How to Optimize the Performance of Plastic Pipe Bagging Machines?
Ensuring your plastic pipe bagging machines operate at peak efficiency is essential for maintaining productivity and minimizing downtime. Optimizing these machines involves a combination of proactive maintenance, data-driven insights, and skilled operation.
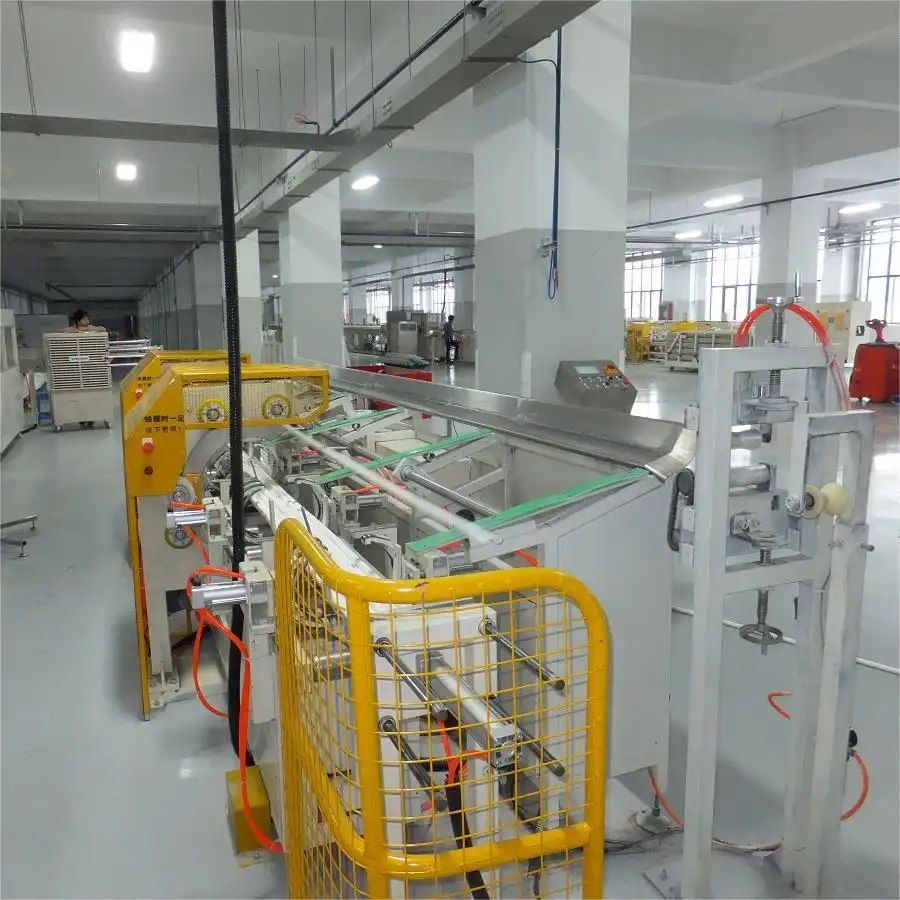
To optimize the performance of plastic pipe bagging machines, focus on regular maintenance, proper setup, and operator training. Maintenance minimizes downtime. Proper setup ensures smooth operation. Well-trained operators can identify and resolve issues quickly. Efficient bagging operations increase throughput and reduce costs.
Transitioning to a proactive approach not only enhances machine reliability but also significantly improves overall operational efficiency and positions businesses for sustained success. Here’s how to achieve optimal performance.
1. Understanding the Fundamentals of Bagging Machine Optimization
For plastic pipe bagging machines, consistent operation is key to meeting production demands. Understanding the basic principles of bagging machine operation is essential for effective optimization.
Plastic pipe bagging machine optimization involves understanding the machine’s components, identifying potential bottlenecks, and implementing data-driven strategies. This approach ensures consistent, efficient, and reliable bagging operations, leading to increased throughput and reduced waste. Proper lubrication, timely parts replacement, and optimized settings are key to maximizing machine performance.
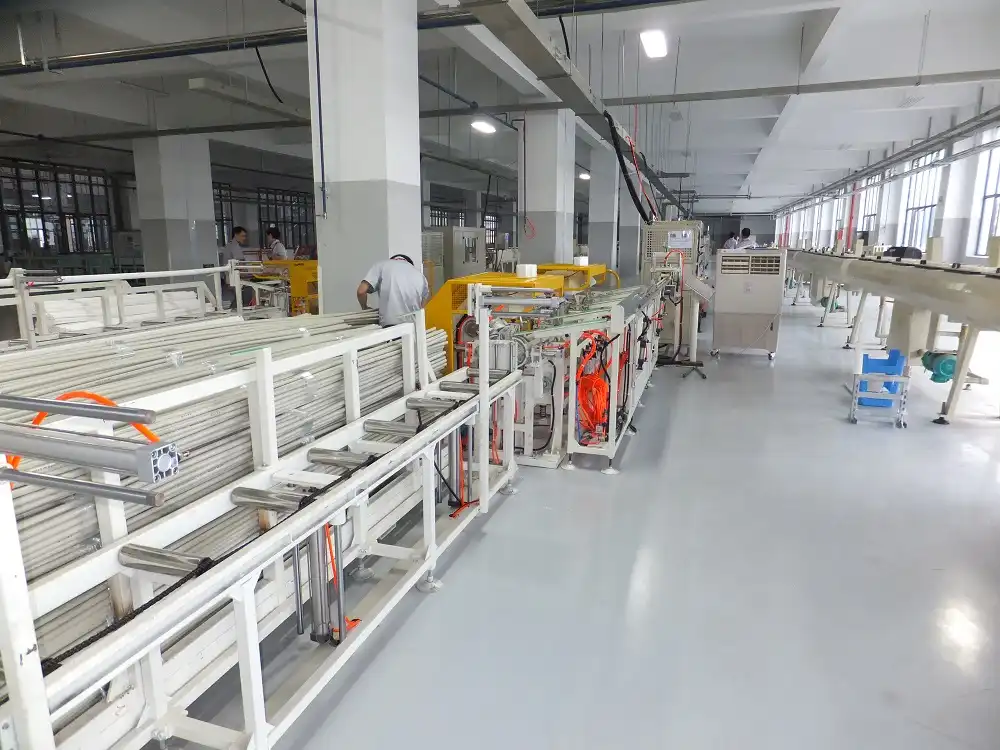
Decoding Machine Inefficiencies: A Data-Driven Approach to Optimization
Pinpointing areas for improvement requires a deep dive into machine data and operational metrics. By monitoring key performance indicators (KPIs) and analyzing trends, you can identify the root causes of inefficiencies and implement targeted solutions. A data-driven approach allows for proactive optimization, ensuring efforts are focused on areas with the biggest potential for improvement, leading to tangible gains in bagging machine efficiency.
Identifying Key Performance Indicators (KPIs)
To effectively optimize your bagging machine, it’s crucial to track and analyze relevant KPIs. These metrics provide valuable insights into machine performance, helping you identify bottlenecks and areas for improvement. Let’s consider these areas:
Overall Equipment Effectiveness (OEE)
A comprehensive metric encompassing Availability, Performance, and Quality, OEE is the gold standard for measuring manufacturing productivity. It takes into account all losses, resulting in a measure of truly productive manufacturing time. OEE is calculated as:
OEE = Availability x Performance x Quality
A high OEE score indicates efficient utilization of your equipment, while a low score signals areas needing improvement.
Downtime Analysis
Downtime refers to the total time the machine is not operational due to breakdowns, changeovers, or other issues. Analyzing downtime helps identify the most frequent causes of interruptions.
Throughput Rate
The throughput rate is the number of bags produced per hour or shift. Monitoring throughput helps assess the machine’s speed and efficiency in packaging pipes.
Rejection Rate
The rejection rate is the percentage of bags rejected due to errors such as sealing issues or incorrect counts. Tracking this metric highlights problems in the bagging process.
Changeover Time
Changeover time is the time taken to switch between different pipe sizes or bag types. Reducing changeover time improves the machine’s flexibility and overall productivity.
Here’s a table summarizing these KPIs:
KPI | Description | How to Track | Target Improvement |
---|---|---|---|
Overall Equipment Effectiveness (OEE) | A comprehensive metric encompassing Availability, Performance, and Quality. | Automated systems, manual data logging | Aim for 85% OEE or higher |
Downtime | Total time the machine is not operational due to breakdowns, changeovers, etc. | Machine sensors, operator logs, maintenance records | Reduce downtime by 15-20% through preventative actions |
Throughput Rate | Number of bags produced per hour or shift. | Production counters, automated tracking systems | Increase throughput by 5-10% by optimizing settings |
Rejection Rate | Percentage of bags rejected due to errors (sealing issues, incorrect counts). | Quality control checks, automated inspection systems | Decrease rejection rate below 2% |
Changeover Time | Time taken to switch between different pipe sizes or bag types. | Timed procedures, operator logs | Reduce changeover time by 20-30% through standardization |
By consistently monitoring these KPIs, you gain a clear picture of your bagging machine’s performance. Analyzing trends in these metrics will highlight specific areas dragging down efficiency. For example, a consistently low OEE coupled with high downtime points directly to maintenance issues. A high rejection rate might indicate problems with machine calibration or operator errors.
Using Data to Diagnose Issues
Once you’re collecting data, the next step is to analyze it to diagnose the root causes of inefficiencies.
Pareto Charts for Downtime: Categorize downtime events (e.g., mechanical failures, electrical issues, material jams) and create a Pareto chart. This visually highlights the most frequent causes of downtime, allowing you to prioritize corrective actions.
Trend Analysis for Throughput: Track throughput rates across different shifts and days. Significant variations might indicate inconsistencies in operator performance or material supply issues.
Correlation Analysis for Rejection Rates: Investigate if rejection rates correlate with specific operators, shifts, or material batches. This can pinpoint training needs or material quality problems.
2. Implementing a Robust Preventative Maintenance Program
Consistent uptime is paramount in bagging operations. A well-structured preventative maintenance schedule is the cornerstone of minimizing downtime and maximizing bagging machine availability.
For continuous PVC pipe bagging, a preventative maintenance schedule is essential. This involves regular checks and in-depth inspections to minimize breakdowns. Proactive maintenance extends machine lifespan and ensures consistent performance. Daily cleaning, lubrication, and belt tension checks are crucial for smooth, efficient bagging operations.
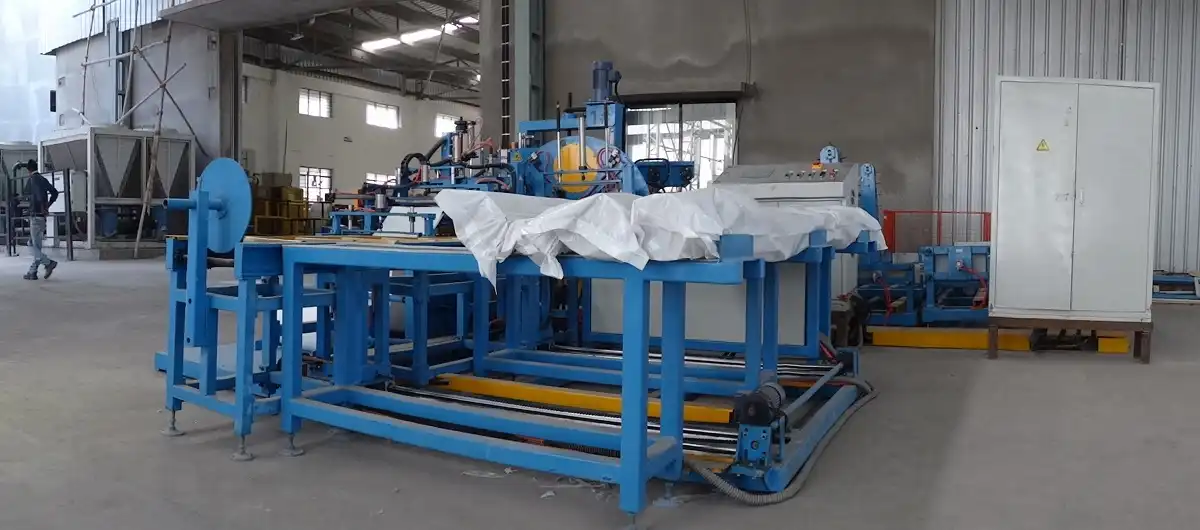
Crafting a Multi-Tiered Preventative Maintenance Plan
A truly effective preventative maintenance plan needs to be structured, comprehensive, and consistently executed. It should encompass various levels of maintenance, performed at different intervals.
Daily Maintenance (End of Each Shift)
Cleaning: Remove PVC dust and debris from all accessible machine parts, especially sealing areas, conveyors, and sensors. Use compressed air and brushes. Visual Inspection: Check for loose bolts, worn belts, damaged wires, or any signs of wear and tear. Pay attention to critical components like sealing jaws and cutting blades. Lubrication (Minor): Apply a light lubricant to designated points as per the manufacturer’s manual, focusing on chains, gears, and moving joints. Sensor Check: Ensure all sensors (proximity, photoelectric) are clean and functioning correctly. Test their response if possible.
Weekly Maintenance
Detailed Cleaning: More thorough cleaning, including removing guards (when safe and permissible) to access less accessible areas. Lubrication (Comprehensive): Lubricate all grease points and bearings according to the maintenance schedule, using the correct type of lubricant. Belt Tension Check: Verify and adjust belt tension for conveyors and drive systems. Improper tension can lead to slippage and premature wear. Chain and Sprocket Inspection: Inspect chains for wear, stretch, and proper lubrication. Check sprocket teeth for damage. Pneumatic System Check (if applicable): Drain air filters, check for leaks in hoses and fittings, and ensure proper air pressure. Safety System Check: Test emergency stops, safety interlocks, and light curtains to ensure they are functioning correctly. Document the checks.
Monthly/Quarterly Maintenance (Scheduled Downtime)
In-Depth Inspection: A comprehensive inspection of all mechanical, electrical, and pneumatic systems by trained maintenance personnel. Component Replacement (Preventative): Replace wear parts proactively based on usage hours or manufacturer recommendations (e.g., sealing jaws, cutting blades, belts, bearings). Calibration and Adjustment: Recalibrate sensors, adjust timing mechanisms, and fine-tune machine settings to maintain optimal performance. Electrical System Inspection: Check wiring connections, motor condition, control panel components, and safety grounds. Software/PLC Check (if applicable): Verify software versions, backup PLC programs, and check for any error logs.
Diving into Technical Details: Lubrication Systems
Proper lubrication is essential for the longevity and efficiency of PVC pipe bagging machines. Different components require different types of lubricants and lubrication schedules.
Bearing Lubrication: Bearings are critical components that support rotating shafts and reduce friction. The type of lubricant used depends on the bearing type and operating conditions. Ball bearings often require light oils or greases, while roller bearings may need heavier greases. Regular lubrication, typically weekly or monthly, ensures smooth operation and prevents premature wear.
Chain and Sprocket Lubrication: Chains and sprockets transmit power and require lubrication to minimize friction and wear. Chain lubricants should penetrate the chain links and provide a protective film. Regular lubrication, often daily or weekly, keeps the chains running smoothly and extends their lifespan.
Pneumatic System Lubrication: Pneumatic systems use compressed air to actuate cylinders and other components. Lubricating these systems involves adding oil to the air stream using an oiler. This ensures that the cylinders and valves operate smoothly and prevents corrosion. Regular monitoring and replenishment of the oiler are essential for maintaining system performance.
Automated Lubrication Systems: To simplify lubrication and ensure consistent application, automated lubrication systems can be installed. These systems deliver precise amounts of lubricant to designated points at predetermined intervals. This reduces the risk of over- or under-lubrication and minimizes maintenance time.
Here’s a table outlining typical lubrication points and schedules:
Component | Lubricant Type | Schedule | Notes |
---|---|---|---|
Bearings | Light Oil or Grease | Weekly/Monthly | Consult manufacturer’s recommendations for specific lubricant types. |
Chains and Sprockets | Chain Lubricant | Daily/Weekly | Ensure lubricant penetrates chain links. |
Pneumatic Cylinders | Pneumatic Oil | As Needed | Monitor and replenish oiler regularly. |
Sliding Surfaces | Grease or Oil | Weekly | Apply to sliding surfaces to reduce friction. |
3. Optimizing Material Flow and Changeover Procedures
Efficient material flow and rapid changeovers are critical for minimizing downtime and maximizing throughput in plastic packaging bagging operations.
Effective material handling and quick changeovers minimize disruptions to the continuous flow of production. Automated infeed systems, buffer zones, and ergonomic material presentation are essential. Standardized procedures, quick-release mechanisms, and checklists reduce changeover times, ensuring high output and minimal waste.
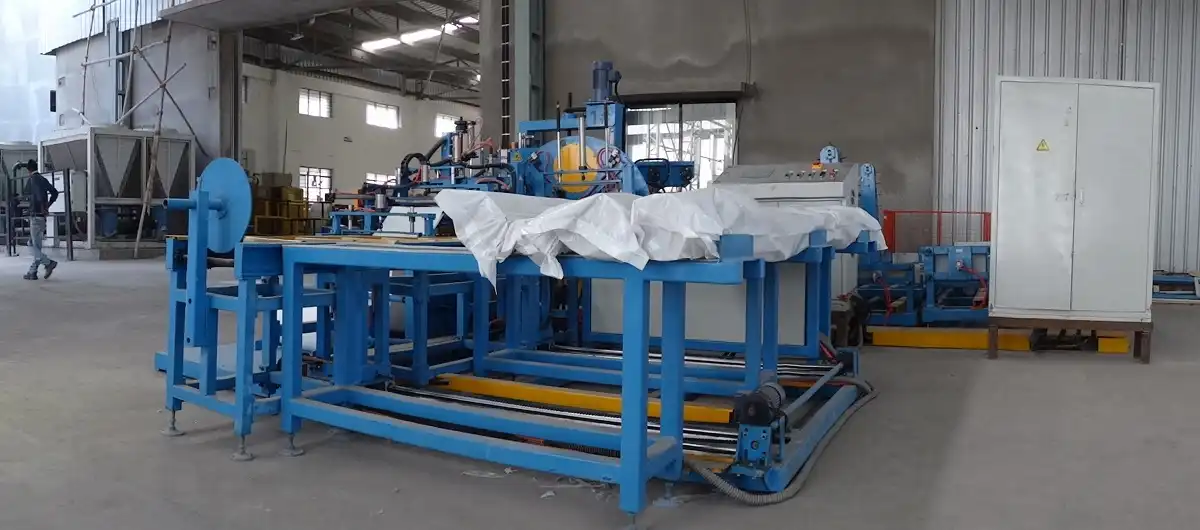
Streamlining for Sustained High Performance
In multi-shift operations, even small delays in material handling or changeovers can accumulate significantly, impacting overall efficiency. Streamlining these processes is key to sustained high performance.
Technical Details: Analyzing Changeover Time Reduction Techniques
Reducing changeover time involves both organizational and technical improvements. Organizational improvements include standardized procedures, checklists, and dedicated changeover teams. Technical improvements involve quick-release mechanisms, modular tooling, and pre-staged components.
Quick-Release Mechanisms: Quick-release mechanisms allow for rapid removal and installation of tooling and components. These mechanisms can reduce changeover time by eliminating the need for tools and minimizing the number of fasteners. Examples include cam locks, quick-release clamps, and snap-fit connectors.
Modular Tooling: Modular tooling consists of interchangeable components that can be quickly assembled and disassembled. This allows for rapid adaptation to different pipe sizes and bag types. Modular tooling can be pre-staged and quickly installed during changeovers.
Pre-Staged Components: Pre-staging involves preparing all necessary components, tools, and materials before the changeover begins. This reduces the time spent searching for items and minimizes interruptions. Pre-staged components can be organized on carts or shelves for easy access.
Standardized Procedures: Standardized procedures provide a clear and consistent framework for changeovers. These procedures should include step-by-step instructions, checklists, and visual aids. Standardized procedures ensure that changeovers are performed correctly and efficiently.
Strategy | Description | Benefits |
---|---|---|
Automated Infeed Systems | Implement automated conveyor systems or robotic arms to feed PVC pipes to the bagging machine. | Reduces manual handling, ensures a consistent supply. |
Buffer Zones | Create buffer zones for pipes waiting to be bagged and for finished bags. | Prevents bottlenecks, ensures continuous machine operation. |
Optimized Layout | Design the bagging machine layout to minimize material travel distances. | Eliminates unnecessary movements, improving efficiency. |
Quick-Release Mechanisms | Utilize quick-release clamps, fasteners, and tooling. | Reduces changeover time by converting internal tasks to external tasks. |
Standardized Changeover Procedures | Develop detailed, step-by-step procedures for changeovers. | Minimizes the time spent on adjustments and component changes. |
Training and Practice | Train operators thoroughly on quick changeover procedures and conduct regular practice sessions. | Improves speed and accuracy, reduces errors, and enhances production flexibility. |
Checklists and Verification | Use checklists to ensure all steps in the changeover process are completed correctly and to verify machine readiness. | Reduces downtime, increases throughput, improves operator efficiency, lowers material waste. |
4. Training and Skill Development for Operators
Investing in thorough operator training is crucial for maximizing plastic pipe bagging machine efficiency in any operational environment. Well-trained operators can optimize machine settings and quickly troubleshoot minor issues.
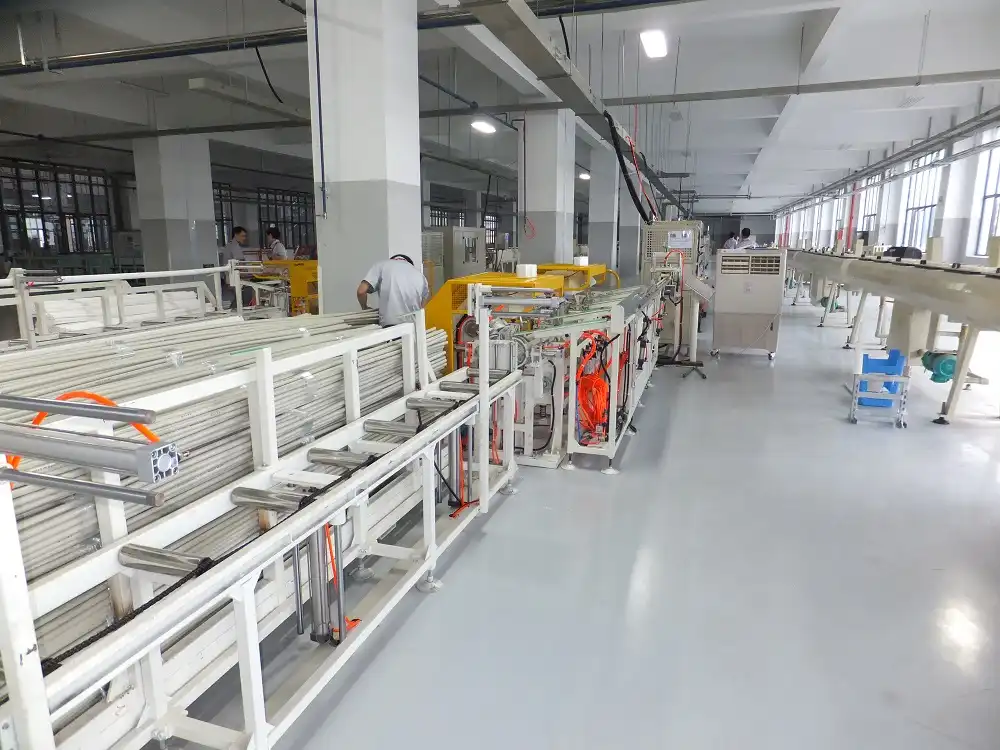
Comprehensive operator training is key to efficient bagging machine performance. Well-trained operators can optimize settings and quickly address issues. Basic operation and safety training is essential, followed by advanced optimization and maintenance skills. Hands-on training, structured manuals, and regular refresher sessions are vital for creating efficiency champions.
Building a Multi-Level Program
An effective operator training program should be structured, progressive, and ongoing, catering to different skill levels and experience. It should encompass both theoretical knowledge and hands-on practical skills.
Basic Operation and Safety (Initial Training for All New Operators):
Machine Overview: Introduction to the bagging machine components, functions, and overall operation. Control Panel Operation: Detailed explanation of the control panel, HMI interface, and all control functions (start, stop, speed adjustment, sealing parameters, etc.). Safety Procedures: Comprehensive training on all safety protocols, emergency stops, lockout/tagout procedures, and safe operating practices. Basic Troubleshooting: Identification of common error messages and simple troubleshooting steps (e.g., clearing jams, resetting sensors). Quality Control Basics: Understanding quality standards for bagged pipes, visual inspection criteria, and rejection procedures.
Advanced Operation and Optimization (For Experienced Operators):
Parameter Optimization: In-depth training on adjusting machine parameters (sealing temperature, pressure, speed, film tension) to optimize performance for different pipe types and bag materials. Changeover Procedures: Detailed, step-by-step training on performing efficient and accurate changeovers between pipe sizes and bag types, minimizing downtime. Preventative Maintenance (Operator Level): Training on daily and weekly maintenance tasks operators are responsible for (cleaning, lubrication, visual checks). Advanced Troubleshooting: Diagnosis and resolution of more complex issues, using machine diagnostics and troubleshooting manuals. Data Logging and KPI Monitoring: Training on how to collect production data, monitor KPIs, and identify areas for improvement.
Supervisory and Maintenance Skills (For Lead Operators and Potential Technicians):
Machine Mechanics and Electrics (Basic): Fundamental understanding of machine mechanics, electrical systems, and pneumatic components. Advanced Maintenance Procedures: Training on more complex preventative maintenance tasks and basic repairs under supervision. Operator Training (Train-the-Trainer): Developing skills to train new operators and conduct refresher training for existing staff. Production Management Basics: Understanding production planning, scheduling, and efficiency metrics. Inventory Management (Basic): Managing consumables (bags, film) and spare parts at the operator level.
Addressing Common Skill Gaps
To ensure the effectiveness of the training program, it’s essential to identify and address common skill gaps among operators. This can be achieved through assessments, feedback, and targeted training modules.
Troubleshooting Skills: Many operators struggle with diagnosing and resolving machine problems. Providing hands-on training on troubleshooting techniques, such as using diagnostic tools and interpreting error codes, can improve their ability to quickly resolve issues.
Parameter Optimization Skills: Optimizing machine parameters for different pipe types and bag materials requires a deep understanding of the machine’s capabilities and limitations. Training operators on parameter optimization techniques can help them achieve optimal performance.
Maintenance Skills: Performing basic maintenance tasks, such as lubrication and sensor cleaning, can prevent machine problems and extend its lifespan. Training operators on these tasks can reduce the need for maintenance personnel.
Changeover Skills: Efficient changeovers are essential for minimizing downtime. Training operators on quick changeover techniques can improve their speed and accuracy, reducing changeover time.
Data Analysis Skills: Collecting and analyzing production data can help identify areas for improvement. Training operators on data analysis techniques can empower them to make data-driven decisions.
Implementing a Structured Training Program
A structured training program should include the following elements:
Training Needs Assessment: Identify the specific skills and knowledge that operators need to improve their performance.
Training Objectives: Define clear and measurable objectives for each training module.
Training Content: Develop training materials that are relevant, engaging, and easy to understand.
Training Methods: Use a variety of training methods, such as hands-on training, classroom instruction, and online modules.
Training Evaluation: Evaluate the effectiveness of the training program through assessments, feedback, and performance metrics.
By implementing a structured training program, you can equip your operators with the skills and knowledge they need to maximize the performance of your PVC pipe bagging machines.
Conclusion
Maximizing the efficiency and lifespan of plastic pipe bagging machines requires a strategic, multifaceted approach. By focusing on data-driven analysis, proactive maintenance, skilled operators, and streamlined processes, businesses can unlock significant gains. These strategies ensure consistent output, reduced downtime, and enhanced profitability, leading to a more efficient and competitive operation. Proper maintenance, comprehensive operator training, and optimized material flow are the keys to unlocking maximum potential and sustaining long-term success. By combining these elements, manufacturers can ensure their bagging operations contribute significantly to their bottom line and overall operational efficiency.