How to Reduce Labor Costs with Automated Pipe Bagging Systems?
Industries striving for peak efficiency are increasingly turning to automation. Automated pipe bagging systems offer a game-changing approach to packaging, optimizing operations while significantly reducing labor expenses. This makes them essential for modern manufacturers.
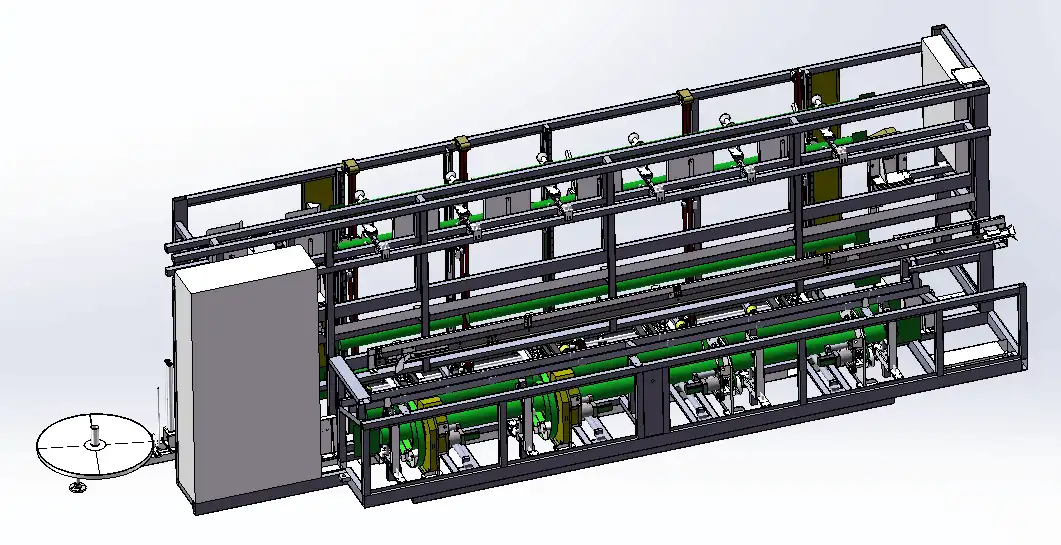
Automated pipe bagging systems dramatically reduce labor costs by automating the entire bagging process. Replacing manual labor minimizes the need for large teams, cuts down on labor-related expenses, and allows companies to reallocate their workforce to more valuable tasks, leading to significant operational savings and enhanced efficiency.
Transitioning to automated pipe bagging systems can revolutionize your production line. Let’s delve into how these systems drive down labor costs and boost operational efficiency. This article explores the strategic benefits of investing in automation.
1. Quantifiable Benefits of Automation
Automated pipe bagging systems offer significant labor cost reductions by automating a labor-intensive process. The financial and strategic advantages are substantial.
The most immediate benefit of automated pipe bagging is the reduction of direct labor costs. Manual bagging necessitates a large workforce, making it both time-consuming and expensive. Automating this process saves money across several key areas, freeing up valuable resources and improving your bottom line.
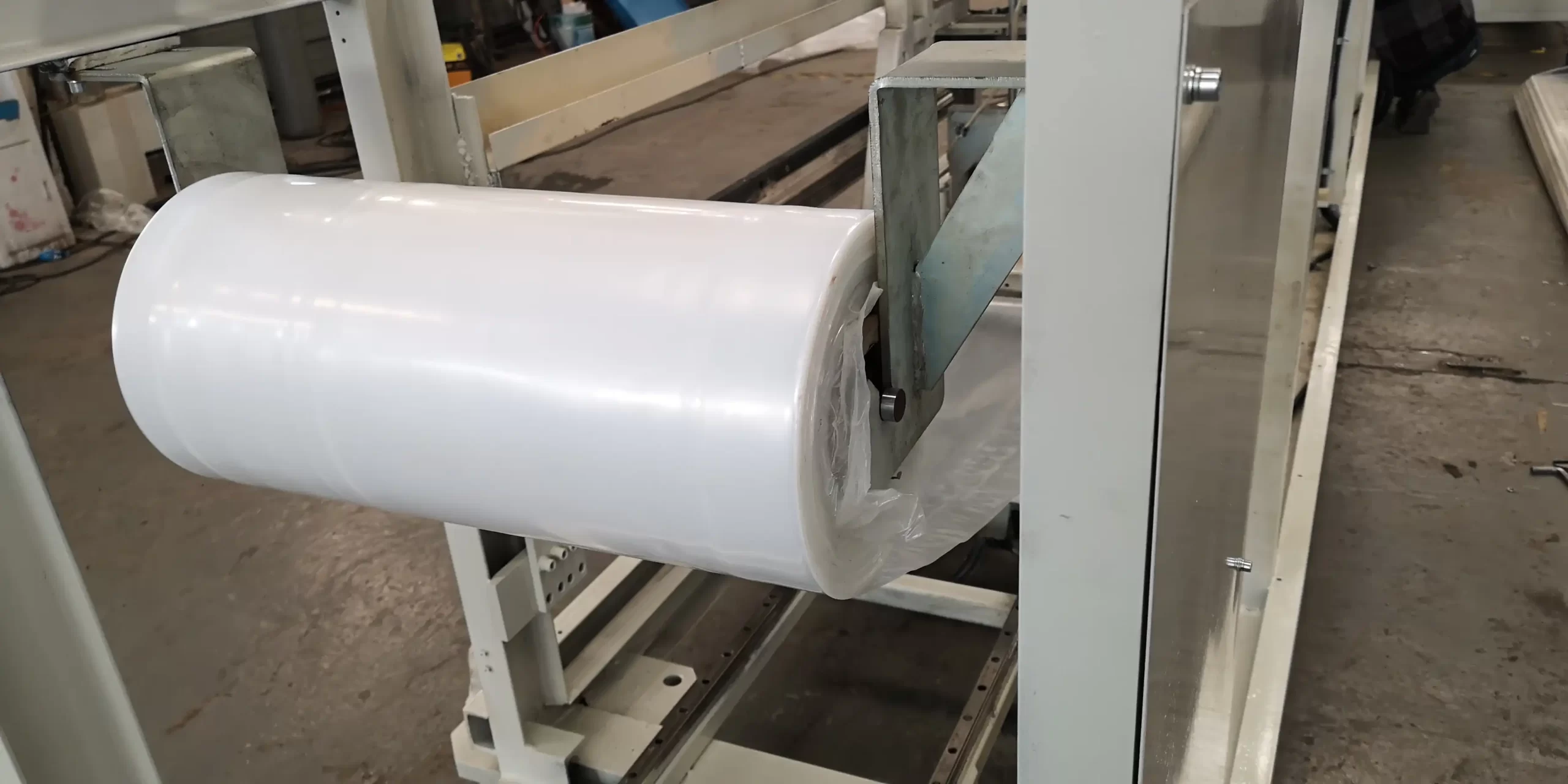
Unpacking the Cost Savings: A Detailed Look
The reduction in direct labor is just the beginning. Automated bagging offers cascading effects that amplify savings across multiple operational areas. Let’s break down the specifics:
Direct Labor Cost Savings: A Side-by-Side Comparison
To illustrate the potential savings, consider this comparison between manual and automated bagging:
Cost Factor | Manual Bagging | Automated Bagging | Cost Reduction Potential |
---|---|---|---|
Labor Wages | High – Requires multiple workers | Low – Minimal supervision | 60-80% |
Benefits & Insurance | Higher for larger workforce | Lower with reduced workforce | Proportional to Wage Savings |
Training Costs | Continuous for bagging teams | Reduced, machine operation focus | 40-60% |
Error Rate | Higher – Human error prone | Lower – Consistent automation | 70-90% |
Throughput | Lower – Limited by manual pace | Higher – Consistent speed | 100-300% |
Reduced Training Costs: Focus on Expertise
Training manual bagging teams requires significant resources. With automation, training shifts to machine operation, substantially reducing the time and money spent on instruction. Employees learn to manage and maintain the system, a skill with broader applications within the manufacturing environment.
Lower Error Rates: Precision Packaging
Human error is a common and costly issue in manual bagging. Automated systems guarantee consistent and accurate packaging, drastically minimizing errors. This translates directly to reduced waste, fewer rejected products, and improved customer satisfaction. Investing in Automated pipe bagging minimizes inconsistencies and ensures a higher-quality output.
Increased Throughput: Boosting Productivity
Automated bagging systems operate at a consistent, high speed, significantly increasing throughput. This means more pipes are packaged per hour, translating to higher productivity with the same or reduced workforce. This efficiency is crucial for meeting demanding production schedules and maximizing profitability.
Strategic Advantages: Reallocating Resources
Automation allows companies to reallocate human resources to more critical areas, such as quality control, maintenance, and process improvement. This not only enhances operational efficiency but also elevates the value of the workforce. By freeing employees from repetitive tasks, you can invest in their skills and contribute to innovation.
Overcoming Implementation Challenges
While the benefits are clear, implementing automated bagging systems can present challenges:
- Initial Investment Costs: The initial cost can be a barrier. However, the long-term ROI typically justifies the upfront investment through labor savings, reduced waste, and increased productivity.
- Integration Issues: Integrating new machinery into existing production lines can be complex. Careful planning and professional installation are crucial for a smooth transition.
-
Maintenance Requirements: Automated systems require regular maintenance to ensure optimal performance. Investing in maintenance training and support can mitigate this issue.
By addressing these challenges proactively, pipe manufacturers can fully realize the benefits of automated bagging systems.
2. Optimizing Warehouse Space with Automated Bagging
Efficient warehouse space utilization is vital for minimizing inventory costs. Automated bagging systems optimize space by creating consistently sized and tightly packed bundles, maximizing storage density.
Automated bagging systems enhance warehouse operations by creating uniform and compact pipe bundles. Consistent sizing allows for denser storage configurations, maximizing both vertical and horizontal space utilization. This directly reduces the warehouse footprint and lowers storage-related costs, contributing to significant savings.
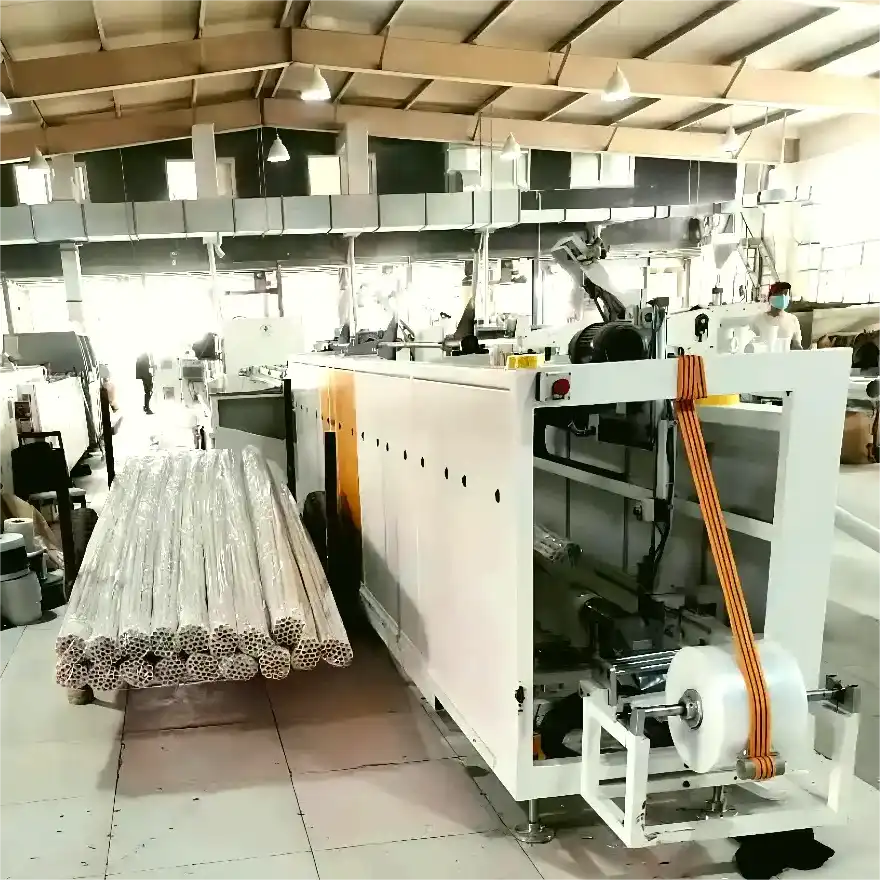
The Space-Saving Impact: A Warehouse Revolution
Manually bundled pipes often result in irregular shapes and sizes, leading to wasted space during storage. Automated bagging ensures uniform and compact bundles, offering significant improvements:
Space Efficiency and Cost Savings in Warehousing:
Warehouse Cost | Manual Bundling | Automated Bagging | Space/Cost Reduction |
---|---|---|---|
Storage Footprint | Larger – Irregular shapes | Smaller – Uniform, compact | 20-40% space reduction |
Rent/Lease | Higher – More space needed | Lower – Less space needed | 20-40% proportional saving |
Utilities (Lighting) | Higher – Larger space | Lower – Smaller space | 10-20% utility reduction |
Handling Costs | Higher – Less efficient | Lower – Easier stacking | 15-25% handling cost cut |
Inventory Management | Complex, less accurate | Simpler, accurate | Improved efficiency |
Detailed Breakdown of Space-Related Savings:
- Reduced Storage Footprint: Uniform bundle dimensions translate to a smaller storage footprint, allowing for more efficient use of available space. This directly impacts the bottom line by reducing the need for expansion or off-site storage.
- Lower Rent/Lease Costs: A smaller storage area directly reduces rent or lease costs, providing significant savings over time. These savings can be reinvested in other areas of the business.
- Decreased Utility Expenses: Less space requires less energy for lighting, heating, and cooling, further contributing to reduced utility expenses. Energy efficiency is not only good for the environment but also for your budget.
- Improved Handling Efficiency: Uniform bundles are easier to stack and manage, reducing handling costs and simplifying inventory management. This streamlines operations and reduces the risk of workplace injuries.
- Maximizing Vertical Space: Consistent bundle sizes make it easier to stack pipes higher and more securely, maximizing the use of available height in the warehouse. This optimization is critical for high-volume operations.
-
Inventory Management Improvements: Accurate space planning simplifies inventory management, making it easier to track and retrieve items. This reduces the risk of lost or misplaced inventory, further contributing to cost savings. Accurate inventory leads to better order fulfillment and improved customer satisfaction.
By implementing automated bagging systems, businesses can unlock significant cost savings related to warehouse space and inventory management.
3. Reducing Material Waste with Automated Bagging
Damage during handling and storage leads to significant losses in the pipe manufacturing industry. Automated bagging provides secure and protective packaging, minimizing the risk of damage.
Automated bagging machines minimize product damage by providing secure and consistent packaging, thereby reducing material waste. This secure packaging reduces damage during handling and transit, lowering the number of rejected products and minimizing waste from both damaged pipes and packaging materials.
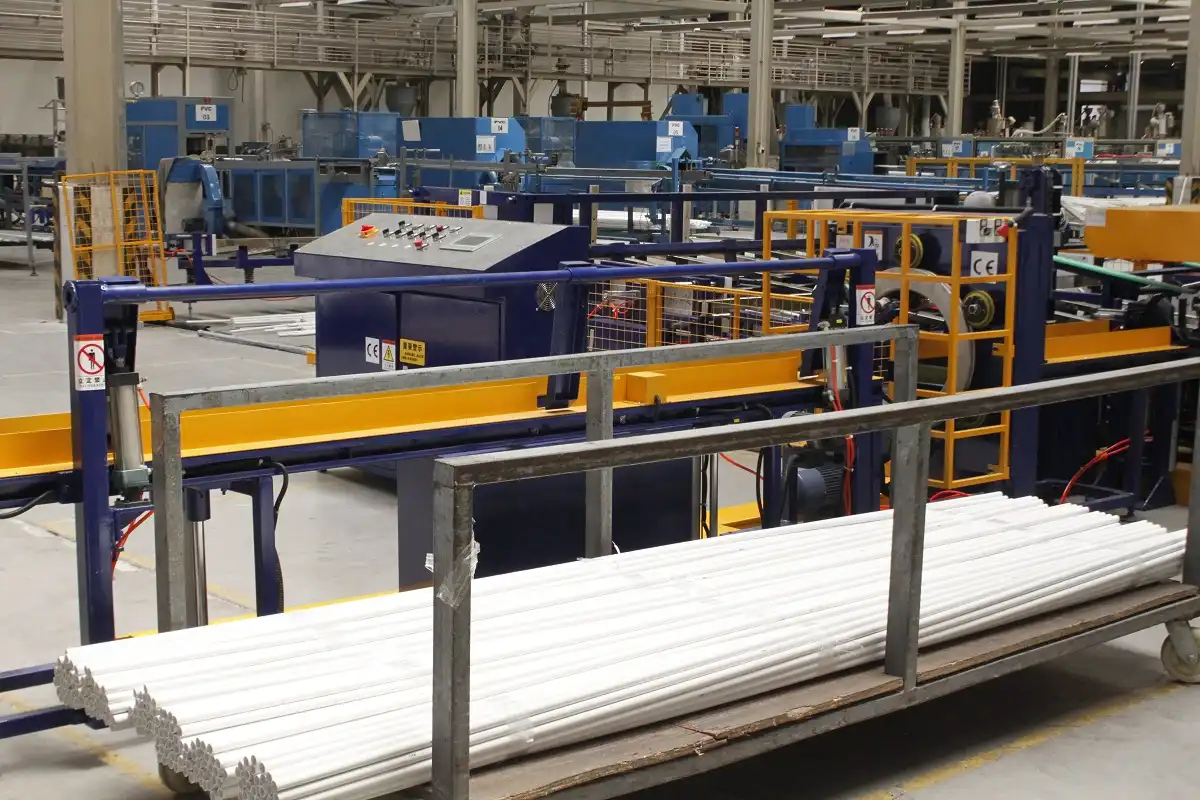
Waste Minimization Strategies: Protecting Your Investment
Compared to manual packaging methods, automated bagging machines employ several strategies to minimize damage and waste. Let’s explore these strategies in detail:
Damage Reduction and Waste Minimization: A Comparative View
Factor | Manual Packaging | Automated Bagging | Damage/Waste Reduction |
---|---|---|---|
Bundle Security | Less secure, inconsistent | Tighter, consistent | 30-50% |
Protection from Elements | Less protection, open | Full enclosure, weather protected | 20-40% |
Handling Damage | Higher risk, manual | Reduced handling, stable | 40-60% |
Packaging Material Waste | Higher, inconsistent use | Lower, optimized use | 15-30% |
Product Rejection Rate | Higher, handling damage | Lower, protective | 20-35% |
Enhancing Bundle Security: Stability in Transit
Automated bagging machines provide tighter and more consistent wrapping compared to manual tying, significantly enhancing bundle security. This reduces damage from impacts or vibrations during handling and transit, ensuring the product arrives in perfect condition.
Providing Weather Protection: Shielding from the Elements
The full enclosure offered by bagging machines provides better protection against environmental elements like moisture and dust, further minimizing damage. This is particularly important for pipes stored outdoors or transported over long distances.
Reducing Manual Handling: Minimizing Risk
Reduced manual handling due to automated systems minimizes the risk of damage during the packaging process itself. Each touchpoint increases the potential for damage, so minimizing handling is key to protecting the product.
Optimizing Material Usage: Precision Packaging
Automated systems optimize packaging material usage, reducing waste from excess material application, which is common in manual packaging. Precise measurements ensure that only the necessary amount of material is used, saving money and reducing environmental impact.
By implementing these strategies, businesses can reduce product rejection rates due to damage, leading to substantial savings and a more sustainable operation. The reduction in waste is not only beneficial for the bottom line but also promotes responsible manufacturing practices.
4. Enhancing Operational Efficiency for Cost Savings
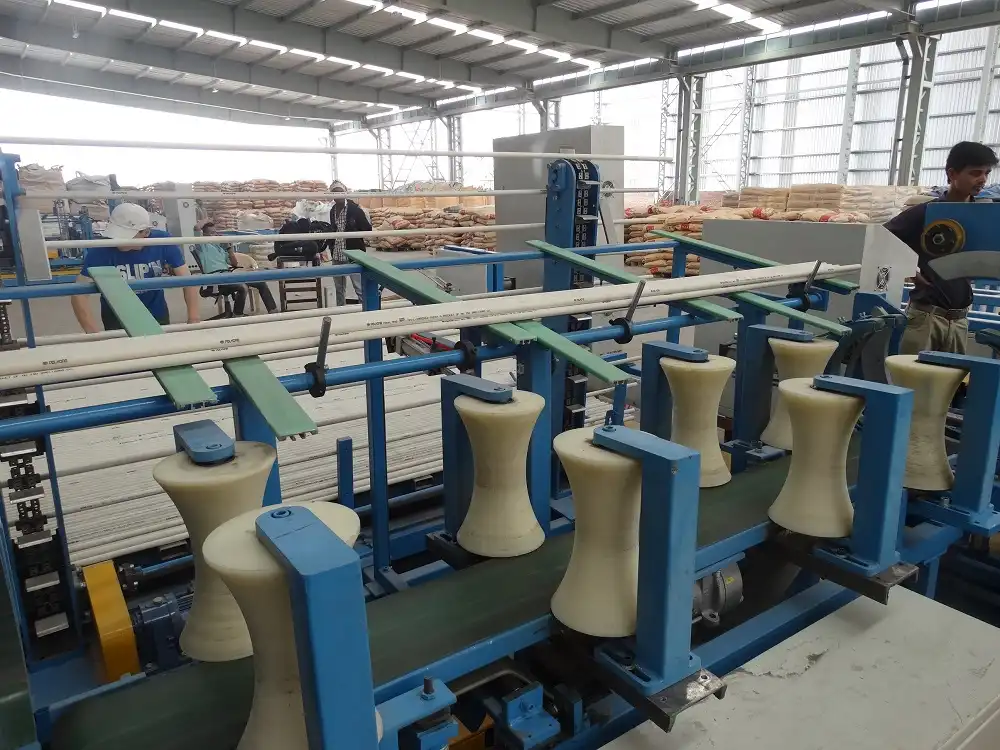
Manual methods are often slow and inefficient. Bagging machines operate at consistent high speeds, drastically increasing the number of bundles packaged per hour. This increases throughput and contributes to operational cost savings by optimizing resource utilization and reducing bottlenecks.
PVC pipe bagging machines are designed for high-speed operation, significantly increasing packaging throughput. Efficiency gains are crucial for maintaining competitiveness in the PVC pipe industry. Automated bagging can speed up the production process and contributes to substantial operational cost savings by optimizing resource utilization and reducing bottlenecks.
The increased speed dramatically boosts throughput capacity, eliminating bottlenecks that can slow down the entire production line. The increased throughput and streamlined operations translate to lower per-unit production costs. This operational efficiency is a key driver in achieving substantial cost savings and improving profitability for pipe manufacturers.
Conclusion
Automated pipe bagging systems offer a compelling solution for reducing labor costs and enhancing operational efficiency. These machines deliver quantifiable benefits across various aspects of operations. The ROI and sustained financial advantages make them a strategically sound investment. Automating bagging systems is a step toward a more efficient, cost-effective, and sustainable future. Investing in automated systems can yield a significant return, optimizing resource allocation and streamlining the packaging process for enhanced profitability.