What Are the Common Issues with Pipe Bundling Machine Calibration?
Ensuring your pipe bundling machine operates at peak efficiency requires accurate calibration. Miscalibration leads to inconsistent bundles, wasted materials, and increased downtime. Identifying common calibration issues is crucial for smooth operations.
The most common issues involve inaccurate length measurements, inconsistent bundle sizes, misaligned strapping, and incorrect pipe counts. These problems lead to material waste, unstable bundles, and reduced production efficiency. Regular checks and precise adjustments are essential for optimal performance.
When a pipe bundling machine isn’t correctly calibrated, the consequences can ripple throughout your production line. Let’s delve into these issues and explore how to keep your operations running smoothly.
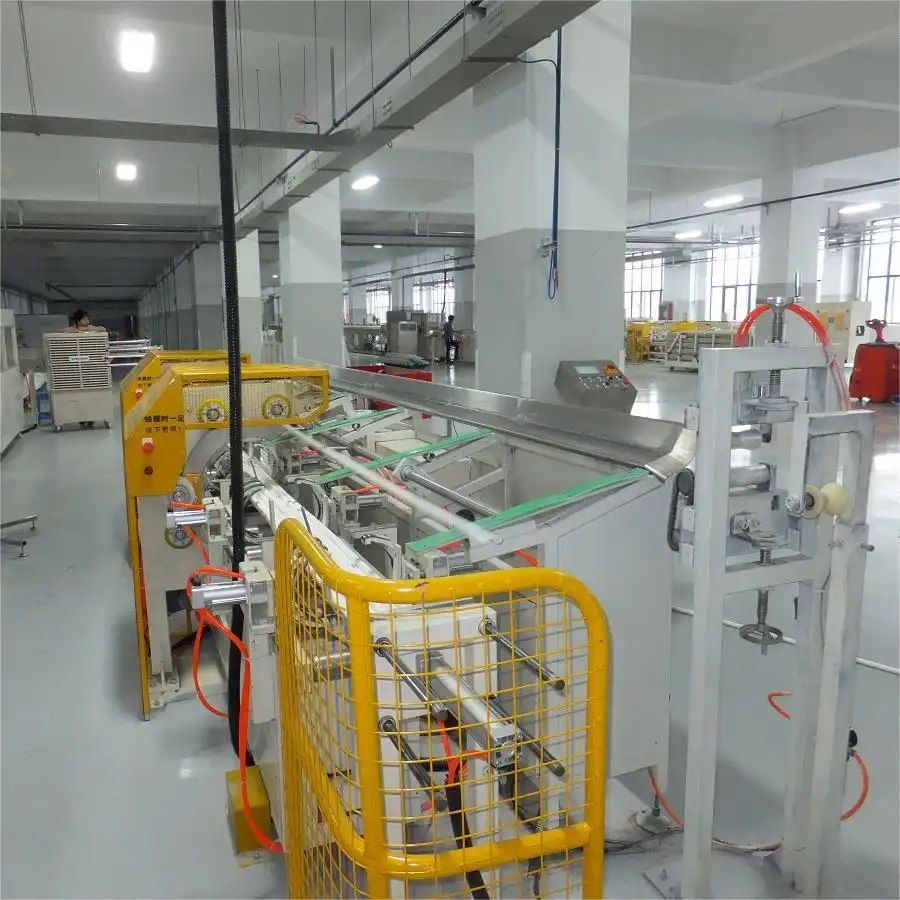
Inaccurate Length Measurements
Accurate length measurement is the bedrock of any pipe bundling operation. Inaccurate measurements result in bundles that don’t meet specifications, leading to unhappy customers and wasted materials.
Inaccurate length measurements stem from sensor misalignment, encoder malfunction, or incorrect calibration parameters. Addressing these issues through meticulous sensor alignment, encoder maintenance, and precise parameter settings is critical for consistent and accurate bundle lengths.
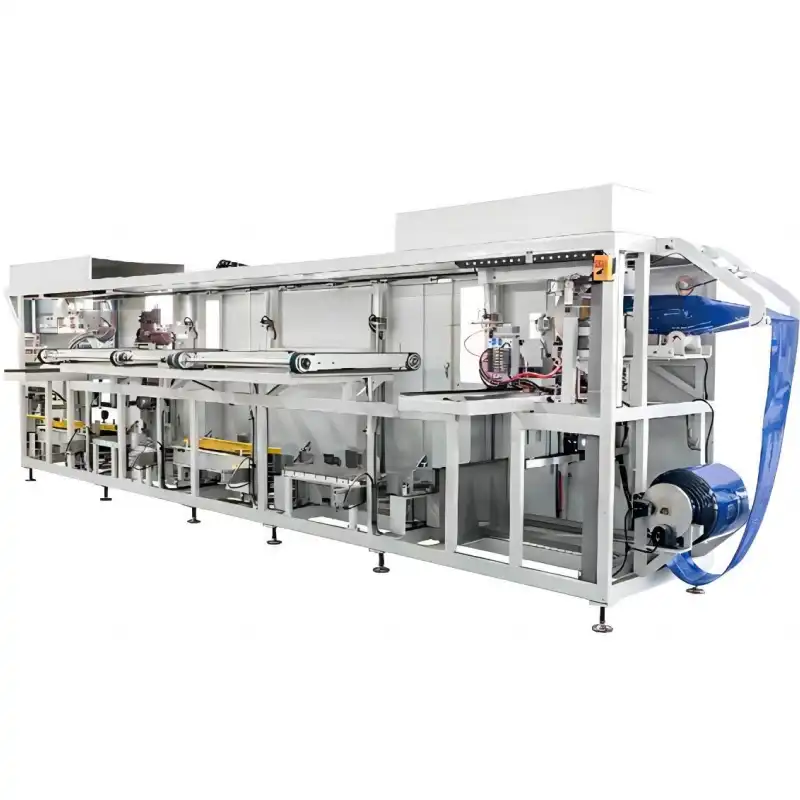
Achieving Precise Length Control: Sources of Error and Calibration Strategies
Achieving consistent and accurate pipe lengths requires a deep dive into the potential sources of error and the implementation of precise calibration techniques.
Analyzing Sources of Length Inaccuracy
Source of Inaccuracy | Description | Impact | Diagnostic Steps |
---|---|---|---|
Encoder Miscalibration | Rotary encoders provide inaccurate length readings due to drift, damage, or improper initial setup. | Inconsistent pipe lengths; under or over length bundles. | Use a calibrated measuring device to verify encoder accuracy. Check encoder wiring and connections. Recalibrate using manufacturer guidelines. |
Sensor Misalignment | Proximity or laser sensors are misaligned, leading to premature or delayed pipe detection. | Inaccurate length measurements; inconsistent cut-off points. | Visually inspect sensor alignment. Use a precision level to ensure correct positioning. Adjust sensor sensitivity. |
Mechanical Slippage | Slippage in belts, rollers, or gears can cause deviations between the encoder reading and actual length. | Length variations; inconsistent bundle dimensions. | Inspect belts for wear and tension. Check rollers and gears for slippage and proper engagement. |
Control System Errors | Programming errors, incorrect parameters, or communication issues can affect length calculation. | Inaccurate length control; unpredictable cut-off points. | Review control system settings. Verify program logic and data transmission. |
Implementing Precision Calibration and Control
Accurate length control hinges on precise calibration procedures and robust control mechanisms.
- Encoder Calibration: Use certified measuring tools to calibrate encoders regularly, adhering to the manufacturer’s instructions with precision. Account for the full length range utilized in production.
- Sensor Alignment: Use laser alignment tools to ensure sensors are accurately positioned. Verify sensor readings against known pipe lengths.
- Mechanical System Checks: Regularly inspect and maintain belts, rollers, and gears. Replace worn components and ensure proper tension and engagement.
- Control System Optimization: Implement a closed-loop control system that monitors length feedback and adjusts cutting parameters in real-time.
The Critical Role of Regular Maintenance
Beyond calibration, regular maintenance plays a vital role in ensuring accurate length measurements. Neglecting maintenance can lead to a cascade of issues that compromise the precision of your pipe bundling machine.
- Belt Tension and Condition: Belts are a critical link in the length measurement process. Over time, they can stretch, crack, or become contaminated with debris, leading to slippage and inaccurate readings. Regularly inspect belt tension and condition, and replace worn belts promptly.
- Roller and Gear Maintenance: Rollers and gears are responsible for transferring motion and ensuring accurate length measurements. Over time, they can wear down, develop play, or become misaligned, leading to inaccuracies. Regularly inspect rollers and gears for wear, alignment, and proper lubrication.
- Sensor Cleaning and Inspection: Sensors are the eyes and ears of the length measurement system. Over time, they can become dirty, misaligned, or damaged, leading to inaccurate readings. Regularly clean sensors and inspect them for damage or misalignment.
By meticulously addressing potential sources of length inaccuracy and implementing precision calibration strategies, you can significantly improve length control consistency in your pipe bundling machine, reducing waste, ensuring customer satisfaction, and optimizing production efficiency.
Inconsistent Bundle Sizes
Maintaining consistent bundle sizes is vital for efficient handling, storage, and transportation. Variations in bundle dimensions can disrupt downstream processes and negatively impact customer satisfaction.
Inconsistent bundle sizes are due to issues with pipe feeding mechanisms, clamping systems, or the control logic governing bundle formation. Proper calibration involves synchronizing feeding speeds, calibrating clamp pressure, and fine-tuning control parameters.
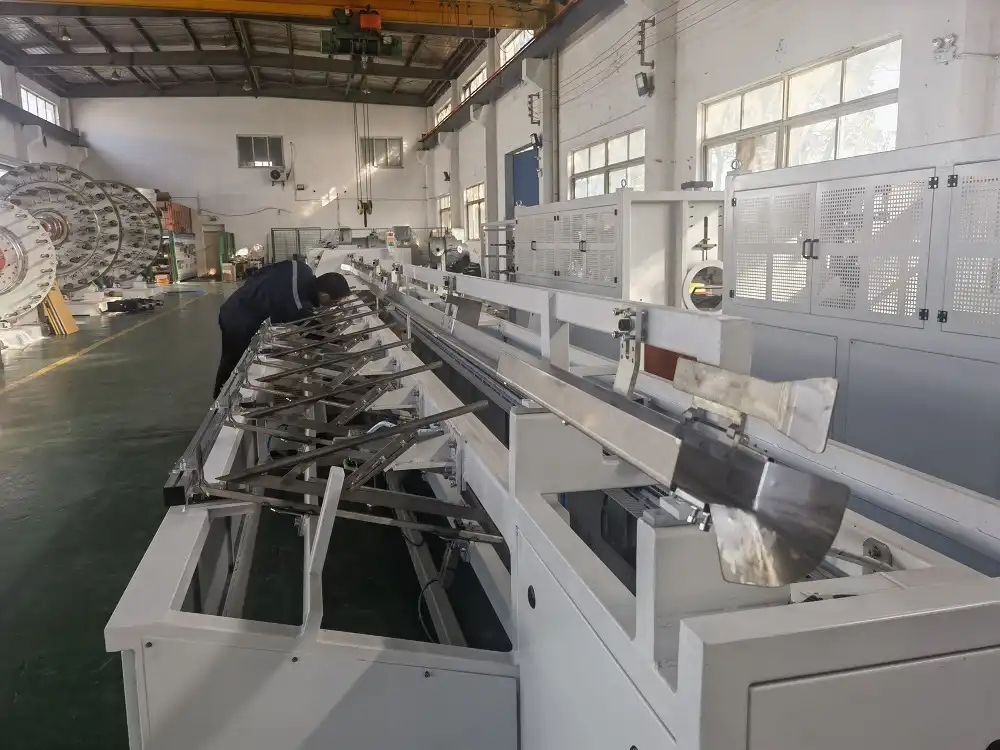
Technical Examination: Fine-Tuning Bundle Formation
To address bundle size inconsistencies, a meticulous examination of the machine’s pipe feeding, clamping, and control systems is paramount.
Pipe Feeding Mechanism Synchronization
Ensuring smooth and synchronized pipe feeding is essential for consistent bundle sizes.
- Feeding Speed Calibration: Calibrate the speed of the feeding mechanism to ensure that pipes are delivered at a consistent rate. Variations in feeding speed can lead to inconsistent bundle sizes, especially when dealing with different pipe diameters.
- Synchronization with Clamping System: Synchronize the feeding mechanism with the clamping system to ensure that pipes are delivered precisely when the clamp is ready to receive them. Poor synchronization can result in misaligned pipes and inconsistent bundle dimensions.
Clamping System Calibration
The clamping system is responsible for securing the pipes during bundle formation.
- Pressure Calibration: Calibrate the pressure applied by the clamping system to ensure that pipes are held securely without being damaged. Excessive pressure can deform the pipes, while insufficient pressure can lead to slippage and inconsistent bundle sizes.
- Alignment and Symmetry: Ensure that the clamping system is properly aligned and symmetrical. Misalignment can result in uneven pressure distribution and distorted bundles.
- Regular Maintenance: Regularly inspect the clamping system for wear and tear, and replace any worn components. Worn clamping pads or cylinders can compromise the clamping force and lead to inconsistent bundle sizes.
Control System Parameter Optimization
The control system governs the entire bundle formation process.
- Pipe Counting Algorithm: Choose a counting algorithm that accurately counts the number of pipes being delivered to the clamping system. Inaccurate counting can result in bundles that are underfilled or overfilled.
- Bundle Size Settings: Carefully configure the bundle size settings in the control system to match the desired bundle dimensions. Incorrect settings can result in bundles that are too large or too small.
- Feedback Mechanisms: Implement feedback mechanisms that monitor the bundle size and adjust the feeding and clamping systems accordingly. Feedback mechanisms can help to compensate for variations in pipe diameter and other factors that can affect bundle size.
By meticulously addressing these technical aspects and implementing precise calibration procedures, you can ensure consistent bundle sizes, improving the efficiency and quality of your pipe packaging machines operations.
Misaligned Strapping
Properly aligned strapping is critical for securing bundles and preventing damage during handling and transportation. Misaligned strapping can lead to unstable bundles, increased risk of pipe damage, and potential safety hazards.
Misaligned strapping occurs due to incorrect strapping head positioning, sensor malfunction, or inconsistent bundle presentation. Calibration involves precise adjustment of the strapping head, sensor calibration, and ensuring uniform bundle positioning.
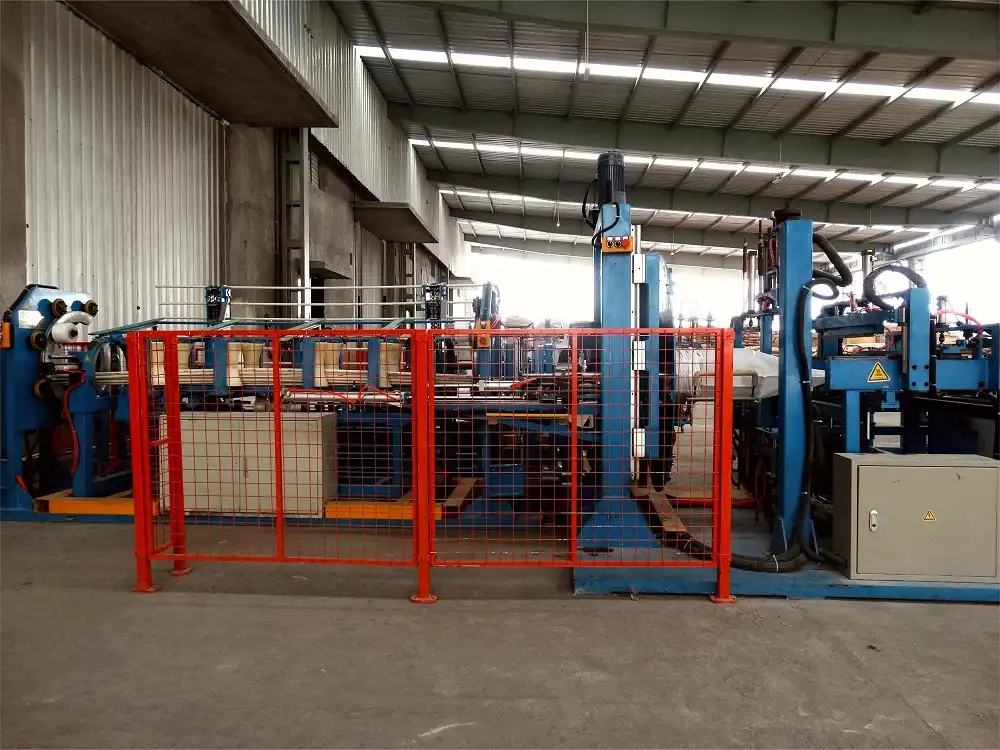
Troubleshooting Strapping Alignment: A Comprehensive Guide
Achieving consistently aligned strapping requires a multifaceted approach.
Ensuring Accurate Strapping Head Positioning
The strapping head is the heart of the strapping system. Its accurate positioning is paramount for achieving consistent strap placement.
- Vertical and Horizontal Alignment: Use laser alignment tools to ensure that the strapping head is perfectly aligned both vertically and horizontally. Misalignment can result in straps that are placed too high, too low, or off-center.
- Distance from Bundle: Maintain the correct distance between the strapping head and the bundle. Too much distance can result in straps that are loose or misaligned, while too little distance can damage the pipes.
- Strapping Head Stability: Ensure that the strapping head is securely mounted and free from vibration. Vibration can cause inconsistent strap placement.
Calibrating Sensors for Accurate Strap Placement
Sensors are used to detect the position of the bundle and trigger the strapping process.
- Sensor Type Selection: Choose sensors that are appropriate for the size, shape, and material of the pipes being bundled. Common sensor types include photoelectric sensors, proximity sensors, and laser sensors.
- Sensor Placement: Position sensors strategically to ensure reliable detection of the bundle. Consider factors such as pipe spacing, orientation, and potential for interference.
- Sensor Calibration: Calibrate sensors regularly according to the manufacturer’s instructions. Use reference bundles of known dimensions to verify sensor accuracy.
- Sensor Maintenance: Clean sensors regularly to remove dust, dirt, and debris that can interfere with detection accuracy. Inspect sensor wiring and connections for damage or looseness.
Ensuring Consistent Bundle Presentation
Consistent bundle presentation is essential for achieving consistently aligned strapping.
- Bundle Alignment: Ensure that bundles are aligned properly as they enter the strapping station. Misaligned bundles can result in straps that are placed incorrectly.
- Bundle Shape: Ensure that bundles are consistently shaped. Irregularly shaped bundles can make it difficult for the strapping head to apply the straps accurately.
- Bundle Density: Ensure that bundles are consistently dense. Loose bundles can shift during the strapping process, resulting in straps that are misaligned.
By implementing these strategies, you can achieve and maintain accurate strap alignment, ensuring bundle integrity and preventing damage during handling and transportation.
Incorrect Counting
Ensuring an accurate count of pipes per bundle is crucial for inventory management and customer satisfaction. Errors in pipe counting can lead to discrepancies in inventory, potential customer disputes, and ultimately, reduced profitability.
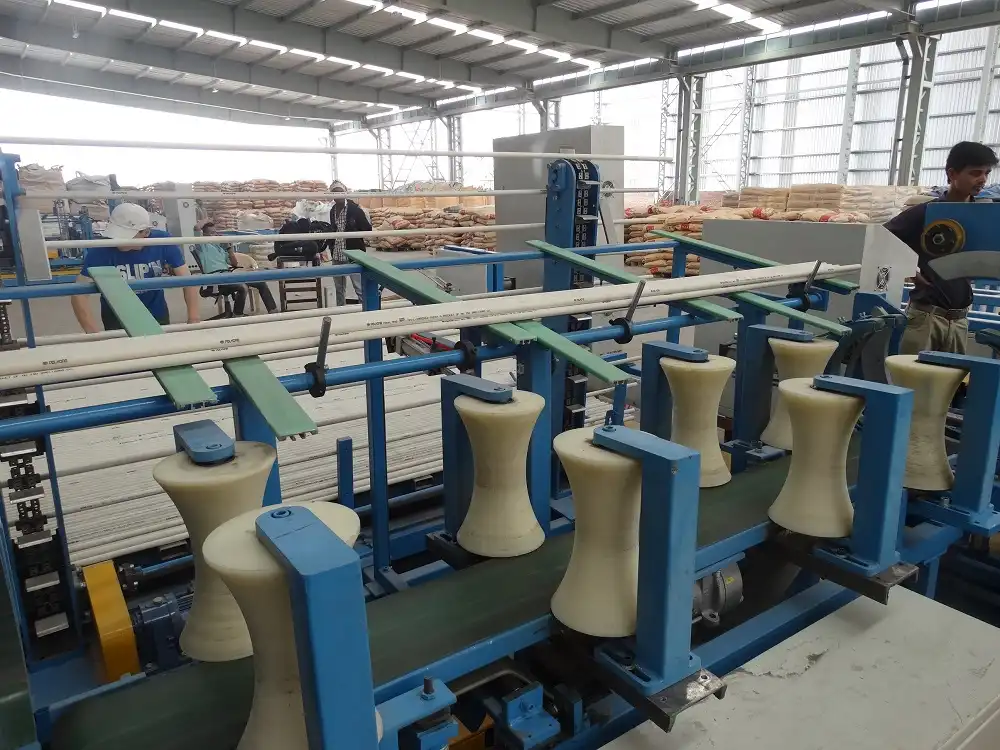
Incorrect counting arises from sensor failures, miscalibration of the counting system, or inconsistencies in pipe feeding. Solving this requires meticulous sensor maintenance, system recalibration, and ensuring a consistent flow of pipes through the counting zone.
Accurate counting is essential for inventory management and customer satisfaction. Miscalibration of the counting mechanism can lead to bags containing incorrect quantities of PVC pipes, causing discrepancies in inventory and potential customer disputes. Correct counting procedures require a multifaceted approach, focusing on sensor reliability, control system calibration, and process optimization.
A Multi-Faceted Approach to Mastering Counting Precision
Conclusion
Proper calibration of a pipe bundling machine is the difference between smooth operations and a costly headache. Addressing issues of length, size, strap alignment and count ensures consistency and quality. Investing in regular maintenance and properly trained staff maximizes efficiency and keeps your production line running smoothly.