Are you overlooking a hidden danger in your industrial operations? Mold, often unseen, can pose significant health risks, especially in environments utilizing mold upenders. Ignoring OSHA compliance in mold safety isn’t just a regulatory oversight—it’s a gamble with worker health and operational efficiency. Are you prepared to ensure your workplace is safe from mold-related hazards and fully OSHA compliant?
Navigating mold safety standards for mold upenders is critical for workplace health and regulatory compliance. This guide breaks down OSHA’s guidelines, remediation levels, and best practices to ensure your operations are safe and compliant, protecting your employees from mold-related hazards.
Ignoring mold risks can lead to severe health issues, reduced productivity, and hefty OSHA fines. Let’s delve into understanding and implementing robust mold safety standards for your mold upender operations, ensuring a healthier, safer, and compliant workplace.
Understanding Mold Hazards and OSHA’s Role
Mold in industrial settings, particularly around mold upenders, isn’t just a cosmetic issue—it’s a significant health hazard. Workers exposed to mold can suffer from allergies, respiratory problems, and more severe health complications. Are you truly aware of the extent of these risks and OSHA’s stance on workplace mold?
OSHA addresses mold hazards primarily through the General Duty Clause, requiring employers to provide a workplace free from recognized hazards. While there are no specific OSHA mold standards, compliance involves adhering to hazard communication, respiratory protection, and other relevant regulations to mitigate mold-related risks in workplaces using mold upenders.

Delving Deeper into OSHA and Mold: Beyond Specific Standards
OSHA’s approach to mold regulation is often perceived as indirect, leading to confusion and potential compliance gaps. While OSHA lacks explicit mold-specific standards, its existing regulations and guidelines are fully applicable to mold hazards in industrial environments, including those utilizing mold upenders. Understanding this nuanced approach is crucial for effective risk management and workplace safety.
The General Duty Clause: OSHA’s Broad Sword Against Unspecified Hazards
Section 5(a)(1) of the Occupational Safety and Health Act, known as the General Duty Clause, is OSHA’s overarching tool to address hazards not specifically covered by existing standards. For mold, this clause is paramount. It mandates employers to furnish a workplace "free from recognized hazards that are causing or are likely to cause death or serious physical harm." Mold, with its well-documented health risks, falls squarely under this clause when present at hazardous levels in the workplace.
Relevant OSHA Standards Applicable to Mold
While no single standard targets mold directly, several OSHA standards are critical in mold hazard management:
- Hazard Communication Standard (29 CFR 1910.1200): Requires employers to inform employees about chemical and other hazards in the workplace, which, depending on the context, could extend to mold, especially concerning cleaning agents or biocides used in remediation.
- Respiratory Protection Standard (29 CFR 1910.134): Crucial for protecting workers during mold remediation or in environments with significant airborne mold spores. This standard dictates requirements for respirators, fit testing, medical evaluations, and a written respiratory protection program.
- Personal Protective Equipment (PPE) Standards (29 CFR 1910 Subpart I): Encompasses the need for appropriate PPE, including gloves, eye protection, and protective clothing, during mold cleanup and in areas with potential mold exposure.
OSHA Guidance Documents: Informational, Not Regulatory
OSHA provides Safety and Health Information Bulletins (SHIBs) and other guidance documents, such as "A Brief Guide to Mold in the Workplace." These documents are advisory and informational, offering recommendations for mold prevention and remediation. They do not create new legal obligations but are invaluable resources for employers seeking to understand best practices and OSHA’s recommended approaches to mold management.
Challenges in Enforcement and Compliance
The lack of specific Permissible Exposure Limits (PELs) for mold spores creates challenges in OSHA enforcement and employer compliance. Without definitive thresholds, determining "hazardous levels" of mold relies on professional judgment, industry best practices, and documented health effects. This ambiguity necessitates a proactive and informed approach from employers, focusing on prevention and comprehensive risk management rather than merely reacting to violations.
State Plans: Potential for More Stringent Regulations
It’s also important to note that OSHA-approved State Plans can have their own, more stringent standards and enforcement policies regarding workplace safety and health, including mold. Employers in states with such plans must be aware of and comply with these state-specific regulations, which may go beyond federal OSHA requirements.
By understanding OSHA’s multi-faceted approach—utilizing the General Duty Clause, applying relevant existing standards, and providing guidance through informational documents—employers can develop robust mold safety programs. This proactive stance is not just about avoiding penalties; it’s about genuinely protecting worker health and fostering a safer, more productive work environment around operations like mold upenders.
Implementing Mold Upender Safety Standards
Ensuring mold upender safety goes beyond understanding regulations—it’s about practical implementation. What concrete steps can your organization take to create a mold-safe environment around these critical pieces of machinery? Are you proactively addressing moisture, ventilation, and cleaning protocols?
Implementing mold upender safety standards involves proactive measures such as regular inspections for moisture and mold growth, effective ventilation, and prompt remediation of any mold found. Training employees on mold hazards, providing necessary PPE, and establishing clear cleaning protocols are crucial steps in maintaining a safe and OSHA-compliant workplace around mold upenders.

Practical Strategies for Mold Prevention and Control Around Mold Upenders
Creating a mold-safe environment around mold upenders requires a multifaceted approach, focusing on prevention, early detection, and effective remediation. Here are key strategies for practical implementation:
1. Regular Inspections and Moisture Control: The First Line of Defense
- Routine Visual Inspections: Implement a schedule for regular visual inspections of mold upender areas, focusing on signs of moisture, water damage, and visible mold growth on equipment, surrounding structures, and materials.
- Moisture Monitoring: Utilize moisture meters to assess humidity levels in the air and moisture content in building materials and around the mold upender itself. Aim to maintain relative humidity below 70%, ideally between 25% and 60%.
- Leak Detection and Repair: Establish protocols for promptly reporting and repairing any leaks from plumbing, roofs, or the mold upender’s hydraulic systems. Address condensation issues by improving insulation or ventilation in affected areas.
- Proper Drainage: Ensure adequate drainage around the building and mold upender foundations to divert water away and prevent water intrusion. Check and maintain gutters and downspouts regularly.
2. Ventilation and Airflow: Reducing Mold-Friendly Conditions
- Adequate Ventilation: Ensure sufficient ventilation in areas housing mold upenders to reduce humidity and prevent moisture buildup. Natural ventilation (opening windows and doors when feasible) and mechanical ventilation systems (fans, HVAC) are crucial.
- HVAC System Management: Regularly inspect and maintain HVAC systems, including drip pans, to prevent mold growth within the system itself. Ensure proper airflow and filtration. Consider upgrading to higher-efficiency filters (MERV 8 or higher) to capture mold spores. Change filters regularly as part of a scheduled maintenance program.
- Local Exhaust Ventilation: In areas prone to moisture or mold, consider implementing local exhaust ventilation to remove humid air and potential airborne mold spores directly at the source.
3. Cleaning and Remediation Protocols: Addressing Mold When It Occurs
- Prompt Cleanup of Spills and Water Damage: Establish procedures for immediate cleanup of water spills and leaks, aiming to dry affected areas within 24-48 hours to prevent mold growth. Use wet vacuums for water removal and dehumidifiers and fans to expedite drying.
- Mold Remediation Plan: Develop a comprehensive mold remediation plan that outlines procedures for different levels of mold contamination (following OSHA guidelines – see Section 3). This plan should include containment, removal, cleaning, and disposal methods, as well as PPE requirements.
- Appropriate Cleaning Agents: For non-porous surfaces (metal, hard plastics of the mold upender), use detergent and water for cleaning. Disinfectants (like diluted bleach solution) can be used if necessary, but always with proper ventilation and PPE, and never mixed with ammonia-containing cleaners. Avoid bleach on metal parts of the mold upender to prevent corrosion.
- HEPA Vacuuming: Utilize HEPA vacuums for final cleanup after remediation and for routine cleaning in mold-prone areas. HEPA vacuums are essential for capturing fine mold spores and preventing their dispersal.
- Proper Disposal of Mold-Contaminated Materials: Dispose of mold-contaminated porous materials (like insulation, drywall) in sealed, impermeable bags to prevent spore dispersal during removal and disposal.
4. Employee Training and Awareness: Empowering the Workforce
- Mold Hazard Training: Conduct regular training for all employees working with or around mold upenders, educating them about mold hazards, health effects, prevention strategies, and proper response procedures.
- PPE Training and Provision: Train employees on the correct use of respirators, gloves, eye protection, and protective clothing required for different levels of mold exposure and remediation tasks. Provide readily accessible PPE and ensure proper fit and maintenance.
- Reporting Procedures: Establish clear procedures for employees to report suspected mold growth, water leaks, or any mold-related health symptoms. Encourage a culture of proactive reporting without fear of reprisal.
5. Documentation and Record Keeping: Demonstrating Compliance
- Maintain Records: Keep detailed records of all inspections, maintenance, repairs, water damage incidents, mold remediation activities, and employee training related to mold safety. This documentation is crucial for demonstrating OSHA compliance and for tracking the effectiveness of your mold management program.
- Regular Program Review: Periodically review and update your mold safety program to incorporate new information, adjust procedures based on experience, and ensure continuous improvement in workplace safety.
By consistently implementing these practical strategies, organizations can create a safer working environment around mold upenders, significantly reduce the risk of mold-related health issues, and ensure ongoing OSHA compliance. Proactive prevention and control are not just regulatory necessities; they are investments in employee well-being and operational efficiency.
OSHA Compliance and Mold Remediation Levels
OSHA’s guidance on mold remediation is tiered, based on the extent of contamination. Are you familiar with these different levels and the specific safety protocols each demands? Understanding these distinctions is key to appropriate and compliant mold remediation in your facility.
OSHA categorizes mold remediation into four levels (I-IV) based on the area of contamination, each with specific requirements for worker protection, containment, and cleanup methods. Compliance involves accurately assessing the contamination level and implementing the corresponding OSHA-recommended procedures to ensure worker safety during mold remediation around mold upenders and in affected areas.
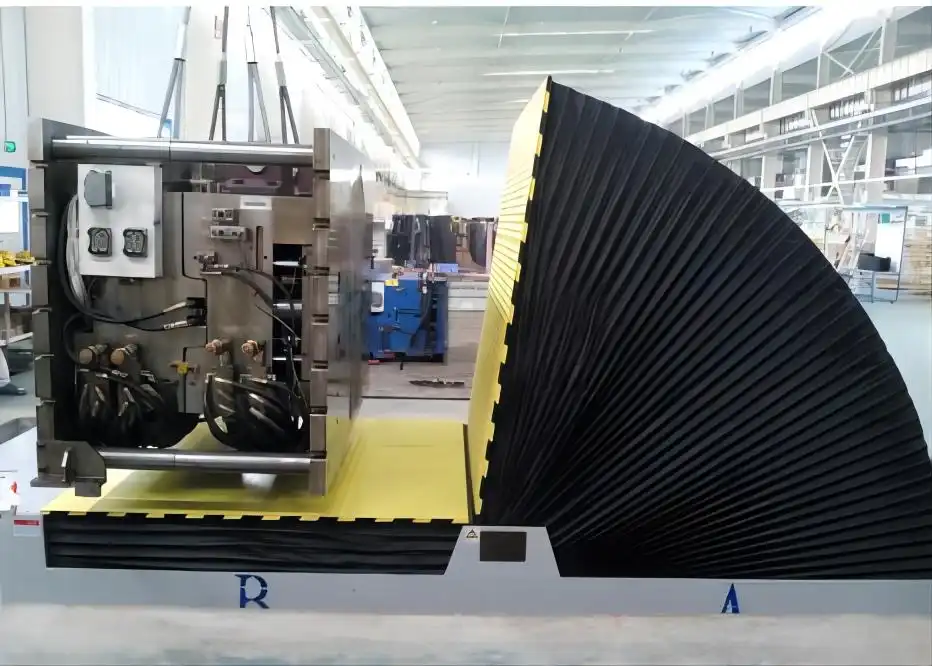
Decoding OSHA’s Mold Remediation Levels: A Practical Guide for Compliance
OSHA’s tiered approach to mold remediation provides a practical framework for businesses to respond appropriately to different scales of mold contamination. Understanding these levels and their corresponding requirements is crucial for ensuring both worker safety and OSHA compliance during mold cleanup, particularly in industrial settings involving equipment like mold upenders.
OSHA Remediation Levels: A Comparative Overview
The following table summarizes OSHA’s four levels of mold remediation, outlining key differences in required procedures:
Level | Area of Contamination | Personnel | Respiratory Protection (Minimum) | Containment | Cleanup Methods | PPE Requirements (Beyond Respiratory) | When to Consult Professionals |
---|---|---|---|---|---|---|---|
Level I | Small Isolated (≤10 sq ft) | Regular Building Maintenance Staff (Trained) | N-95 Disposable Respirator | Not Necessary | Damp cloth/mop with detergent solution | Gloves, Eye Protection | Routine Maintenance |
Level II | Mid-Sized Isolated (10-30 sq ft) | Regular Building Maintenance Staff (Trained) | N-95 Disposable Respirator | Not Necessary | HEPA Vacuum, Damp cloth/mop with detergent solution | Gloves, Eye Protection, Plastic Sheeting for Surfaces | Routine Maintenance |
Level III | Large Isolated (30-100 sq ft) | Trained Personnel (Hazardous Materials Handling Recommended) | N-95 Disposable Respirator | Recommended | HEPA Vacuum, Damp cloth/mop with detergent solution | Gloves, Eye Protection, Plastic Sheeting for Surfaces, Ventilation Duct Sealing | Consult Industrial Hygienist/EHS Professional (Especially for Heavy Dust/Mold) |
Level IV | Extensive (>100 sq ft) | Personnel Trained in Hazardous Materials Handling | Full Facepiece Respirator with HEPA Cartridges | Complete Isolation (Critical) | HEPA Vacuum, Damp cloth/mop with detergent solution | Full Body Disposable Protective Clothing, Gloves, Eye Protection | Required: Industrial Hygienist/EHS Professional Oversight |
Key Considerations for Each Level:
- Level I (Small Isolated Areas): Typically manageable by in-house maintenance staff who have received basic training on mold cleanup methods and hazard communication. Focus is on simple removal and preventing recurrence. Respiratory protection is recommended but containment is not deemed necessary for these small areas.
- Level II (Mid-Sized Isolated Areas): Still within the scope of trained maintenance staff, but with increased precautions. HEPA vacuuming becomes a requirement, and surface containment using plastic sheeting is advised to prevent spore dispersal. Respiratory protection remains at the N-95 level.
- Level III (Large Isolated Areas): This level signals a transition to more serious contamination. OSHA recommends consulting industrial hygienists or EHS professionals for oversight, especially if significant dust generation or heavy mold growth is anticipated. Containment is recommended, and personnel should ideally have hazardous materials handling training.
- Level IV (Extensive Contamination): Represents the highest risk level and necessitates professional involvement. Full containment with negative pressurization and airlocks is required to prevent widespread contamination. Personnel must wear full facepiece respirators with HEPA cartridges and full-body protective clothing. Industrial hygienist/EHS professional oversight is essential for planning and executing remediation.
Practical Implications for Mold Upender Areas:
- Assessment is Key: Accurate assessment of the contaminated area is the first critical step in determining the appropriate remediation level. Don’t underestimate the extent of mold growth, especially in hidden areas around and under mold upenders.
- Training is Paramount: Ensure all personnel involved in any level of mold remediation are adequately trained, not just on cleanup methods but also on hazard recognition, PPE use, and respiratory protection requirements, as mandated by OSHA standards like Hazard Communication and Respiratory Protection standards.
- Professional Consultation: For Level III and IV remediations, engaging qualified industrial hygienists or environmental health and safety professionals is not just recommended—it’s a best practice and often a necessity to ensure effective and safe remediation and to maintain OSHA compliance. Their expertise is crucial for complex situations and for developing comprehensive remediation plans.
- Documentation is Crucial: Meticulously document all steps taken during remediation, including initial assessment, level determination, methods used, personnel involved, PPE utilized, and post-remediation verification. This documentation serves as evidence of compliance and is vital for any potential OSHA inspections or liability concerns.
By diligently following OSHA’s remediation level guidelines and adapting them to the specific context of mold upender operations, businesses can effectively manage mold hazards, protect worker health, and maintain regulatory compliance. The tiered approach allows for scalable responses, ensuring resources are appropriately allocated to the level of risk presented by the mold contamination.
Navigating Regulations and Best Practices Beyond Compliance
Compliance is the baseline, but true safety leadership goes further. Are you just meeting the minimum regulatory requirements, or are you striving for best-in-class mold safety practices? Going beyond basic compliance can significantly enhance worker protection and long-term operational resilience.

Moving beyond mere regulatory compliance in mold safety is about adopting a proactive, comprehensive approach that prioritizes worker well-being and long-term risk mitigation. While OSHA guidelines and standards provide a crucial framework, true leadership in safety involves implementing best practices that exceed minimum requirements.
Proactive Strategies for Superior Mold Safety:
-
Develop a Comprehensive Mold Management Plan: Go beyond reactive remediation. Create a written mold management plan that outlines prevention strategies, inspection schedules, remediation procedures, training programs, and roles/responsibilities. This plan should be a living document, regularly reviewed and updated.
-
Prioritize Prevention through Design and Engineering Controls: Incorporate mold prevention into the design of workspaces and equipment layouts. Ensure adequate ventilation from the outset, select moisture-resistant building materials where feasible, and design for easy cleaning and maintenance around mold upenders. Consider enclosing or isolating mold-prone processes to minimize moisture release into the general workspace.
-
Implement Advanced Monitoring Technologies: Explore the use of continuous humidity and temperature monitoring systems, especially in critical areas around mold upenders. Consider investing in early mold detection technologies, such as air sampling devices or surface swab tests, for proactive identification of potential issues before visible growth occurs.
-
Enhance Ventilation and Air Purification: Beyond basic ventilation, explore advanced air purification systems, such as HEPA filtration for the entire workspace or localized air purification units in high-risk zones. Consider UVGI (Ultraviolet Germicidal Irradiation) systems in HVAC to kill airborne mold spores and prevent system contamination.
-
Elevate Cleaning and Sanitation Standards: Implement enhanced cleaning protocols that go beyond routine janitorial services. Incorporate regular deep cleaning of mold upender areas, focusing on moisture-prone zones and hard-to-reach spaces. Utilize specialized cleaning agents and techniques proven effective against mold, while ensuring worker safety and material compatibility.
-
Invest in Advanced Worker Training and Education: Expand worker training beyond basic awareness to include in-depth education on mold ecology, health effects, risk factors, and advanced prevention and control techniques. Empower employees to be active participants in mold safety by encouraging hazard identification and proactive reporting.
-
Establish a Medical Surveillance Program: For workers in high-risk areas, consider implementing a medical surveillance program to monitor for early signs of mold-related health issues. This could include periodic respiratory health assessments and allergy screenings. Early detection and intervention can significantly improve health outcomes.
-
Regularly Audit and Benchmark Your Program: Conduct periodic audits of your mold management program to assess its effectiveness, identify areas for improvement, and ensure ongoing compliance. Benchmark your program against industry best practices and seek external certifications or accreditations to demonstrate your commitment to superior mold safety.
-
Foster a Culture of Safety and Continuous Improvement: Cultivate a workplace culture where mold safety is not just a compliance issue but a core value. Encourage open communication, proactive hazard reporting, and continuous improvement initiatives. Recognize and reward employees who contribute to enhancing mold safety.
-
Stay Updated on Emerging Research and Best Practices: Mold science and remediation techniques are constantly evolving. Stay informed about the latest research, industry guidelines, and best practices by subscribing to relevant publications, attending industry conferences, and engaging with professional organizations focused on industrial hygiene and environmental health.
By embracing these proactive strategies, organizations can move beyond basic OSHA compliance and establish themselves as leaders in mold safety. This commitment not only protects worker health and well-being but also enhances operational efficiency, reduces liability risks, and fosters a culture of excellence in workplace safety.
Conclusion
Navigating mold upender safety standards and achieving OSHA compliance is not merely about avoiding penalties—it’s about creating a healthier, safer, and more productive workplace. By understanding OSHA’s guidelines, implementing proactive prevention strategies, and adhering to appropriate remediation levels, businesses can effectively mitigate mold hazards. Prioritizing mold upender safety demonstrates a commitment to worker well-being and operational excellence, fostering a resilient and compliant industrial environment.