What Are the Best Practices for Maintaining Pipe Bundling Equipment?
Maintaining pipe bundling equipment is crucial for efficient operations, minimizing downtime, and extending its lifespan. Adhering to best practices ensures productivity and cost-effectiveness in pipe manufacturing, preventing unexpected breakdowns, and maintaining a competitive edge.
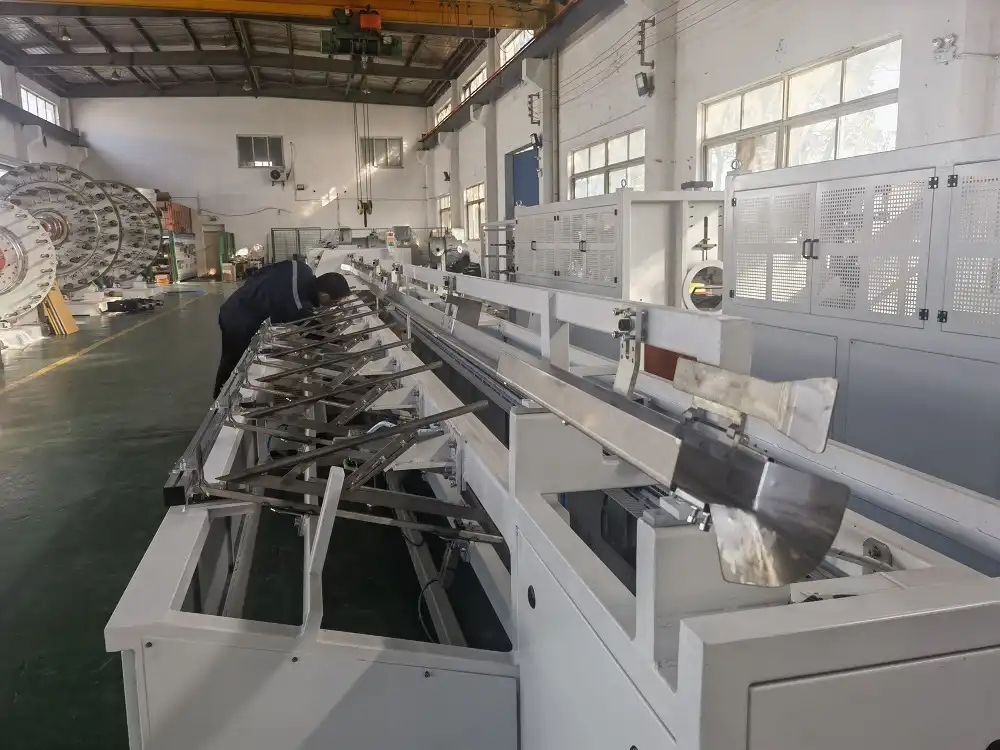
The best practices for maintaining pipe bundling equipment include developing a comprehensive maintenance schedule, implementing regular inspection procedures, ensuring proper lubrication, maintaining hygiene through cleaning, and training operators to follow safety protocols. These measures significantly reduce downtime, extend equipment life, improve safety, and enhance operational efficiency.
To ensure your pipe bundling equipment operates efficiently, it’s crucial to delve into specific maintenance practices. These practices will keep your equipment running smoothly and minimize disruptions to your production schedule. This guide will explore key strategies and actionable tips for optimizing the performance and longevity of your pipe bundling equipment.
1: Developing a Comprehensive Maintenance Schedule
A well-structured maintenance schedule is the foundation of effective equipment care. It outlines tasks, frequency, and responsibilities, ensuring that every aspect of the pipe bundling machine receives attention.
Developing a maintenance schedule for pipe bundling equipment involves defining daily, weekly, monthly, and annual tasks. These tasks include cleaning, lubrication, component inspections, and calibrations. A clear schedule prevents oversights, ensures consistent maintenance, maximizes equipment uptime, and enhances the overall operational efficiency of the equipment.
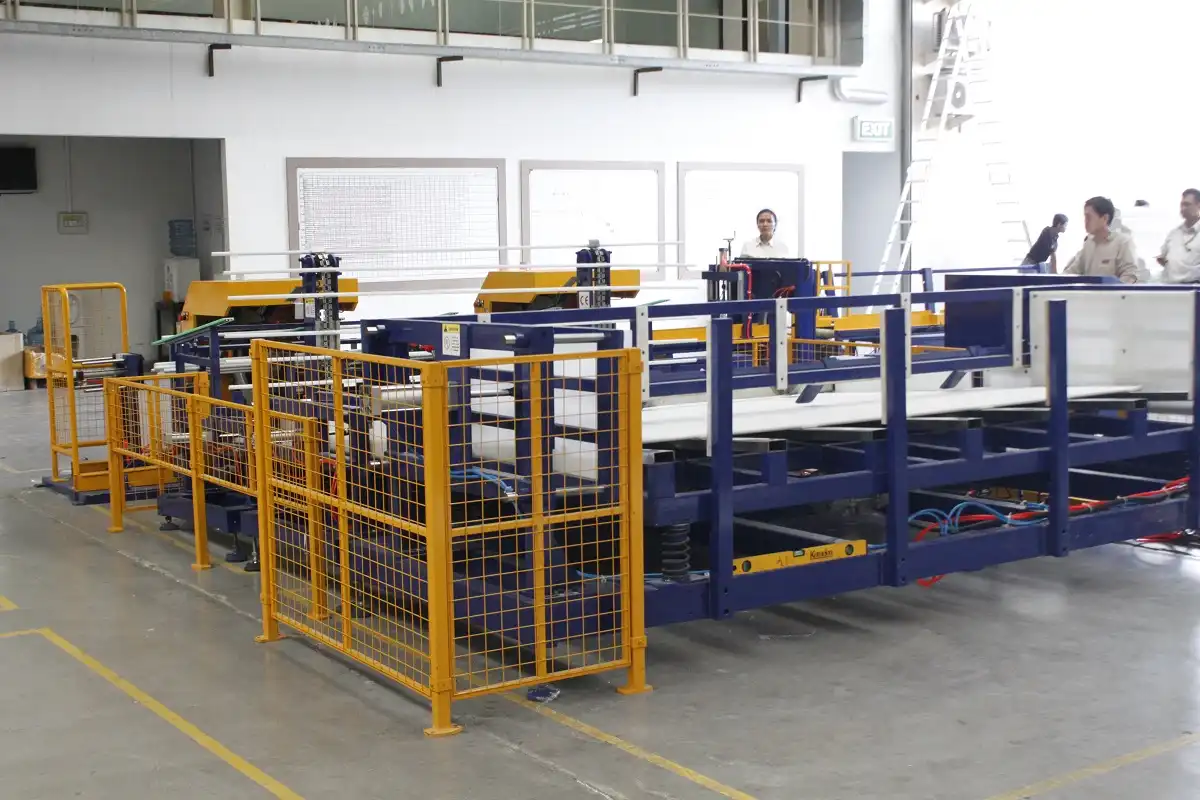
Crafting an Effective Maintenance Schedule: A Detailed Approach
Creating a maintenance schedule involves several key steps. It’s not just about ticking boxes; it’s about understanding your equipment and its specific needs.
Identifying Critical Components: The Heart of Your Equipment
The first step involves pinpointing which parts of the pipe bundling equipment are most susceptible to wear, failure, or misalignment. These components often include:
- Sealing mechanisms: Crucial for preventing leaks and ensuring bundle integrity.
- Cutting blades: Responsible for precise and consistent cuts, requiring regular sharpening or replacement.
- Conveyor belts and rollers: Essential for smooth material transport, demanding frequent checks for wear and tear.
- Sensors and control panels: Vital for accurate operation, necessitating periodic calibration and inspection.
- Motors and drive systems: Powering the entire process, requiring careful monitoring for overheating and unusual noises.
Defining Tasks: Tailoring Maintenance to Each Component
Once the critical components are identified, specify the tasks needed for each one. These tasks might include:
- Cleaning: Removing debris, dust, and residue to prevent malfunctions.
- Lubrication: Reducing friction and wear on moving parts.
- Inspection: Thoroughly examining components for signs of damage, wear, or misalignment.
- Calibration: Adjusting sensors and settings for optimal performance.
- Parts Replacement: Replacing worn components before they cause major failures.
Setting Frequency: Striking the Right Balance
Establishing the right frequency for each task is vital. Over-maintaining can be as detrimental as under-maintaining. Consider the following guidelines:
- Daily Checks: Quick visual inspections and cleaning of accessible parts.
- Weekly Tasks: More detailed inspections, lubrication of moving parts, and cleaning of sensors.
- Monthly Activities: Comprehensive inspections, calibration of sensors, and tightening of fasteners.
- Annual Overhaul: Complete disassembly, thorough cleaning, replacement of worn parts, and detailed calibration.
Assigning Responsibilities: Who Does What?
Clearly assign each task to specific personnel. This ensures accountability and prevents tasks from being overlooked. Consider the following:
- Daily checks: Can be assigned to machine operators.
- Weekly tasks: Often handled by maintenance technicians.
- Monthly activities: Typically managed by senior technicians or maintenance supervisors.
- Annual overhaul: May require specialized personnel or external contractors.
Documenting the Schedule: Making It Accessible and Actionable
Create a written or digital schedule that is easily accessible to all relevant personnel. This schedule should include:
- A list of all maintenance tasks.
- The frequency of each task.
- The person responsible for each task.
- Any specific instructions or procedures.
- A log for recording completed tasks.
By implementing a comprehensive maintenance schedule, pipe manufacturers can significantly reduce downtime, extend equipment life, ensure consistent bundling quality, and improve safety.
Task | Frequency | Responsibility |
---|---|---|
Visual Inspection | Daily | Operator |
Lubrication | Weekly | Technician |
Sensor Calibration | Monthly | Sr. Technician |
Full Disassembly/Clean | Annually | Contractor |
2: Implementing Regular Inspection Procedures
Regular inspections are vital for spotting potential problems early. Trained personnel should conduct thorough examinations of all critical machine components.
Regular inspection procedures for pipe bundling equipment involve checking belts, sensors, motors, and sealing mechanisms for wear, damage, or misalignment. Identifying and addressing minor issues proactively prevents them from escalating into major problems, ensuring consistent operation and minimizing downtime.
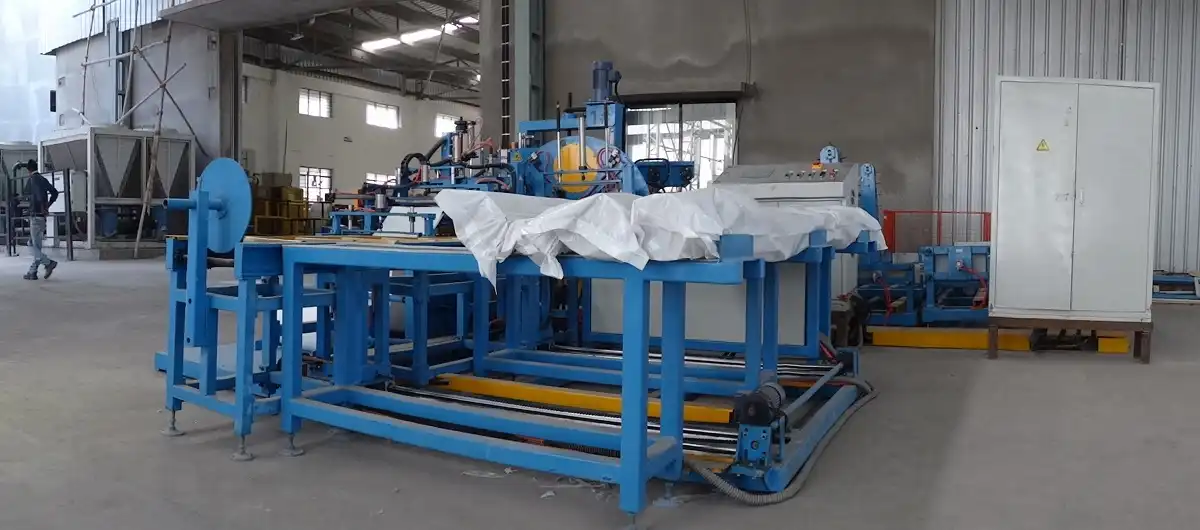
Focus Areas for Inspections
Effective inspection procedures should focus on the following:
- Belts and Chains: Check for wear, cracks, or looseness. Ensure they are properly tensioned and aligned.
- Sensors: Verify proper functioning and alignment. Clean sensors regularly to prevent inaccuracies.
- Motors: Listen for unusual noises and check for overheating. Ensure proper ventilation and cooling.
- Sealing Mechanisms: Ensure proper alignment and temperature control. Inspect for leaks and wear.
- Electrical Connections: Inspect for loose or frayed wires. Tighten connections and replace damaged wiring.
- Pneumatic Systems: Check for leaks and proper pressure levels. Ensure filters are clean and regulators are functioning correctly.
Tools and Techniques
Equipping inspection personnel with the right tools and techniques is essential:
Tool/Technique | Description | Benefit |
---|---|---|
Visual Inspection | Thoroughly examine components for visible signs of wear or damage. | Identifies obvious issues and potential problems. |
Vibration Analysis | Measures the vibration levels of motors and bearings. | Detects imbalances and early signs of wear. |
Thermal Imaging | Uses infrared cameras to detect temperature anomalies. | Identifies overheating components, which can indicate friction or electrical faults. |
Ultrasonic Testing | Detects leaks in pneumatic or hydraulic systems. | Pinpoints leaks that can reduce efficiency. |
Measurement Tools | Calipers, micrometers, and gauges. | Ensures parts meet specified dimensions and tolerances. |
Documentation and Follow-Up
Proper documentation of inspection findings is essential for tracking trends and planning maintenance activities:
- Record Findings: Document all inspection results, including any issues identified.
- Track Trends: Monitor inspection data over time to identify recurring problems or patterns.
- Schedule Repairs: Promptly schedule repairs for any identified issues.
- Follow-Up: Verify that repairs have been completed correctly and effectively.
Regular inspection procedures are a proactive approach that enhances the reliability and longevity of pipe bundling equipment.
3: Lubrication: Reducing Friction and Wear
Lubrication is necessary for the longevity of your pipe bundling equipment. Moving parts like bearings, rollers, and chains must be adequately lubricated to reduce friction and minimize wear.
Proper lubrication of pipe bundling equipment involves applying the correct type and amount of lubricant to all moving parts. Regular lubrication minimizes friction, reduces wear, and prevents overheating. Adhering to the manufacturer’s lubrication schedule and using high-quality lubricants are essential for optimal performance.
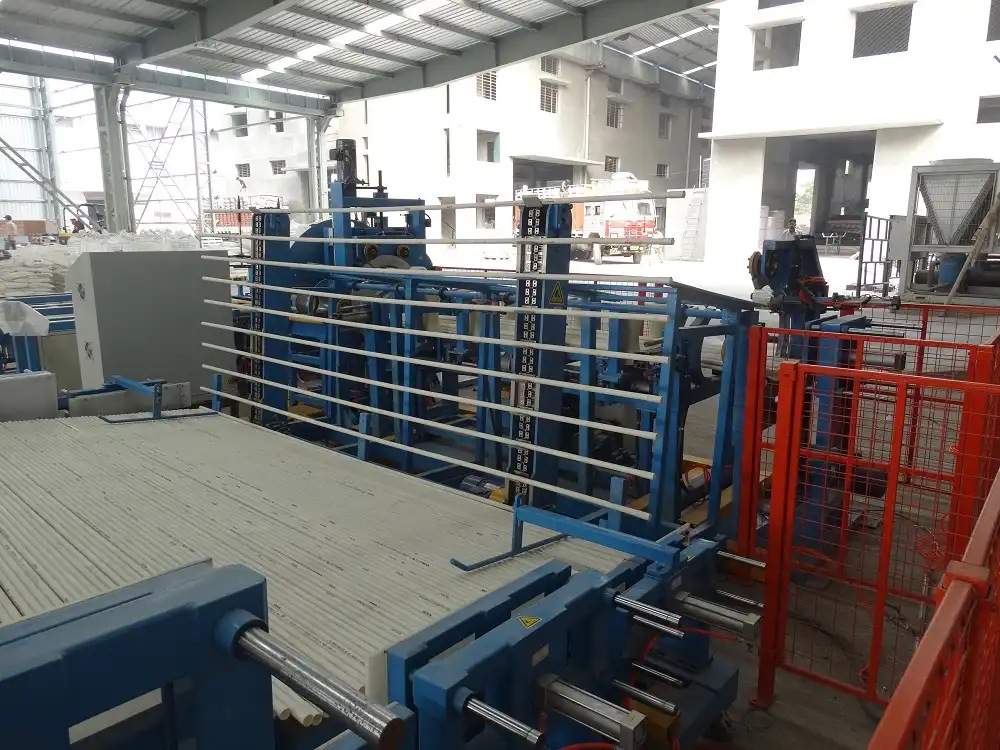
Selecting the Right Lubricants
Choosing the appropriate lubricants is crucial for effective maintenance:
- Manufacturer Recommendations: Always follow the manufacturer’s guidelines for lubricant types.
- Temperature Considerations: Select lubricants that perform well within the equipment’s operating temperature range.
- Compatibility: Ensure lubricants are compatible with the materials used in the equipment.
- Specialized Lubricants: Consider using specialized lubricants for specific applications, such as food-grade lubricants for equipment used in food processing.
Establishing a Lubrication Schedule
Create a lubrication schedule as part of your maintenance routine to ensure nothing is missed:
- Identify Lubrication Points: Determine all points on the equipment that require lubrication.
- Define Frequency: Establish how often each point should be lubricated.
- Assign Responsibilities: Clearly assign lubrication tasks to specific personnel.
- Document the Schedule: Create a written or digital schedule that is easily accessible.
Avoiding Common Lubrication Mistakes
To ensure effective lubrication, avoid these common mistakes:
Mistake | Consequence | Solution |
---|---|---|
Inadequate Lubrication | Increased wear, overheating, and premature part failure | Adhere to the lubrication schedule and use the correct amount of lubricant. |
Over-Lubrication | Attracting dust and contaminants, causing wear | Use the recommended amount of lubricant and clean excess lubricant. |
Using the Wrong Lubricant | Reduced effectiveness and potential damage to components | Always use the type of lubricant recommended by the manufacturer. |
4: Cleaning: Maintaining Hygiene and Performance
Cleaning your pipe bundling equipment is essential for both hygiene and machine performance. Debris, dust, and residue can clog moving parts and cause malfunctions.
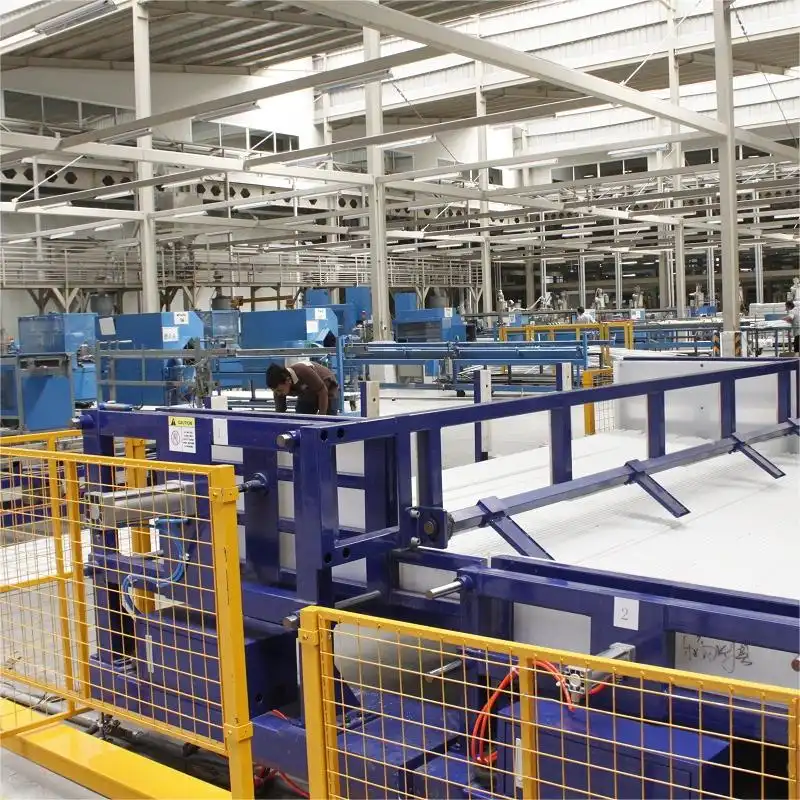
Regular cleaning of pipe bundling equipment involves removing debris, dust, and material residue from all accessible parts. Using recommended cleaning agents and following a consistent cleaning schedule ensures optimal performance and prevents malfunctions. Cleanliness also promotes a hygienic environment.
The benefits of keeping your equipment clean include:
- Hygiene: By implementing a regular cleaning routine using the recommended cleaning products to maintain operational efficiency.
- Improved Machine Performance: Keep machines clean by debris, dust, and residue to clog moving parts and cause malfunctions.
- Machine life: keeping your machine clean will greatly extend its life.
Effective cleaning is vital for maintaining both hygiene and machine performance.
Conclusion
Maintaining pipe bundling equipment through comprehensive training, hands-on practice, continuous education, and rigorous safety protocols, manufacturers can cultivate a skilled and safe workforce that drives operational excellence and maximizes the return on their machinery investments.