What Are the Key Considerations for Pipe Bundling Machine Installation?
Installing a pipe bundling machine can significantly streamline your operations. However, success hinges on careful planning and consideration of several key factors. Overlooking these aspects can lead to costly delays and inefficiencies. Ensuring a smooth installation is paramount.
To ensure a successful pipe bundling machine installation, consider mechanical, electrical, and operational compatibility. Assess space, power, and control system interfaces. Adhere to integration guidelines, conduct thorough testing, and prioritize regular maintenance. This proactive approach optimizes performance and minimizes disruptions.
Implementing a new pipe bundling machine can be a game-changer for your production line. However, before diving in, let’s delve into the key considerations that will pave the way for a seamless and efficient installation.
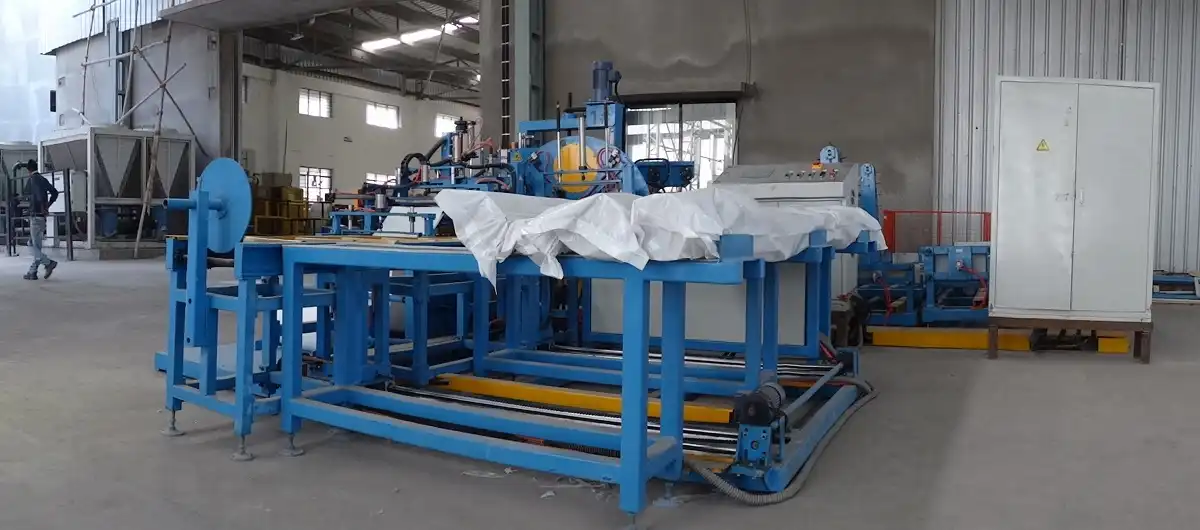
1. Mechanical Compatibility: Ensuring a Seamless Physical Fit
A seamless mechanical integration is the cornerstone of any successful pipe bundling machine installation. It’s about more than just fitting the machine into your existing space; it’s about ensuring it enhances the overall flow and efficiency of your production line.
Mechanical compatibility involves assessing the physical dimensions, conveyor alignment, and material handling systems. Verify the machine fits the available space, aligns with existing conveyors, and can handle the pipe sizes and weights. Addressing these points minimizes disruptions and maximizes efficiency.
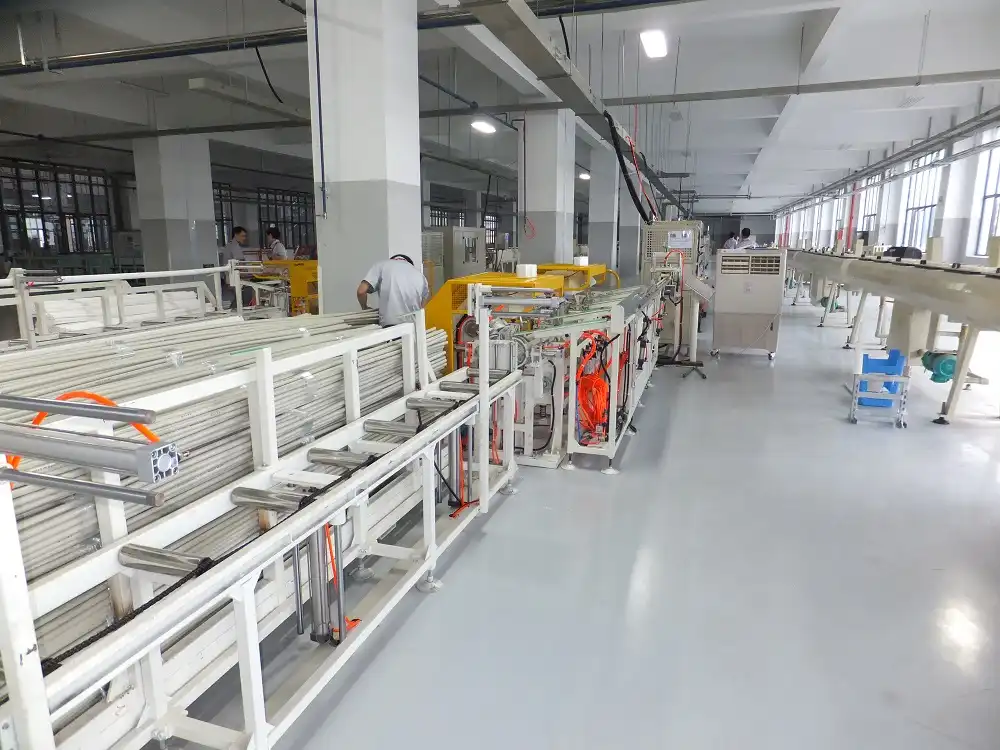
Subtitle: Key Considerations for Seamless Mechanical Integration
Achieving seamless mechanical integration involves detailed planning and precise execution. Let’s break down the critical aspects:
1.1 Physical Dimensions and Space Requirements
The first step is to meticulously measure the available space. This includes not just the footprint of the machine but also the overhead clearance and surrounding areas required for operation and maintenance. Consider:
- Machine Footprint: Measure the length, width, and height of the new machine.
- Operational Space: Account for space needed for operators to move around, access controls, and perform maintenance.
- Safety Clearances: Ensure adequate safety clearances around moving parts and emergency stops.
1.2 Conveyor and Transfer System Alignment
The integration of the new machine with existing conveyor and transfer systems is critical for continuous operation. Key factors to consider include:
- Height Alignment: Verify that the infeed and outfeed heights of the new machine align with the existing conveyors. Height discrepancies can cause jams, damage pipes, and disrupt flow.
- Transfer Mechanisms: Evaluate the transfer mechanisms. How will pipes be moved from the existing system to the new machine and back? Common solutions include roller conveyors, belt conveyors, and pneumatic systems. Ensure these are compatible.
- Pipe Diameter and Weight: Ensure the transfer system can handle the range of PVC pipe diameters and weights that your facility processes. Overloading the system can lead to failures.
1.3 Material Handling and Support
Proper material handling and support are essential to prevent damage and ensure consistent feeding. This includes:
- Infeed and Outfeed Support: Adequate support structures should be in place to prevent pipes from sagging or bending as they enter and exit the machine.
- Cushioning and Protection: Implement cushioning materials or mechanisms to prevent scratches or damage to the pipes during handling.
- Jam Detection: Integrate sensors and jam detection systems to automatically stop the machine in case of issues, preventing further damage.
1.4 Addressing Challenges
Even with careful planning, challenges may arise during mechanical integration. This table outlines common issues and their solutions:
Challenge | Solution |
---|---|
Misalignment of Conveyors | Use adjustable conveyor sections to fine-tune height and alignment. Consider custom-built transfer sections to bridge significant gaps. |
Space Constraints | Reconfigure the existing layout, explore vertical integration, or opt for a more compact machine design. |
Pipe Damage During Transfer | Implement cushioned transfer mechanisms, reduce transfer speeds, and ensure smooth transitions. |
Inconsistent Pipe Feeding | Install sensors to detect pipe presence and adjust feeding speeds. Implement a buffer system to ensure a consistent supply of pipes. |
By carefully assessing these mechanical aspects, you can ensure a seamless and efficient integration of the new pipe packaging solutions, minimizing disruptions and maximizing productivity.
2. Electrical and Control System Integration: Harmonizing the Machine’s Brain
Electrical and control system compatibility ensures the new machine can communicate effectively with existing systems, enabling seamless operation.
Electrical and control system integration requires matching voltage, current, and wiring configurations. Control system synchronization requires understanding communication protocols and software synchronization. Proper integration minimizes conflicts and ensures a harmonized, efficient production line.

Subtitle: Ensuring Seamless Electrical and Control System Integration
A pipe bundling machine’s electrical and control systems must integrate with existing infrastructure to avoid operational conflicts and maximize efficiency. This involves careful consideration of power requirements, communication protocols, and software compatibility.
2.1 Electrical System Requirements
Matching the electrical system requirements is fundamental for safe and reliable operation.
- Voltage Compatibility: Verify the machine’s voltage requirements (e.g., 220V, 480V) and ensure they match your facility’s electrical supply. Installing a transformer may be necessary if there’s a mismatch.
- Current Capacity: Check the machine’s current draw and ensure your electrical circuits can handle the load. Overloading circuits can cause breakers to trip or, worse, electrical fires.
- Wiring Configurations: Confirm the wiring configurations (e.g., three-phase, single-phase) are compatible. Incorrect wiring can damage the machine.
- Safety Compliance: Ensure the machine meets all relevant electrical safety standards (e.g., UL, CE). Look for certifications that guarantee adherence to these standards.
2.2 Control System Synchronization
Integrating the control system allows the new machine to communicate with existing equipment, creating a cohesive production line. Key elements include:
- Communication Protocols: Identify the communication protocols used by your existing systems (e.g., Ethernet/IP, Profinet, Modbus). The new machine’s controller must support these protocols for seamless data exchange.
- Software Compatibility: Ensure the new machine’s software is compatible with your existing Manufacturing Execution System (MES) or Enterprise Resource Planning (ERP) systems. Data synchronization is crucial for monitoring performance and tracking production.
- PLC Integration: Programmable Logic Controllers (PLCs) often manage automated systems. If your facility uses PLCs, ensure the new machine can be integrated into the PLC network.
- Sensor Synchronization: Integrate sensors to provide real-time feedback and coordination between the new and existing machines. This can optimize material flow and prevent bottlenecks.
2.3 Power Management and Surge Protection
Electrical systems must also be protected from voltage fluctuations and power surges. Key precautions:
- Surge Suppressors: Install surge suppressors to protect sensitive electronic components from voltage spikes.
- Voltage Regulators: Use voltage regulators to stabilize voltage levels, especially in areas with unreliable power.
- Emergency Power-Off (EPO) Systems: Integrate the new machine into your facility’s EPO system for quick and safe shutdowns during emergencies.
2.4 Addressing Integration Challenges
Electrical and control system integration can present unique challenges. Here’s a table outlining common issues and their solutions:
Challenge | Solution |
---|---|
Protocol Mismatches | Use protocol converters or gateways to translate between different communication protocols. Work with a qualified integrator to configure these devices properly. |
Software Incompatibilities | Update existing software to support the new machine, or use middleware to bridge the gap. Custom software development may be necessary in some cases. |
Electrical Overloads | Upgrade electrical circuits or distribute the load. Consult with an electrical engineer to ensure your facility’s electrical system can handle the new machine’s power requirements. |
Interference Issues | Use shielded cables and filters to minimize electromagnetic interference (EMI). Ensure proper grounding to prevent ground loops. |
By meticulously addressing these electrical and control system aspects, you can achieve a fully integrated and efficient pipe bundling operation, minimizing downtime and maximizing throughput.
3. Adhering to Integration Guidelines: Charting a Course for Success
Compatibility isn’t just about technical specifications; it’s also about following best practices and guidelines to ensure a smooth integration process.
Integration guidelines encompass pre-installation checks, sequential implementation, comprehensive testing, and documentation. Perform thorough assessments before installation and test after. Sequential implementation helps to manage risks. Document every step for future reference.
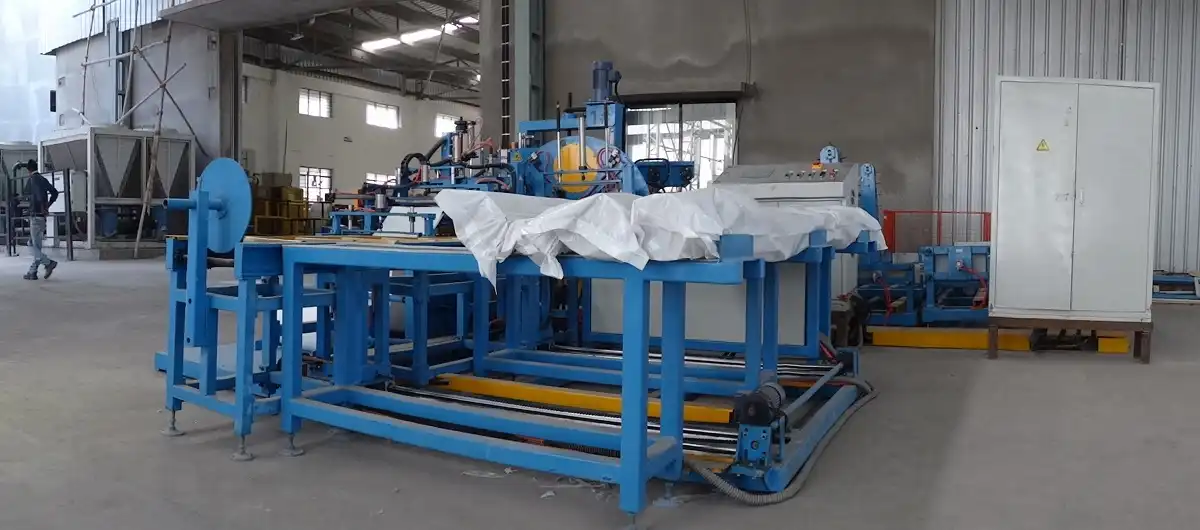
Subtitle: Streamlining Integration through Strategic Guidelines
To guarantee the successful integration of a pipe bundling machine, adhering to specific guidelines is essential. These guidelines encompass careful planning, structured implementation, rigorous testing, and meticulous documentation.
3.1 Pre-Installation Assessments
Thorough assessments prior to installation lay the foundation for a seamless integration. This includes:
- Detailed Site Survey: Conduct a detailed site survey to identify any physical constraints, electrical infrastructure limitations, or environmental factors that may impact the installation.
- Compatibility Checklists: Develop checklists to verify the compatibility of all mechanical, electrical, and software interfaces.
- Risk Assessment: Perform a risk assessment to identify potential integration challenges and develop mitigation strategies.
3.2 Sequential Implementation
A phased implementation approach minimizes disruptions and allows for early detection of issues. Common phases include:
- Preparation: Prepare the site, including any necessary modifications to the layout, electrical systems, or support structures.
- Installation: Install the machine according to the manufacturer’s specifications.
- Testing: Conduct initial testing to verify basic functionality.
- Integration: Integrate the machine with existing systems.
- Optimization: Fine-tune the machine settings and system parameters to achieve optimal performance.
3.3 Comprehensive Testing
Rigorous testing at each stage of implementation is critical for identifying and addressing issues early on. This includes:
- Functional Testing: Verify that all machine functions are operating correctly.
- Performance Testing: Evaluate the machine’s performance under load, including throughput, accuracy, and efficiency.
- Integration Testing: Test the integration with existing systems to ensure seamless communication and data exchange.
- Stress Testing: Subject the machine to prolonged periods of operation to identify potential weaknesses or failure points.
3.4 Documentation and Training
Thorough documentation and adequate training are essential for long-term success. This includes:
- Detailed Manuals: Ensure comprehensive operation, maintenance, and troubleshooting manuals are available.
- Training Programs: Conduct training programs for operators and maintenance staff to ensure they are proficient in using and maintaining the machine.
- Version Control: Implement version control for software and configurations to manage changes and prevent compatibility issues.
3.5 Example Scenario
Consider this scenario: A company is integrating a new pipe bundling machine into an existing production line. By meticulously following these guidelines, they can ensure a smooth transition and maximize the benefits of the new technology.
First, they conduct a site survey to identify a potential height difference between the existing conveyor system and the new machine. To address this, they plan for a height-adjustable conveyor section to bridge the gap. Secondly, the test phase confirmed a software incompatibility, and it was resolved before integration.
Here is a table with maintenance schedules: | Task | Frequency | Description |
---|---|---|---|
Visual Inspection | Daily | Check for loose parts, leaks, and damage. | |
Lubrication | Weekly | Lubricate moving parts as per manufacturer’s instructions. | |
Filter Replacement | Monthly | Replace air and fluid filters to maintain optimal performance. | |
Component Calibration | Annually | Calibrate sensors and control systems for accuracy. |
4. Prioritizing Regular Maintenance: Sustaining Performance and Longevity
To ensure the longevity of your pipe bundling machines, a few maintenance tactics should be applied.
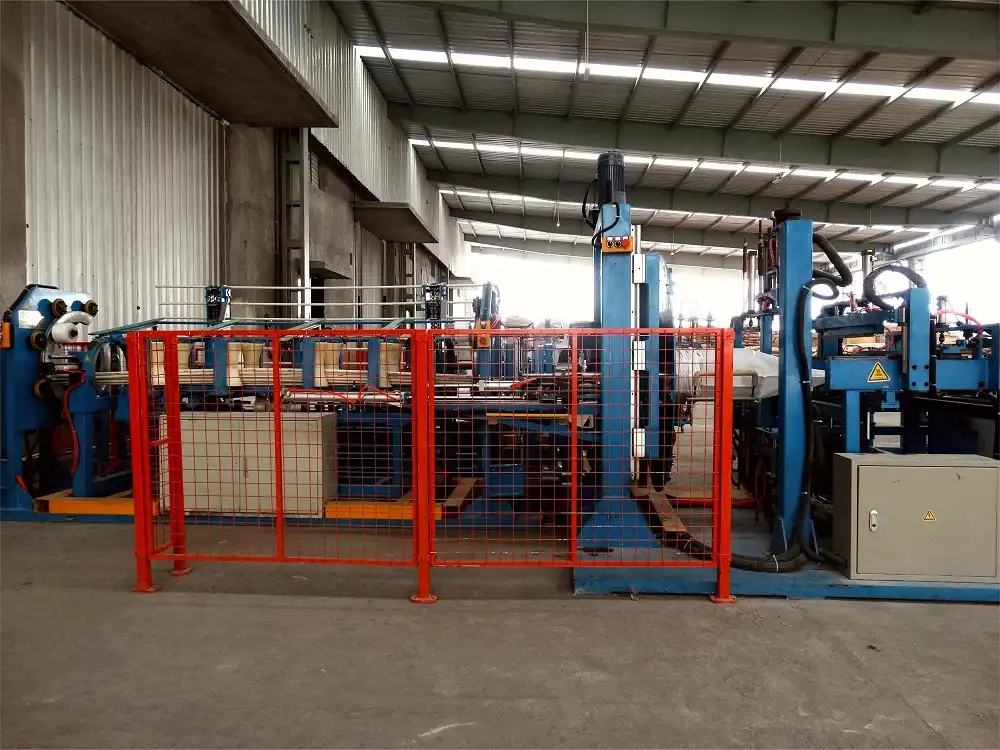
Regular maintenance enhances machine reliability and extends service life. Consistent maintenance, along with inspections, lubrication, and component replacement, reduce breakdowns. Prevent expensive repairs and optimize the machine’s performance, maintaining bagging efficiency and quality. Preventative and reactive measures help guarantee peak performance.
Adhering to a structured maintenance program is crucial for sustained performance. Preventative measures, including frequent mechanical and electrical component reviews, ensure proper working order. Routine inspections can identify wear and tear, preventing costly future problems. A regular cleaning schedule prevents buildup that affects performance, while scheduled firmware updates keep systems aligned and up-to-date.
Reactive maintenance addresses unexpected breakdowns, with a plan for quick part replacement and access to qualified technicians.
Preventative Maintenance
- Routine Inspections: These inspections can save a lot of costly future problems if they are performed frequently. There are a lot of wear and tear parts that may need replacing, and it is good to identify these parts before they cause a failure.
- Cleaning Schedule: The machine must be cleaned on a regular basis. This is more than just wiping it down. This involves making sure that any areas of buildup that might affect the overall performance of the machine is removed.
- Firmware Updates: Firmware updates can also be scheduled and programmed ahead of time, taking away a headache in the future. These updates may also have to coincide with existing systems, so it is good to get ahead of the curve.
Reactive Maintenance
There are some things that can’t be planned or helped. That is where reactive maintenance comes in. When parts break or systems fail unexpectedly, these parts have to be identified and replaced in an efficient manner. These plans include:
- Having a parts supplier. Having a supplier on standby that will send the part needed, is essential to getting back to work. It is also good to have multiple vendors.
- On hand parts inventory. Having wear and tear parts on site will save a great deal of time. These parts are known to fail, and if they are on site, they can be swapped in right away, with no wait.
- Qualified technicians. Having technicians on staff or on call ensures that your system will be maintained by someone who understands its complexities.
Preventative Maintenance Steps:
Here’s how to go about each step:
Preventative Maintenance | Details |
---|---|
Checking all parts | Checking all parts |
Replace when neccecary | Replace when neccecary |
Lubricating the parts | Lubricating the parts |
Overall, it is important to maintain these PVC bagging systems with both preventive and reactive measures. As long as everything is planned ahead of time and executed correctly, the downtime can be minimized and productivity can increase.
Conclusion
In conclusion, ensuring a seamless pipe bundling machine installation hinges on mechanical, electrical, and operational compatibility. Thorough assessments, strategic implementation, proactive maintenance, and effective troubleshooting are essential. A well-integrated machine not only optimizes production but also enhances the reliability and longevity of your bundling processes. By carefully considering and addressing these key aspects, you can unlock the full potential of your new equipment and achieve significant gains in efficiency and productivity within [Collection].