What Are the Challenges of Maintaining Pipe Bundling Machines in Harsh Environments?
Maintaining pipe bundling machines in harsh environments presents numerous difficulties. These range from extreme temperatures and abrasive materials to remote locations and limited access to skilled technicians, impacting operational efficiency.
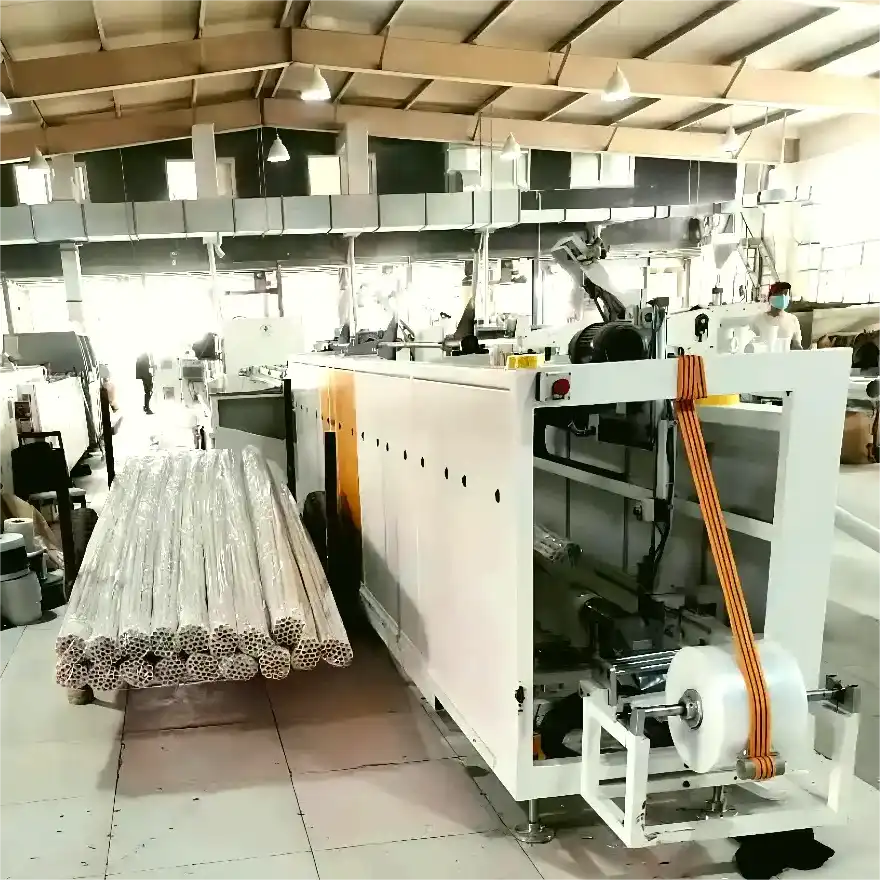
Maintaining pipe bundling machines in harsh environments poses significant challenges. Exposure to extreme temperatures, dust, and corrosive substances accelerates wear and tear. Remote locations complicate logistics, limit access to skilled technicians, and increase downtime. Proactive maintenance strategies and robust equipment are critical for reliable operation.
Transitioning from a general understanding of these issues to concrete solutions requires a detailed examination of material selection, maintenance protocols, and strategies for environmental control, which we’ll explore in depth.
1. Logistical Hurdles in Remote Maintenance
Maintaining pipe bundling machines in remote locations presents unique logistical challenges that can impact operational efficiency and increase downtime. This requires careful planning and strategic resource allocation.
Maintaining pipe bundling machines in remote industrial sites is challenging due to logistical constraints. The scarcity of skilled technicians, coupled with the difficulty of transporting specialized tools and parts, leads to extended downtime. Harsh environmental conditions further exacerbate maintenance issues, increasing the risk of corrosion and component failure. To mitigate these challenges, proactive planning is essential.
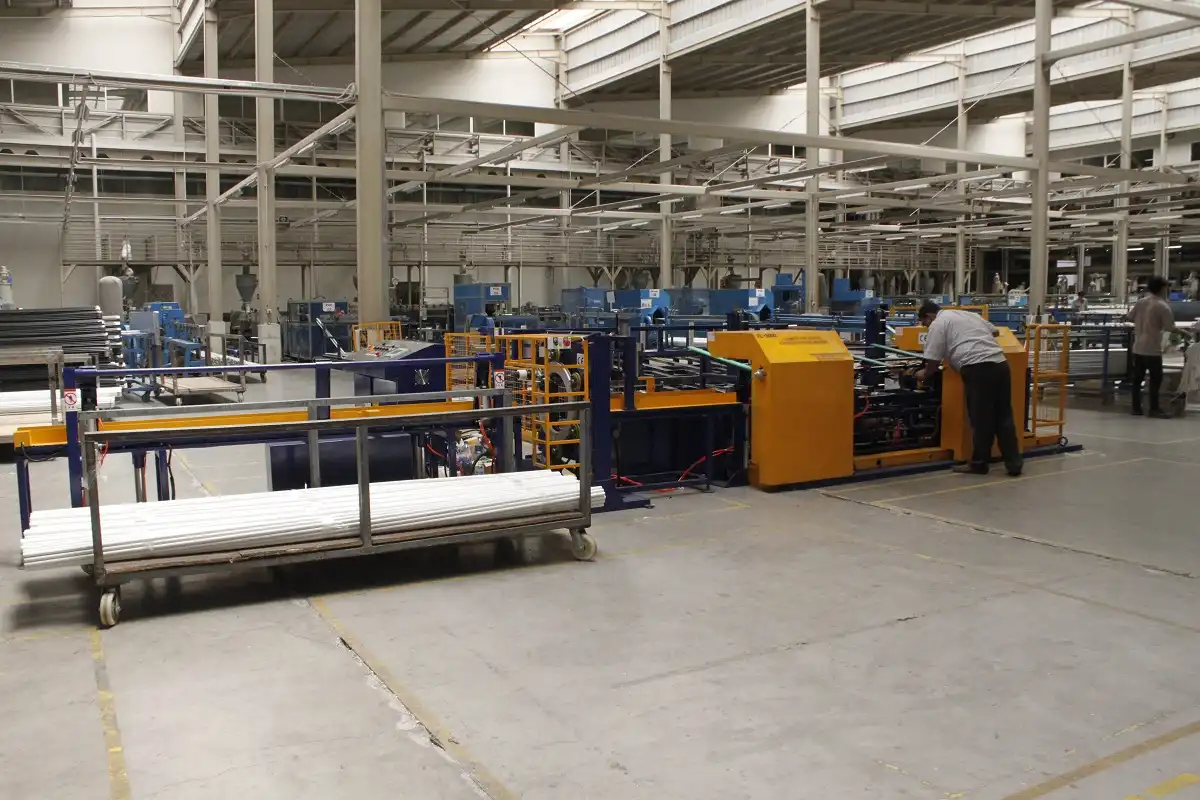
Mitigating Downtime Through Strategic Planning
The key to overcoming these logistical nightmares lies in meticulous planning and proactive strategies. Consider the following aspects:
The Criticality of Spare Parts Management
One of the biggest challenges is ensuring the availability of spare parts. Remote locations often mean long lead times for deliveries, which can bring production to a standstill.
Maintaining an optimal inventory of critical spare parts on-site is crucial. The challenge is to balance the cost of holding inventory against the potential cost of downtime. This requires a detailed analysis of failure rates, lead times, and the criticality of each part. For highly critical components with long lead times, consider strategic stockpiling. Develop strong relationships with suppliers who can provide expedited delivery services.
The Technician Deployment Challenge
Getting skilled technicians to remote sites can be a logistical nightmare. Factors such as travel time, accommodation, and local regulations can all add to the complexity and cost.
Invest in remote diagnostic tools that allow technicians to troubleshoot problems from a central location. This can reduce the need for on-site visits and speed up the repair process. Train local personnel to perform basic maintenance tasks. This can reduce the reliance on external technicians and ensure that minor issues can be resolved quickly. Establish contracts with local service providers who can provide on-site support on short notice.
Overcoming Environmental Challenges
Remote industrial sites are often located in harsh environments that can accelerate the wear and tear on equipment.
Implement measures to protect equipment from the elements. This can include building shelters, using corrosion-resistant materials, and implementing regular cleaning and maintenance programs. Monitor environmental conditions and adjust maintenance schedules accordingly. Select equipment that is specifically designed to withstand the harsh conditions of the remote site.
To better illustrate the impact of these strategies, consider the following scenario:
Strategy | Impact on Downtime | Cost of Implementation |
---|---|---|
On-site spare parts | -50% | $50,000 |
Remote diagnostics | -30% | $20,000 |
Local technician training | -20% | $10,000 |
This table highlights the potential benefits of implementing a comprehensive maintenance strategy that addresses the unique logistical challenges of remote industrial sites. Prioritize strategies that offer the most significant reduction in downtime for the investment. Remote diagnostics coupled with on-site spare parts can create a robust system.
2. Skill Set and Training Gaps
One significant hurdle is the availability of skilled technicians who can effectively diagnose and repair complex pipe packaging machines in remote areas. Proper training is essential to bridge this gap.
Finding and retaining qualified technicians in remote industrial settings is difficult. The lack of local talent pools and the high cost of bringing in external experts contribute to skill shortages. Investing in training programs and offering competitive compensation packages are essential for bridging this gap. Effective training improves machine uptime.

Addressing the Expertise Deficit: A Multi-Faceted Approach
The shortage of skilled maintenance personnel in remote areas isn’t merely an inconvenience; it’s a critical vulnerability that demands immediate and comprehensive attention. To effectively bridge the expertise deficit, organizations must embrace a multi-faceted strategy encompassing targeted recruitment, comprehensive training, and innovative knowledge transfer mechanisms.
Enhancing Local Workforce Skills
The most sustainable solution lies in cultivating local talent. This involves partnering with vocational schools and technical colleges to develop specialized training programs tailored to the specific needs of pipe bundling machines. These programs should cover:
- Fundamentals of mechanical and electrical engineering: Equipping trainees with a solid foundation in the underlying principles of machine operation and maintenance.
- Hydraulics and pneumatics: Providing in-depth knowledge of the systems that power and control pipe bundling machines.
- Programmable logic controllers (PLCs): Training technicians to diagnose and troubleshoot PLC-controlled systems.
- Machine-specific training: Offering hands-on training on the specific models of pipe bundling machines used at the remote site.
Leveraging Technology for Remote Support
Remote diagnostics and virtual assistance are transforming the way maintenance is performed in remote locations. By leveraging technologies such as:
- Augmented reality (AR): Technicians can use AR-enabled devices to overlay digital information onto the physical machine, providing step-by-step guidance for repairs.
- Video conferencing: Remote experts can provide real-time assistance to on-site technicians, guiding them through complex procedures.
- IoT-enabled sensors: Sensors can monitor machine performance and alert technicians to potential problems before they cause downtime.
Knowledge Management and Best Practices
Creating a centralized knowledge repository that captures best practices, troubleshooting guides, and maintenance procedures is essential for ensuring consistent and effective maintenance across remote sites. This repository should be:
- Easily accessible: Technicians should be able to quickly find the information they need, regardless of their location.
- Regularly updated: The repository should be updated with new information as it becomes available.
- User-friendly: The repository should be designed to be easy to use, even for technicians with limited computer skills.
3. Environmental Factors and Equipment Durability
Harsh conditions significantly impact the performance and lifespan of pipe bundling machines. Addressing these challenges requires robust equipment and preventative maintenance.
Extreme temperatures, dust, humidity, and corrosive elements can accelerate wear and tear on equipment, leading to more frequent breakdowns. Selecting machines designed for harsh environments and implementing robust preventive maintenance programs are crucial for mitigating these challenges. Consider the environment when developing a maintenance schedule.
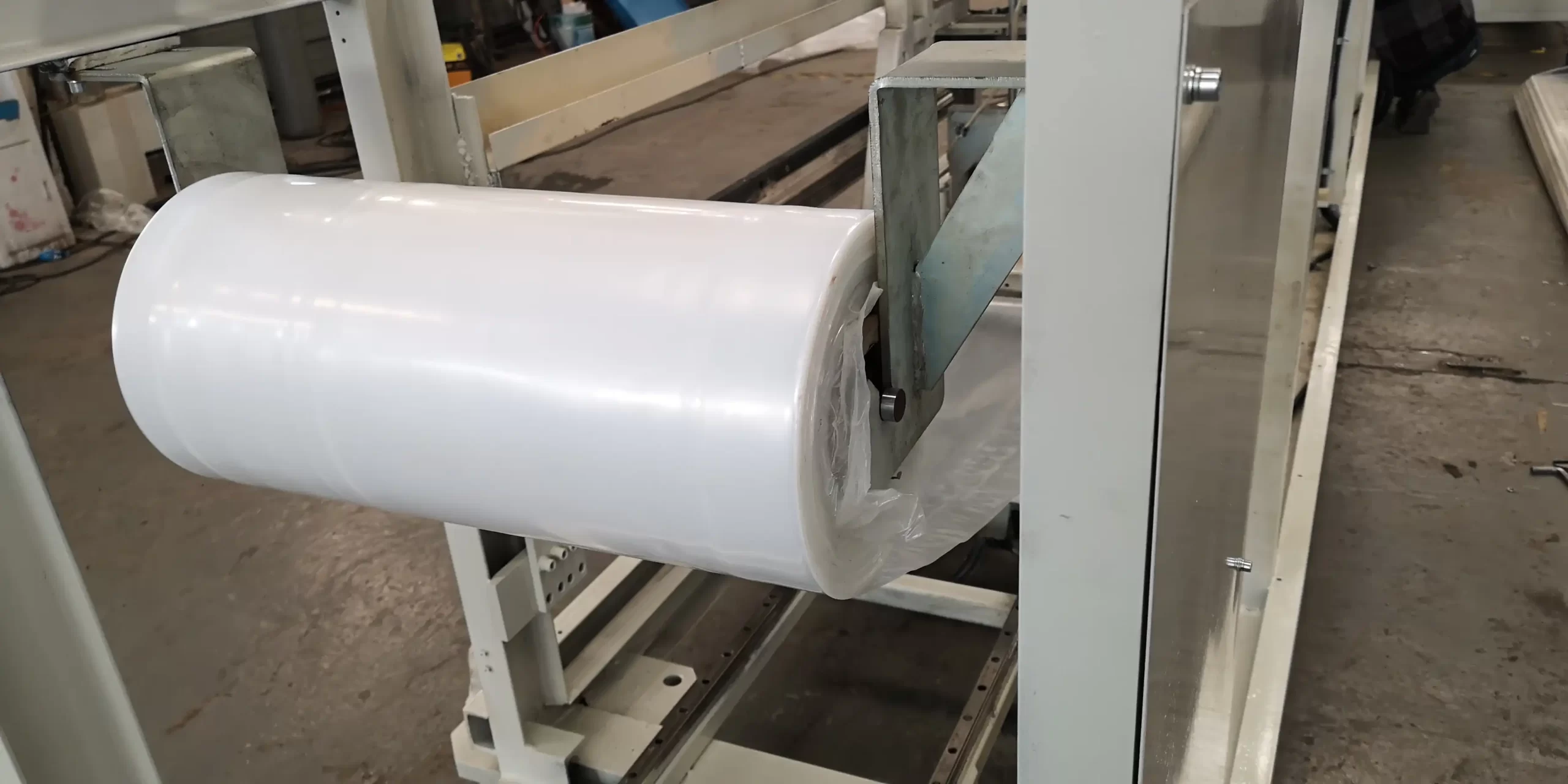
Fortifying Equipment Resilience: Counteracting Environmental Degradation
The environmental factors prevalent in remote industrial settings pose a formidable threat to the longevity and operational efficiency of pipe bundling machines. To effectively combat these challenges, a proactive and comprehensive approach is required, focusing on equipment selection, protective measures, and advanced maintenance strategies.
Robust Equipment Selection
Choosing equipment specifically engineered to withstand the rigors of remote industrial environments is paramount. This involves:
- Material Selection: Opting for machines constructed with corrosion-resistant materials such as stainless steel or specialized alloys.
- Sealed Components: Prioritizing equipment with sealed enclosures to prevent the ingress of dust, moisture, and other contaminants.
- Temperature Tolerance: Selecting machines capable of operating within the extreme temperature ranges typical of the remote site.
Implementing Protective Measures
In addition to selecting robust equipment, implementing protective measures is crucial for shielding machines from environmental damage.
- Protective Enclosures: Constructing shelters or enclosures to shield machines from direct exposure to sunlight, rain, and wind.
- Filtration Systems: Installing high-efficiency filtration systems to remove dust and other airborne particles from the operating environment.
- Corrosion Inhibitors: Applying corrosion inhibitors to metal surfaces to prevent rust and degradation.
Proactive Maintenance Strategies
A well-defined preventive maintenance program is essential for detecting and addressing potential problems before they lead to costly breakdowns.
- Regular Inspections: Conducting frequent inspections to identify signs of wear, corrosion, or damage.
- Lubrication: Implementing a rigorous lubrication schedule to ensure that all moving parts are properly lubricated.
- Cleaning: Regularly cleaning machines to remove dust, dirt, and other contaminants.
To illustrate the effectiveness of these strategies, consider the following table:
Environmental Factor | Mitigation Strategy | Expected Impact on Machine Lifespan |
---|---|---|
Extreme Temperatures | Temperature-resistant components | Increased lifespan by 25% |
Dust & Debris | Sealed enclosures & filtration | Reduced downtime by 40% |
Corrosion | Corrosion-resistant materials | Reduced maintenance costs by 30% |
4. Communication and Connectivity Issues
Reliable communication is vital for coordinating maintenance activities and accessing technical support. Poor connectivity hinders these efforts.

Poor internet connectivity and unreliable communication networks in remote areas can hinder these efforts. Implementing satellite communication systems and establishing clear communication protocols are essential for overcoming these obstacles. This ensures timely support and minimizes machine downtime. Consider redundancy in communication methods.
Satellite communication offers a solution for remote sites. Clear protocols are essential for effective communication. By addressing communication and connectivity challenges, organizations can ensure maintenance teams have the tools they need.
Addressing the challenges of maintaining pipe bundling machines in harsh environments requires a multifaceted approach. Proactive equipment selection, comprehensive maintenance programs, robust environmental protection measures, and effective communication strategies are crucial for ensuring operational efficiency and minimizing downtime. Furthermore, prioritizing local workforce development and leveraging remote support technologies can significantly enhance maintenance capabilities in these challenging environments. Embracing these strategies allows businesses to navigate the unique hurdles of remote operations and maintain consistent productivity.
Conclusion
Maintaining pipe bundling machines in harsh environments requires a proactive and resourceful approach. By addressing logistical hurdles, skill gaps, environmental factors, and communication challenges, a holistic strategy is crucial. Investing in robust equipment, skilled personnel, and innovative solutions ensures reliable operation, minimizing downtime and maximizing productivity, even in the most challenging environments.