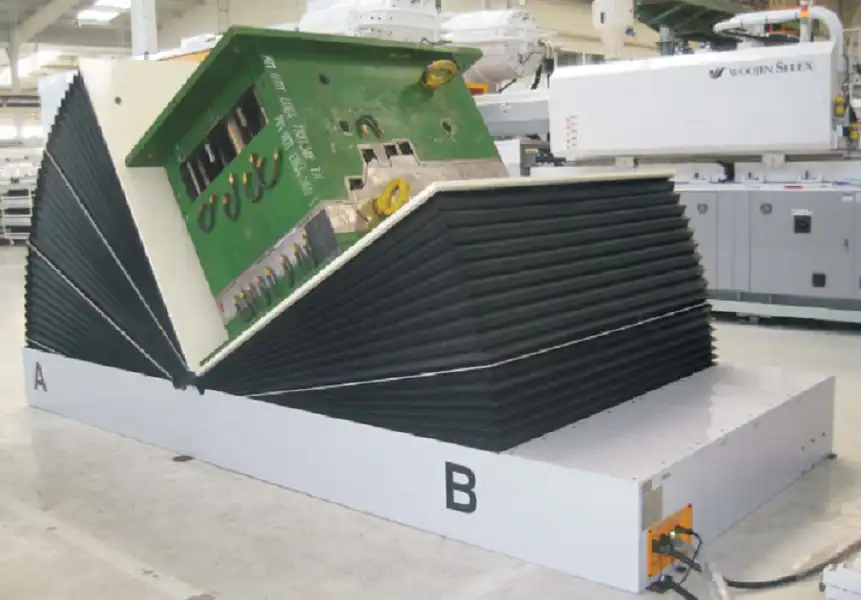
Overcoming Lightweighting Hurdles in Upender Manufacturing
Addressing these challenges is key to successfully implementing lightweight designs:
Material Cost Analysis
The raw material cost is often the most immediate barrier. While prices fluctuate, lightweight alternatives are consistently more expensive per kilogram than standard structural steel.
- Steel: Baseline cost.
- Advanced High-Strength Steel (AHSS): Moderately higher cost than mild steel, offering a good balance for structural components.
- Aluminum Alloys: Significantly more expensive than steel, requires different processing.
- Magnesium Alloys: Even more expensive than aluminum, with added processing and corrosion concerns.
- Carbon Fiber Composites: Highest material cost by a large margin, often prohibitive for general industrial equipment.
Manufacturers must weigh the upfront material cost against potential long-term operational savings (energy, maintenance) and performance gains.
Manufacturing Process Adjustments
Working with lightweight materials often necessitates changes throughout the production line:
- Joining: Welding aluminum requires different techniques (MIG/TIG with specific shielding gases, friction stir welding) and equipment compared to steel. Joining dissimilar materials (e.g., aluminum to steel) presents galvanic corrosion risks and requires specialized transition joints or fasteners. Composites often rely on adhesive bonding, demanding meticulous surface preparation and curing processes.
- Forming: Some high-strength steels and aluminum alloys have lower formability than mild steel, requiring more powerful presses or different forming strategies. Composites are often molded into shape, a completely different process from metal fabrication.
- Machining: Machining aluminum is generally faster than steel but requires different tooling and coolant strategies. Machining composites generates abrasive dust and requires specialized diamond-coated tools.
- Handling: While lighter, some materials like composites can be susceptible to damage from impact or improper handling during manufacturing.
Design Considerations for Durability
Lightweight doesn’t mean weak, but achieving comparable strength and fatigue life requires careful engineering. Finite Element Analysis (FEA) becomes critical to identify stress concentrations and optimize geometry. Material selection must consider not just static strength but also fatigue resistance, impact toughness, and environmental factors (temperature, corrosion). For instance, aluminum generally has lower fatigue endurance than steel, requiring careful design in cyclic loading scenarios common in upenders. Reinforcements or localized use of stronger materials might be necessary in critical areas.
Repair and Maintenance Implications
Repairing damage to lightweight structures can be more complex and costly. Welding repairs on aluminum require specialized skills. Damage to composite structures often necessitates patch repairs or component replacement, which can be expensive and time-consuming. Maintenance personnel may need additional training to work with these materials safely and effectively. Accessibility for inspection and repair must be considered during the design phase.
Material Focus: Choosing the Right Lightweight Option
Feeling overwhelmed by material choices? Selecting the appropriate lightweight material is not a one-size-fits-all decision. Each option presents a unique profile of strengths, weaknesses, costs, and manufacturing considerations. Making the wrong choice can negate potential benefits or lead to premature failure, highlighting the importance of matching the material to the specific demands of the upender application.
Choosing the optimal lightweight material for an upender involves balancing weight reduction goals with cost constraints, manufacturing capabilities, and performance requirements. Advanced High-Strength Steels (AHSS) offer moderate weight savings with good strength and relatively easy integration. Aluminum alloys provide significant weight reduction but come with higher costs and joining challenges. Carbon fiber composites deliver maximum weight savings and stiffness but are typically reserved for specialized, high-budget applications due to extreme cost and complex manufacturing.
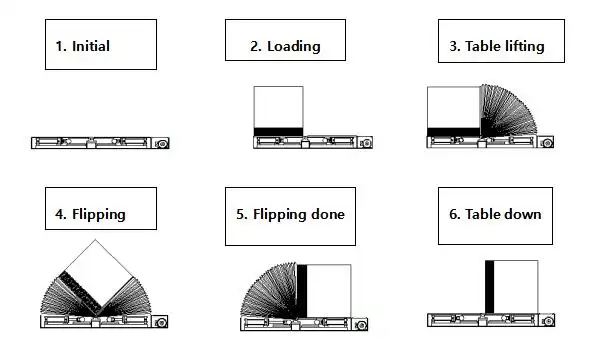
Comparative Analysis of Lightweight Materials for Upenders
A deeper look into the most relevant lightweight materials for upender construction reveals their specific trade-offs:
Advanced High-Strength Steel (AHSS)
- Pros: Offers a good strength-to-weight ratio improvement over mild steel (up to 25% weight reduction for similar strength). Generally compatible with existing steel fabrication infrastructure (welding, forming with adjustments). Relatively low cost compared to other lightweight options. Good stiffness and durability.
- Cons: Higher cost than mild steel. Can increase wear on stamping/forming tooling. Ductility decreases as strength increases, potentially limiting complex shapes. Joining requires careful parameter control.
Aluminum Alloys
- Pros: Excellent strength-to-weight ratio (potential for 40-60% weight reduction). Good corrosion resistance (depending on alloy and environment). Relatively mature technology with well-understood properties. Good energy absorption characteristics.
- Cons: Significantly higher material cost than steel. Joining requires specialized techniques (welding, fasteners, bonding) and careful consideration of galvanic corrosion when joined with steel. Lower fatigue strength than steel requires careful design. Lower stiffness than steel requires larger cross-sections for equivalent rigidity.
Carbon Fiber Reinforced Polymers (CFRP / Composites)
- Pros: Highest strength-to-weight and stiffness-to-weight ratios (potential for 50-70% weight reduction). Excellent fatigue resistance. Ability to create complex, integrated shapes through molding. Tremendous potential for performance optimization.
- Cons: Extremely high material and manufacturing costs. Manufacturing processes (layup, curing) are slow and complex compared to metal fabrication. Joining to metal structures is challenging. Susceptible to impact damage. Repair is specialized and costly. Performance modeling can be complex.
Material Properties Comparison Table
Property | Mild Steel (Baseline) | AHSS (Typical) | Aluminum (6061-T6) | Carbon Fiber (Typical) | Notes |
---|---|---|---|---|---|
Density (g/cm³) | ~7.85 | ~7.85 | ~2.70 | ~1.60 | Lower density is key to lightweighting |
Yield Strength (MPa) | ~250 | 400 – 1000+ | ~276 | 600 – 2000+ | Strength indicates load before permanent deformation |
Stiffness (Young’s Modulus GPa) | ~200 | ~200 | ~69 | 70 – 200+ | Stiffness impacts deflection under load |
Relative Cost Index | 1 | 1.2 – 2 | 3 – 5 | 20 – 50+ | Approximate cost comparison per unit weight |
Key Challenge for Upenders | Weight | Formability/Joining | Cost/Fatigue/Joining | Cost/Impact/Repair | Primary hurdles for implementation |
Note: Values are approximate and vary significantly based on specific alloys, grades, and fiber/resin systems.
The optimal choice often involves a multi-material approach, using the right material in the right place – perhaps AHSS for the main frame, aluminum for the platform structure, and composites for specific high-performance components if the budget allows.
The Future Outlook: Innovation and Integration
The journey towards lighter, more efficient upenders is ongoing, driven by advancements in material science, manufacturing processes, and computational design tools. While challenges remain, the potential benefits continue to spur innovation, suggesting that lightweight materials will play an increasingly significant role in the future of industrial load handling equipment, moving beyond niche applications towards broader adoption.

The future of lightweighting in upenders likely involves sophisticated multi-material designs, leveraging the strengths of each material where it’s most effective. Advanced computational tools like topology optimization and generative design will enable engineers to create highly efficient structures impossible with traditional methods. Improved joining technologies for dissimilar materials, potentially lower costs through increased adoption and research (like efforts seen in the automotive sector), and advancements in additive manufacturing for complex geometries will further facilitate the integration of lightweight solutions without compromising safety or performance. Continued research and development, focusing on cost reduction, improved manufacturing processes (especially for joining and forming), enhanced durability modeling, and easier recycling, are essential. Computational materials science promises to accelerate the development and deployment of new alloys and composites tailored for industrial machinery needs. Tools like Finite Element Analysis (FEA) are already indispensable, but future software will likely offer even more integrated optimization capabilities, allowing designers to automatically generate lightweight structures that meet specific performance criteria (stiffness, strength, fatigue life) while minimizing mass. Additive manufacturing (3D printing), while currently expensive for large structural parts, holds potential for creating highly complex, internally optimized lightweight components, jigs, or fixtures that are difficult or impossible to make conventionally. As these technologies mature and costs decrease, their application in upender construction could become more viable. Furthermore, developing robust and cost-effective methods for recycling multi-material structures will be crucial for sustainability as lightweight designs become more common.
Conclusion
Ultimately, the decision to use lightweight materials in modern upenders hinges on a careful cost-benefit analysis specific to the application. The pros – improved equipment performance, energy efficiency, faster cycle times, and easier handling – are compelling, particularly for demanding, high-throughput operations. However, these must be weighed against the significant cons of higher initial costs, increased manufacturing complexity, and the need for specialized design and maintenance expertise. Utilizing Advanced materials like AHSS, aluminum, or even composites requires a strategic approach, often involving multi-material designs and sophisticated engineering to ensure durability and safety. As technology progresses and costs potentially decrease, lightweighting will undoubtedly become more prevalent, but for now, it requires a clear understanding of the trade-offs involved for successful implementation in equipment like a mold upender.