Are you in the metal processing industry and struggling to decide between a steel coil packing line and a slit coil packing line? The wrong choice can lead to inefficiencies, increased costs, and even damaged products. Imagine the frustration of a packaging line that can’t handle your coil dimensions or slows down your entire production.
Understanding the core differences between steel coil packing lines and slit coil packing lines is crucial for optimizing your operations. This article provides a detailed comparison to guide your decision, ensuring you choose the best solution for your specific needs and achieve peak efficiency in your coil packaging process.
Choosing the right coil packing line is a critical investment. Let’s delve into the specifics to help you make an informed decision.
Steel Coil Packing Lines
Are you dealing with heavy, full-width steel coils straight from the mill? The challenge lies in efficiently and securely packaging these substantial materials for shipping and storage. Without a robust solution, you risk product damage, unsafe handling, and bottlenecks in your production line.
Steel coil packing lines are specifically engineered to handle these full-width coils, providing a robust and efficient packaging solution. Designed for heavy-duty operations, these lines streamline the process of preparing large steel coils for transport, ensuring stability and protection. They are characterized by their ability to manage substantial weights and dimensions, making them indispensable for businesses processing mill-width coils.

Deep Dive into Steel Coil Packing Line Features
Steel coil packing lines are more than just packaging machines; they are integrated systems designed to handle the specific challenges of full-width steel coils. To fully appreciate their capabilities, let’s break down the key features and functionalities that set them apart.
Handling Capacity and Dimensions
The primary differentiator of steel coil packing lines is their capacity to manage large and heavy coils. These lines are built to accommodate the significant dimensions and weights associated with mill-width steel.
Feature | Steel Coil Packing Lines | Slit Coil Packing Lines |
---|---|---|
Coil Width | 600mm – 2000mm (and wider for specialized lines) | 10mm – 600mm |
Weight Capacity | 10 tons – 40 tons (and higher for heavy-duty models) | Significantly lower, typically up to a few tons |
Packaging Dimensions | Larger, designed for full-width coils | Compact, optimized for narrower slit coils |
Material Thickness | Handles a wide range of thicknesses common in full coils | Typically designed for thinner gauge slit coil material |
As the table illustrates, steel coil packing lines are in a different league when it comes to handling substantial material. This robust design translates to greater efficiency and safety when dealing with full-size steel coils.
Automation and Throughput for Large Coils
Automation is a cornerstone of steel coil packing lines, crucial for managing the volume and weight of full-width coils. These lines often incorporate a high degree of automation to maintain throughput and reduce manual handling.
- Automated Coil Handling: Features like coil cars, upenders, and downenders are integrated to automatically move and position heavy coils throughout the packaging process.
- High-Speed Strapping and Wrapping: Automated strapping and wrapping stations quickly secure and protect coils, minimizing cycle times.
- Integrated Control Systems: Advanced PLCs and HMIs synchronize the entire line, optimizing flow and minimizing downtime.
This level of automation not only increases speed but also enhances safety by reducing the need for manual intervention with heavy materials. For high-volume operations dealing with full-width coils, the throughput advantage of a steel coil packing line is undeniable.
Material and Protection for Heavy Steel
Packaging materials and methods in steel coil packing lines are designed to provide maximum protection for heavy steel coils during transit and storage.
- Heavy-Duty Packaging Materials: Thicker VCI paper, robust plastic films, and corrugated steel or heavy cardboard are used to withstand the weight and potential abrasions of large coils.
- Reinforced Securing Methods: Heavy-gauge steel strapping, edge protectors, and specialized pallets are employed to ensure coil stability and prevent shifting during transportation.
- Weather and Corrosion Resistance: Packaging often includes multiple layers and weather-resistant materials to protect coils from environmental factors, particularly important for long-term storage or overseas shipping.
The emphasis on robust materials and securing methods reflects the need to protect valuable steel coils from damage during handling and shipping, preserving their quality and minimizing potential losses.
Slit Coil Packing Lines
Do you process master coils into narrower strips to meet specific customer orders? Then you understand the challenge of efficiently packaging these multiple, smaller coils. Manual packing can be time-consuming, inconsistent, and prone to error.
Slit coil packing lines are the answer, designed specifically for handling and packaging slit coils with precision and speed. These specialized lines streamline the packaging of narrower coils, ensuring each coil is securely wrapped and protected, ready for delivery or further processing. Their design focuses on managing multiple smaller coils efficiently, a stark contrast to the full-width focus of steel coil packing lines.
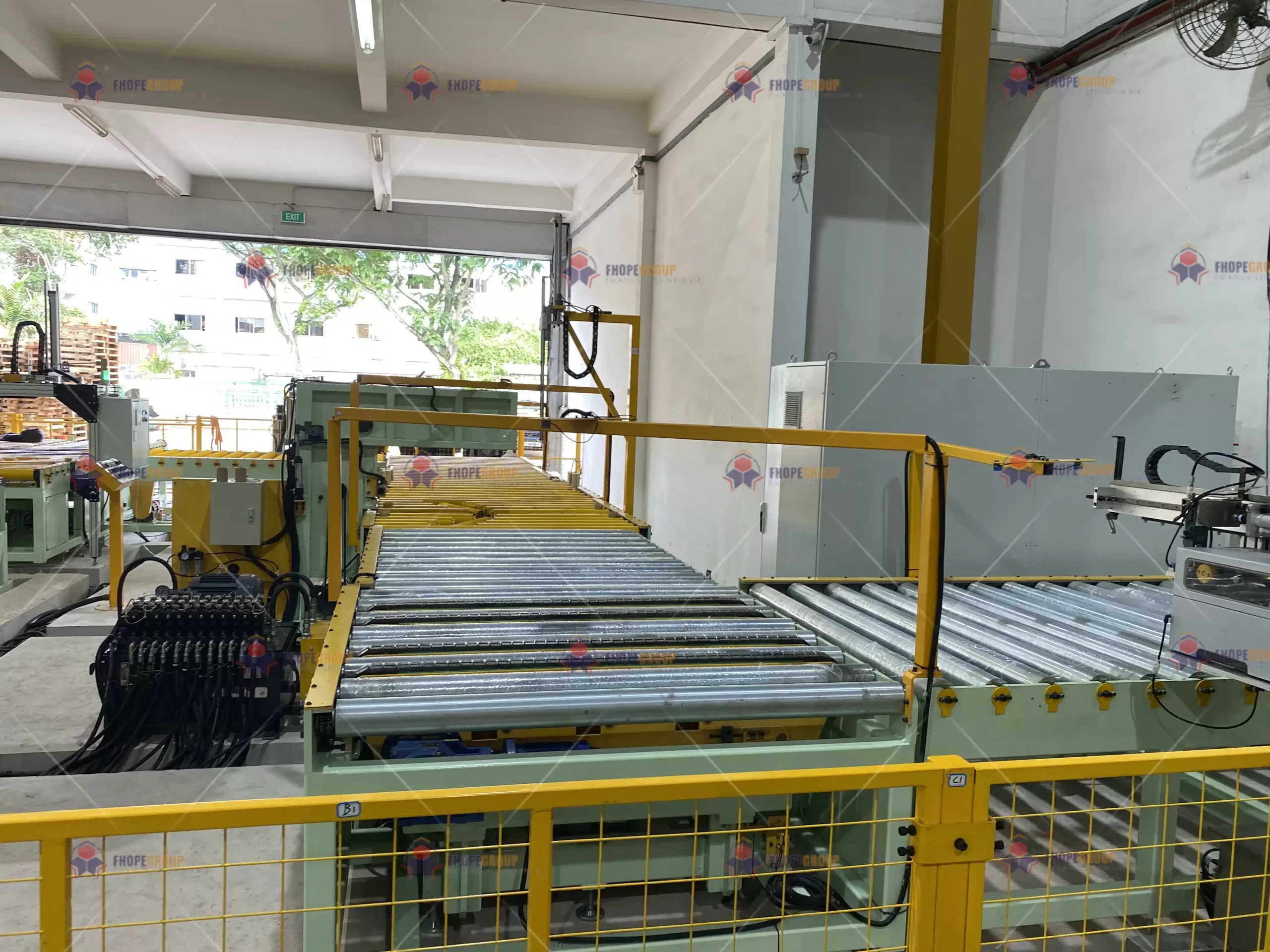
Exploring the Nuances of Slit Coil Packing Lines
Slit coil packing lines are tailored for the unique demands of handling narrower, slit coils. Their design and functionality are optimized for efficiency and precision in packaging these smaller units.
Optimized for Narrow Widths and Multiple Coils
The core design of slit coil packing lines revolves around efficiently handling and packaging coils that have been slit from a wider master coil.
- Narrow Coil Focus: Designed to accommodate coil widths from 10mm up to 600mm, these lines excel at managing the dimensions typical of slit coils.
- Multi-Coil Packaging: Many slit coil lines are designed to package multiple slit coils together as a unit, increasing efficiency and reducing handling of individual coils.
- Compact Line Footprint: Due to the smaller coil dimensions, slit coil lines often have a more compact footprint compared to steel coil lines, saving valuable floor space.
This focus on narrow widths and multi-coil handling directly addresses the needs of businesses that process and distribute slit coils, optimizing their packaging operations for this specific product type.
Flexibility and Customization in Slit Coil Packaging
Flexibility is a key advantage of slit coil packing lines, allowing for customization to meet diverse packaging requirements for different slit coil sizes and customer specifications.
- Adjustable Packaging Configurations: Lines can be configured to package coils individually, in stacks, or in bundles, offering flexibility in packaging formats.
- Variable Strapping and Wrapping Patterns: Adjustable strapping heads and wrapping mechanisms allow for customized securing and protection based on coil size and material.
- Labeling and Identification Systems: Integrated labeling systems can automatically apply labels to individual coils or bundles, improving inventory management and traceability.
This adaptability is crucial for businesses that offer a variety of slit coil sizes and need to cater to specific packaging requests from their customers.
Material Efficiency and Cost-Effectiveness
Slit coil packing lines are designed with material efficiency and cost-effectiveness in mind, reflecting the need to manage packaging costs for potentially higher volumes of smaller coils.
- Optimized Material Usage: Packaging material application is precisely controlled to minimize waste, particularly important when packaging numerous smaller coils.
- Lighter-Weight Packaging Materials: Typically utilize thinner gauge VCI paper, plastic films, and lighter strapping, reducing material costs without compromising necessary protection.
- Energy-Efficient Operation: Often designed for lower energy consumption compared to heavy-duty steel coil lines, contributing to operational cost savings.
By focusing on efficient material use and optimized operation, slit coil packing lines provide a cost-effective packaging solution for businesses dealing with slit coil products, balancing protection with economic considerations.
Coil Dimensions and Weight: The Deciding Factor
When it comes to choosing between a steel coil packing line and a slit coil packing line, the dimensions and weight of your coils are the most critical determinants. Trying to package a full-width master coil on a line designed for narrow slit coils, or vice versa, is a recipe for inefficiency and potential damage.
The fundamental difference in coil size and weight dictates which type of packing line is appropriate. Steel coil lines are built for large, heavy coils, while slit coil lines are designed for smaller, lighter, and often multiple coils. Understanding these distinct capabilities is paramount for making the right investment.
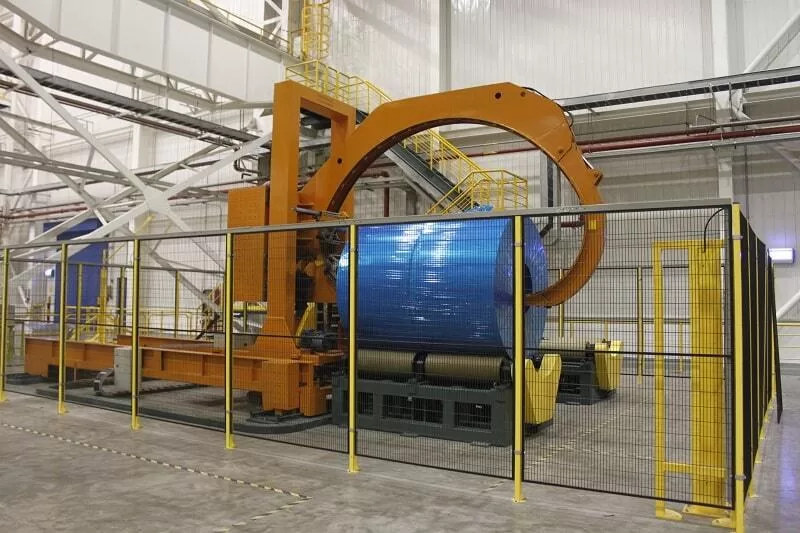
Matching the Line to Your Coil Specs
To illustrate the importance of coil dimensions and weight in line selection, let’s consider a comparative analysis.
Width and Weight Parameters
Feature | Steel Coil Packing Line | Slit Coil Packing Line | Implication for Choice |
---|---|---|---|
Coil Width Range | 600mm – 2000mm | 10mm – 600mm | Mismatched Width: Attempting to run full-width coils on a slit coil line will physically be impossible. Conversely, running very narrow coils on a steel coil line might lead to instability and inefficient packaging. |
Coil Weight Capacity | 10 tons – 40 tons (typical, can be higher) | Significantly lower, typically under 5 tons | Overweight Coils: Exceeding the weight capacity of a slit coil line poses serious safety risks and equipment damage. Underutilizing a steel coil line’s capacity with light coils is less problematic from a safety standpoint but represents an inefficient use of a more robust and expensive system. |
Coil Thickness | Wide range of gauges common in mill-width steel | Typically designed for thinner gauges common in slit coils | Material Compatibility: While less critical than width and weight, extremely thick gauge material might be difficult to handle on some slit coil lines, and very thin gauge might require specialized tension control on steel coil lines. |
This table underscores that coil dimensions and weight are not merely specifications; they are the defining parameters that dictate the fundamental suitability of a packing line for your operation. Accurate assessment of your coil specs is the first and most crucial step in the selection process.
Consequence of Mismatch: Operational Bottlenecks
Choosing the wrong type of packing line based on coil dimensions and weight will inevitably lead to operational bottlenecks and inefficiencies.
- Steel Coil Line for Slit Coils: Underutilization of capacity, inefficient material usage due to larger packaging dimensions, and potentially slower processing times for smaller coils.
- Slit Coil Line for Steel Coils: Physical inability to handle coil width and weight, risk of equipment damage, safety hazards, and complete breakdown of the packaging process.
These scenarios highlight that the mismatch is not just about suboptimal performance; it can result in significant disruptions and even operational failure. Therefore, aligning your coil specifications with the designed capabilities of the packing line is paramount.
Optimizing for Future Needs
When evaluating coil dimensions and weight, consider not only your current product range but also potential future changes in your production.
- Scalability: If you anticipate handling larger or heavier coils in the future, choosing a steel coil line with sufficient capacity from the outset might be a prudent long-term investment, even if your current needs are smaller.
- Flexibility: If your product mix is highly variable, explore packing line options that offer some degree of adjustability and flexibility to accommodate a range of coil sizes within the appropriate category (steel or slit).
By considering future needs in addition to immediate requirements, you can make a more strategic decision that ensures your chosen packing line remains efficient and effective as your business evolves.
Packaging Materials and Methods: Protection and Presentation
Beyond the physical dimensions, the way coils are packaged is crucial for protection during transit and storage, as well as for presentation to the customer. Steel coil packing lines and slit coil packing lines differ significantly in their approach to packaging materials and methods, reflecting the different nature of the coils they handle.
Steel coil lines prioritize robust protection for large, heavy coils, while slit coil lines often balance protection with considerations of material efficiency and presentation for smaller units. Understanding these contrasting priorities is key to selecting a line that meets both your functional and customer-facing packaging needs.

Steel coil packing lines typically employ heavier-duty packaging materials and robust securing methods due to the size and weight of the coils. These include thicker VCI paper, plastic film, or corrugated sheets, along with heavy-duty strapping and reinforced pallets. Slit coil lines, on the other hand, use lighter-weight materials like thinner VCI paper or plastic film and may utilize lighter-duty strapping or banding.
The choice of packaging directly impacts protection levels, handling ease, and cost. Selecting appropriate materials and methods is essential for optimizing these factors.
Conclusion
Choosing between a steel coil packing line and a slit coil packing line is a critical decision with far-reaching implications for your metal processing operations. Factors such as coil dimensions, weight, production volume, and packaging requirements must be carefully evaluated. By understanding the key differences outlined and aligning them with your specific business needs, you can select the coil packing line that will drive efficiency, reduce costs, and enhance customer satisfaction.