What Are the Key Features of Advanced Plastic Pipe Bagging Machines?
Advanced plastic pipe bagging machines revolutionize pipe packaging. These machines offer automated solutions for filling and sealing pipes and tubes, and significantly boosting production efficiency. The key features of these machines enhance functionality, minimize maintenance, and ensure high output for various industrial applications.
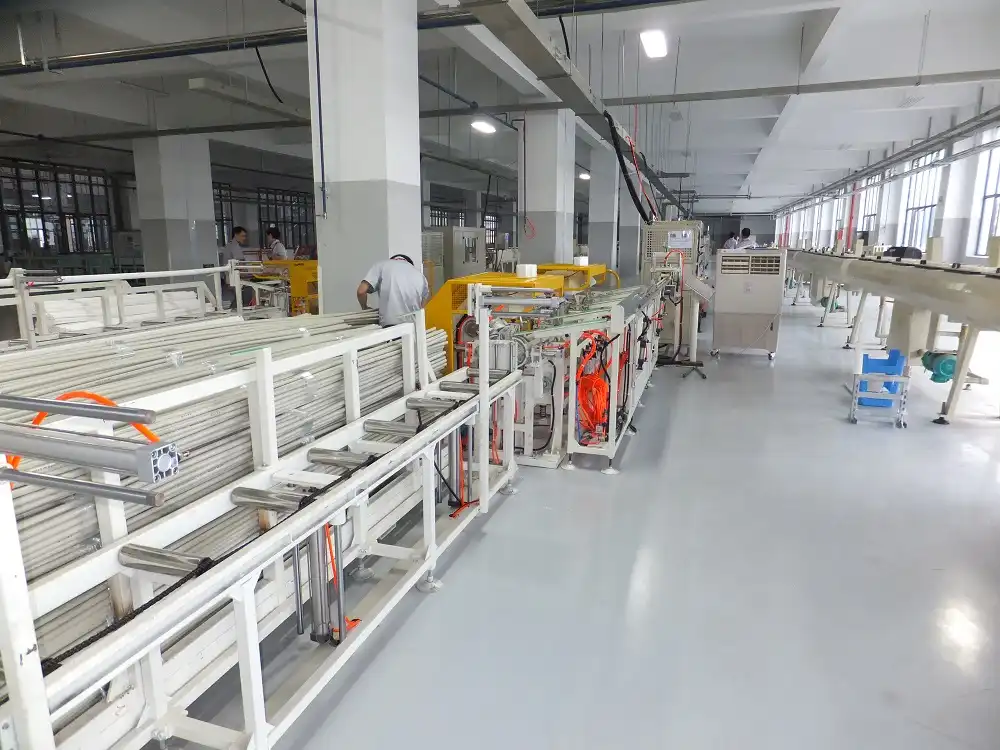
Advanced plastic pipe bagging machines automate pipe packaging with key features. These include automatic feeding, precise cutting, film feeding, reliable sealing, and efficient output. These machines handle single plastic pipes, PVC pipes, rods, and copper pipes. With PLC control and high-speed operation, they provide efficiency, functionality, and minimal maintenance.
As industries increasingly demand efficient and reliable packaging solutions, understanding the features of advanced plastic pipe bagging machines becomes essential. Let’s explore these key aspects in detail.
1. Automation and Feeding Systems
A primary feature of advanced pipe bagging machines is their level of automation. Automation ensures consistent, high-speed operation, and reduces the need for manual intervention, lowering labor costs.
Automatic feeding systems are vital in plastic pipe bagging machines. These systems ensure continuous pipe flow, reduce manual labor, and maintain consistent production speeds. They typically include pipe collectors and aligners, feeding the pipes smoothly into the bagging process. This system guarantees optimized efficiency and minimal downtime.
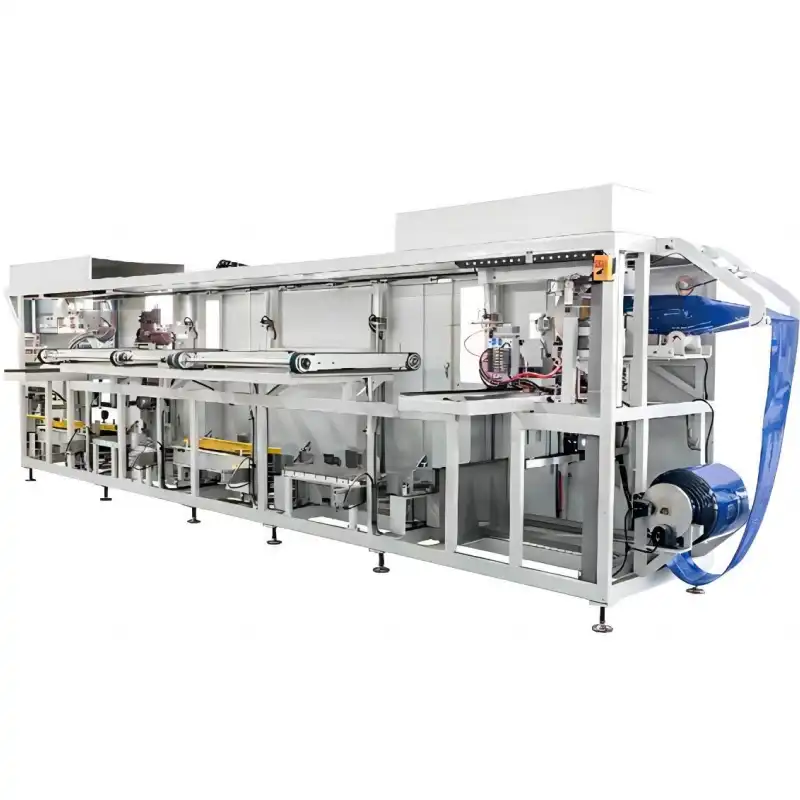
To delve deeper into the automatic feeding and alignment systems, let’s consider the different types of feeders and their impact on overall efficiency.
Types of Automatic Feeders
Automatic feeders can vary based on the type of pipe and the desired production rate. Here’s a comparison of common feeder types:
Feeder Type | Description | Advantages | Disadvantages | Best Suited For |
---|---|---|---|---|
Vibratory Feeders | Uses vibration to move pipes along a track. | Simple, reliable, and cost-effective. | Can be noisy; less precise for very high-speed applications. | High-volume, low-precision applications. |
Belt Conveyor Feeders | Uses a conveyor belt to transport pipes. | Versatile, handles various pipe sizes and materials, and offers good control. | Requires more maintenance than vibratory feeders. | Medium to high-volume, medium-precision applications. |
Robotic Feeders | Uses robotic arms to pick and place pipes. | Highly precise, flexible, and adaptable to different pipe arrangements. | High initial cost; requires skilled programming and maintenance. | High-precision, flexible applications. |
Vibratory Feeders: Efficient and Cost-Effective
Vibratory feeders are a common choice for many pipe bagging applications due to their simplicity and reliability. These feeders use vibration to move the pipes along a track to the bagging station. They are particularly effective when dealing with consistent pipe sizes and materials.
Belt Conveyor Feeders: Versatile Pipe Handling
Belt conveyor feeders provide a more versatile approach. These systems use a conveyor belt to transport the pipes, offering better control over pipe placement and speed. Belt feeders are suitable for handling a wider range of pipe sizes and materials.
Robotic Feeders: Precision and Flexibility
Robotic feeders represent the cutting edge in automation. These systems use robotic arms to pick and place the pipes with high precision. They are highly adaptable to different pipe arrangements and can be programmed to handle complex loading patterns.
Impact on Production Efficiency
The choice of the feeder system significantly impacts the overall production efficiency. The right feeder can reduce downtime, minimize material waste, and improve the consistency of the bagging process.
For instance, a robotic feeder in a high-precision application can dramatically reduce the number of misaligned pipes, leading to fewer rejected bags and higher throughput. Belt conveyor feeders in medium-volume applications offer a balance of versatility and control, ensuring a steady flow of pipes without the high costs associated with robotic systems.
2. Precision Cutting and Sealing Units
Accurate cutting and sealing are fundamental to producing high-quality packaged pipes. These units ensure that each bag is properly sealed and the pipes are securely enclosed.
Cutting and sealing units in pipe bagging machines are designed for accuracy and reliability. Electronic controllers ensure millimetric precision in cutting the film. Sealing units create strong, airtight seals, protecting the pipes. These features are crucial for maintaining product integrity and extending shelf life. Advanced sealing technology is essential for high-quality packaging.
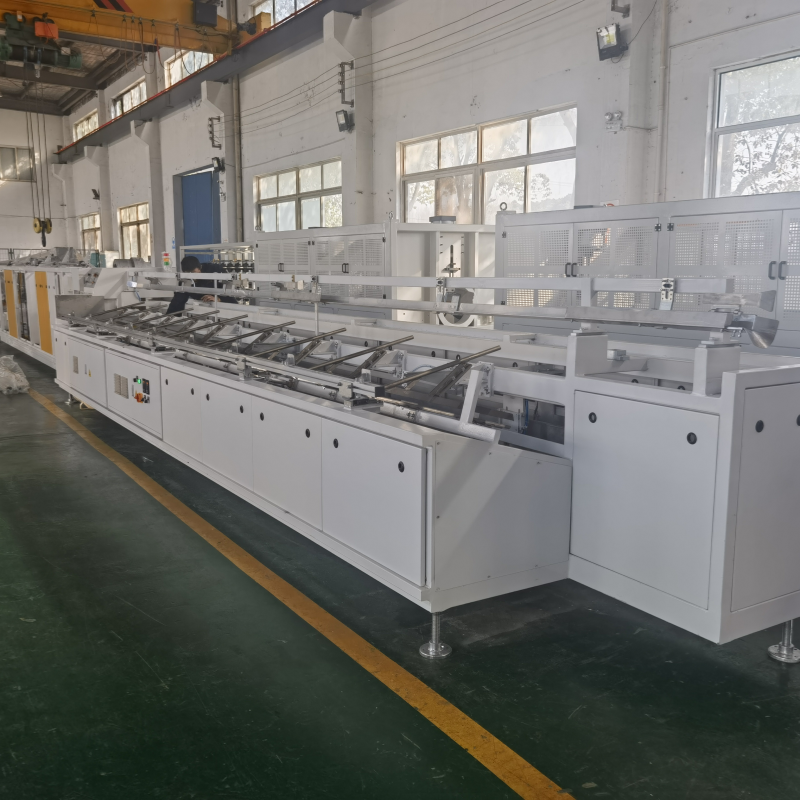
Let’s discuss different types of sealing mechanisms and the specific benefits they bring to the pipe packaging process.
Sealing Mechanisms: Heat Sealing vs. Ultrasonic Sealing
Choosing the right sealing mechanism can significantly affect the quality and durability of the package. Here’s a comparison of two popular methods:
Feature | Heat Sealing | Ultrasonic Sealing |
---|---|---|
Mechanism | Melts the film layers together using heat and pressure. | Uses high-frequency vibrations to create a friction-based seal. |
Materials | Suitable for a wide range of plastic films. | Works well with specific types of films, including those with coatings or laminates. |
Energy Efficiency | Can be less energy-efficient due to the heating process. | Generally more energy-efficient. |
Seal Strength | Provides a strong and reliable seal. | Offers excellent seal strength, especially for difficult-to-seal materials. |
Speed | High-speed sealing is achievable with advanced temperature control systems. | Typically faster than heat sealing. |
Heat Sealing: The Traditional Choice
Heat sealing is a well-established method that uses heat and pressure to melt the film layers together, creating a robust seal. This method is suitable for a broad range of plastic films.
Ultrasonic Sealing: Modern and Efficient
Ultrasonic sealing employs high-frequency vibrations to generate heat through friction, which then seals the film. This method is particularly effective for films with coatings or laminates.
Integration with Cutting Units
The cutting unit works in tandem with the sealing mechanism to ensure the bags are appropriately sized and sealed. Electronic controllers provide millimetric precision, ensuring consistent bag dimensions. This precision is crucial for maintaining the aesthetic appeal of the packaged pipes and reducing material waste.
Benefits of Precise Cutting and Sealing
Precise cutting and sealing offer several key benefits:
- Enhanced Product Protection: Properly sealed bags protect the pipes from moisture, dust, and other contaminants.
- Improved Presentation: Consistent bag sizes and clean cuts enhance the visual appeal of the packaged pipes.
- Reduced Material Waste: Accurate cutting minimizes excess film use, leading to cost savings.
3. Film Feeding and Tension Control
Efficient film feeding and tension control are crucial for consistent and reliable bagging. These systems ensure the film is correctly positioned, tensioned, and fed into the sealing area.
Film feeding systems ensure a continuous supply of packaging film. Automatic tension control maintains consistent film tension, preventing wrinkles and misalignments. These features enhance the quality of the bags and the efficiency of the packing process. Proper film handling is essential for maintaining consistent output and minimizing downtime.
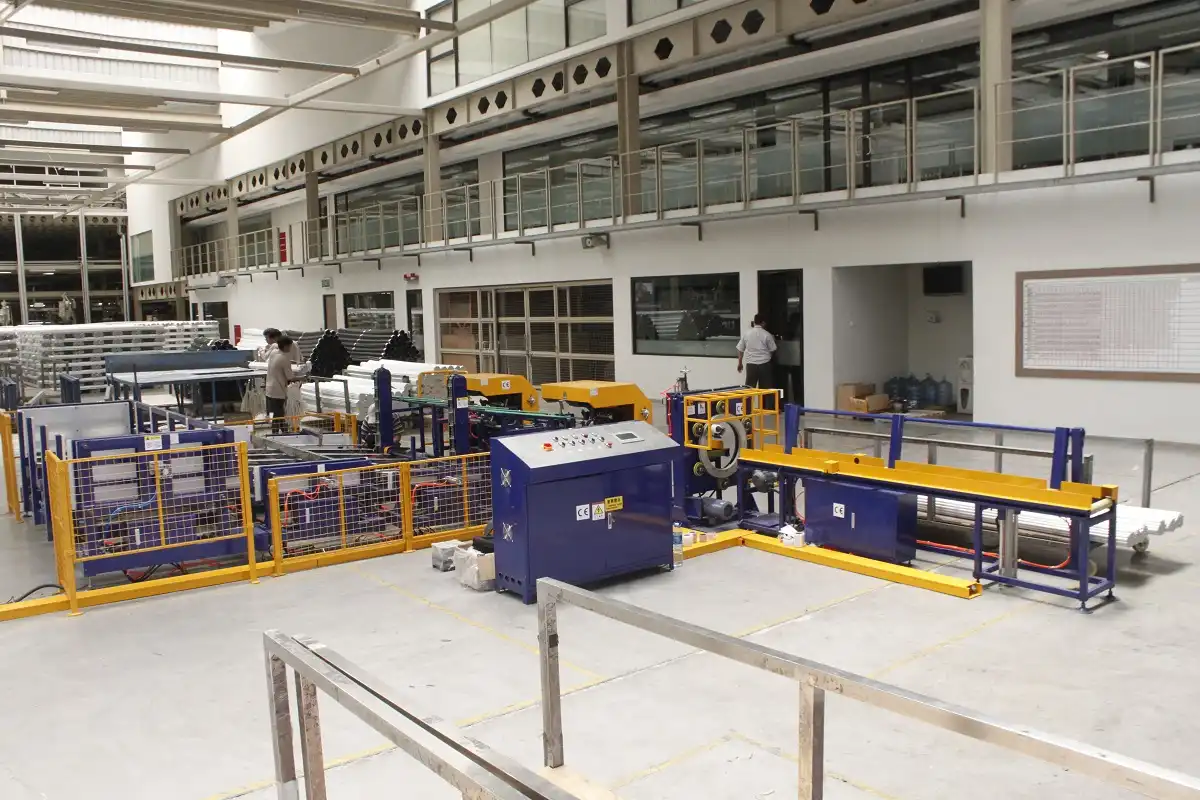
Now, let’s discuss various types of film feeding mechanisms and tension control systems, and how they impact the bagging process.
Types of Film Feeding Mechanisms
Different feeding mechanisms offer unique advantages depending on the type of film used and the desired production speed. Here’s a look at some of the common types:
Feeding Mechanism | Description | Advantages | Disadvantages |
---|---|---|---|
Motorized Unwind Systems | Uses a motor to unwind the film roll. | Provides consistent and controlled film feeding, reduces strain on the film. | Requires precise control systems to avoid over-tensioning or slack. |
Dancer Arm Systems | Employs a weighted arm to maintain film tension. | Simple and reliable, provides good tension control without complex electronics. | Less precise than motorized systems, may require manual adjustments. |
Pneumatic Tension Control | Uses air pressure to control film tension. | Offers responsive tension control, suitable for high-speed applications. | Requires a clean and consistent air supply, can be sensitive to pressure fluctuations. |
How Tension Control Impacts Bag Quality
Maintaining proper film tension is critical for several reasons:
- Wrinkle Prevention: Consistent tension prevents wrinkles in the film, ensuring a smooth, professional-looking bag.
- Accurate Sealing: Proper tension ensures the film is correctly aligned during the sealing process, leading to a stronger, more reliable seal.
- Reduced Material Waste: Consistent tension minimizes film breakage and misalignment, reducing material waste.
4. Integration and Customization
Advanced bagging machines can be integrated with other production line components, creating a seamless packaging solution. Customization options also allow the machines to be tailored to specific needs.
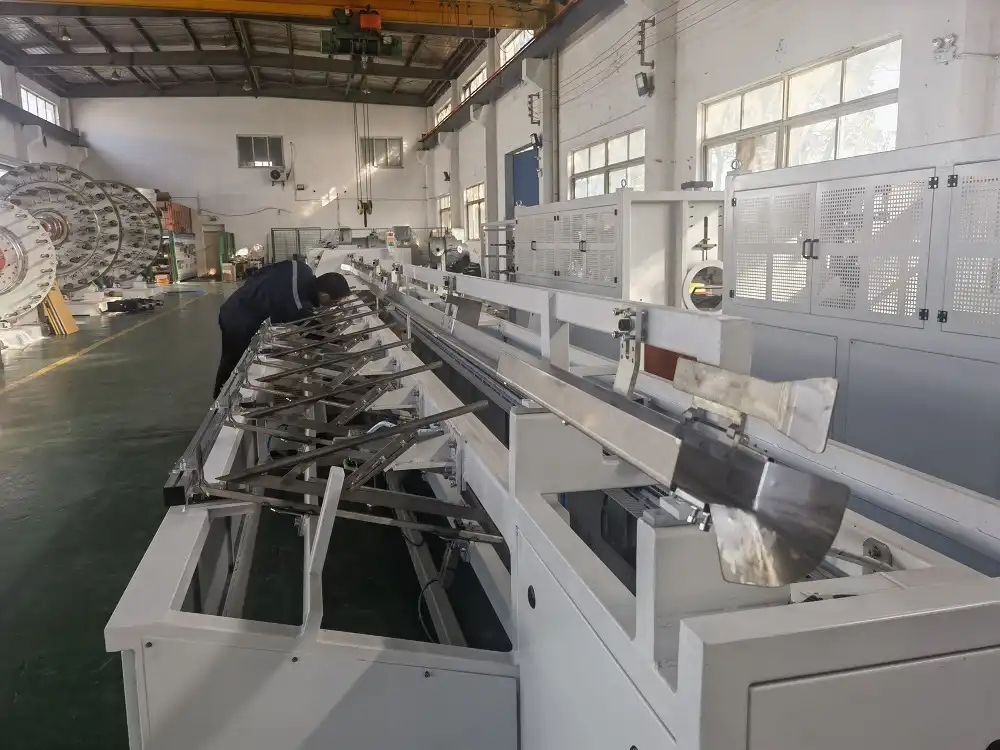
Integrating bagging machines with existing production lines streamlines the packaging process. Customization options enable the machines to meet specific pipe sizes, bag dimensions, and production requirements. This includes adjustable settings for pipe diameter, bag length, and sealing parameters, ensuring optimal performance for diverse applications.
The key to successful integration and customization lies in understanding the specific requirements of the production line.
Successful integration often requires close collaboration between the machine manufacturer and the end-user. By working together, they can identify potential bottlenecks and develop customized solutions to optimize the packaging process.
Advanced plastic pipe bagging machines are indispensable for efficient and reliable pipe packaging. Their key features—automation, precision cutting and sealing, efficient film feeding, and integration capabilities—ensure high-quality results. Investing in these machines optimizes production processes, reduces costs, and delivers consistent performance.
Conclusion
Advanced plastic pipe bagging machines provide a comprehensive solution for packaging needs in the plastic and steel industries. Their key features, such as automatic feeding, precise cutting, and reliable sealing, drive efficiency and reduce operational costs. By automating the bagging process, these machines ensure consistent quality and high throughput, leading to significant improvements in productivity. Investing in this PVC pipe packaging technology enhances overall operational effectiveness and ensures that businesses remain competitive in today’s fast-paced market.