What Are the Challenges of Maintaining Steel Wire Coiling Machines in Harsh Environments?
Maintaining steel wire coiling machines in harsh environments presents unique challenges. These machines, crucial for various industries, face constant wear and tear. Understanding these challenges is essential for ensuring operational efficiency and longevity.
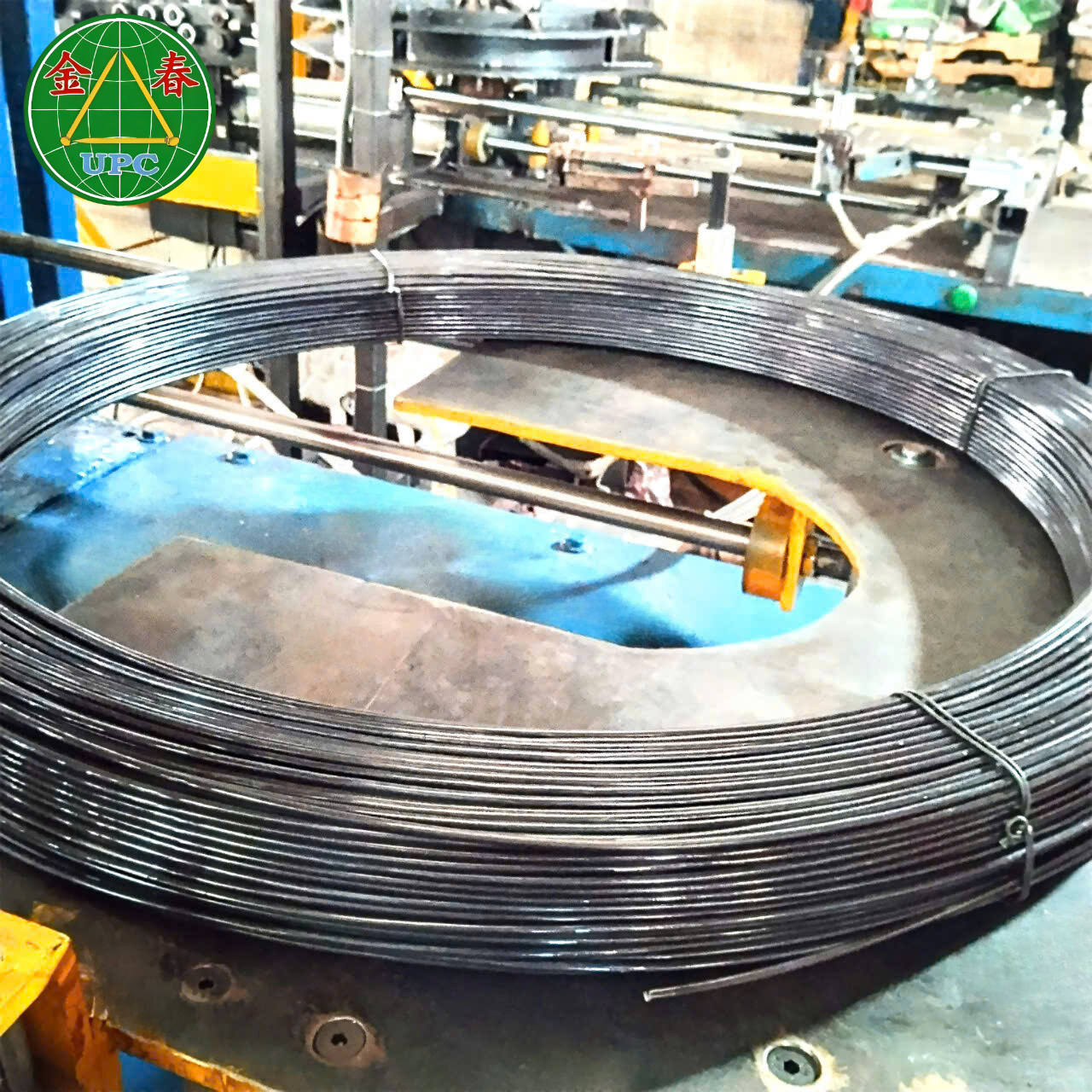
Maintaining steel wire coiling machines in harsh environments involves battling corrosion, abrasion, and extreme temperatures. These conditions demand robust materials, rigorous maintenance schedules, and innovative protective measures. Overcoming these challenges ensures reliable performance and extends the lifespan of the machinery.
Steel wire coiling machines operating in demanding settings require diligent care. Let’s delve into the specific challenges and explore effective maintenance strategies that safeguard your investment and ensure uninterrupted production.
1. Understanding Environmental Impact on Steel Wire Coiling Machines
Steel wire coiling machines are often deployed in challenging environments. These conditions can drastically impact their performance and lifespan. Recognizing the specific environmental factors is the first step in effective maintenance.
Harsh environments significantly challenge steel wire coiling machines, leading to corrosion, abrasion, and material fatigue. Coastal regions cause saltwater corrosion. Extreme temperatures affect material properties. Abrasive particles accelerate wear. Regular inspection, specialized coatings, and environmental control measures are essential to mitigate these detrimental effects.
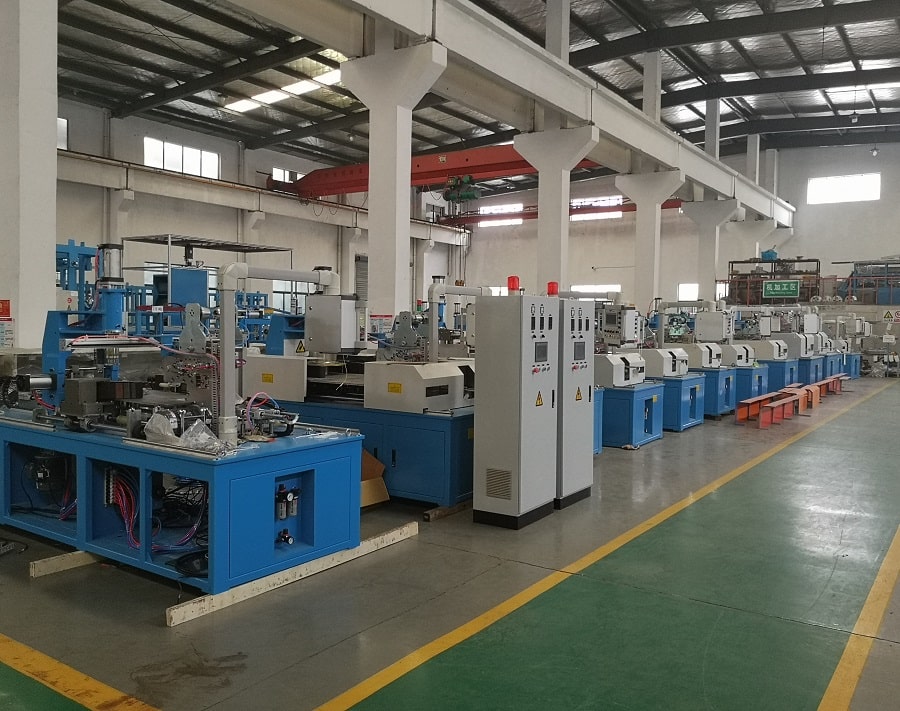
Mitigating Corrosion, Temperature Extremes, and Abrasive Wear
The key to maintaining steel wire coiling machines lies in understanding and addressing the specific environmental threats. By implementing proactive strategies, you can minimize downtime, reduce repair costs, and maximize the operational life of your machinery.
Corrosion Control
Corrosion is a major concern, especially in coastal or humid environments. Steel is vulnerable to oxidation, which weakens the material and can lead to structural failure.
- Protective Coatings: Applying anti-corrosive coatings is essential. Options include galvanization, epoxy coatings, and specialized paints.
- Material Selection: Using corrosion-resistant alloys, such as stainless steel, can significantly extend the lifespan of machine components.
- Regular Cleaning: Removing salt, moisture, and other corrosive substances through regular cleaning is crucial.
- Dehumidification: Controlling humidity in enclosed spaces can help prevent corrosion.
Temperature Extremes
Extreme temperatures, both high and low, can affect the mechanical properties of steel. High temperatures can reduce tensile strength, while low temperatures can make the material brittle.
- Material Selection: Choosing steels with high-temperature or low-temperature resistance is vital.
- Lubrication: Using lubricants that maintain their viscosity and properties across a wide temperature range is essential.
- Thermal Insulation: Insulating critical components can help maintain a stable operating temperature.
Abrasive Wear
Abrasive wear occurs when hard particles rub against the machine’s surface, gradually eroding the material. This is common in environments with dust, sand, or other abrasive materials.
- Sealing: Sealing critical components can prevent abrasive particles from entering the machinery.
- Filtration: Implementing air filtration systems can reduce the concentration of abrasive particles in the environment.
- Hardfacing: Applying hardfacing materials to wear-prone surfaces can increase their resistance to abrasion.
- Regular Cleaning: Removing abrasive particles through regular cleaning is essential.
To illustrate the impact of different environmental factors, consider the following table:
Environmental Factor | Impact on Machine | Mitigation Strategy |
---|---|---|
Saltwater | Rapid corrosion, structural weakening | Galvanization, stainless steel components, regular washdowns |
High Temperature | Reduced tensile strength, lubricant breakdown | High-temperature alloys, specialized lubricants, cooling systems |
Abrasive Dust/Sand | Surface wear, component erosion | Sealing, filtration, hardfacing, frequent cleaning |
Extreme Cold | Embrittlement, lubricant thickening | Low-temperature alloys, specialized lubricants, heating elements |
This table highlights the importance of tailored maintenance strategies based on the specific environmental conditions. Without proper care, Steel wire coiling machine maintenance can lead to unexpected downtimes and costly repairs.
2. Lubrication and Material Selection for Optimal Performance
The correct lubrication and choice of materials are paramount. Selecting the right lubricants and materials is a key factor in minimizing wear and tear.
Lubrication and material selection are crucial for maintaining steel wire coiling machines. Proper lubrication reduces friction and wear, extending component life. Selecting durable materials resistant to corrosion and abrasion ensures machine longevity and reliability in harsh conditions.
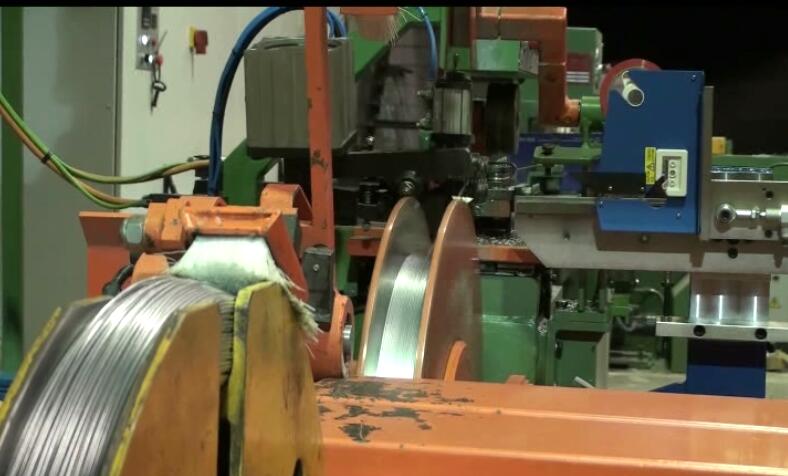
Advanced Lubrication Techniques and Durable Material Options
Beyond environmental protection, optimal durability hinges on the correct lubrication practices and smart material choices. Each element complements the other, resulting in enhanced machinery reliability.
Lubrication Best Practices
Lubrication is not merely applying grease; it’s a science.
- Type Selection: Selecting the right lubricant is critical. Consider synthetic lubricants, which offer superior performance in extreme temperatures and under heavy loads.
- Application Method: Implement automated lubrication systems to ensure consistent and precise application.
- Frequency: Establish a lubrication schedule based on the manufacturer’s recommendations and the severity of the operating conditions.
- Monitoring: Regularly monitor lubricant levels and condition to detect potential problems early.
Material Innovation
- High-Strength Alloys: Explore high-strength, low-alloy steels that offer enhanced durability and resistance to wear.
- Composite Materials: Consider using composite materials for non-structural components to reduce weight and improve corrosion resistance.
- Surface Treatments: Apply surface treatments, such as nitriding or chrome plating, to improve wear resistance and reduce friction.
Modern coiling machines require modern material and lubrication science.
3. Scheduled Inspections and Preventative Maintenance
Implementing a well-structured inspection and maintenance plan is essential. Regular inspections can identify potential problems.
Scheduled inspections and preventative maintenance are vital for ensuring the reliable operation of steel wire coiling machines. Regular inspections identify wear, corrosion, and damage early. Timely maintenance, including lubrication, component replacement, and adjustments, minimizes downtime and extends machine lifespan, ensuring consistent performance.

Maximizing Uptime Through Proactive Strategies
To maintain optimal performance, prioritize detailed inspections and preventative actions. These strategies are fundamental to avoiding malfunctions and securing maximum uptime.
Inspection Protocols
- Visual Inspections: Conduct regular visual inspections to identify signs of wear, corrosion, or damage.
- NDT Testing: Use non-destructive testing (NDT) methods, such as ultrasonic testing and radiography, to detect hidden flaws.
- Performance Monitoring: Monitor key performance indicators (KPIs), such as motor current, vibration levels, and temperature, to identify potential problems.
Preventative Actions
Maintenance Task | Frequency | Description |
---|---|---|
Lubrication | Daily | Apply lubricant to all moving parts according to manufacturer’s recommendations. |
Cleaning | Weekly | Remove dirt, debris, and contaminants from the machine’s surface and internal components. |
Component Check | Monthly | Inspect critical components, such as bearings, gears, and belts, for wear and damage. |
Alignment | Quarterly | Check and adjust the alignment of machine components to ensure smooth operation. |
Calibration | Annually | Calibrate sensors and control systems to maintain accuracy and reliability. |
By adhering to this strategy, you can reduce the potential for significant failures, ensuring constant and reliable operation.
4. Training and Expertise
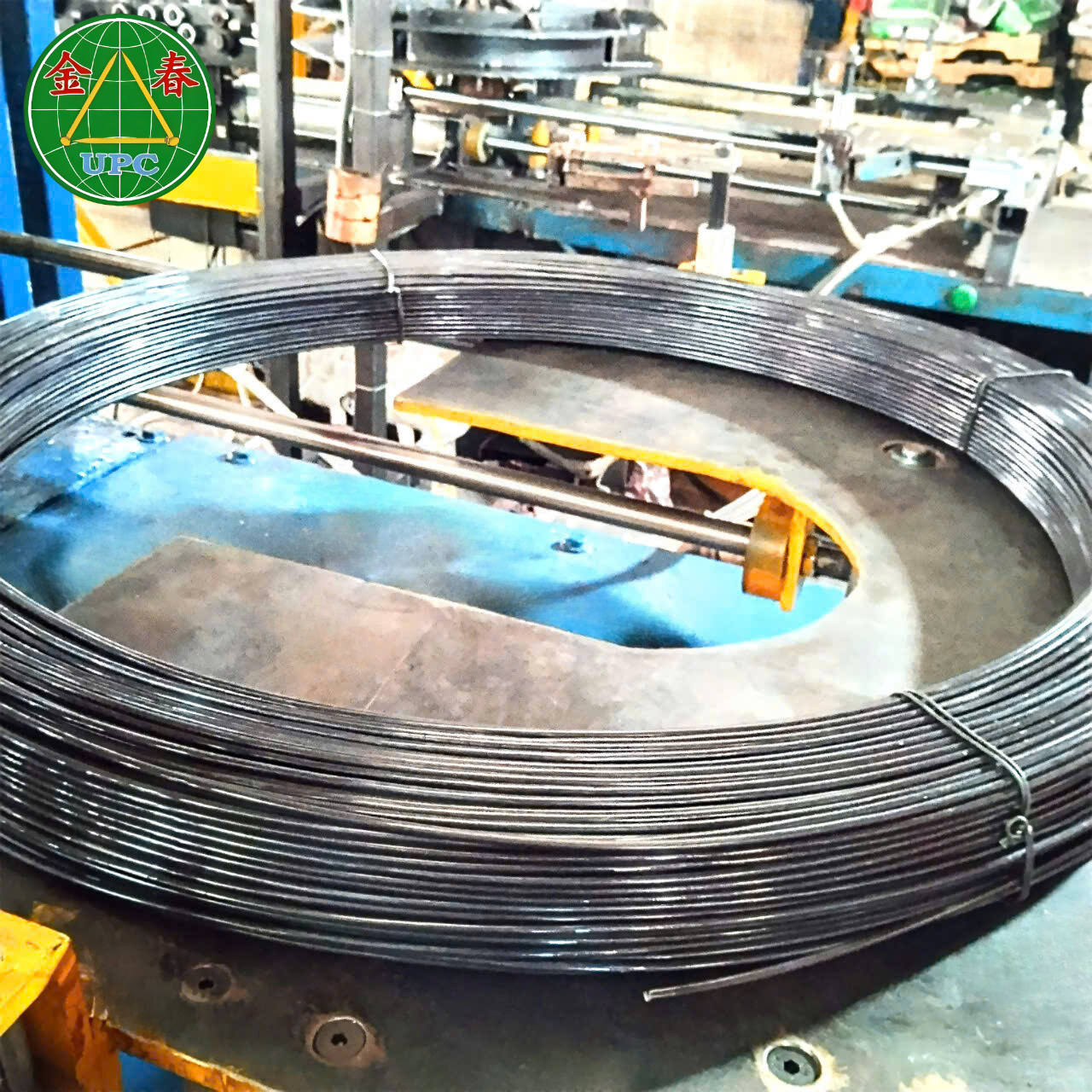
Investing in proper training and expertise is essential. Skilled technicians can identify problems early and perform maintenance.
Proper training and expertise are critical for steel wire coiling machine maintenance. Trained technicians can diagnose issues accurately, perform effective repairs, and implement preventative measures. Investing in ongoing training ensures the workforce is equipped to handle the complexities of maintaining machinery in demanding environments, minimizing downtime and maximizing equipment lifespan.
The value of a skilled and trained maintenance crew cannot be overstated.
Competent technicians are essential in maintaining and increasing the durability of equipment. Their skills ensure the correct operation and timely repairs that are vital for the machines’ life cycle.
Conclusion
Maintaining steel wire coiling machines in harsh environments requires a multifaceted approach. By understanding the environmental impact, selecting appropriate materials and lubricants, implementing scheduled inspections and preventative maintenance, and investing in training and expertise, you can significantly extend the lifespan of your machinery and ensure reliable operation. Embrace these strategies to overcome the challenges and maximize your return on investment. Consistent focus on these key areas guarantees that your equipment can withstand the rigors of any tough environment.